Elevate Thread Quality and Cost Effectiveness with Seco's Experts
The more you know about taps, the more you can improve thread quality and improve cost effectiveness. Whether you have questions about bottoming, spiral pointed, straight flute or thread forming taps, Seco experts have the answers you need.
TABLE OF CONTENT
Inline Content - Gridded Links
Tags: 'webinar_taps_and_drills'
Max links: 1
The initial considerations when choosing the correct tap are the dimensions of the hole to be tapped and whether it’s a blind or through in nature; the desired thread type, size and tolerance; and the characteristics of the workpiece material involved. Then, optimizing your particular threading application will depend on tap geometry, flute and chamfer type.
The type of hole being tapped dictates the choice of tap geometry. Tap flute styles include straight, spiral and combinations of straight flutes and spiral tips
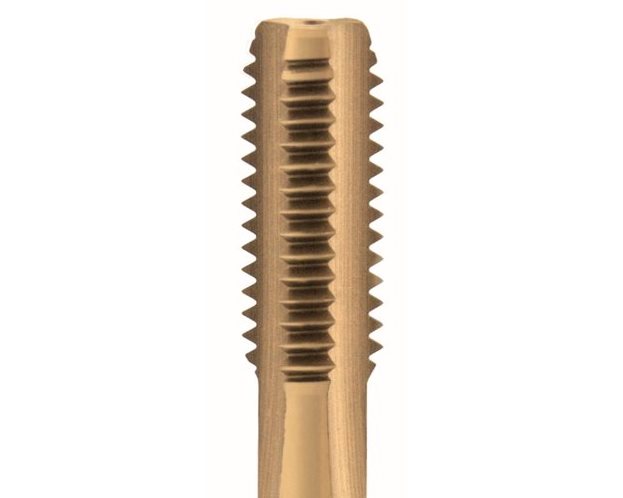
- Straight flutes: These taps are mainly recommended for part materials that generate short chips. The tap grooves evacuate only some of the chips, which slowly move along the axis, which is why they are well suited for through hole applications. These taps handle thread lengths up to 1.5x tap diameter.
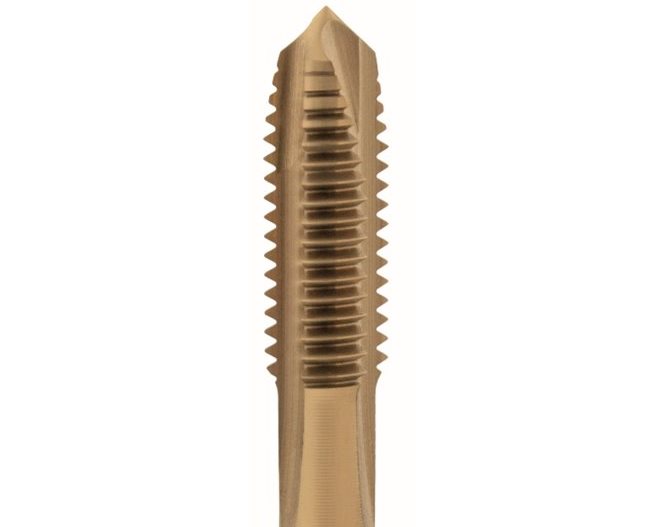
- Straight flutes with spiral point: Designed for through holes, these taps thread the full length of a hole. Used together with a B-type chamfer (see chamfer section below), the spiral point of these taps moves tightly squashed chips in the direction of feed and prevents the grooves from clogging. This also allows coolant to more freely reach the cutting zone. Theses taps generate thread lengths up to 3x tap diameter.
