ActOn’s ‘secret weapon’ is transforming medical implants
ActOn Finishing is renowned in the aerospace and automotive industries for its surface finishing solutions. Now the UK company has entered the medical sector, where its uniquely effective process is used for medical implants, including femurs. Act On’s Managing Director Sid Gulati explains more.If the finish of an implant such as a femur, tibial tray or hip implant is not to specification it may affect its ability to attach to the bone. There is also the potential for metal fragments (burrs or splinters) which are left over from machining to break off into the patient’s body. Incorrect finishing of the implant may have a negative effect on a patient’s movement, which inevitably is a cause of great pain and discomfort and may necessitate replacement revision surgery.
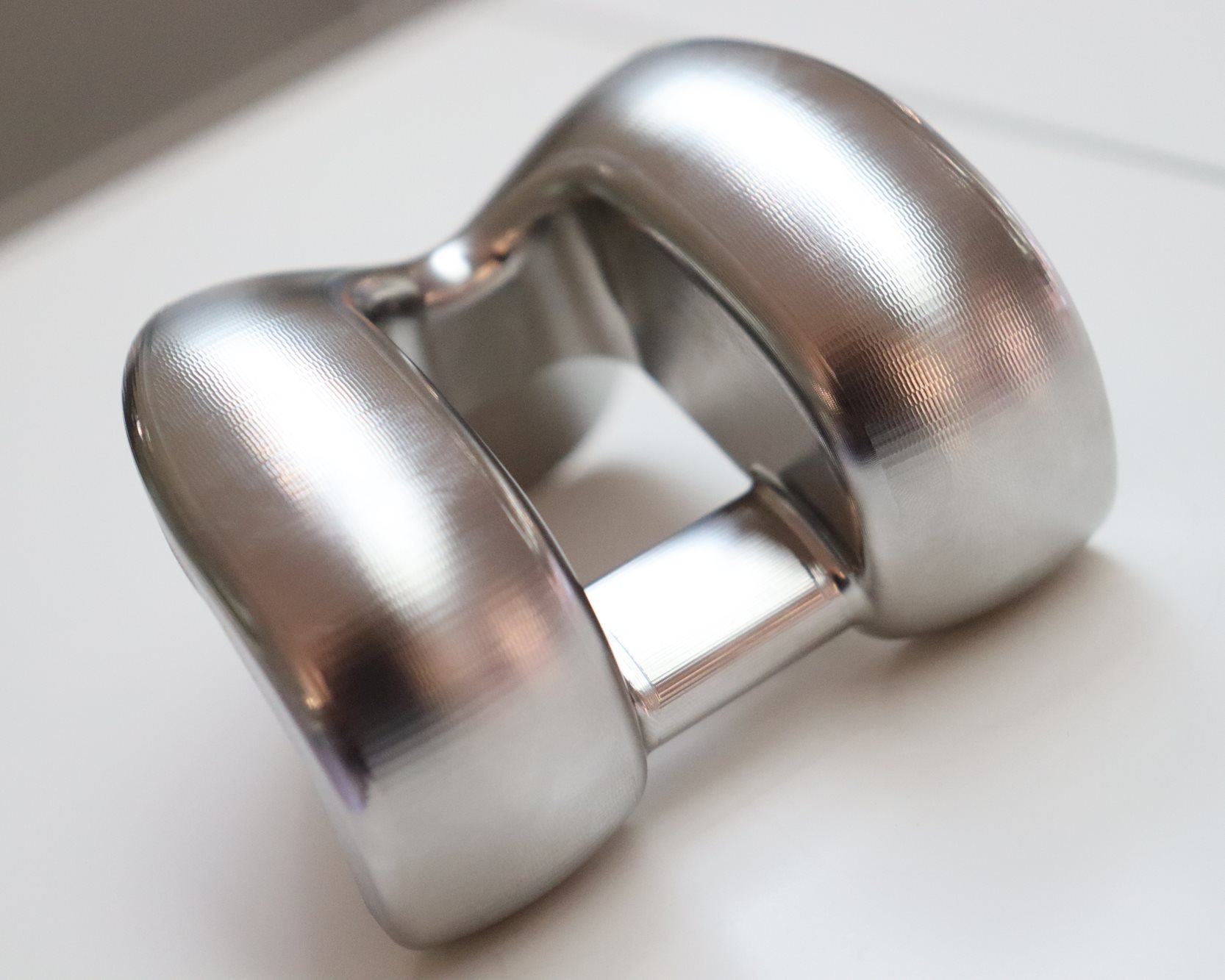
But these implants are made from hard-wearing materials such as cobalt chrome. It’s difficult to remove casting defects and machining lines, especially with high repeatability at great capacity.
