Stop Overlooking Constant Chip Load and Feed Rate
Our specialists are ready to help get you the right tools to help you succeed in hard milling applications.One of the most overlooked concepts when it comes to hard milling applications is maintaining a constant chip load/feed rate.
Complex surfaces and cutter paths used in the mold and die industry cause machine tools to rapidly fluctuate feed rates resulting in a drastic loss of tool life. Keep in mind, feed rates will always fluctuate unless machining in a straight line. When machining complex surfaces, take into consideration that machine tools do not reduce rpm in conjunction with feed rate reductions.
A good rule of thumb is if the programmed feed rates cannot be maintained for 80% of the time, the average feed rates need to be reduced. Subsequently, feed rates and rpm need to be reduced in the program. For example, programmed rpm is 30,000, and the feed rate is 150 ipm. However, the average maintained feed rate is only 75 ipm, so for ultimate success, the rpm needs to be reduced to 15,000. This reduction in rpm can increase the tool life upwards of 50% while having a negligible impact on cycle time.
The manufacturing industry can seem unpredictable, but you can get process reliability and stability with the right tooling technology and processes. Some options for successfully hard milling complex 3D components are the MBZ215 ball nose series of end mills and the MZN410R/510R high feed bull nose end mills from Niagara Cutter, a Seco Tools company.
Click here to find out more information about these tools and other various machining solutions from Seco Tools.
HOMERelated content