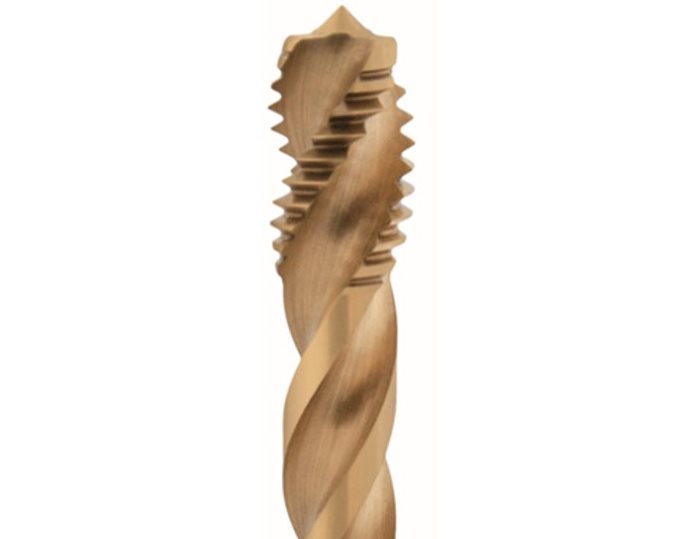
- Spiral flutes: For workpiece materials generating long chips, spiral flute taps provide good chip evacuation in the direction from the hole toward the shank. Depending on the hole diameter, these taps can produce threads of up to 2.x tap diameter.
The tap chamfer is the tapering of the threads that distribute the cutting action over several teeth. Typically, the type of hole to be tapped determines the right chamfer type to use. There are three common chamfer types: B, C and E.
Chamfer type B = 3.5 – 5 x threads. Long chamfer: Provides high torque and the best surface quality. This chamfer generates thin chips and low pressure at the chamfer while ensuring longer tool life. Most commonly used for spiral point taps.
Chamfer type C = 2 – 3.5 x threads. Medium chamfer: Characteristics of this chamfer include low torque, good surface quality, normal chip thickness and medium pressure at the chamfer. This is a standard design that is rated for good tool life and most often used for blind holes and with spiral flute taps.
Chamfer type E = 1.5 – 2 x threads. Short chamfer: For low torque and good surface quality. The chamfer produces thick chips and high pressure at the chamfer. It is considered an extreme design used when clearance in the bottom of a hole is limited.
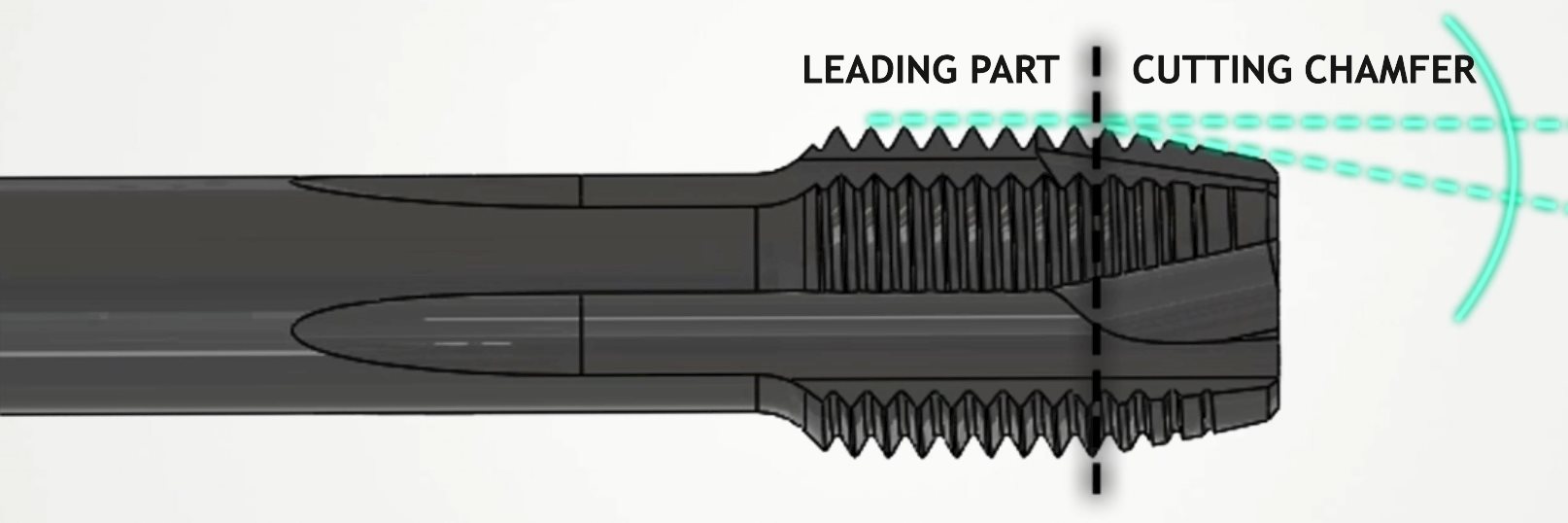
What is the difference between a cutting tap and a forming tap?
