Is average chip thickness an outdated concept?
If the machinist uses the cutting edge with the same working conditions as those which were defined by the designer of the cutting edge, the cutting tool will perform to the maximum of its capacity! In this Getting Technical Live session, we will discuss the theoretical thickness of the undeformed chip (h1)If the machinist uses the cutting edge with the same working conditions as those which were defined by the designer of the cutting edge, the cutting tool will perform to the maximum of its capacity!
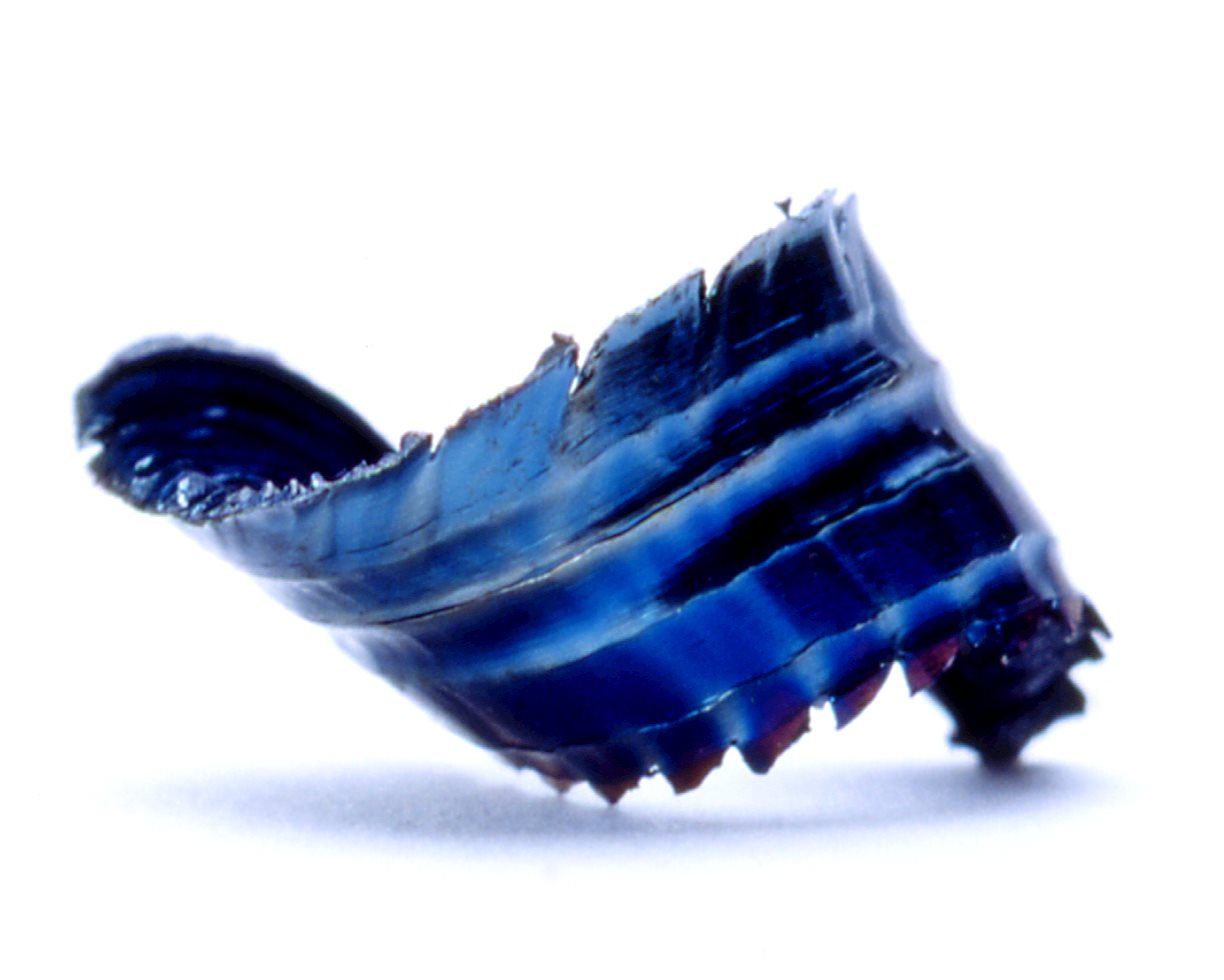
The cutting performance of any cutting edge is strongly depending on the theoretical thickness of the undeformed chip (h1).
In all physical models for cutting forces, cutting temperatures, tool life, ... h1 is the key variable. Machining researchers and tool developers concentrate a lot on h1 to describe the machining process and the tool performance. In the industrial workshop the h1-related cutting parameter is the feed (f).
It is important that the machine operator or production engineer determine the feed so that the h1 used by the tool designer is respected. Only then the tool will perform in line with its full capacity. In discontinuous machining operations (milling), the machining engineer is confronted with the dilemma that physically h1 is not constant but that the feed is a constant value throughout the operation.
To handle this dilemma in a practical manner, the notion of average chip thickness has been developed. And it served the expert machinist well, it still does and it will continue to do so in the future.

