5 Tips for overcoming the skilled Labor Shortage
Machine capacity is hardly an issue when you're dealt with a global labor shortage. Explore these quick tips to re-engineer your skilled labor challenges.In the past, when a shop lacked capacity or wanted to expand, their easiest solution was to add more capital equipment. Unfortunately, that’s not the case these days.
During customer visits, we often see that machine capacity is not the issue. Instead, these shops face another more pressing problem – a lack of skilled labor. While the production demand is there, they are unable to meet it because machines sit idle with no one to run them.

To overcome this skilled labor dilemma, there are five basic tips a shop should apply.
- Update your skills matrix
- Train your people
- Focus on value added tasks
- Standardize and document your processes
- Partner with schools
To start, conduct an overview of the situation and measure the extent of your problem. Many manufacturers already have a skills matrix of some sort where they track the skill level of every operator and which machines they are able to run. If this information is only in the head of your production manager, it is high time to put it on paper so that everyone – managers, HR, but also operators themselves – have a clear understanding of the situation.
While having a proper, up to date skills matrix is a good start, best practice is to add other layers to it, such as a risk assessment. A good skills matrix should help visualize which employees are likely to leave soon. You need to identify any upcoming retirements and the number of temporary workers you have along with any individuals who have expressed dissatisfaction with their job. You must also determine those individuals with critical knowledge that makes them difficult to replace, both upstream and downstream in your manufacturing process. For instance, they are the only ones who can run a particular machine or perform a complex task. Crossing these layers of information – knowledge, skills and risk – will ensure you can always serve your customers even if you lose key workers.
Download here an example file for a skills matrix
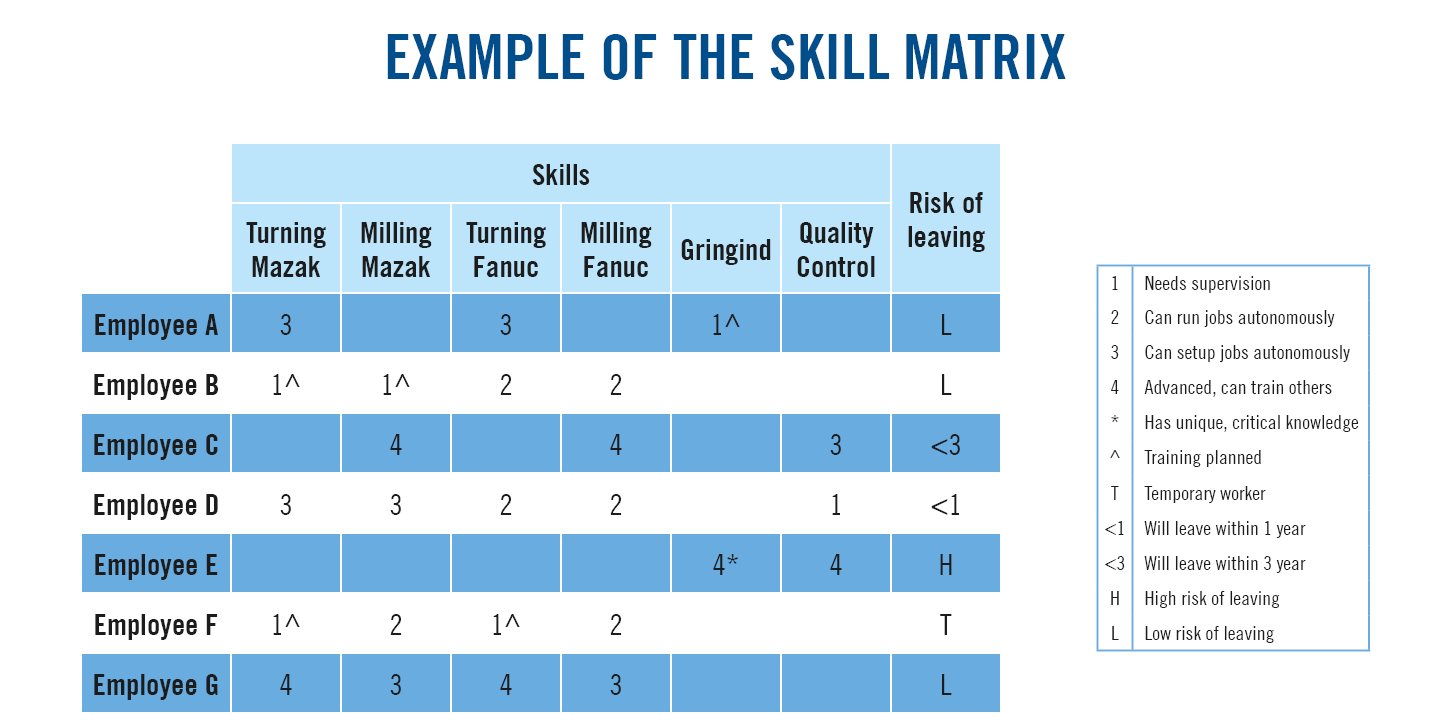
Example of a skill matrix
Once you have your skills matrix in place, you should plan how to make your people move up the ranks and become more skilled or more polyvalent. Internal experts within your company can for instance share their advice and work with newcomers. Consider also changing which machine operators work on every once in a while. You can also rely on external trainers or suppliers for specific topics such as machining strategies or tool wear recognition. Such training and rotation between different machines keeps the job interesting and employees motivated, so they are more likely to stay.While it’s always tough to find the time for training, doing so should be viewed as an investment. The time you invest to train your people now will yield future dividends in the form of operators who work more efficiently and in your ability to keep machines running despite missing people because others have been trained and can cover for them.