Taps form threads by either cutting and removing material from a hole or by pushing and forming the material into the desired shape without removing material. There are advantages and disadvantages to both methods.
A number of strategies are used to improve tap performance. Hard tool coatings increase lubricity for better chip flow and evacuation, minimize built-up edges, improve surface finishes and reduce abrasive wear. Coatings also harden the tap surface and provide a thermal barrier between the cutting edge and the workpiece.
Coating material, most often titanium nitride, is applied to the tap’s cutting edges via a process called Physical Vapor Deposition (PVD). PVD uses a physical process such as heating or sputtering to produce a vapor of material, which is then deposited on the object being coated.
Smooth PVD coatings feature low coefficients of friction along with high hardness and wear resistance that contribute to tapping accuracy and extended tool life. Other coating materials such as titanium carbonitride provide advanced resistance to abrasion, and alumina compounds have greater resistance to high temperatures.
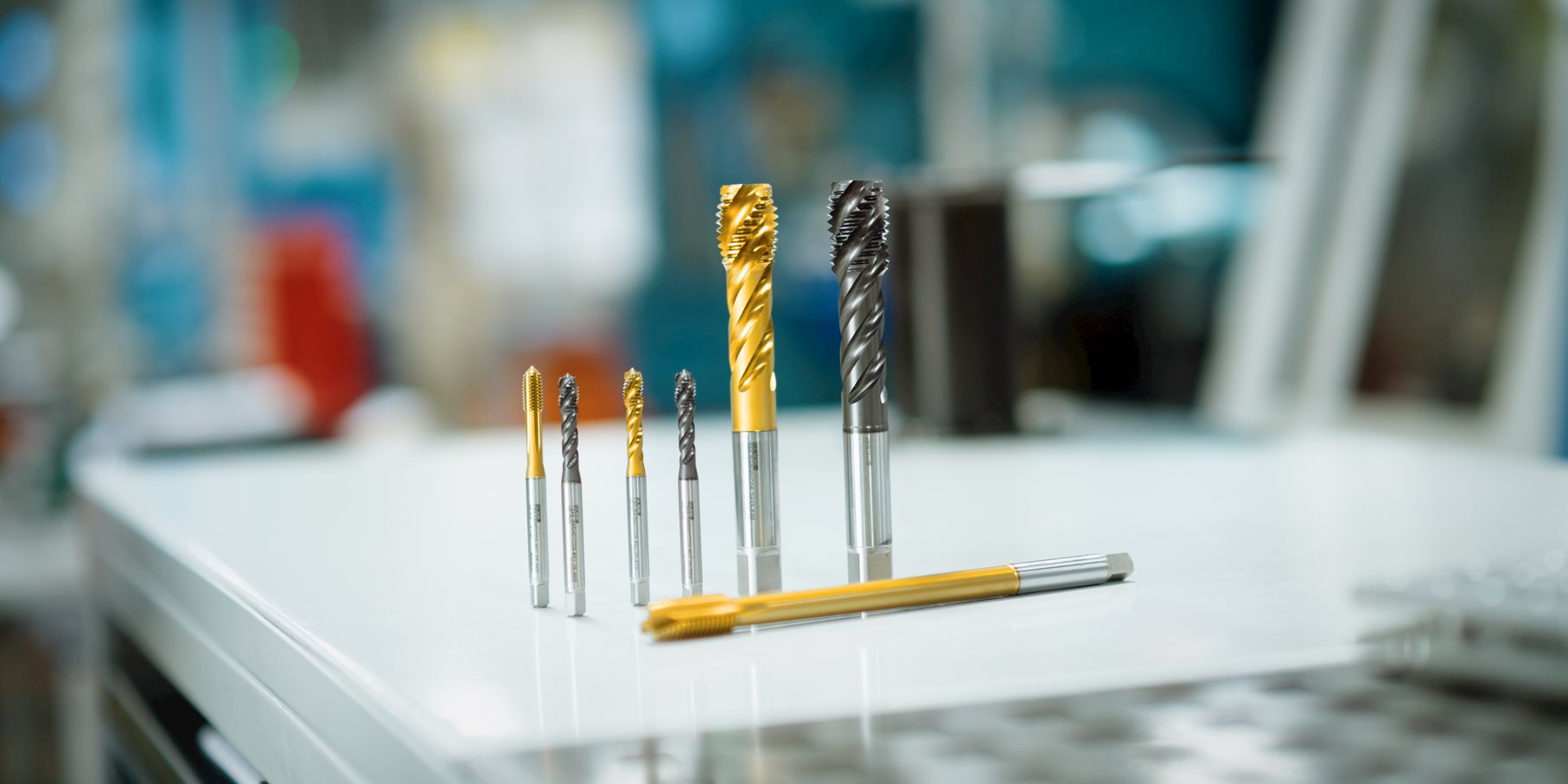
Is coolant necessary, and how should it be used?