HOMERelated content
Getting Technical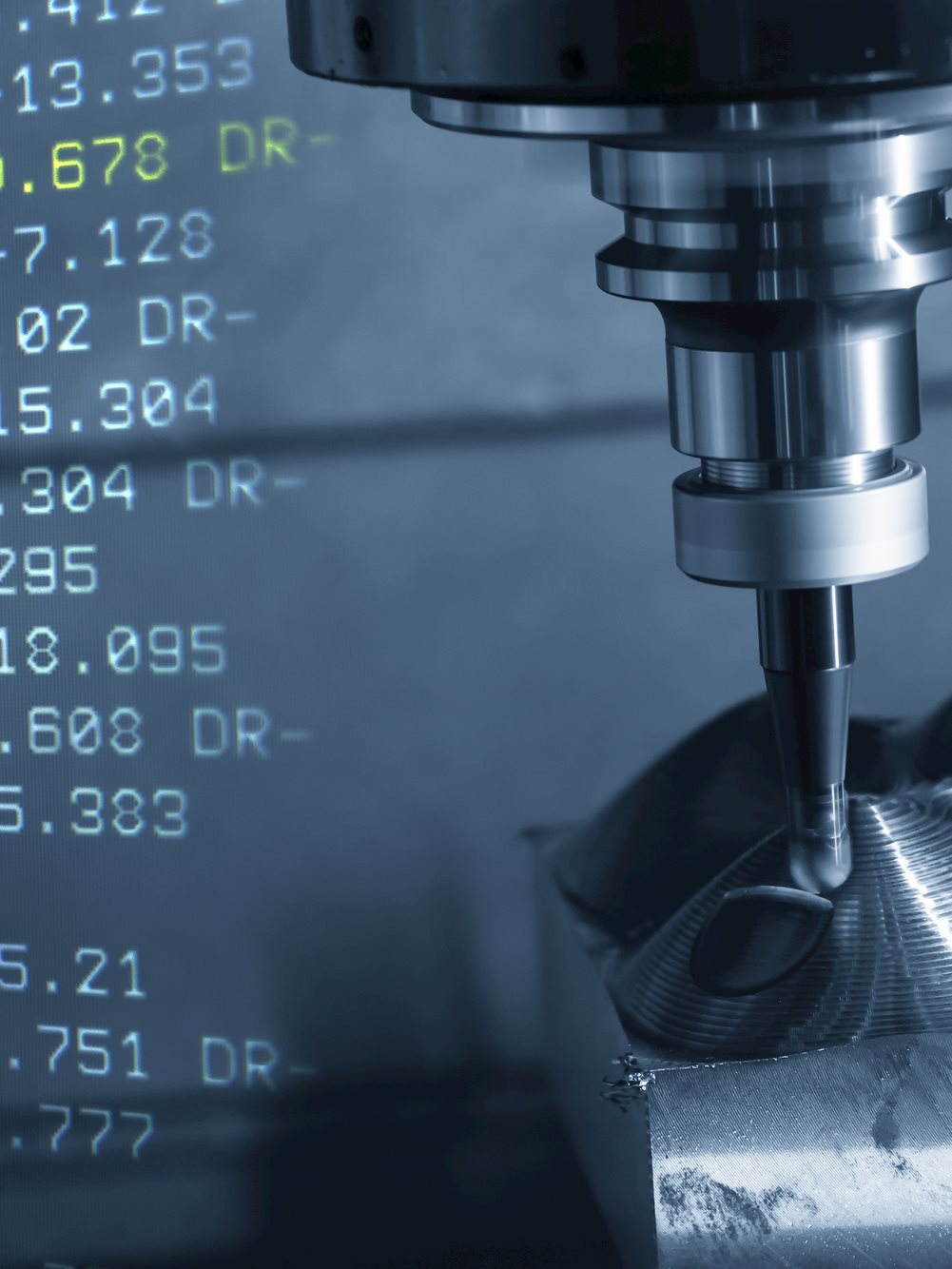
Milling Cutter positioning. What it is? And why is it so important?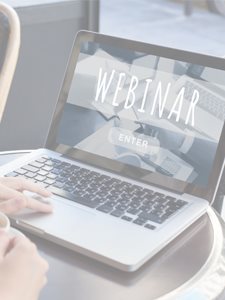
Part 1 - What you don't know about tool holders could hurt your manufacturing!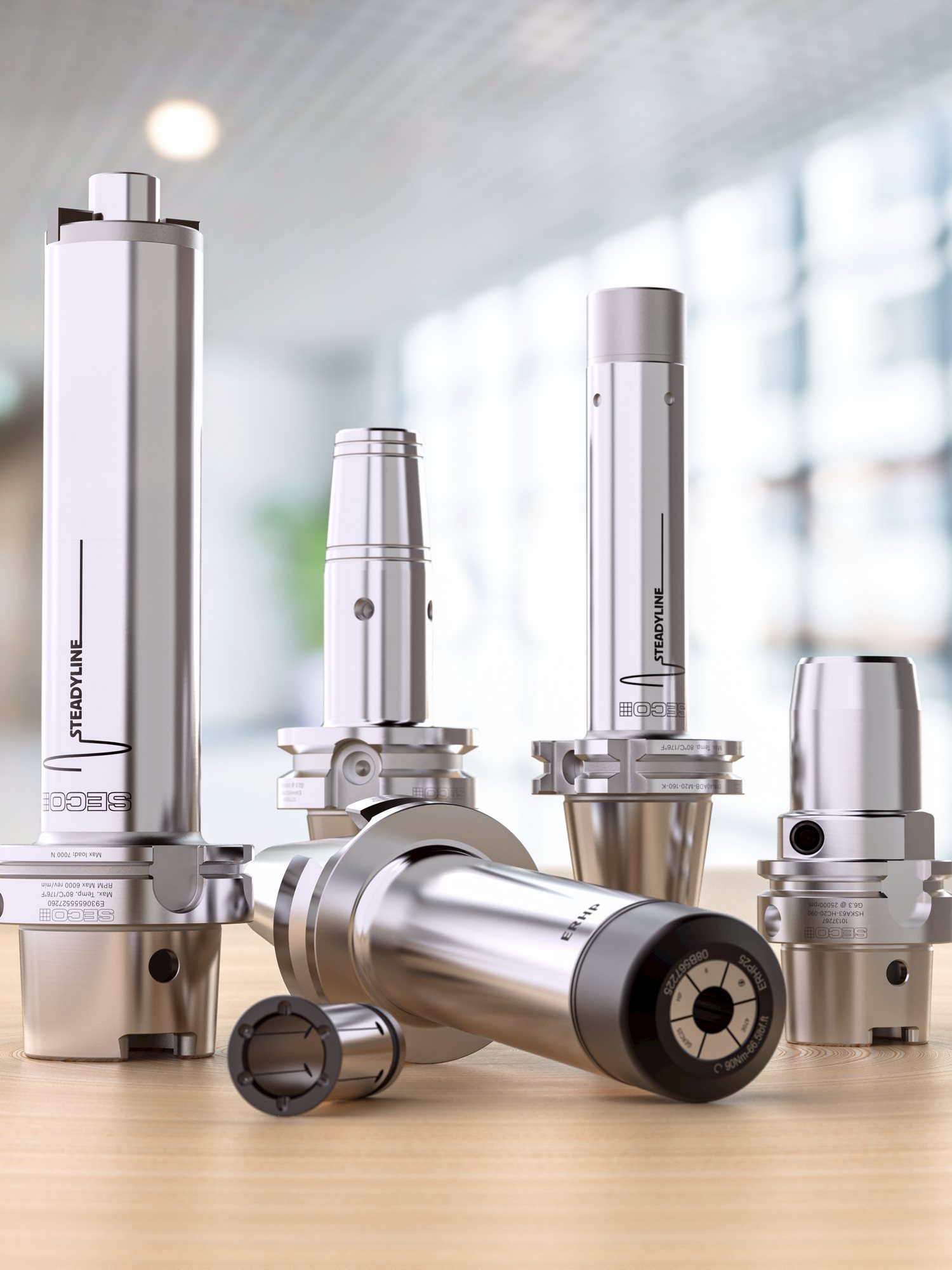
