INCREASE TOOL LIFE WITH ELITE TOOL COATINGS
ALL ABOUT TOOLING COATINGSWHAT DO COATINGS DO?
In short, coatings increase tool life. They provide a thermal barrier between the cutting edge & the workpiece. Coatings increase the hardness on the surface of the tool. Coatings also increase lubricity for better chip flow and evacuation, causing less heat. They minimize built-up edge, improving surface finish, and reduce abrasive wear.
PVD COATINGS
- TiN - TITANIUM NITRIDE
- A general-purpose coating for HSS, HSCO, and Solid Carbide end mills that provides effective protection against wear, abrasion, and edge buildup. Primary applications are milling steels in a non-hardened condition.
- TiCN - TITANIUM CARBONITRIDE
- Incorporation of Carbon into the TiN matrix to increase hardness and abrasion resistance. TiCN is an alternative to TiN for HSS and HSCO applications where additional wear resistance is required. Primary Solid Carbide applications are milling aluminum alloys & cast iron.
- TiAlN - TITANIUM ALUMINUM NITRIDE
- TiAlN offers a higher level of thermal stability above Tin and TiCN with abrasion resistance. Ideal for high heat applications found in milling steels, stainless steels and high temp alloys with a hardness 52 Rc and below.
- AiTiN - ALUMINUM TITANIUM NITRIDE
- Increased thermal stability when milling high temp alloys and Die/Mold steels with a hardness 52 Rc and