Coolant and lubrication during the tapping process significantly improves tool life and thread quality, especially where friction increases cutting temperatures in tough workpieces like alloyed or stainless steels.
Typical emulsion coolants for tapping contain 8-12% oil. An alternative, Minimum Quantity Lubrication (MQL), offers good lubricating and cooling qualities while it also limits environmental and health issues associated with oil-based coolants. Threading fluids and pastes are generally applied by hand and are useful when there is no opportunity to apply coolant continuously.
The best option for tough materials is to use through-cooling tools with cooling channels that direct coolant directly to the cutting zone. For different levels of performance, SECO offers its T32 and T34 lines of cutting taps and T33 selection of forming taps that meet a shop’s specific threading needs.
For tapping blind holes, consider an internal axial head coolant system, while through hole tapping is best suited to internal radial head systems.
Optimize your Thread tapping with our guide/whitepaper Recommended tap diameters for specific hole sizes are typically available from catalogs and online sources. Tap shank dimensions, however, depend on the hole’s location on the part. Reinforced shanks are effective when access to the hole is unobstructed, but when a hole is close to the part wall or other features, it may be necessary to choose a reduced or extended shank length to avoid a collision. Learn more here |
Overall shop cost-efficiency and sustainability involves balancing tool performance versus versatility. While performance favors tool life and throughput, high-performance taps are expensive. Versatility, while controlling inventory costs, especially in high-mix/low-volume manufacturing, might not stand up to challenging applications and specialized processes like heat-resistant materials.
However, tools that can be applied efficiently on a variety of workpiece materials reduce inventory costs and simplify tool choice.
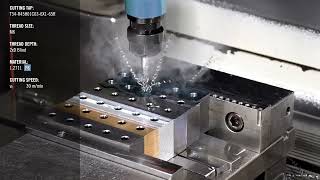
What are some common tapping issues and solutions?
Threads that are too tight with tolerances lower than expected is usually found in threading stainless steel or alloy steels that generate high temperatures during machining. When the tap stops at the bottom of the hole, the material begins cooling, and thread size decreases.
A specially coated, high-performance tap such as the Seco T34 line with a top layer made of carbon will eliminate this problem. Also using the recommended coolant along with the proper tool geometry will combat this issue.
In some cases, spiral flute taps without proper edge preparation held in a flexible floating tool holder can be pulled into a hole faster than anticipated, resulting in threads of incorrect size and pitch.
To correct this condition, select a tap with a lower spiral angle and use a rigid tool holder or one with minimal axial compensation.
To improve chip formation that will allow easier evacuation, increase cutting speed. However, increased cutting speeds will affect tool wear and life, and that will require regular, methodic tool inspection.
Initially applying a center drill (only when using drills made of high-speed steels) at the hole site enables accurate positioning for a hole drilling operation by a correctly sized tap drill. Drill diameters will be different for taps and forming taps. Consult the manufacturer’s table for the drill diameter that correlates to the intended tap size. SECO forming taps have laser markings on their shanks specifying the correct drill diameter.
While specific drill sizes are approved for certain tap sizes, it sometimes helps to use a slightly larger drill than recommended. Using a 5.1 mm-diameter drill in place of a recommended diameter of 5 mm, for example, will remove more material and lessen stress on the tap. Using the largest tap drill diameter possible lowers tapping cutting force and benefits tool life.