Milling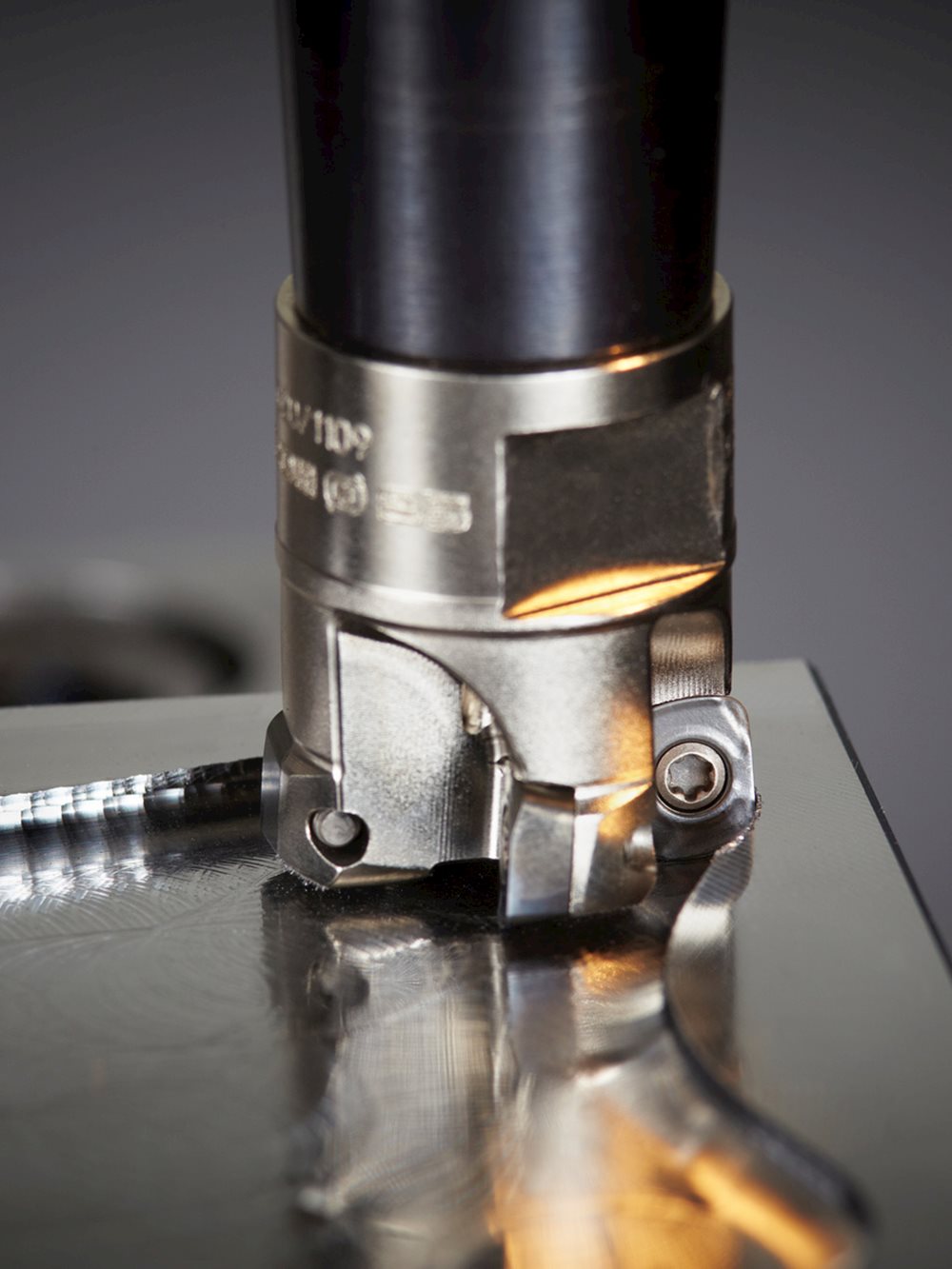
Machining Navigator / Product Catalog Milling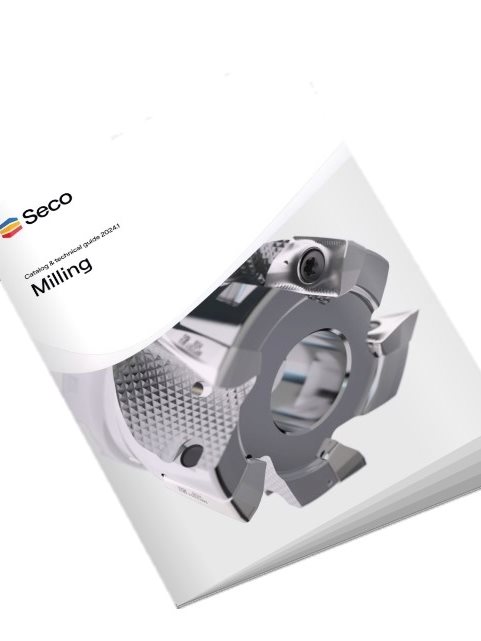
Mold & Die End Mill Expansion Introduction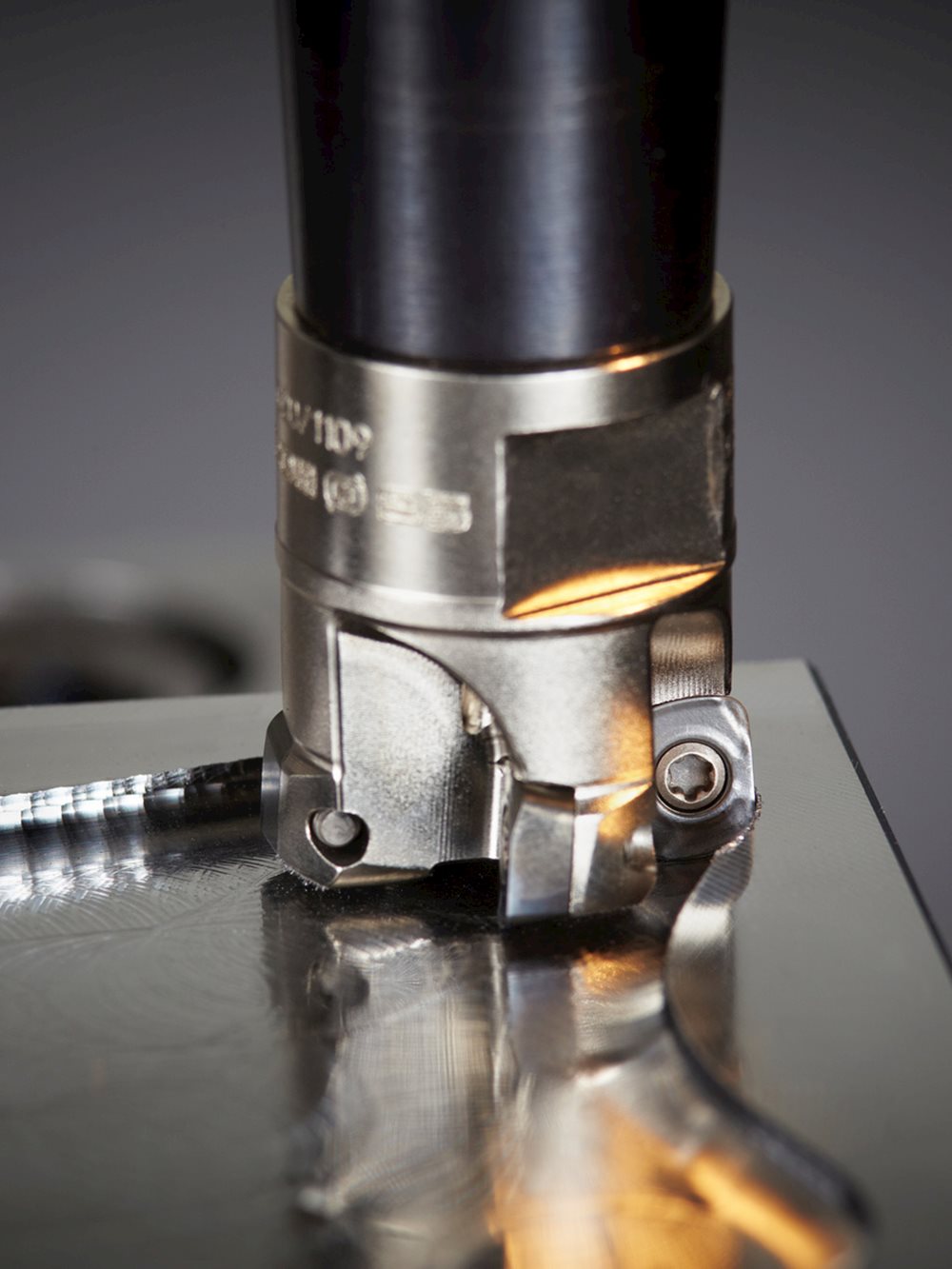
Seco Adds Larger Insert Sizes to T4-12 Square Shoulder, Helical Milling Cutters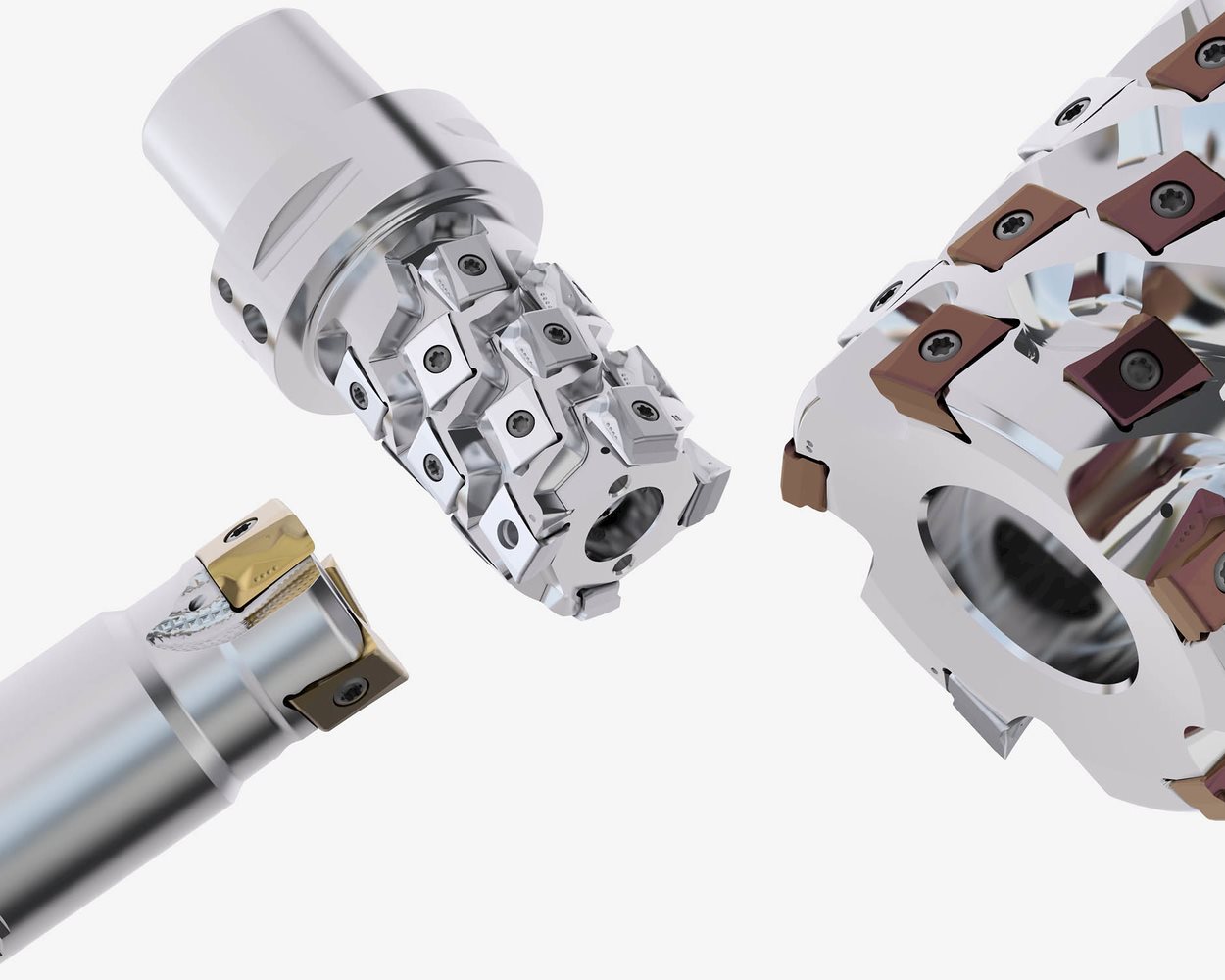
A245 - High Performance - Square and Ball - Aluminum - 2 Flutes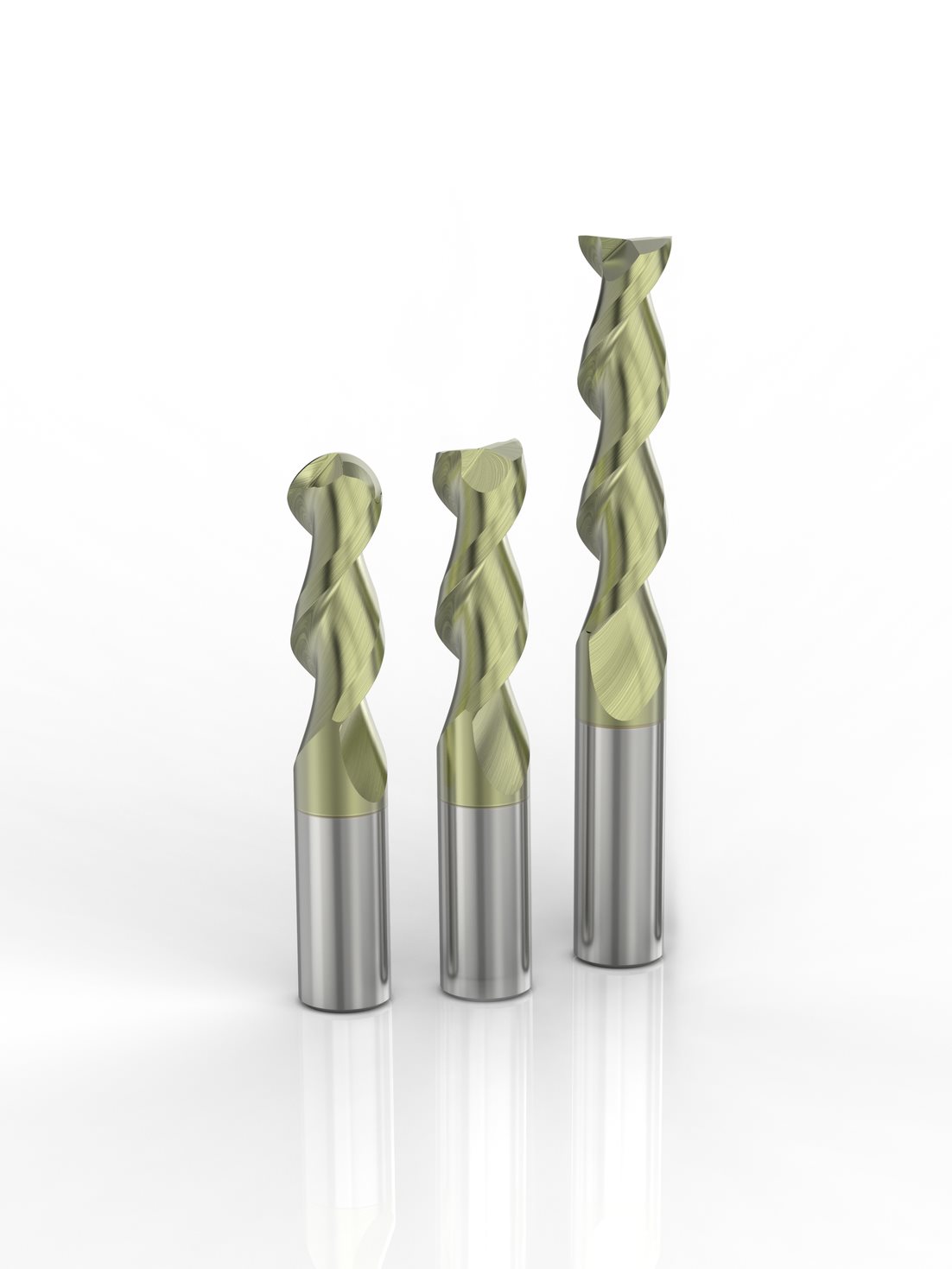
