Inspiration through Innovation 2020 – Aerospace Manufacturing Best-Practice Virtual Event
View recordings from Inspiration through Innovation 2020, focused on aerospace manufacturing in special materials like Inconel and CFRP.
Demonstration – Overcoming Common Machining Challenges in Inconel 718
Hooks, fins, slots ... these can all be difficult features to machine, especially in superalloy materials that traditionally require low speed removal rates. This session will demonstrate significantly improved metal removal rates using B-axis turning and waveform strategies, TGH 1050, ceramic turning inserts, and solid ceramic endmills on a 5-axis simultaneous multi-task machine. Collaborative partner technologies: Hexagon Edgecam Waveform, Hexagon NCSimul, Wogaard Coolant Saver and Seco Tools.
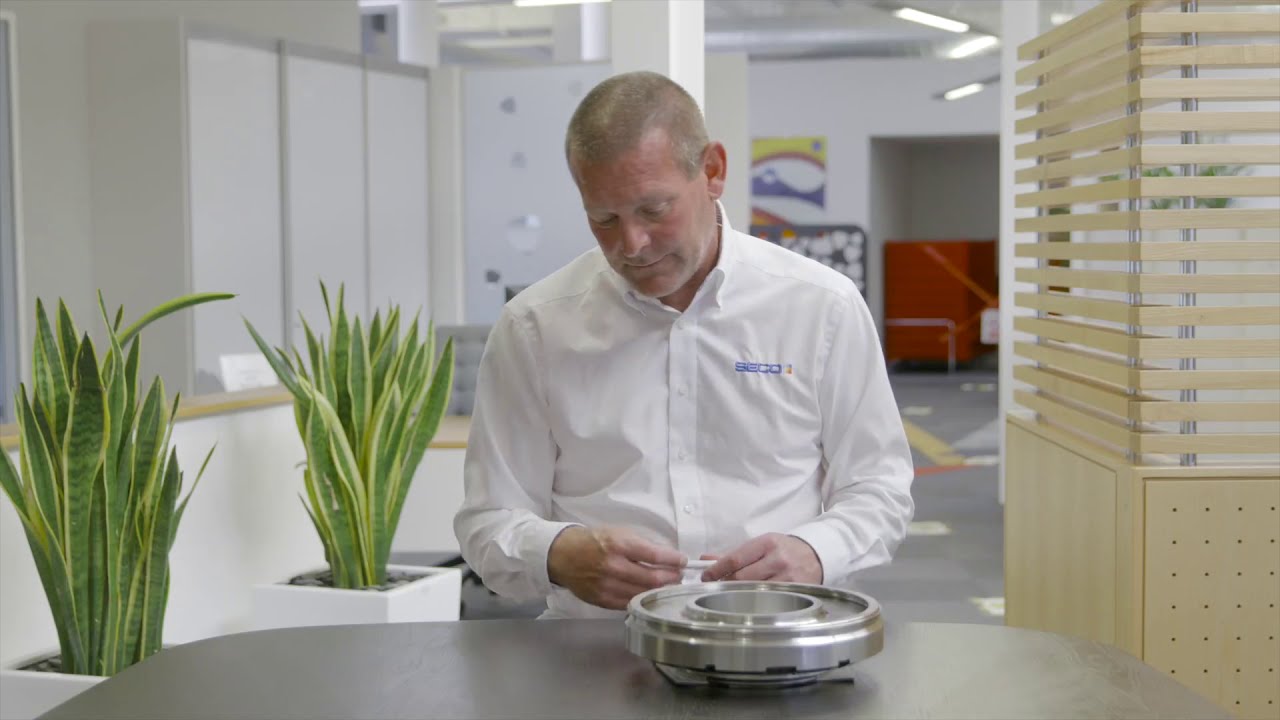
Demonstration – Ensuring Outstanding Quality for Manufacturing a Helicopter Carbon Fibre Tail Fin
Increase productivity while ensuring quality and safety when machining aerospace carbon fibre composites aerostructures on a portal 5-axis milling machine with integrated composite dust extraction system. This demo showcases various milling strategies applicable for composite machining, demonstrating a custom PCD lens tool for surfacing to increase productivity while maintaining surface integrity. Benefit from minimisation of idle times during drilling by fast positioning with linear motor technology for high true part accuracy. Learn about drilling holes with both diamond-coated and PCD drills, focusing on hole quality and size, with minimal delamination which is critical for these components. Discover when and why to use CVD diamond coated versus PCD tools, incorporating the best strategies to apply them. Collaborative partner technologies: H&H AGILE P5 five axis portal milling machine, Siemens 840D and NX12 and Seco Tools.