Machining mastery explored: Model-based machining advancements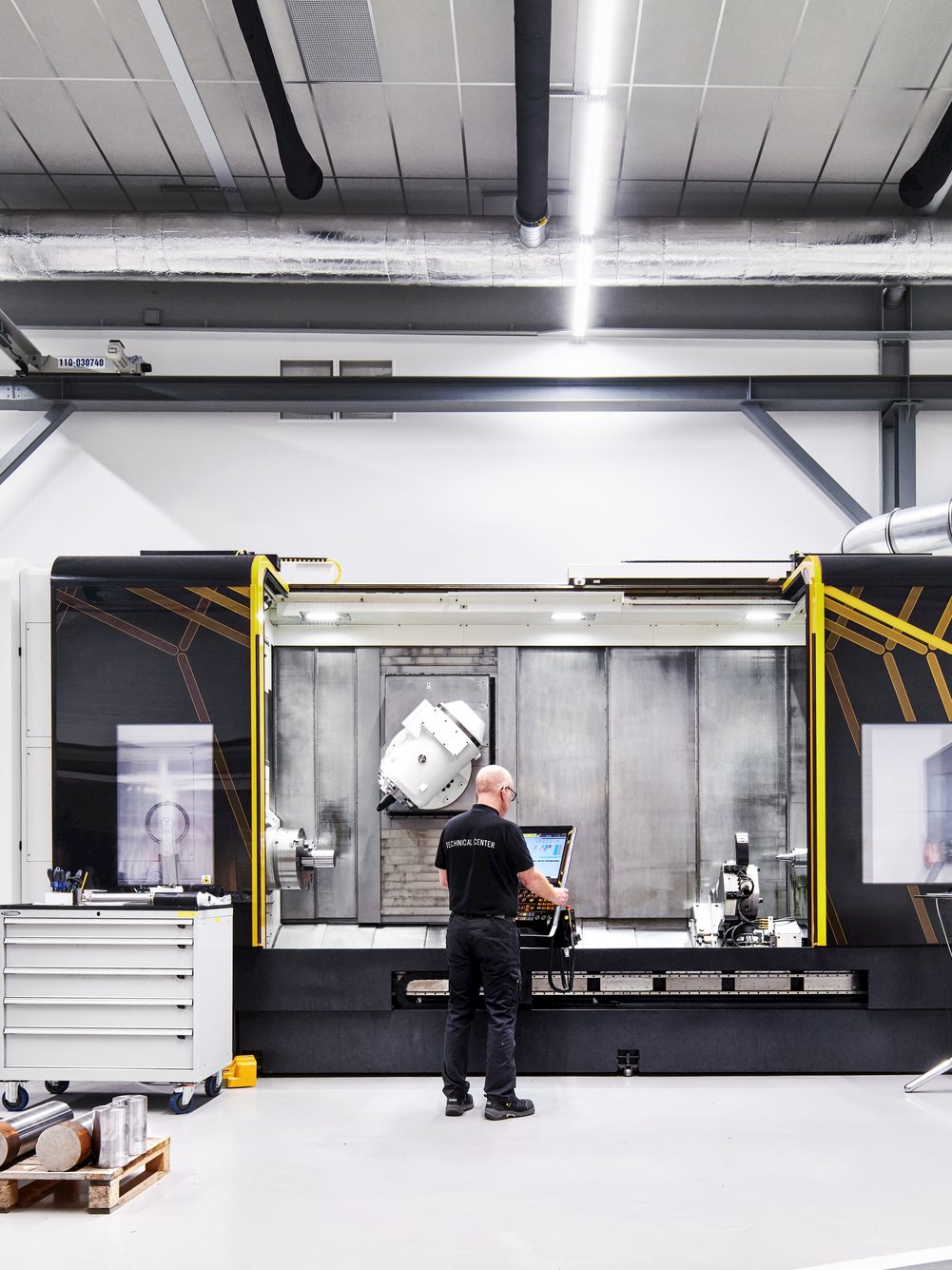
Part 2 - What you don't know about tool holders could hurt your manufacturing!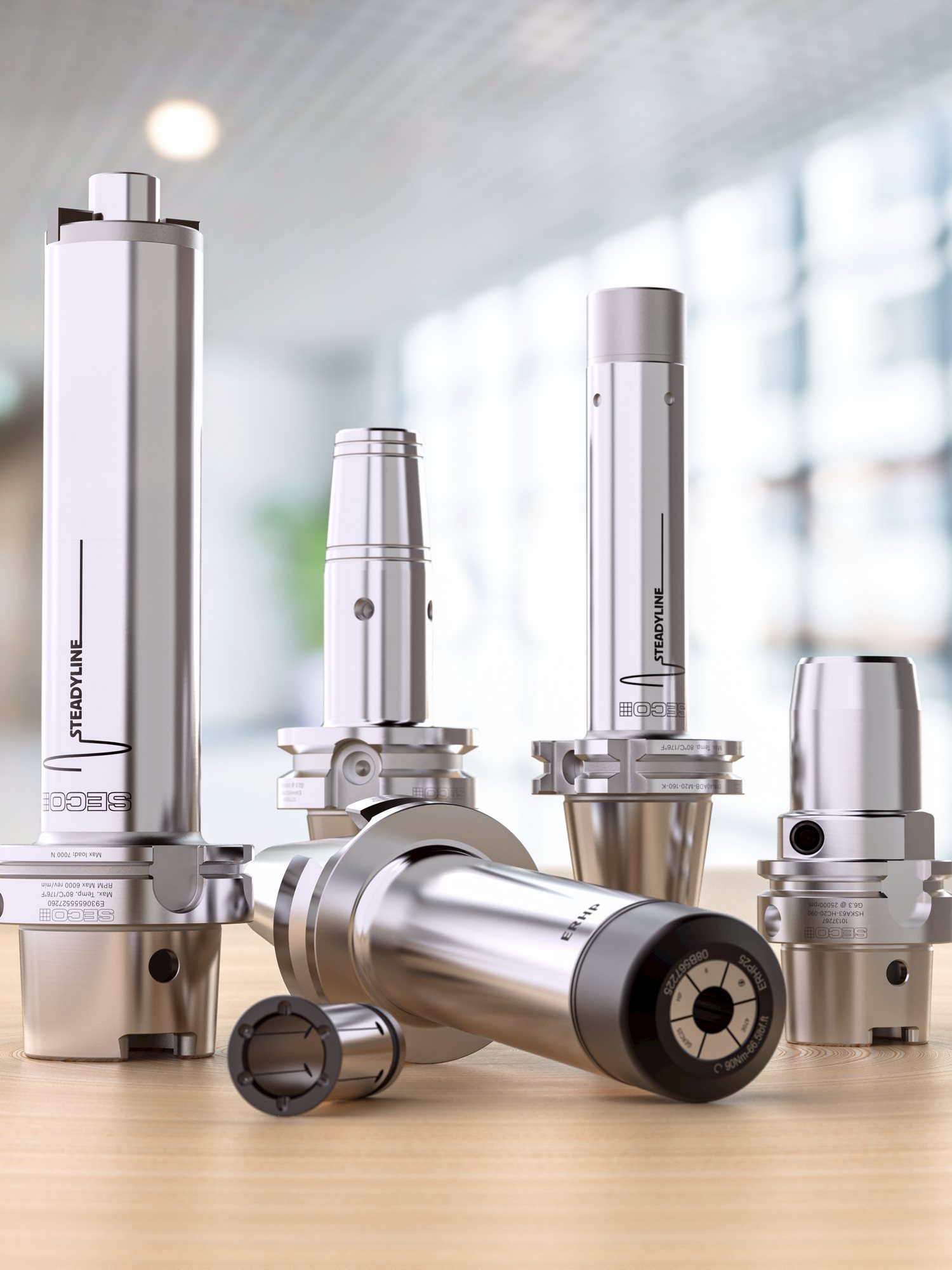