You always want to make sure that your employees are spending time on value added tasks.This starts with addressing operator issues. If you show that you care, you will boost both performance and morale by solving the problems that bother them in their daily tasks. Conversely, not acting on their feedback will only make them stop reporting issues and leave them disgruntled. Using established problem-solving techniques such as Root Cause Analysis, 5 Why, 8D or Ishikawa diagrams will help ensure you effectively solve problems.
Another way to keep your operators focused on value added tasks is to reduce the time they spend walking around and looking for equipment, tools or fixtures. Because these items are often not identified or tracked, no one knows where they are, so operators go from machine to machine asking their colleagues – wasting their time in the process – where an item is located.Having a good data structure and well-organized storage areas will help operators find what they need quickly. Nowadays, there are even digital solutions like smart cabinets and Data Matrix codes that can speed up inventory management and tool identification processes. All these improvements will help you decrease setup times. If you are able to optimize changeovers and make them quick enough, then one operator could have time to set up another job on another machine while the previous job is still running on the first machine.

To free up machine operators for additional production time, you must have in place standard rules, procedures and ways of working. For example, when do your operators change a worn-out tool? Before every new job? When it looks bad? When it sounds bad? And how do you define bad?
Chances are everyone in your shop will have a different answer. To simplify this decision-making process and avoid wasted time and resources, you need to share tips and best practices among everyone. For instance, you should provide instructions along with every setup – comments on how the job was done last time, what issues were encountered and how they were solved.
This will not only make your current employees more productive, but also accelerate the training of future workers while increasing the pool of candidates to choose from when you want to hire. Indeed, when everything is documented and explained, training newcomers is much easier, so you are not limited to hiring already autonomous workers. Instead, you can accommodate people with less experience but who are willing to learn.A good test to determine if your procedures are adequate is to give the available documentation to a newcomer. Look where they struggle and improve the instructions when needed. If they manage to deliver, you can be confident that everyone will perform the task with the same level of quality.
To find new people, partner with local education facilities, universities or vocational schools. Interns, trainees or apprentices provide extra capacity for specific improvement projects, and they form a pool of potential new hires who already know your company and that you can train according to your needs.These individuals also have an outside view, so they can quickly spot improvement opportunities that are obvious for them but that you may have overlooked. They are also aware of the latest production technologies, digital solutions or software that may be relevant for your company. While they may not have all the skills you need today, they already have those you will need tomorrow when your shop inevitably shifts towards digital manufacturing and Industry 4.0.One last, longer-term reason to partner with schools is to give them feedback on their education material and training programs. If those don’t match your needs, you have a chance to influence them by keeping them up to date with the relevant skills and latest trends of your industry. Future students will then be a better fit for your company.
With no end in sight, the current shortage of skilled workers is testing the resilience of even the most agile of companies. Those who act now to address it will certainly gain a competitive advantage: the demand for machined parts is still strong, so boosting capacity and productivity will ultimately result in increased revenue. In any case, proactively spreading knowledge on critical processes will make your production more flexible, stable, and ready for new challenges to come.
Inline Content - Survey
Current code - 5fce8e61489f3034e74adc64