above. Excellent for HSM applications, Titanium, and Stainless Steels. HSS/HSCO end mills can’t be coated with AlTiN.
- AlCrN - ALUMINUM CHROMIUM NITRIDE
- Excellent wear resistance under conventional and extreme conditions when milling Die/Mold steels with a hardness 52 Rc and below. Excellent choice for tool steel, alloy steel, and stainless steel applications.
CVD COATINGS
- DIAMONDPLUS
- DiamondPlus coatings are made of multiple layers of uniquely structured nano-crystalline diamonds. The 100% ultra fine-grain diamond throughout the coating results in a tool that resists abrasive & adhesive wear and stands up to mechanical shock. The hard, smooth surface provides the best part finish with no built up edges. Primary applications are composite materials, high silicon aluminum, and graphite. When milling graphite, tool life 12-20 times longer than uncoated tungsten carbide is typical.
- Do not use DiamondPlus on steels. The high heat generated from milling steels causes the carbon from the diamond to diffuse into the iron, causing chemical wear. Regrinding a DiamondPlus endmill is not recommended. Standard C430’s or similar cannot be coated with DiamondPlus.
HOMERelated content
High Performance Optimized Roughing in 17 4 PH Stainless Steel Dry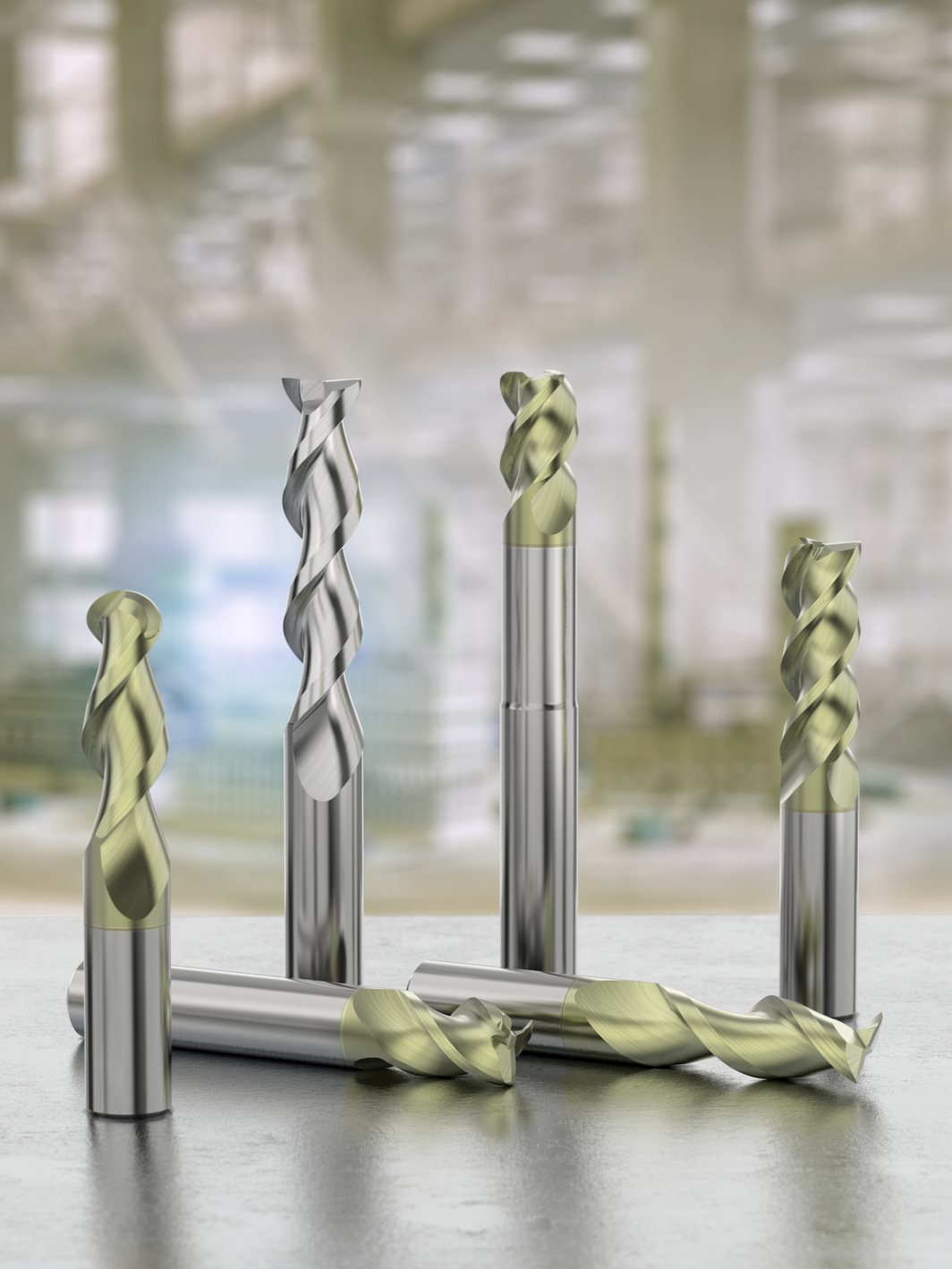
Niagara Cutter High Feed Machining Product Introduction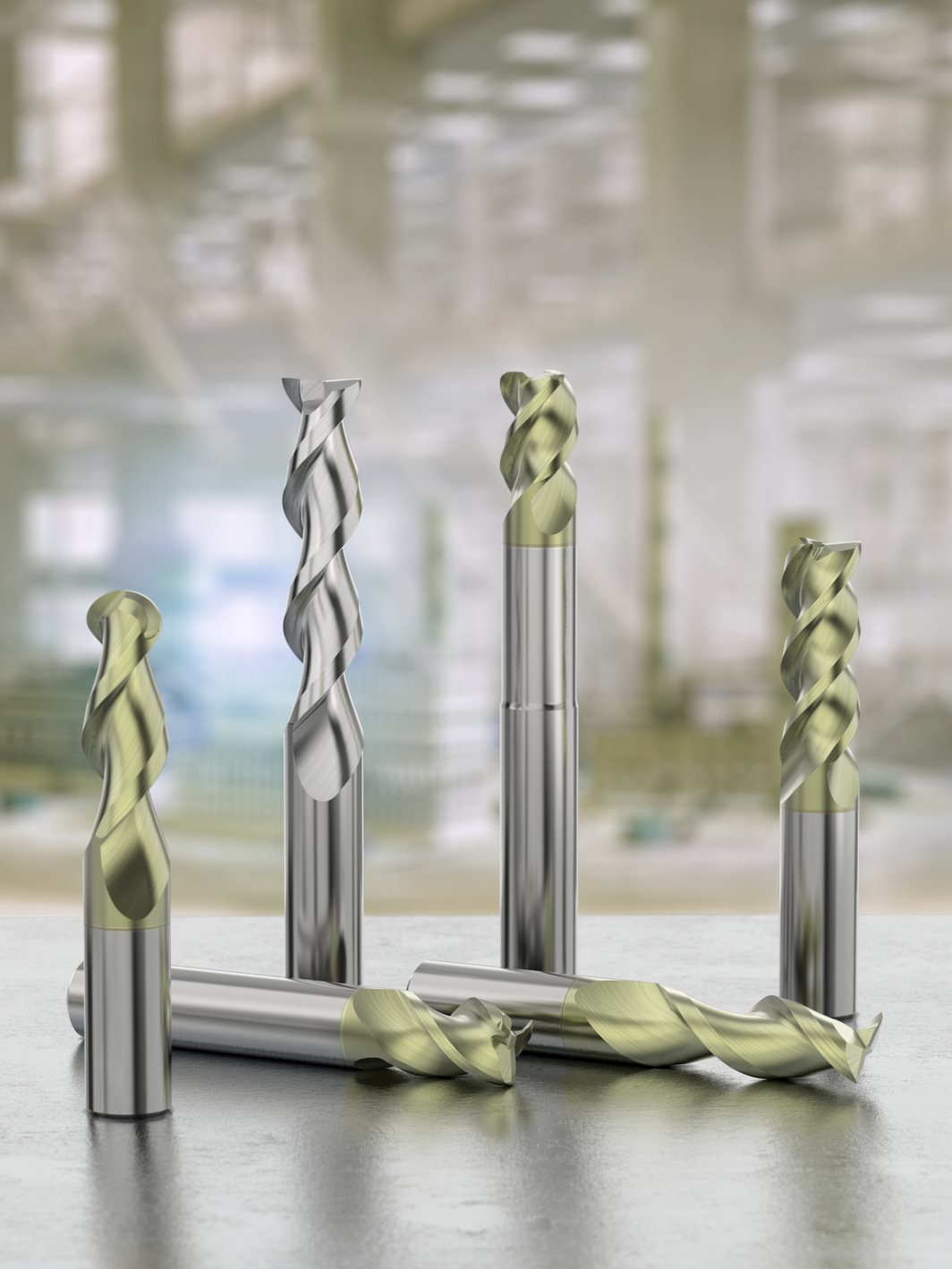