A345 - High Performance - Square - Aluminum - 3 Flutes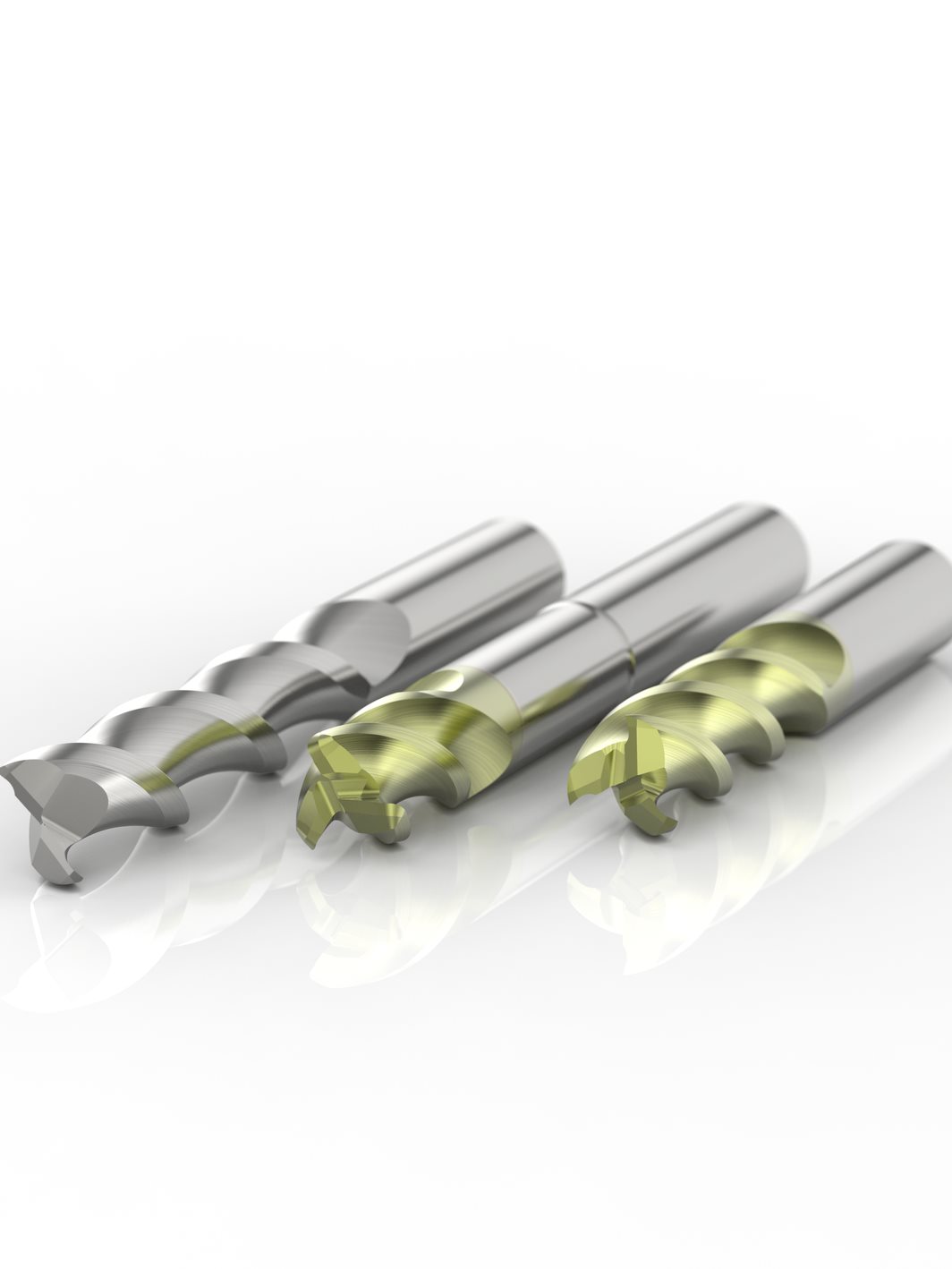
High performance Machining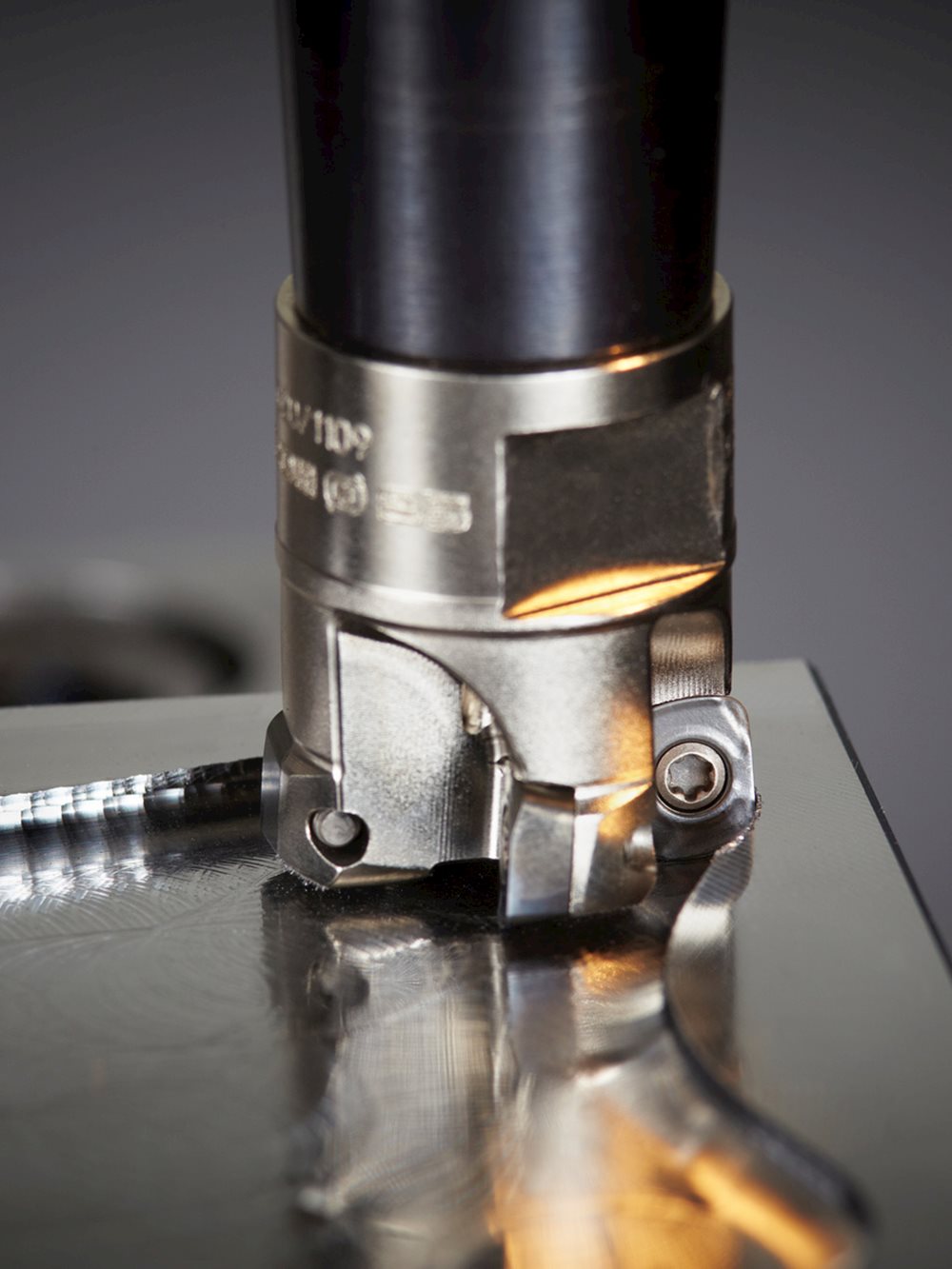
Tips for Successful Hard Milling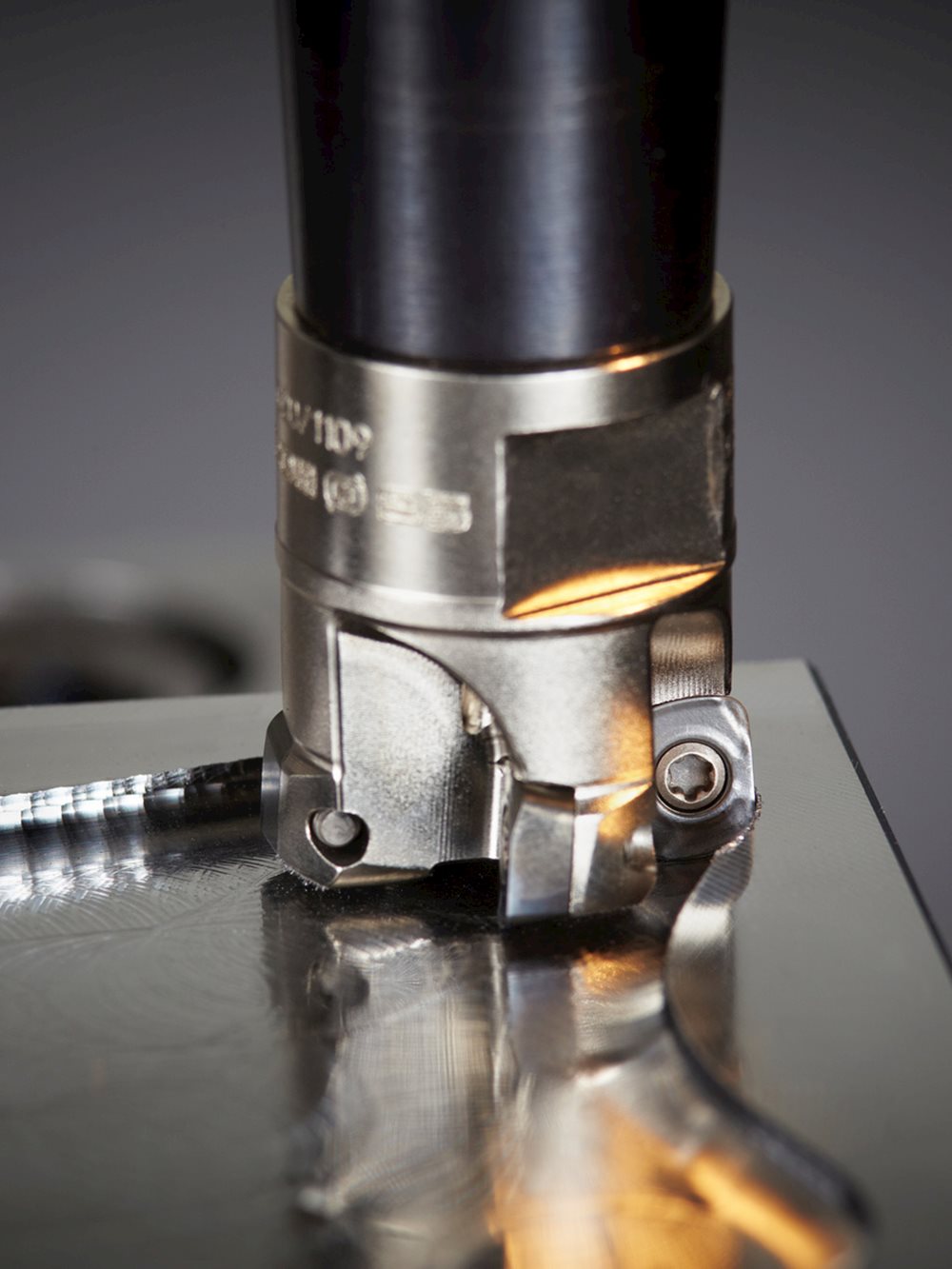
AN230R - High Performance - Square - Aluminum - 2 Flutes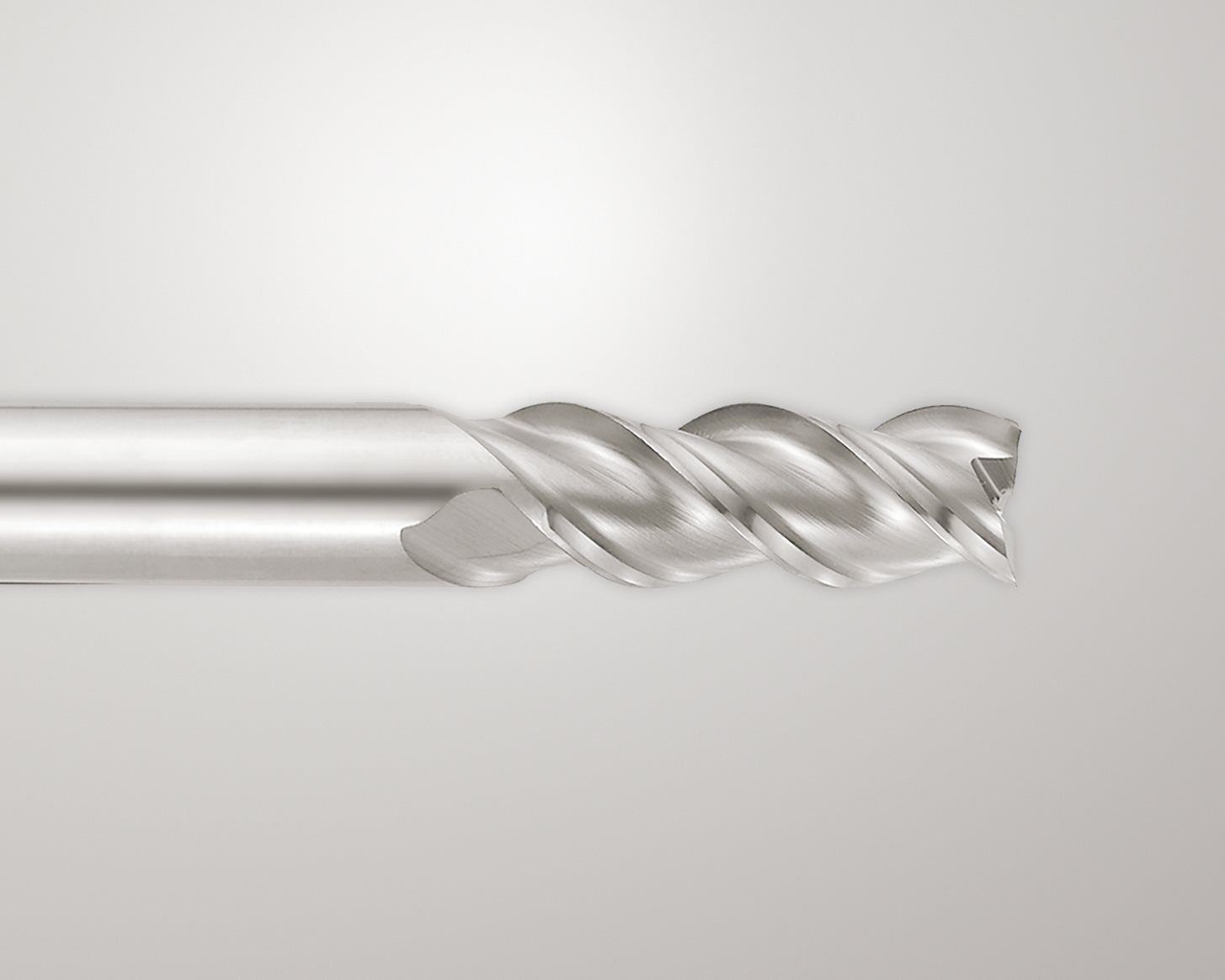
JH722 High Speed - CoCr and Titanium - Ball - 6 Flutes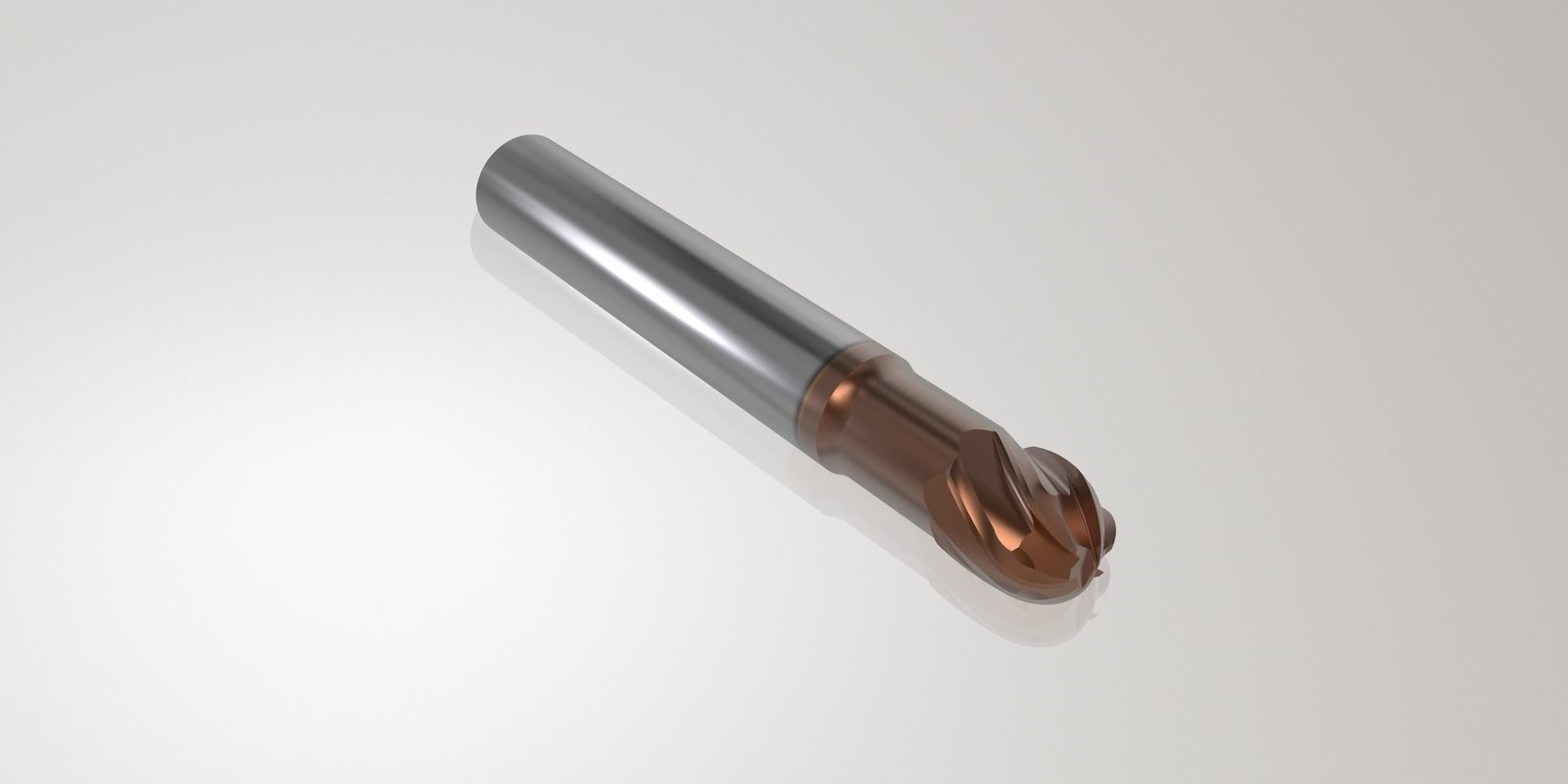
