Successful reaming with Nanojet
Precision is important in the whole manufacturing chain – and also in one of the last steps: hole reaming. Read more about how those precision tools are manufactured.It’s common knowledge that chip control is essential in all holemaking applications – also in reaming - and especially in long-chipping material, such as stainless steel or titanium.
Reaming is used in various manufacturing applications to enlarge or smooth the inner diameter of a hole in a workpiece. It’s often one of the last steps in machining and can decide over output or having to scrap the workpiece. And the precision lies in its nature – the purpose of reaming is indeed to improve shape and size accuracy and the surface quality.
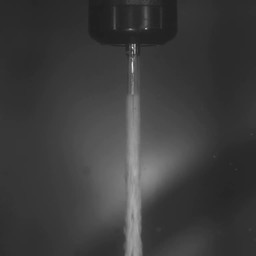
The solid carbide Nanojet Reamer was launched in March 2024. Its design and production originate in La Tour-du-Pin (Isère), the site is fully dedicated to reaming tools. "The new reamer is an evolution of our solid carbide Nanofix reamers. We wanted to eliminate the additional body for coolant delivery," explains Jean-Bernard Hantin, Seco Tools Reaming product manager. “We didn't want lateral cooling, but rather to each flute of the tool," continues Hantin. Ground bars with extruded holes are delivered to the reaming site. "Our challenge is to calibrate the cutting diameter and sharpen the reamer with flutes perfectly indexed to the coolant holes," emphasizes Lilian Rimet, director of the Seco site.
Nothing is left to chance with the production of the Nanojet reamer. During the fully automated production each product is runs through different checkpoints:
"We check the diameter, then we verify under a magnifying glass that there is no chipping," details Rimet. An innovative coolant outlet delivers a precise and powerful coolant flow directly to the cutting zone for better chip control, eliminating the risk of jamming. Dimensional control is ensured on a laser micrometer. "The tool passes a laser beam to give the dimension as precise as to the tenth of a micron," notes Jean-Bernard Hantin.
Most Nanojet requests concern custom design. "If we stock all the round sizes of our reamers, we can also provide the reamer as quickly as possible in the requested size," affirms Rimet. Hence a strong automation of the Nanojet production process. "We can maintain a tolerance on the reamer that is smaller than the size of a red blood cell," continues Jean-Bernard Hantin – which leads to a tolerance of four to six microns, whereas a red blood cell measures 8 microns. "To achieve this, the production workshop is temperature controlled to provide stable air condition, the cutting oils are refrigerated and centrally distributed to each machine.
Before launching the product “field tests” had been conducted on customer sites and brought good results.
And to cite the case of a customer in Italy, who produces injection pump bodies.
"He was having difficulties managing chips on the reaming of a hole that opened into another, smaller diameter hole.
With Nanojet, he increased tool life by more than 50% compared to his previous reamers, and productivity by more than 50% by allowing him to increase his feeds."
The customer was so satisfied that he ordered a hundred reamers, confides Rimet, noting that the customer had previously struggled to maintain the required surface finishes.
The grade for the reamer is RX2000, "a versatile grade for most materials, delivering good performance," says Lilian Rimet. For even the most demanding cases, about ten optimization grades have been developed.
To choose the most suitable grade, the MyDesign configurator will guide you based on the material, hole tolerance, and desired surface finish.
Inline Content - Survey
Current code - 5fce8e61489f3034e74adc64