Video: Niagara Cutter NTM100 Threadmill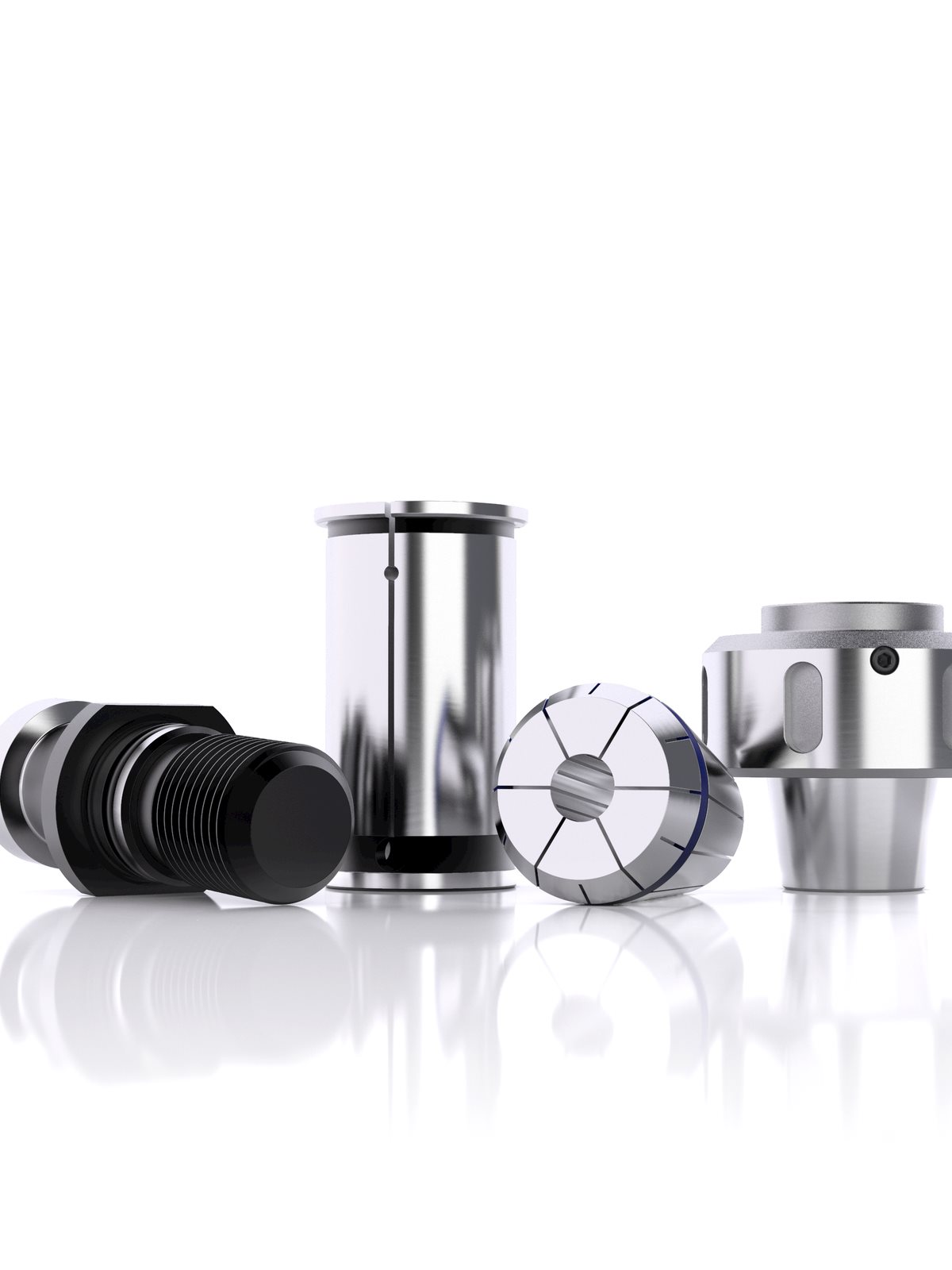
Niagara Thread Mills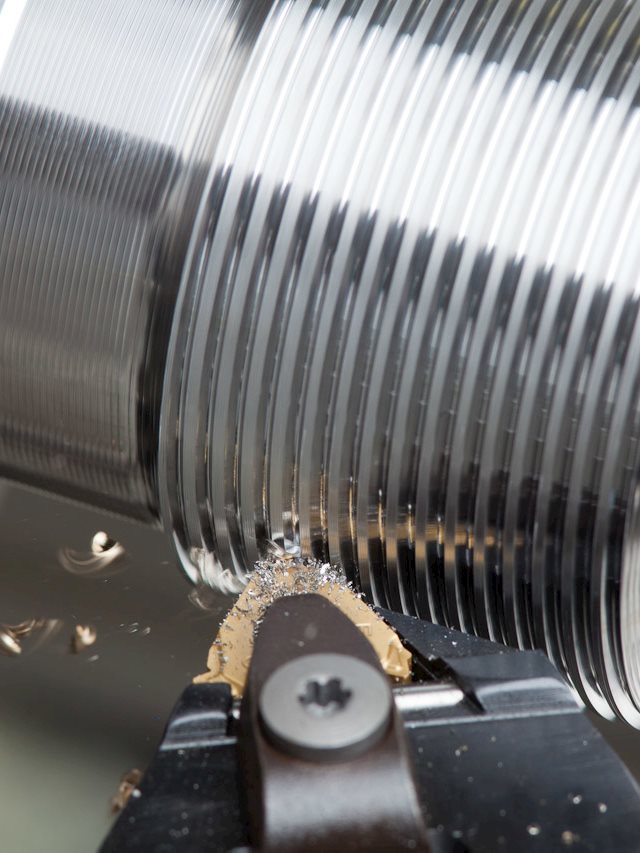
ABOUT NIAGARA CUTTER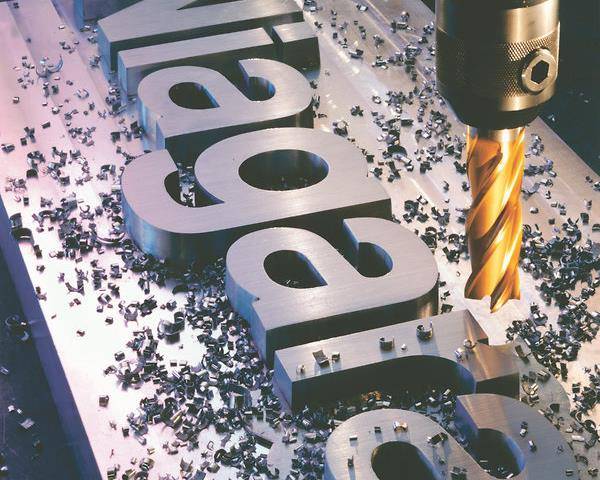
Niagara Cutter Multi Flute - Elite Series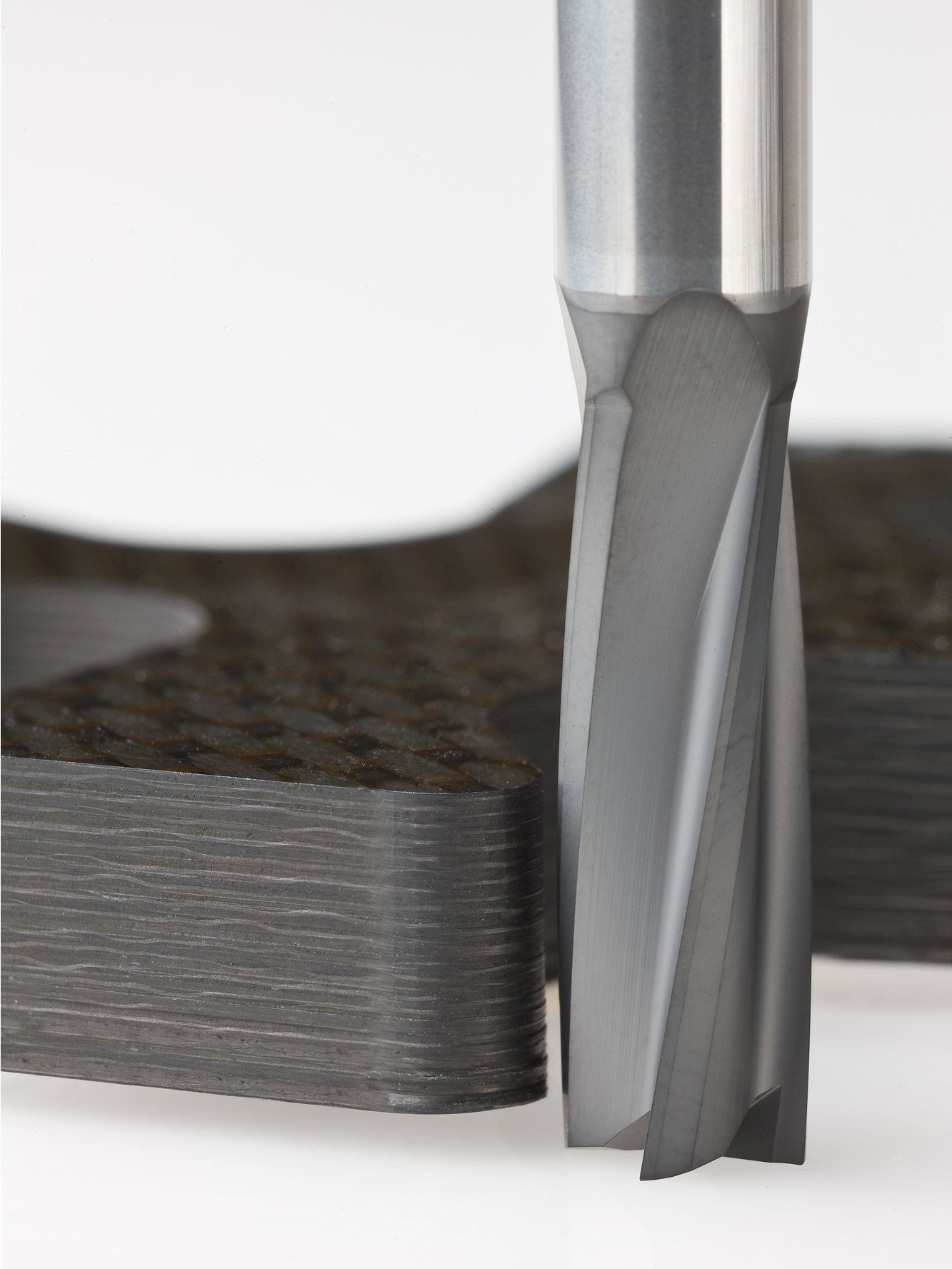
Optimized Roughing 17-4 PH Stainless Steel Dry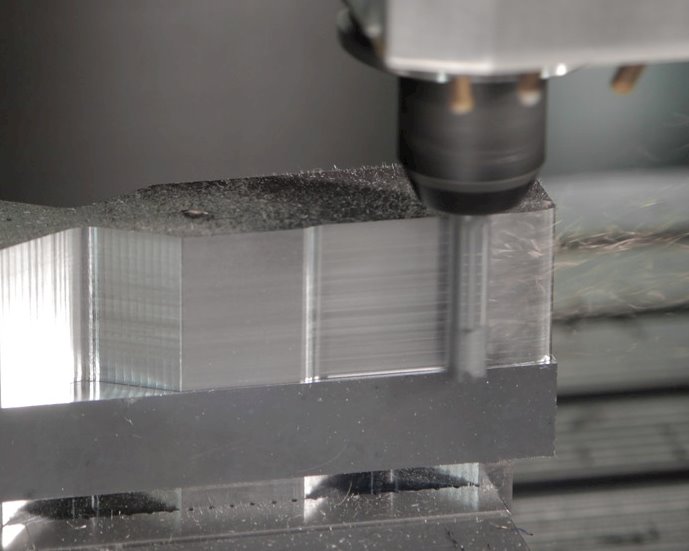
Niagara Cutter's SN200R, SN400R and SN500R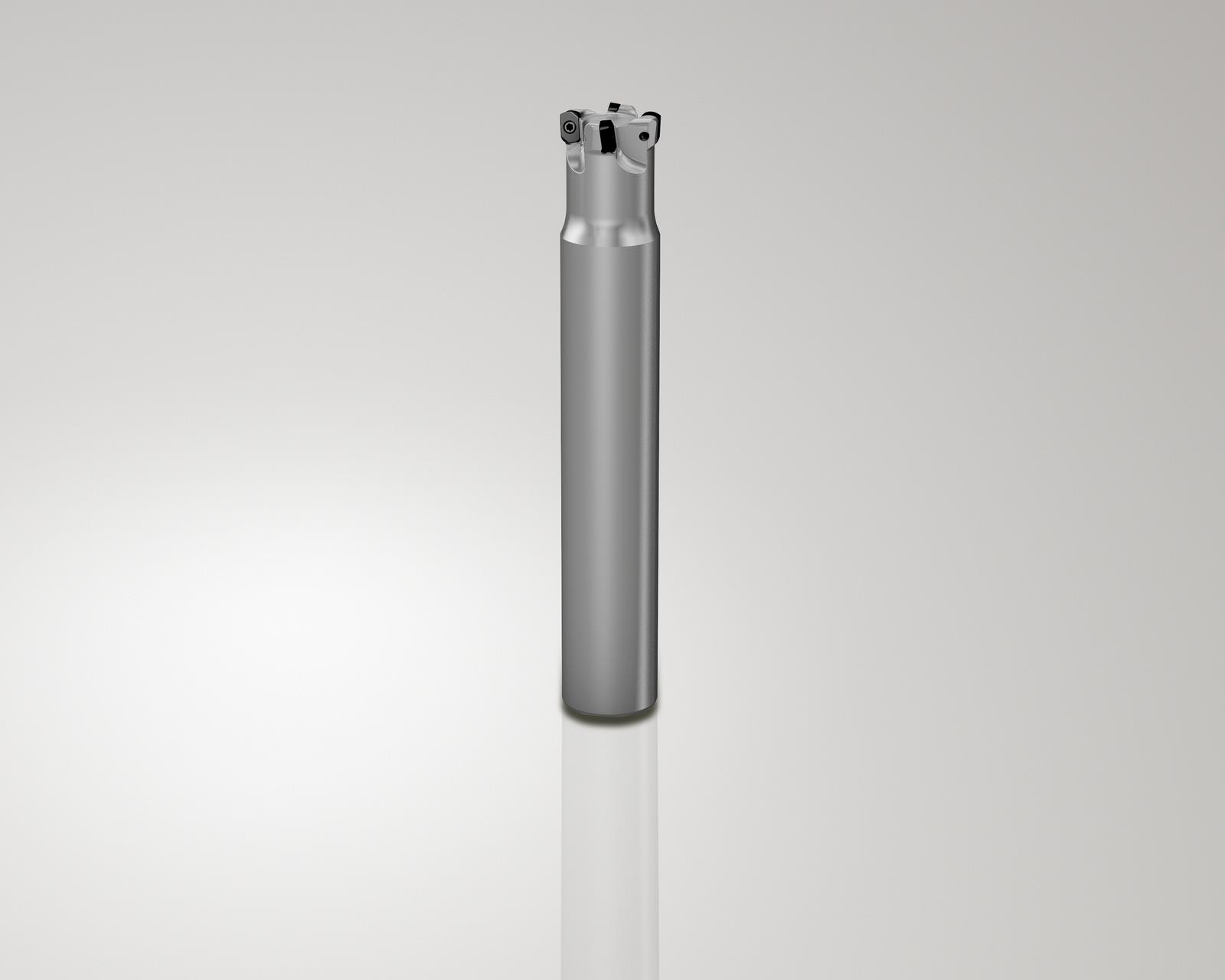