Technical Spotlight – Nickel Alloy Blisk Manufacturing, Starrag
Nickel alloy blisk machining advantages using Starrag's NB151 machine and Seco Tools. Heavy roughing and dynamic finish machining utilising the maximum stiffness and shortest axis moves to guarantee lowest cycle times and lowest ongoing consumable tool costs.
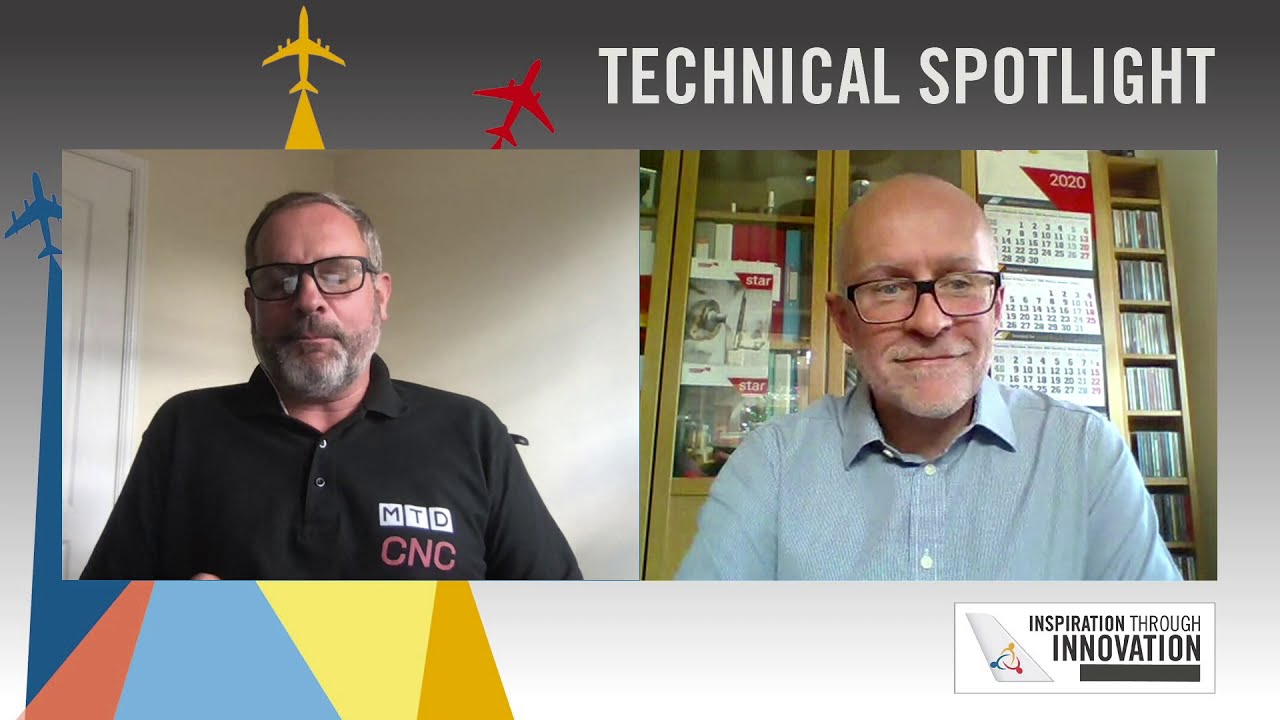
Technical Spotlight – Power Skiving, Mazak
Power skiving technology allows for a component to be machined through all of its phases on a single multi-tasking machine or machining centre with a single setup. It therefore eliminates the need to have more dedicated machines, avoiding setup errors deriving from the transfer from one machine to the next, eliminating radial run-out errors almost completely. This approach significantly reduces the total machining time compared to processes that include broaching, profiling or hobbing operations, ensuring reliable and repeatable machining of the components. Especially when using an interchangeable solid carbide head, skiving allows for machining and finishing of the tooth profile. By using a custom milling cutter synchronised to the rotation of the workpiece, gear teeth are cut by continuous hobbing coupled with axial feed. Learn from Seco and Mazak experts about the skiving process and the latest related technology.