When hole drilling is complete, hole diameter should be checked using a plug gage to confirm that the hole meets dimensional and tolerance specifications.
Chamfering the hole mouth before tapping will ease entry of the tap into the hole and improve chip evacuation. The final step in the tapping operation is checking thread accuracy with the appropriate thread plug gage.
One of the biggest concerns during the tapping process is tap breakage. Generally speaking, tapping is often the last operation on a part, and shops have already invested considerable machining time (and expense) into the process. Scrapping a part at this point is a serious cause for concern.
Carefully match tap geometry, part alignment and machine tool.
Follow tap manufacturer’s cutting parameters and recommendations.
Inspect cutting edges at predetermined intervals as flute damage can result in poor performance as well as breakage.
Check hole surface quality and diameter before tapping.
Be attentive to changes in machine power consumption and out-of-the-ordinary noises.
Tapping with a machine tool requires closely matching the feed rate of the tap into the hole with its radial rotation. Using a floating tap holder can accomplish this goal. The holder’s built-in float allows the tap to be pulled in or out at a feed rate that is proportional to the spindle speed and pitch.
For maximum threading consistency, machine tool makers offer rigid tapping options that automatically match tap feed rate, rpm and thread pitch and enable users to maximize the tap’s full potential while decreasing the chances of breakage.
What kind of materials are used and what kind of materials are machineD?
With more than 800 unique products, Seco threading taps can machine blind and through holes in a broad range of materials including ISO P (steels), M (stainless steels), N (aluminium) and K (cast iron) materials. To meet virtually all applications and machining parameters, we use a variety of materials for our taps, including:
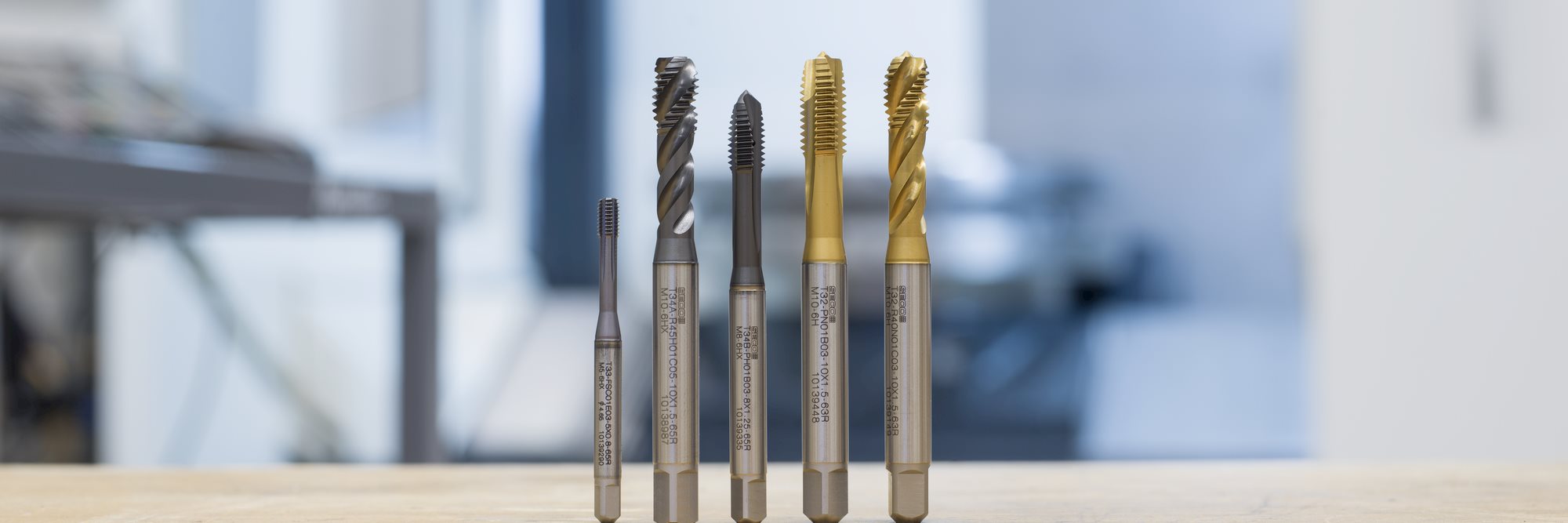