Milling Application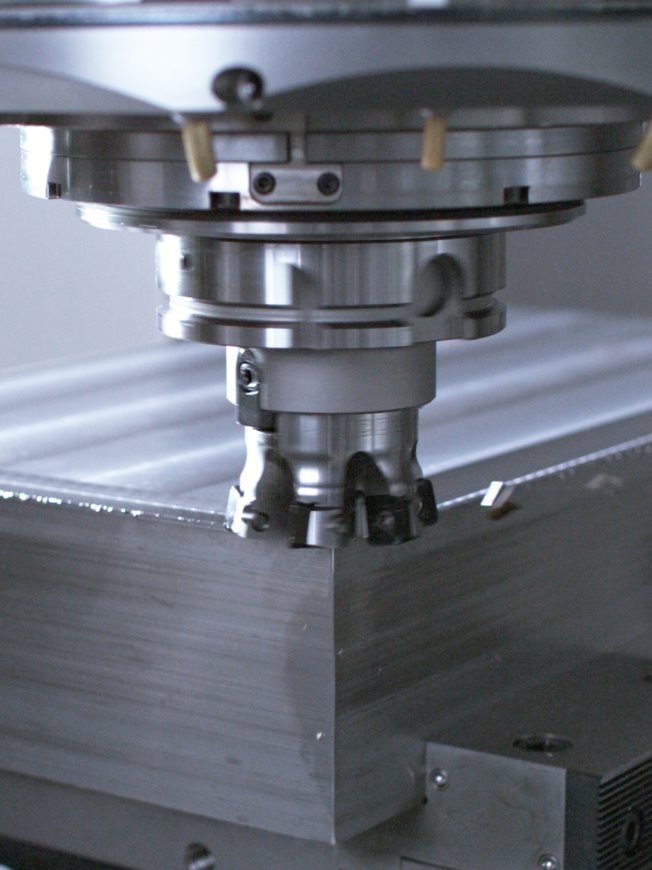
Mini Disc - 335.14 – Thread Milling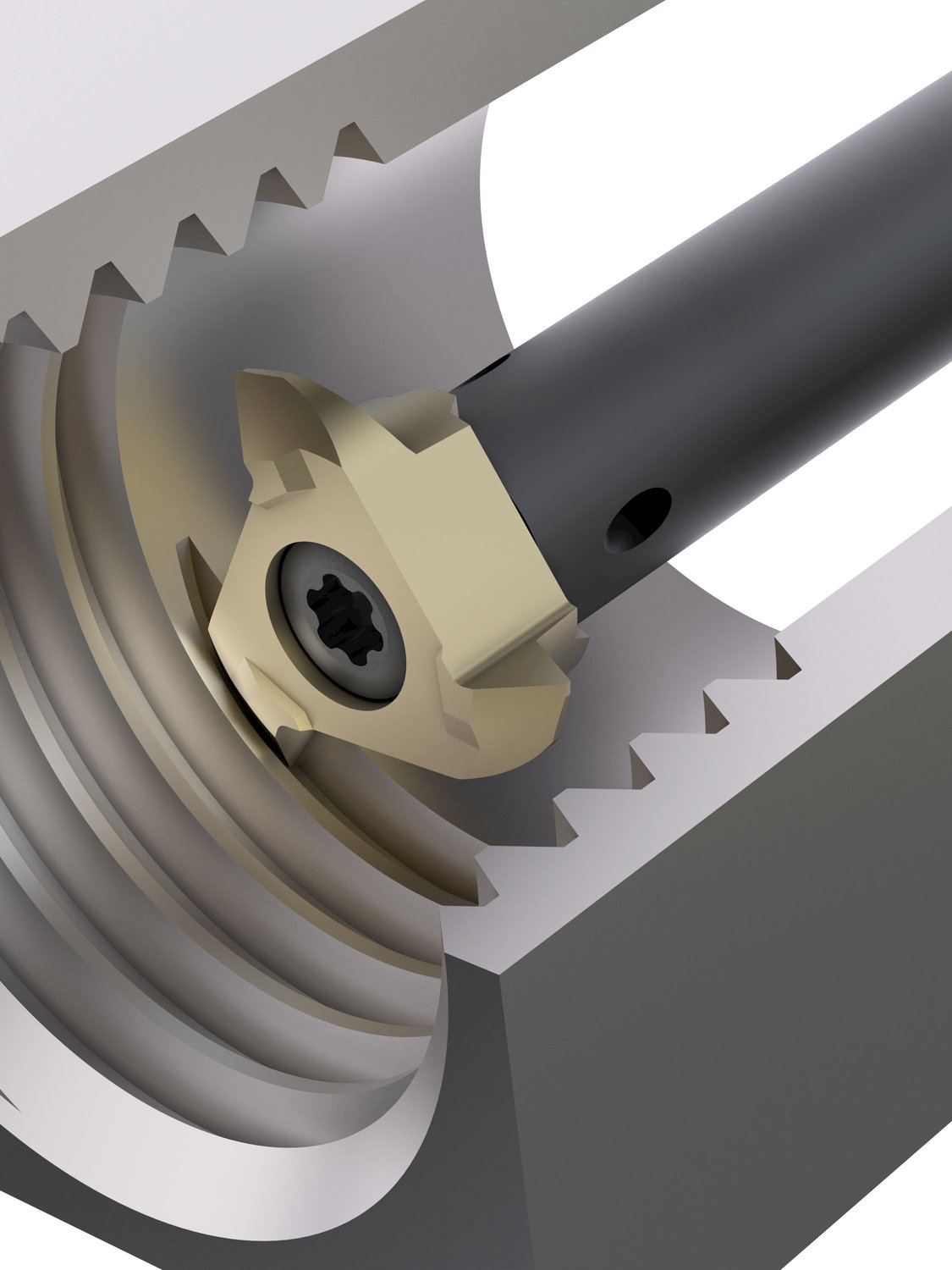
Mini Disc - 335.14 - Dove Tail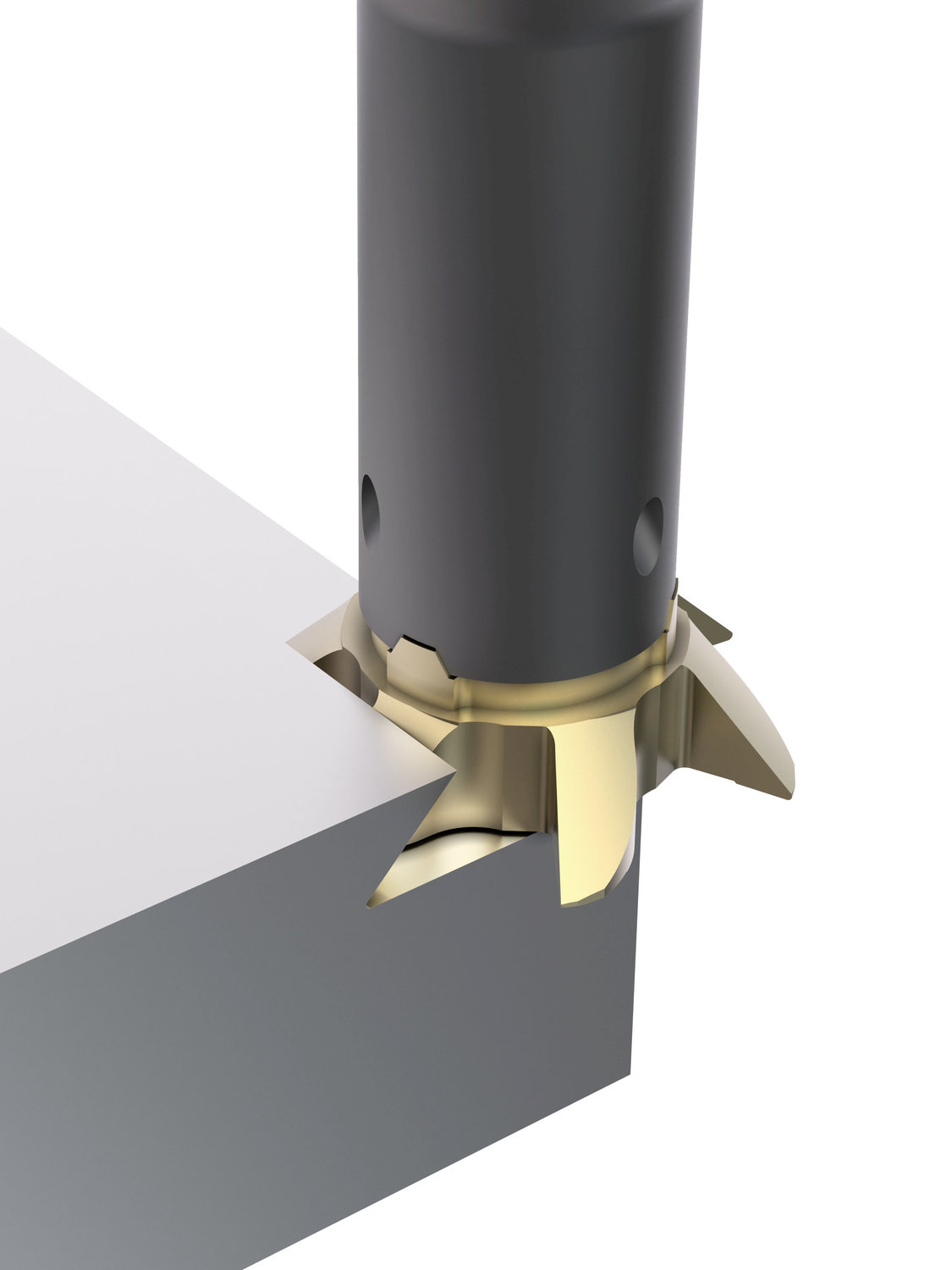
Mini Disc - 335.14 - Corner rounding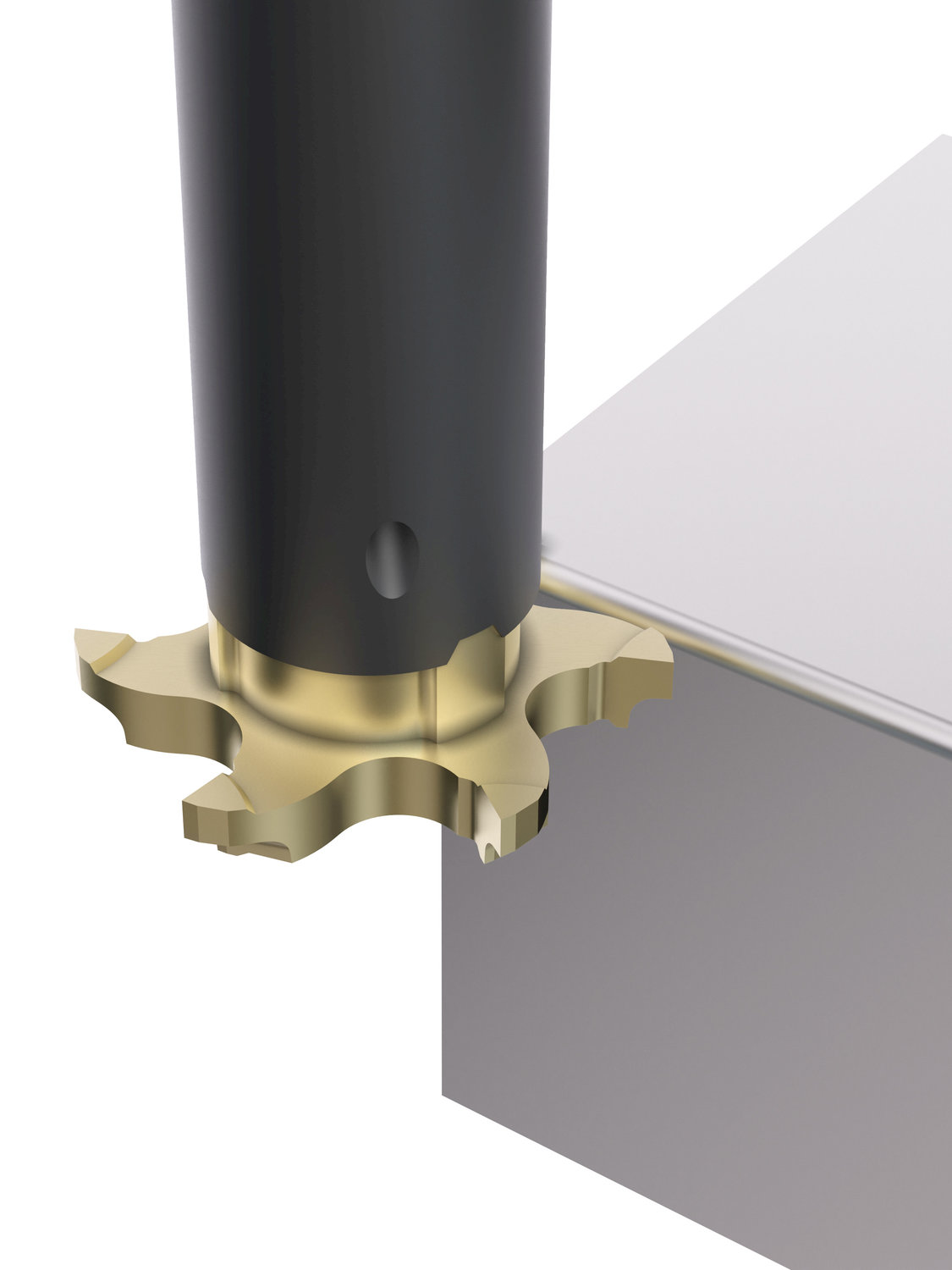
Mini Disc - 335.14 - Top and Bottom Chamfering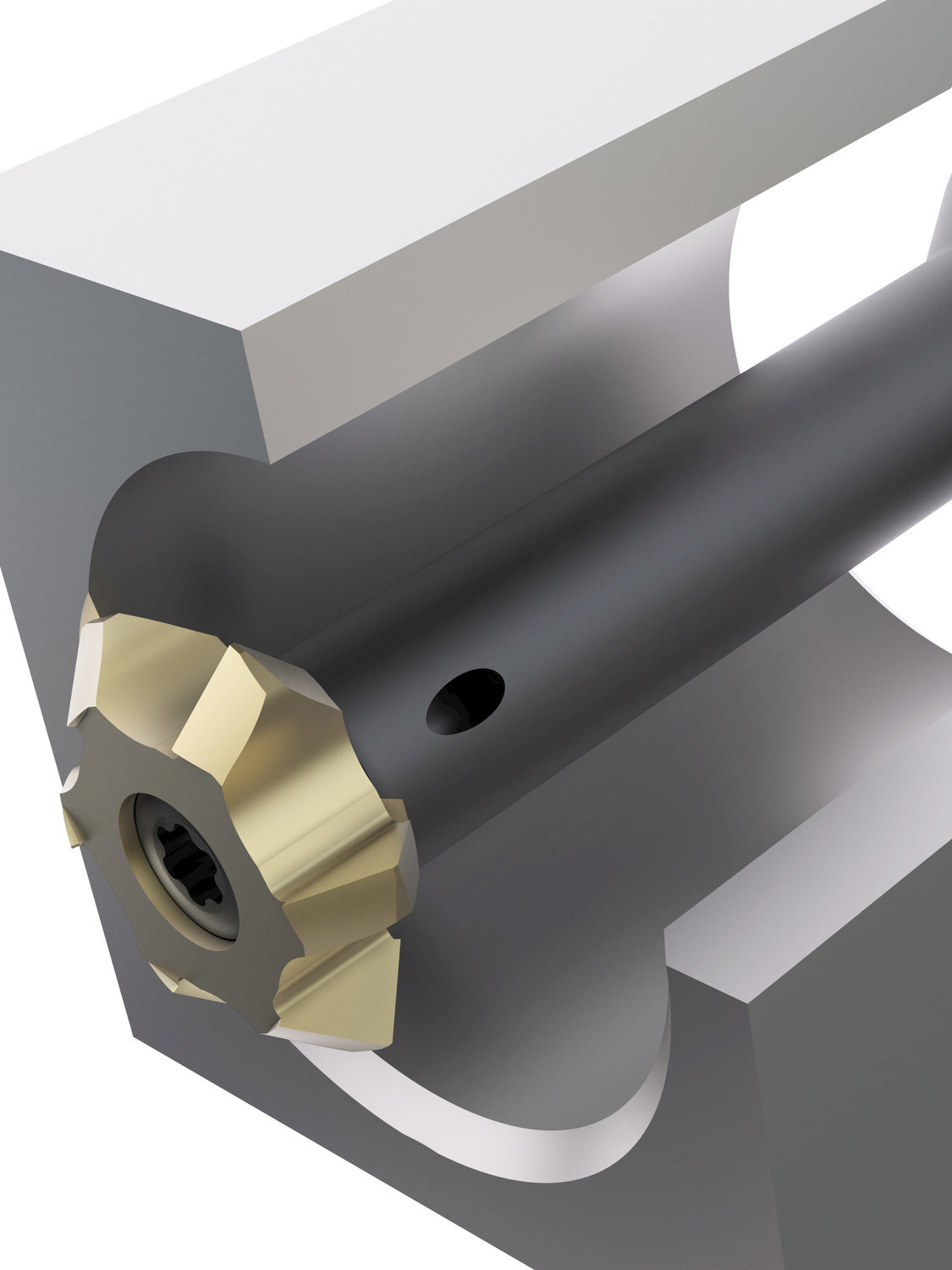