It’s time-consuming, costly and uses up a lot of resources such as labor, finishing materials and water in the filtration process.
Some medical implant manufacturers bought and used their own drag finishing machines for the job. However, these require the work piece to be held in place by specially designed fixtures that then pass through the process drum where the grinding and polishing media smooth the implants. The tooling for that fixturing adds to the cost.
One implant manufacturer’s search for a more efficient alternative led them to a trade fair in 2022, where they met Coventry-based ActOn Finishing. ActOn has pioneered a unique surface finishing solution that generates consistent high repeatability from a much quicker process. It’s been used in the aerospace industry for years, but there was clear potential for medical implants too.
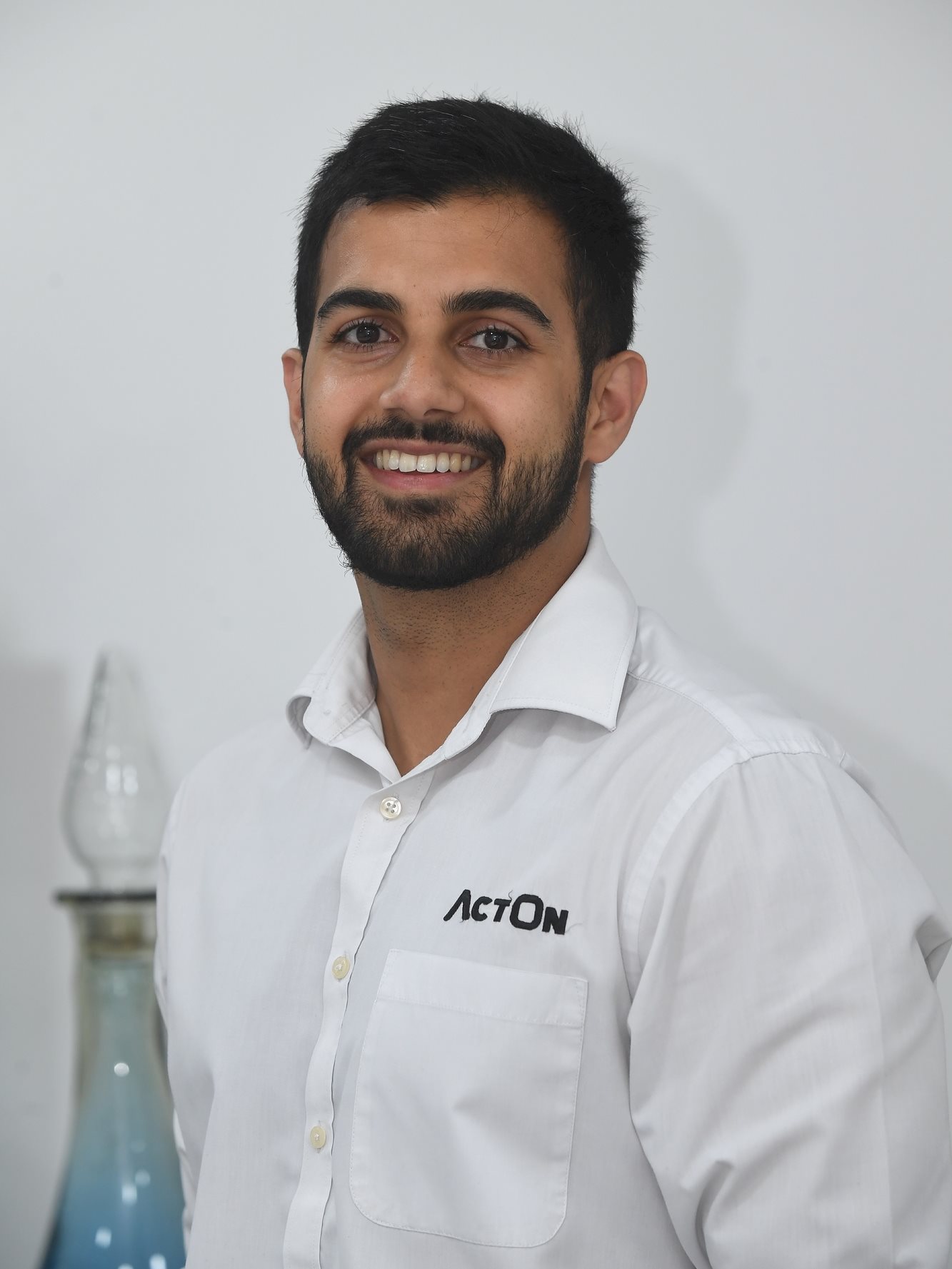
“THE PROCESS STARTED WITH AN ENQUIRY TO REMOVE MACHINING LINES ON A TIBIAL IMPLANT. IT NORMALLY TAKES THE MANUFACTURER HOURS TO DO, BUT OUR MACHINE DID THE SAME JOB IN 25 TO 30 MINUTES, SAVING WATER AND TOOLING COSTS,” EXPLAINS SID GULATI, WHO HAS BEEN MANAGING DIRECTOR OF THIS FAMILY-OWNED BUSINESS SINCE 2015.
ActOn’s secret weapon is its own patented product developed in-house. It’s called the Centrifugal High-Energy Finishing (CHEF) Machine.
“When we surface finish the femur implant in the CHEF Machine, we can use up to 16g force, and that allows us to generate results ten times faster than traditional methods do.
“So, we can remove casting defects in cobalt chrome materials very quickly without any need for tools for holding the parts in place. We also use 70% less water than traditional methods, which is better for the environment.”
Adding to the CHEF Machine’s advantages is ActOn’s partnership with Spanish company GPA Innova, which produces the DLyte machine, an electropolishing machine that automates, simplifies, and standardizes the post-processing of metal parts. Combined with the CHEF machine it gives customers a complete process with a mirror finish.
The traditional finishing of a femoral implant is a seven-stage process including deburring, descaling, surface smoothing and final polishing. Using the CHEF Machine and DLyte, ActOn reduces it to just three stages:
Stage 1, grinding: Removing most of the milling and machining lines.
Stage 2, smoothing: Blending the surface and making it very smooth to prepare for polishing.
Stage 3, polishing: Using the DLyte machine to achieve a mirror finish.