Part 2 - Take full profit of advanced cutting materials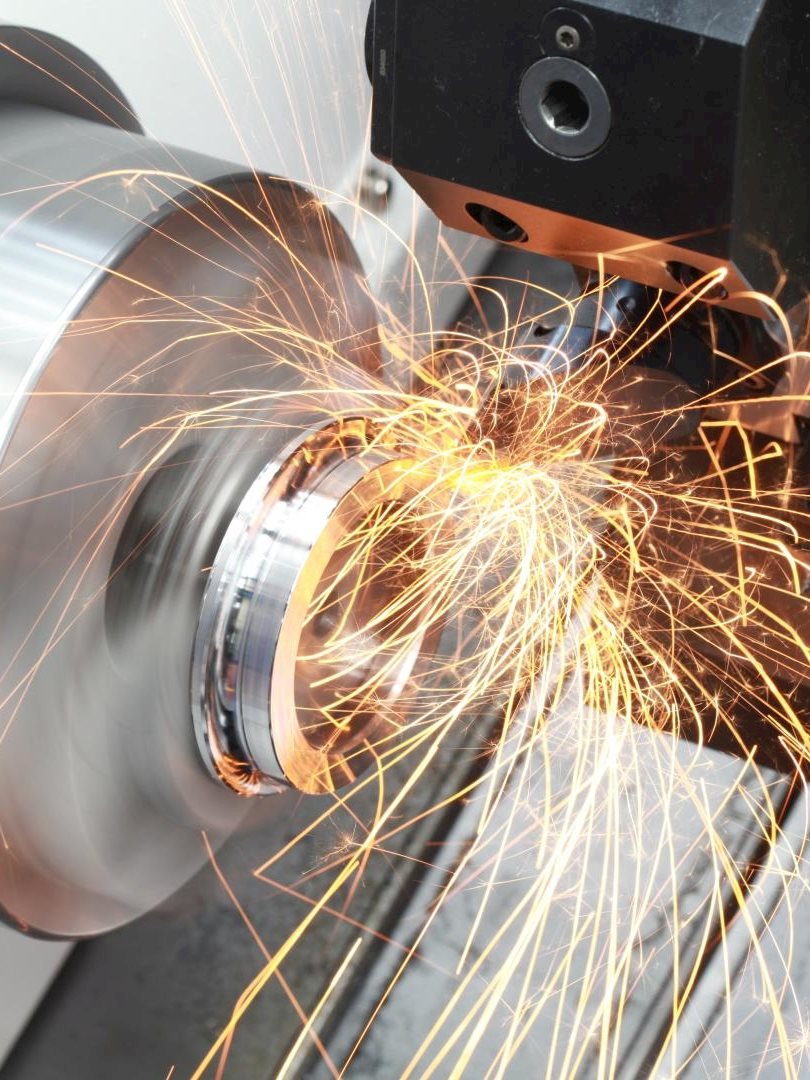
Machining Economics part 2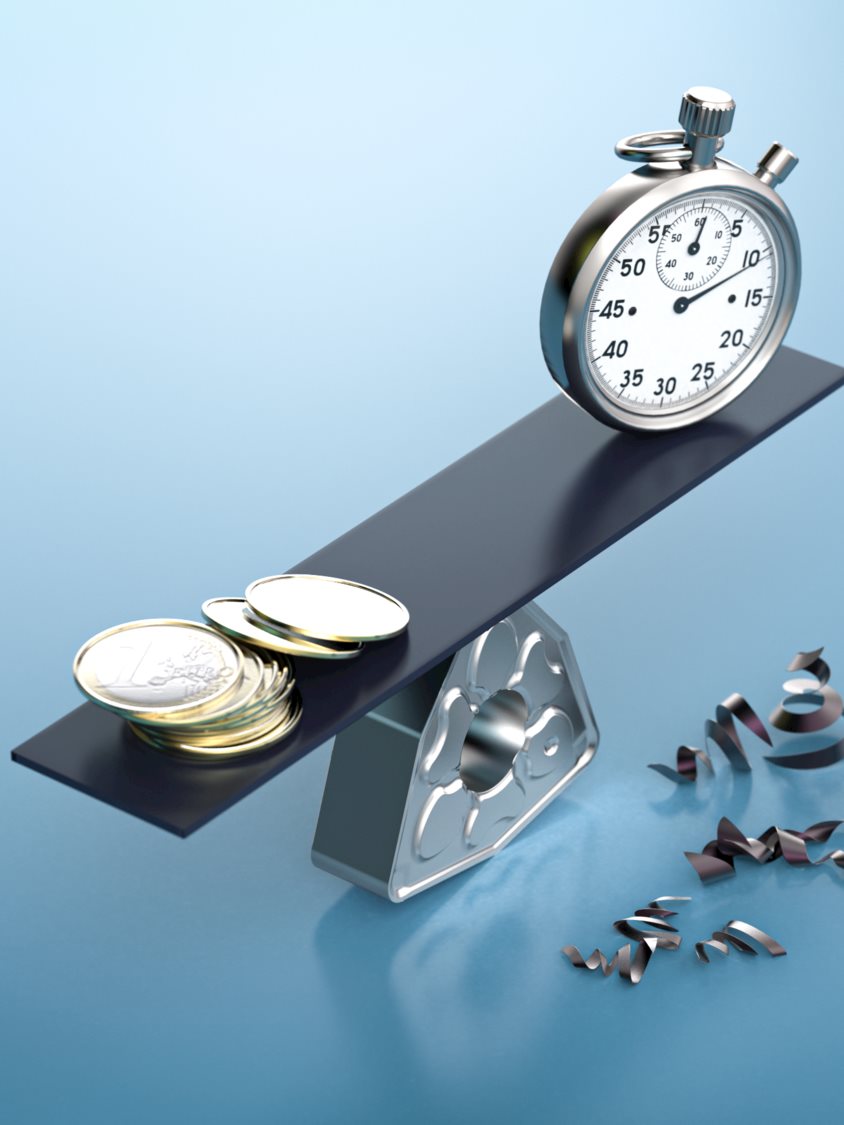
Machining Economics part 1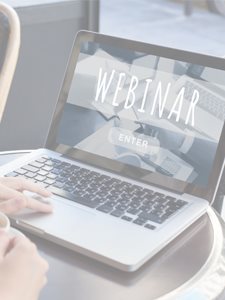
Technical Machining Strategy Part 1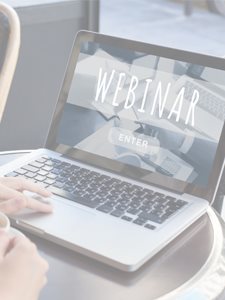