Mini Disc - 335.14 - Full radius profile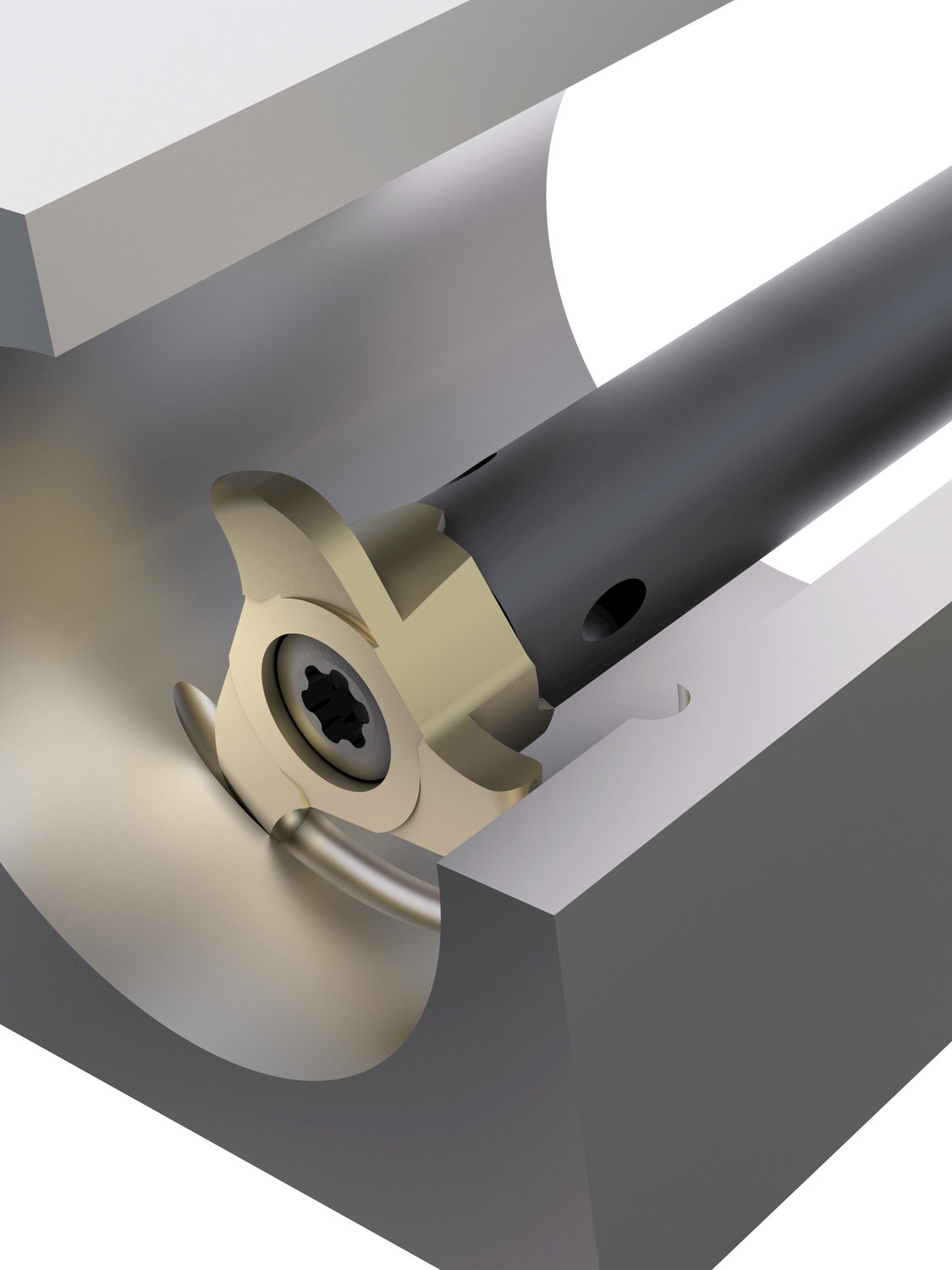
Mini Disc - 335.14 - For circlips groove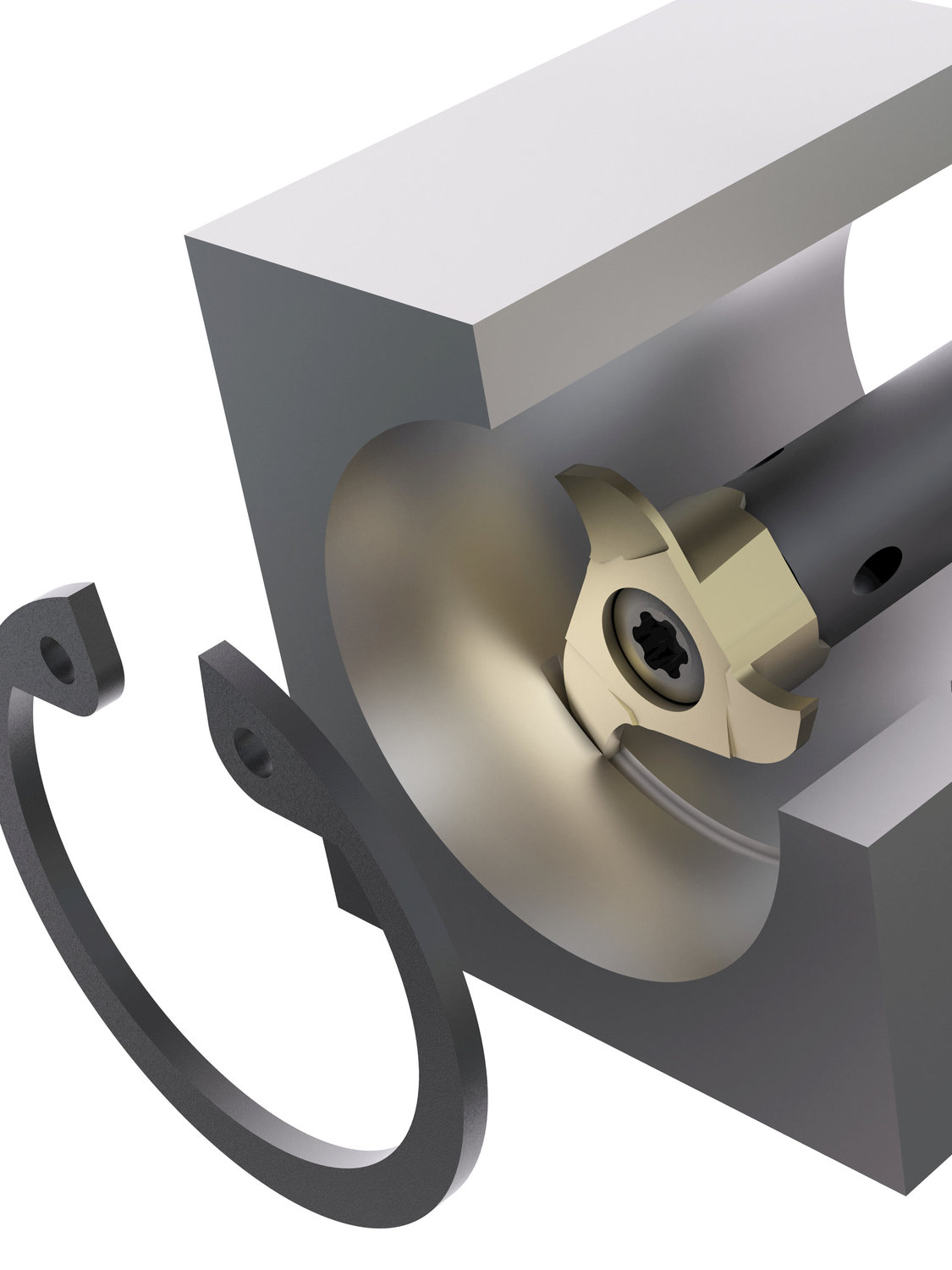
Mini Disc - 335.14 - General Grooving
335.14 - Replaceable Head Disc Cutters DC 6.7 - 50 mm (0.264 to 1.97”)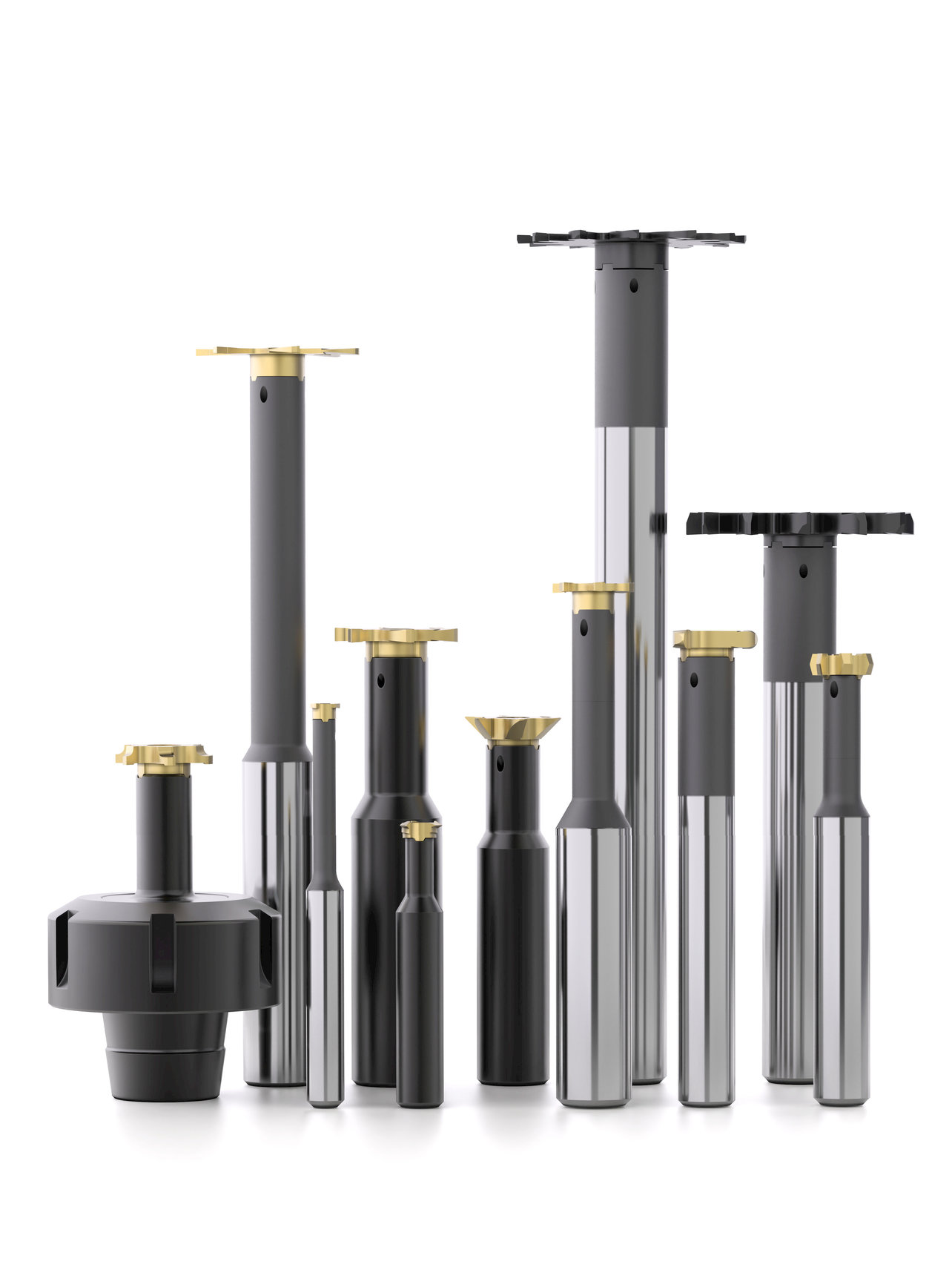
Mini Disc - 335.14 - Shanks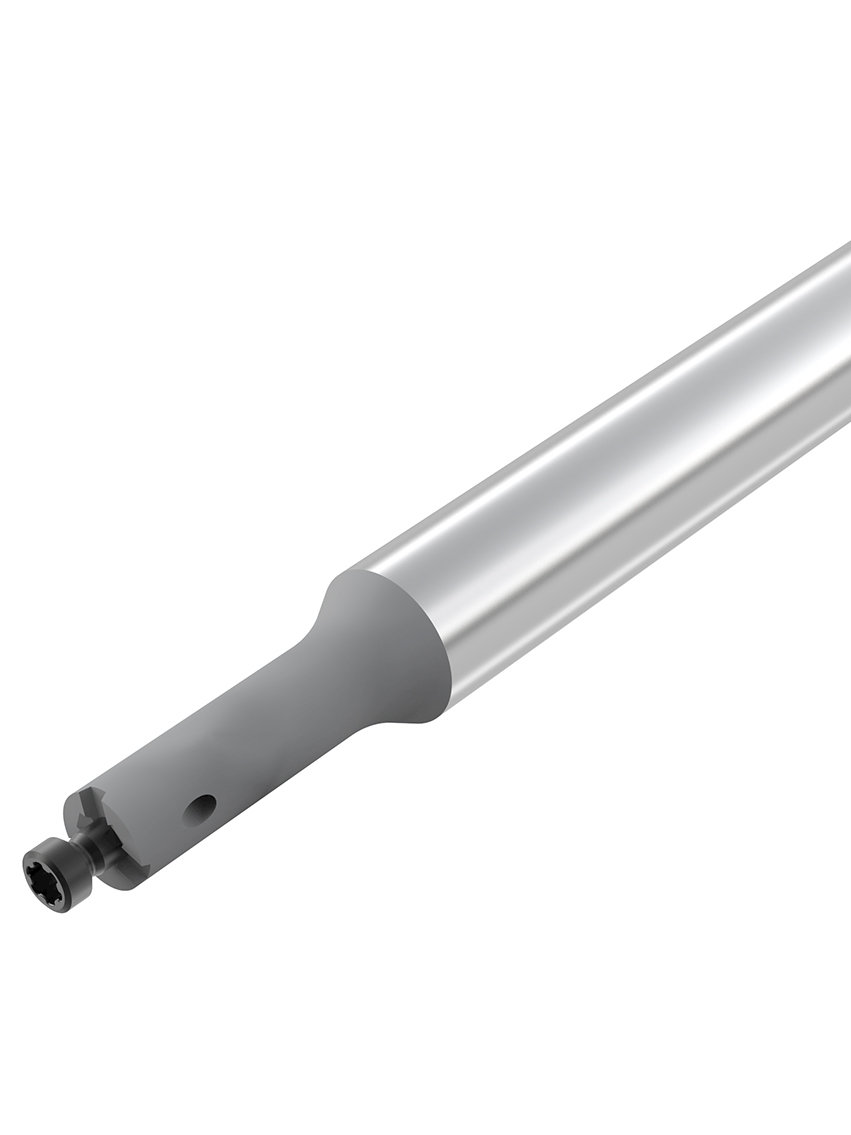
Suggest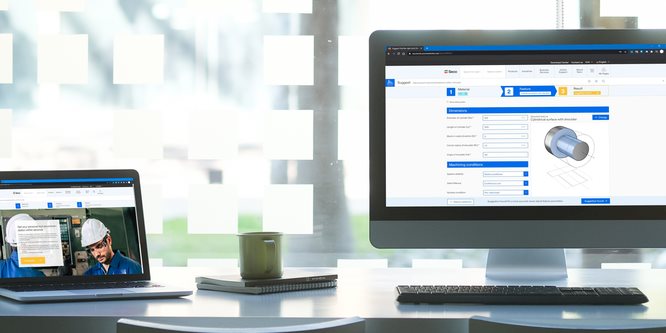