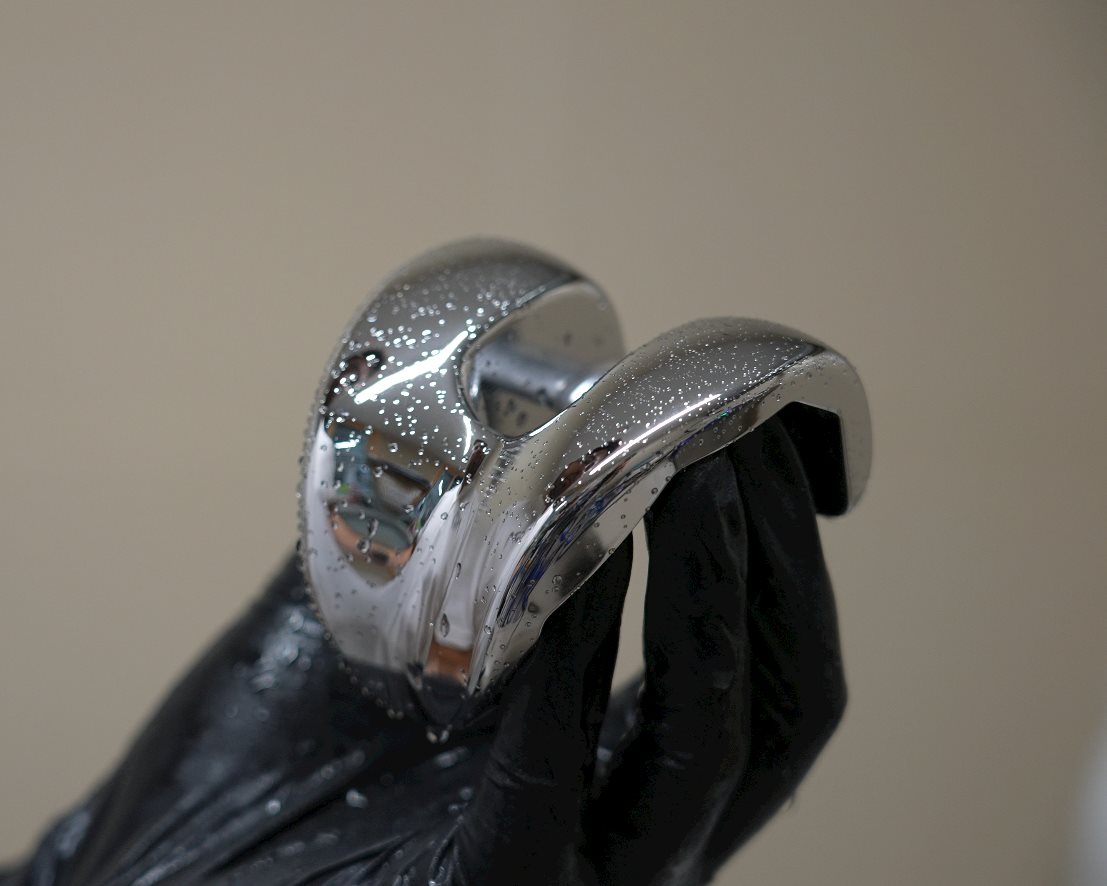
The CHEF Machine can take 12 parts per batch; the DLyte, 24. On a repeated basis the final Roughness Average is 0.04 μm, well within the targeted Ra of 0.07 μm, from an Ra start condition of 3.133 μm.
“We’re reducing the percentage of operations and manual finishing done on the components,” says Sid Gulati. “The reduction in manual polishing means there is less use of belts and less tooling consumption.”
And, of course, the less time the parts are in the machine, the less energy is consumed.
As ActOn continues to develop its business in the medical implants sector, selling its machines to more implant manufacturers or in some cases doing the finishing process for them, it has teamed up with Seco Tools. Sid describes Seco as a “bridge” between ActOn and the implant manufacturer.
“THE COLLABORATION WITH SECO TOOLS IS VITAL BECAUSE THE QUALITY OF THE MACHINING PLAYS A DIRECT ROLE IN TERMS OF THE EFFICIENCY OF THE POLISHING PROCESS,” HE EXPLAINS.
“We can give them feedback to where they can optimize the tool paths and the machining can change, allowing them to concentrate the machining process in the challenging areas of the component, which would mean less finishing for us. Having that expertise would make a big difference for the customer, not just for finishing but the production of a full femoral implant.”
Sid Gulati says the company is looking forward to further development of the successful Seco Tools partnership. ActOn Finishing is only getting started!
“We’re starting to build on our joint offer, speaking to manufacturers in Malaysia, the USA, Germany and explaining the offer. We’re also looking at other medical components and other industries.”
Andrew Fielding, Global Business Development Manager at Seco Tools adds: “Our collaboration is to address the challenges together with the goal of reducing the full process time and costs for our customers.”