Technical Machining Strategy Part 2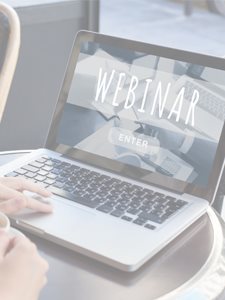
Part 1 - Take full profit of advanced cutting materials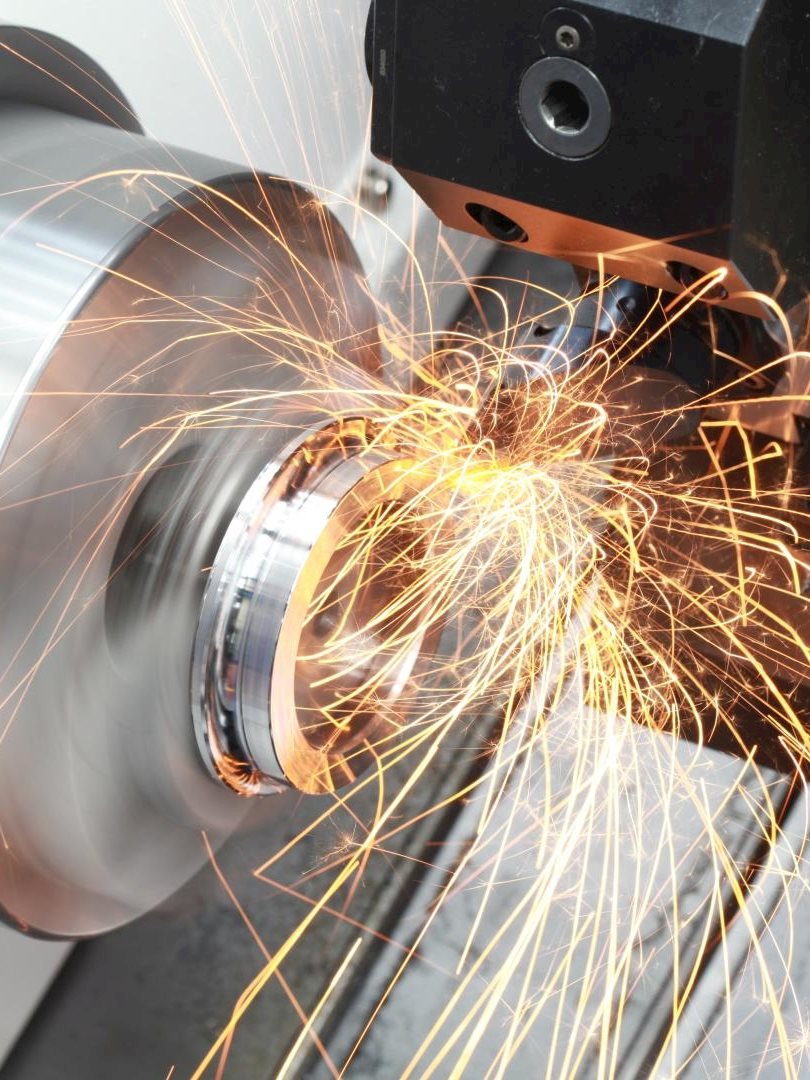
Thermo dynamical considerations on machining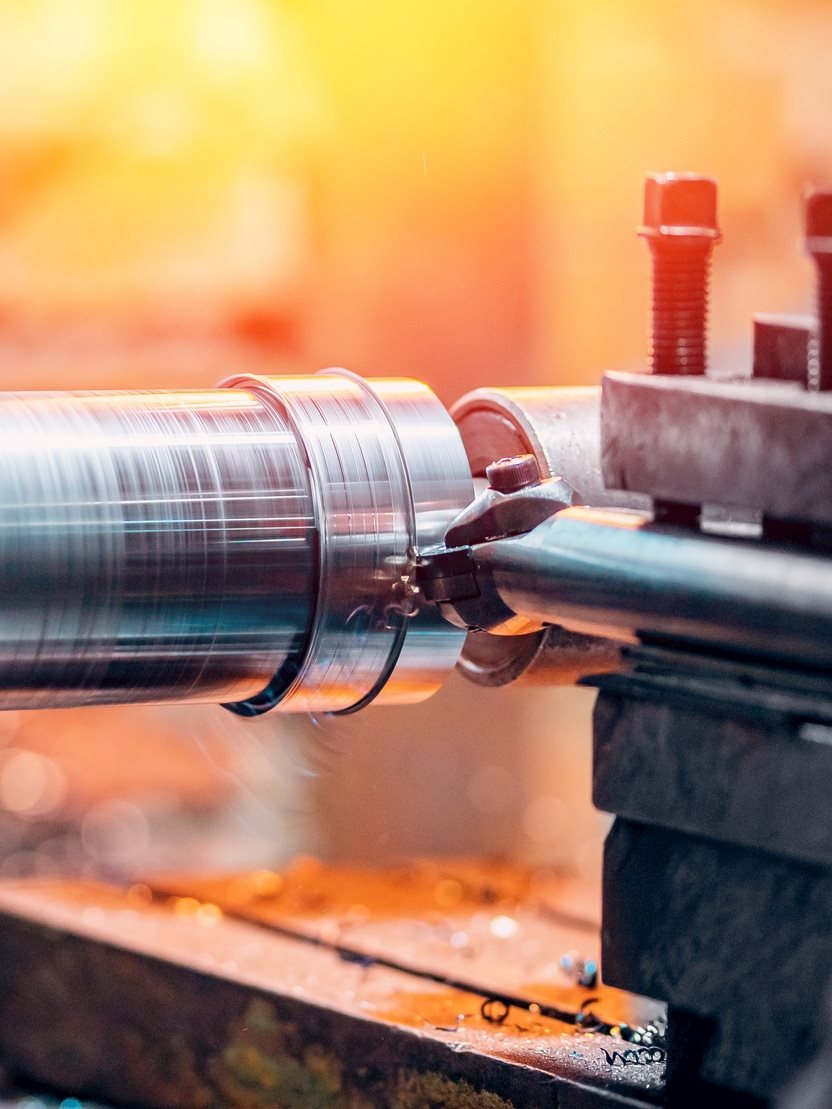
Compensation Techniques For Smart And Sustainable Machining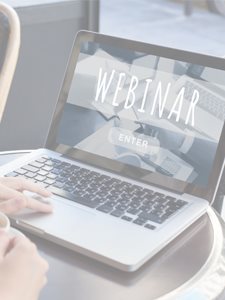
The fascinating tale of microseconds and micrometres, and machining quality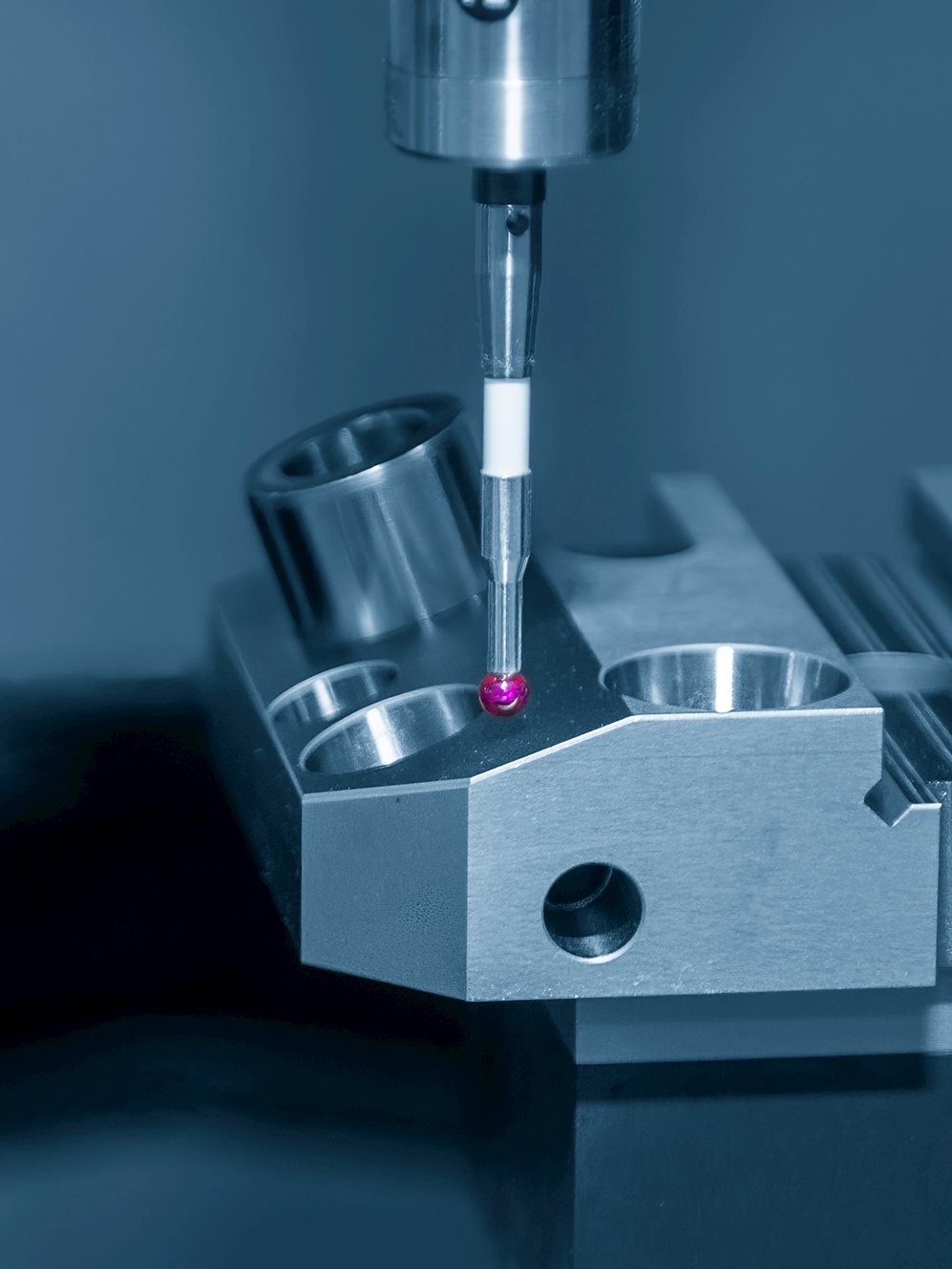
Why geometry is the undisputed champion of efficient machining?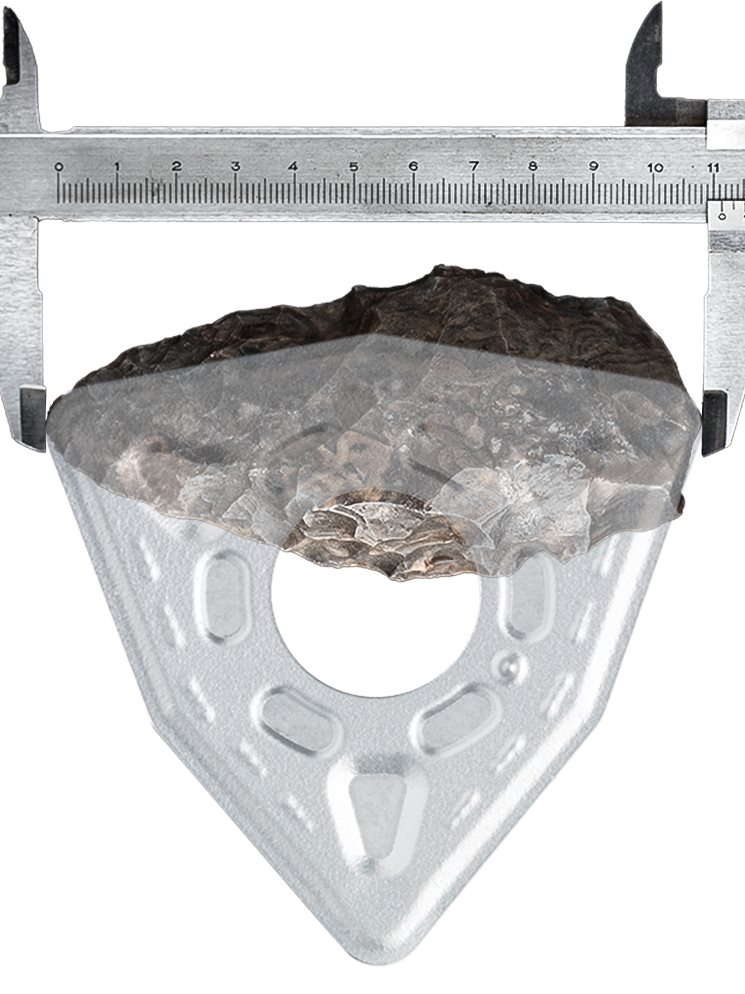
Tool life maximisation through smart tool life cycle management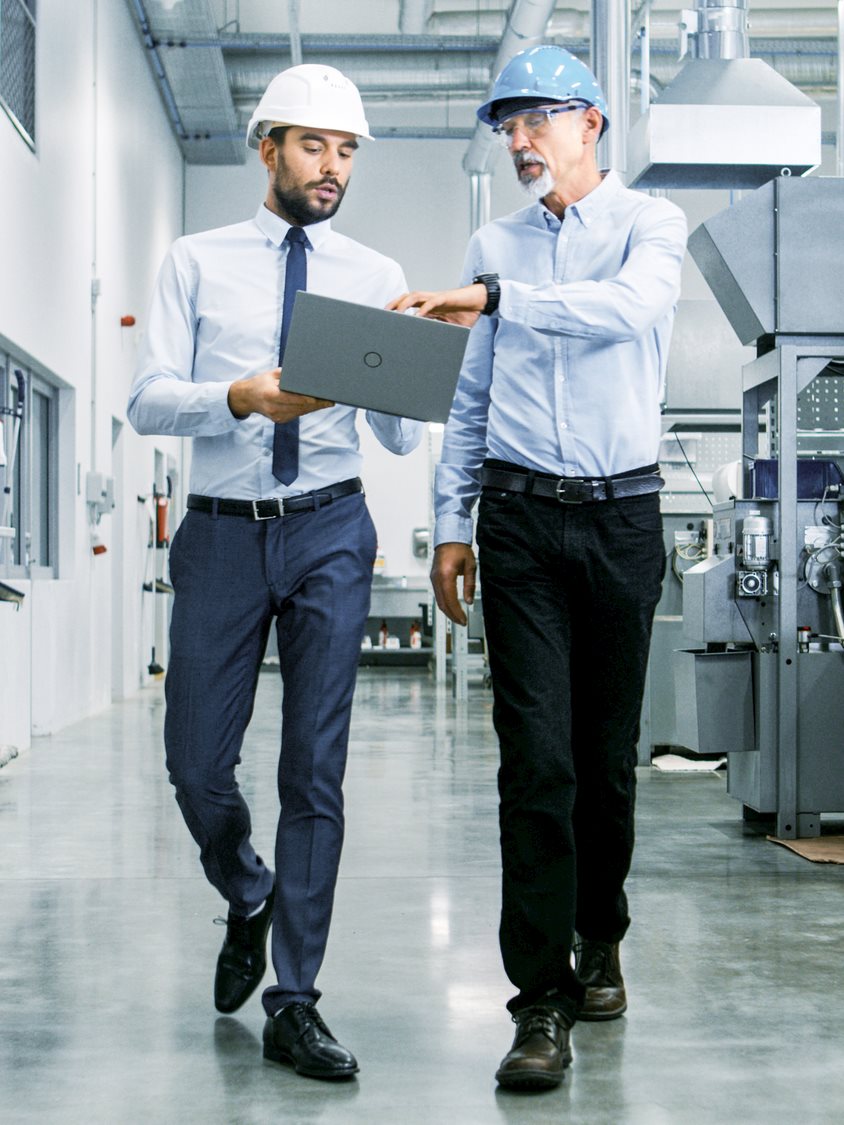
Optimised machining data for small batch production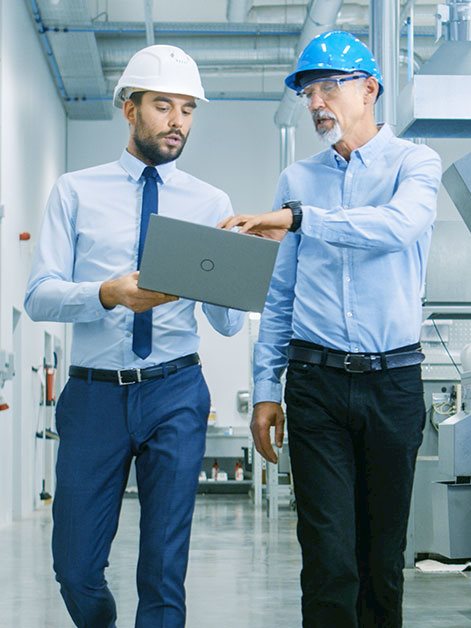
Advances in superalloy machinability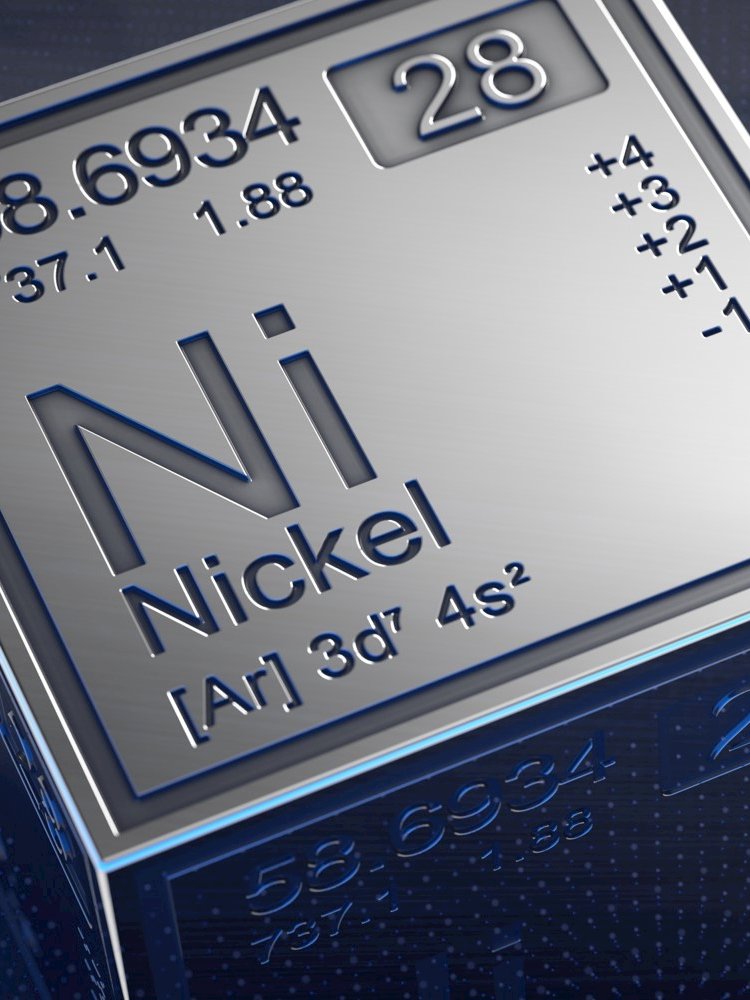
Reducing the climate impact of manufacturing utilizing life cycle analysis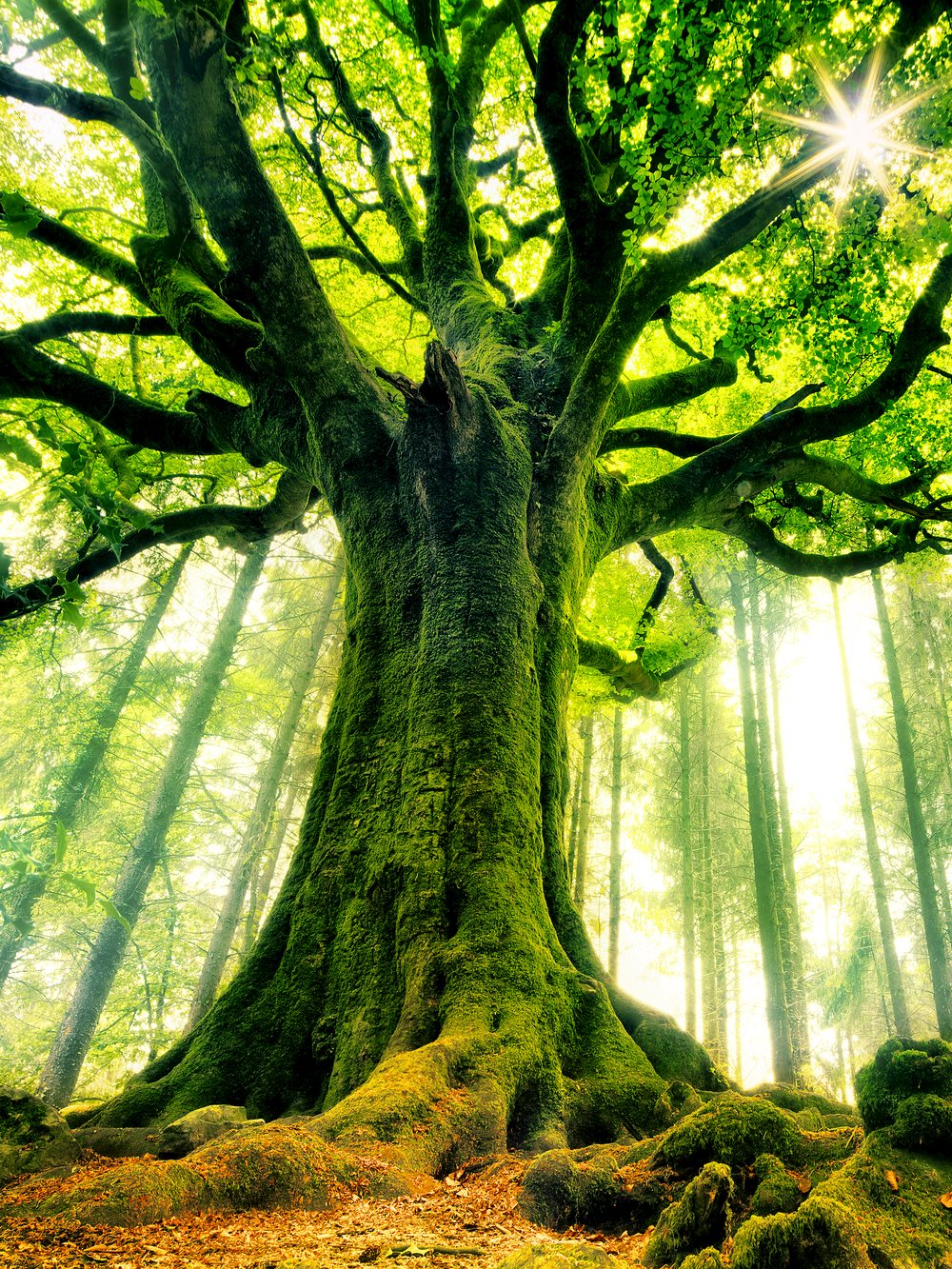
Part 2 - Structural analysis of tool deterioration: strategies for optimal machining performance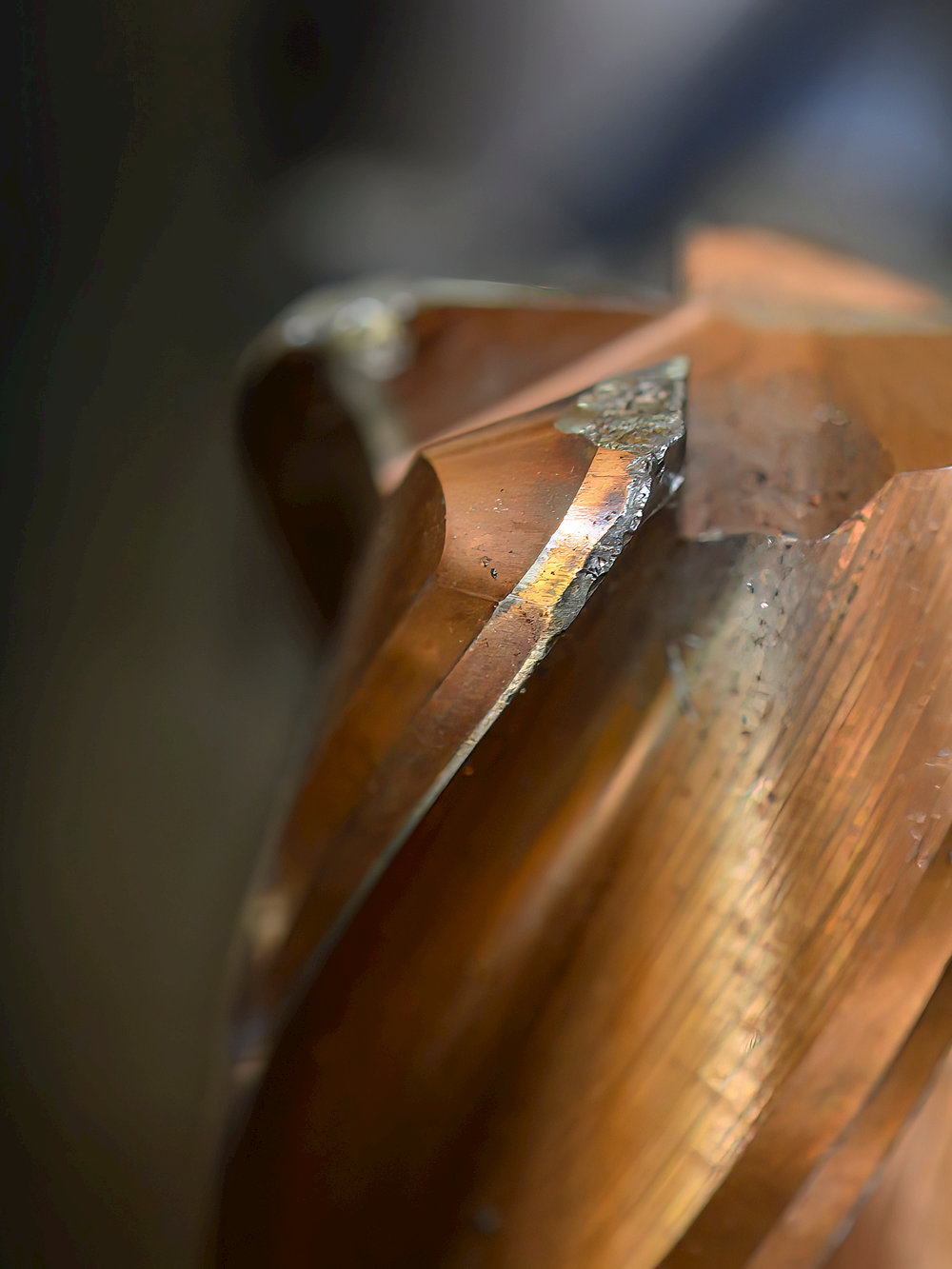