High Performance Optimized Roughing with Stabilizer 2.0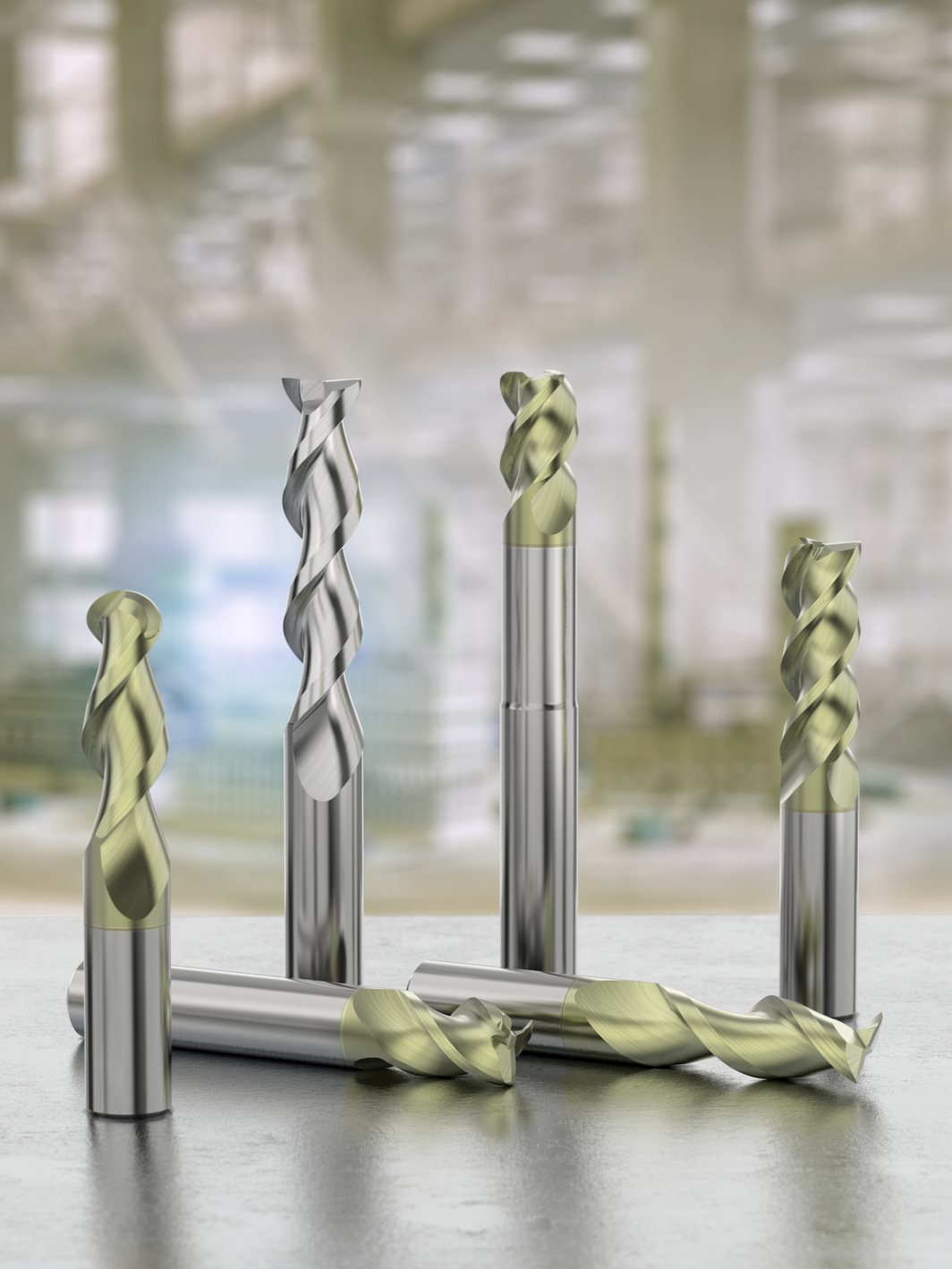
Mold & Die End Mill Expansion Introduction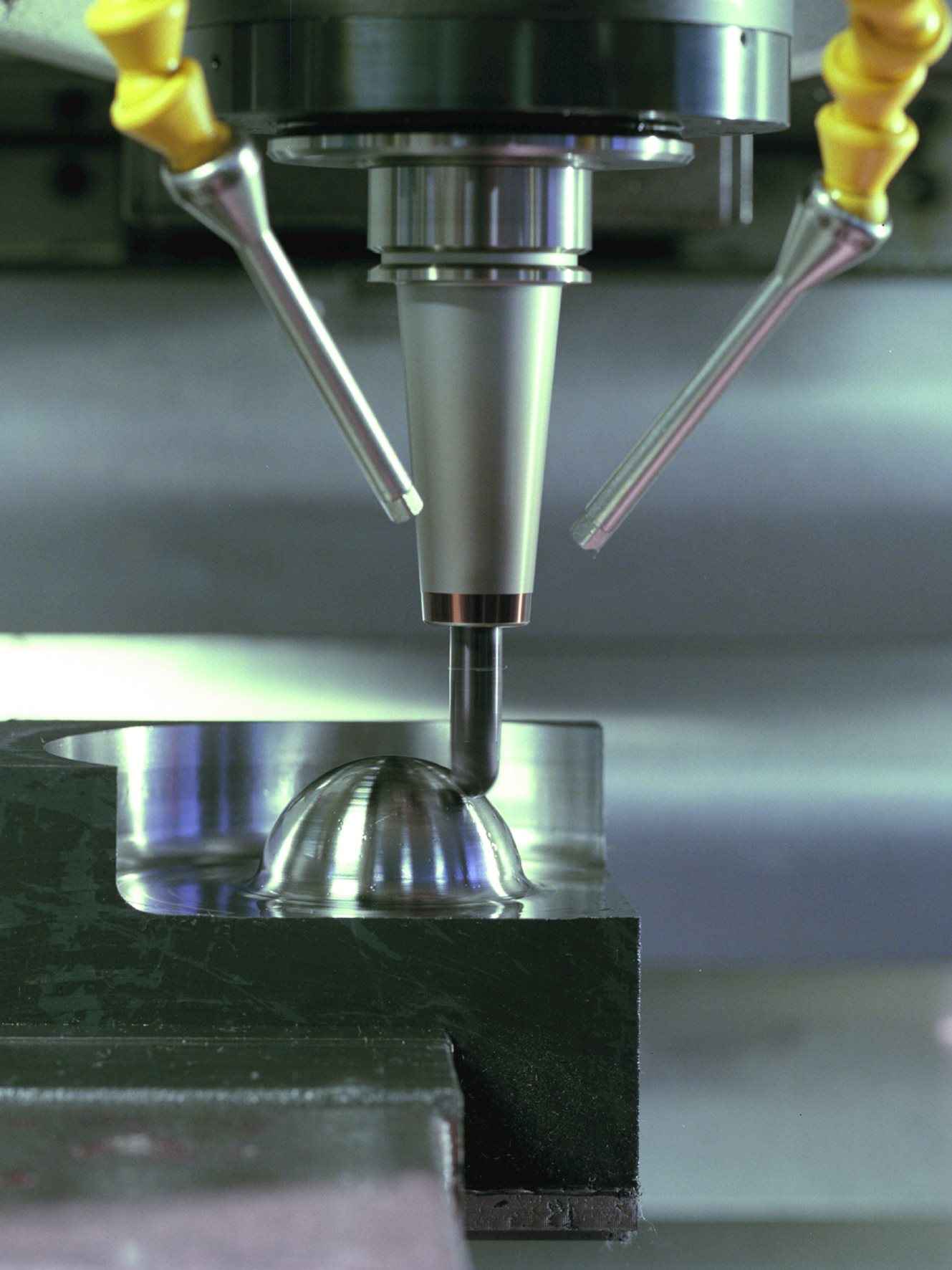
Optimized Roughing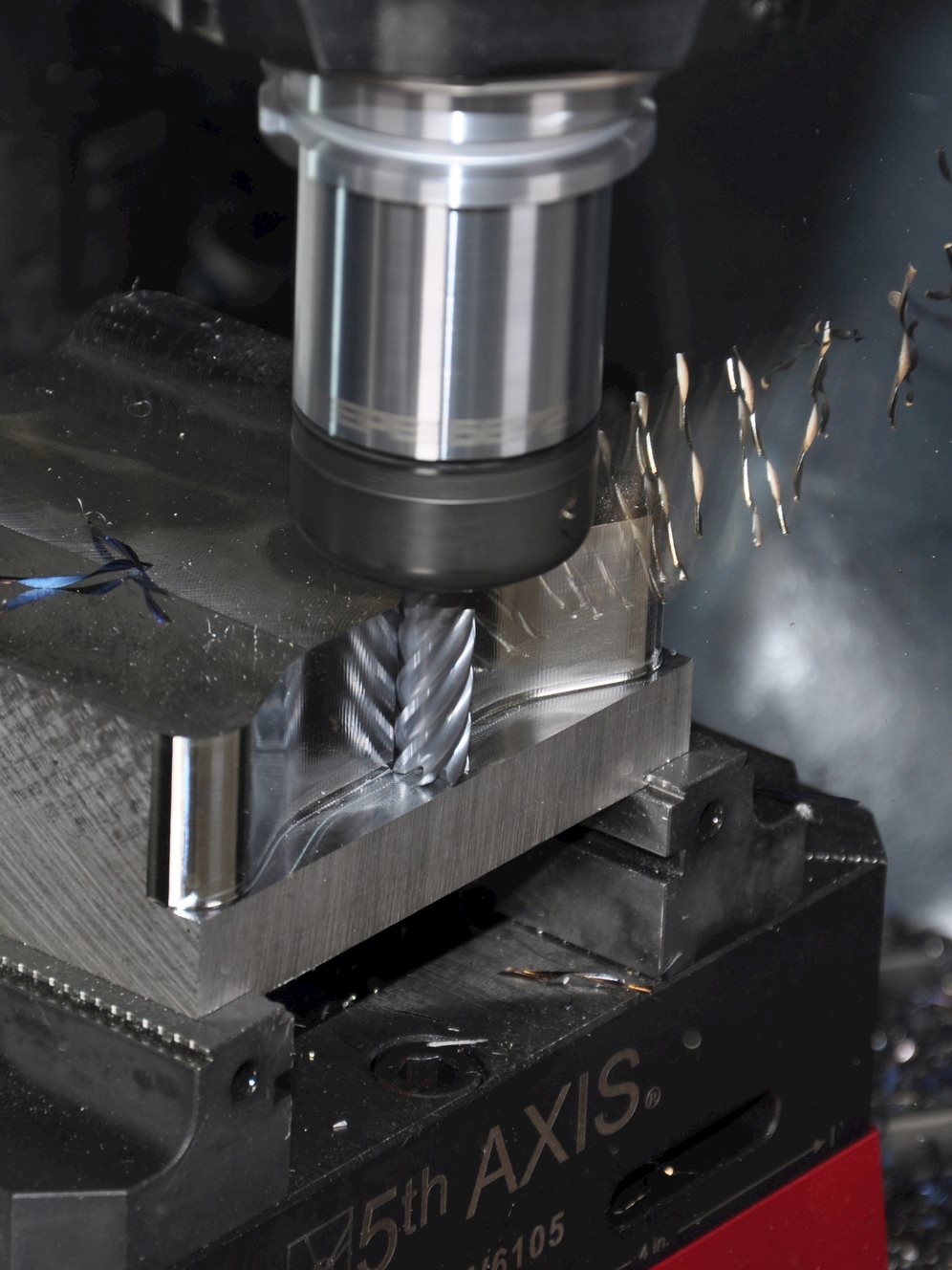
Optimize Your Machining Processes with these 7 Tips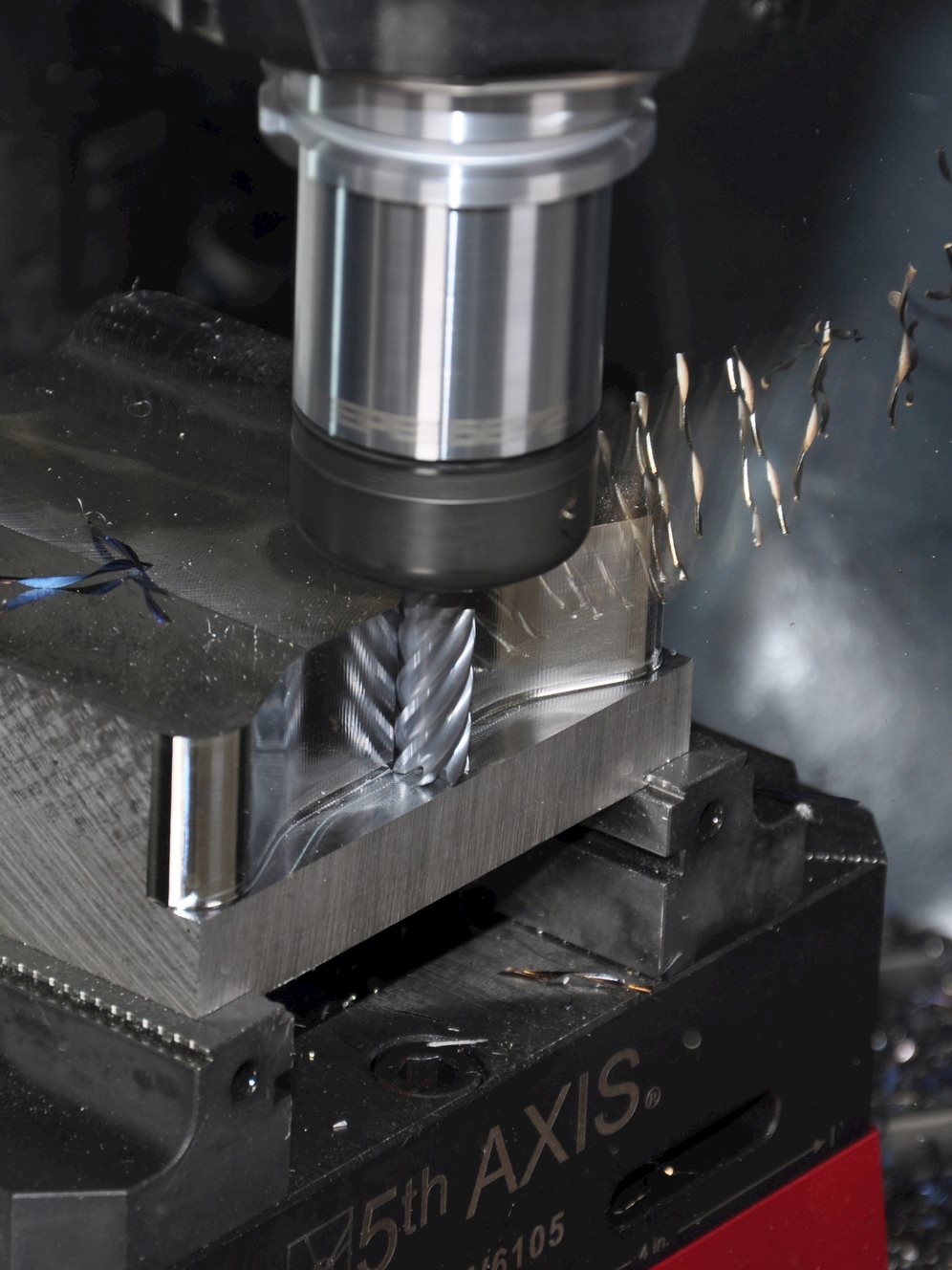
Machining Navigator / Catalog Solid End Mills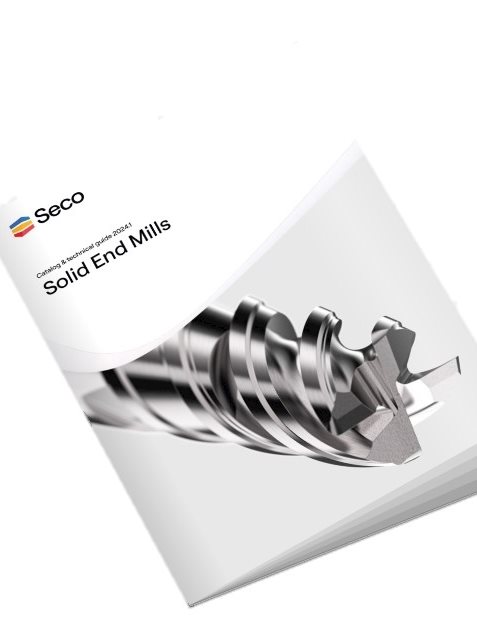
Video: High Performance Optimized Roughing with Stabilizer 2.0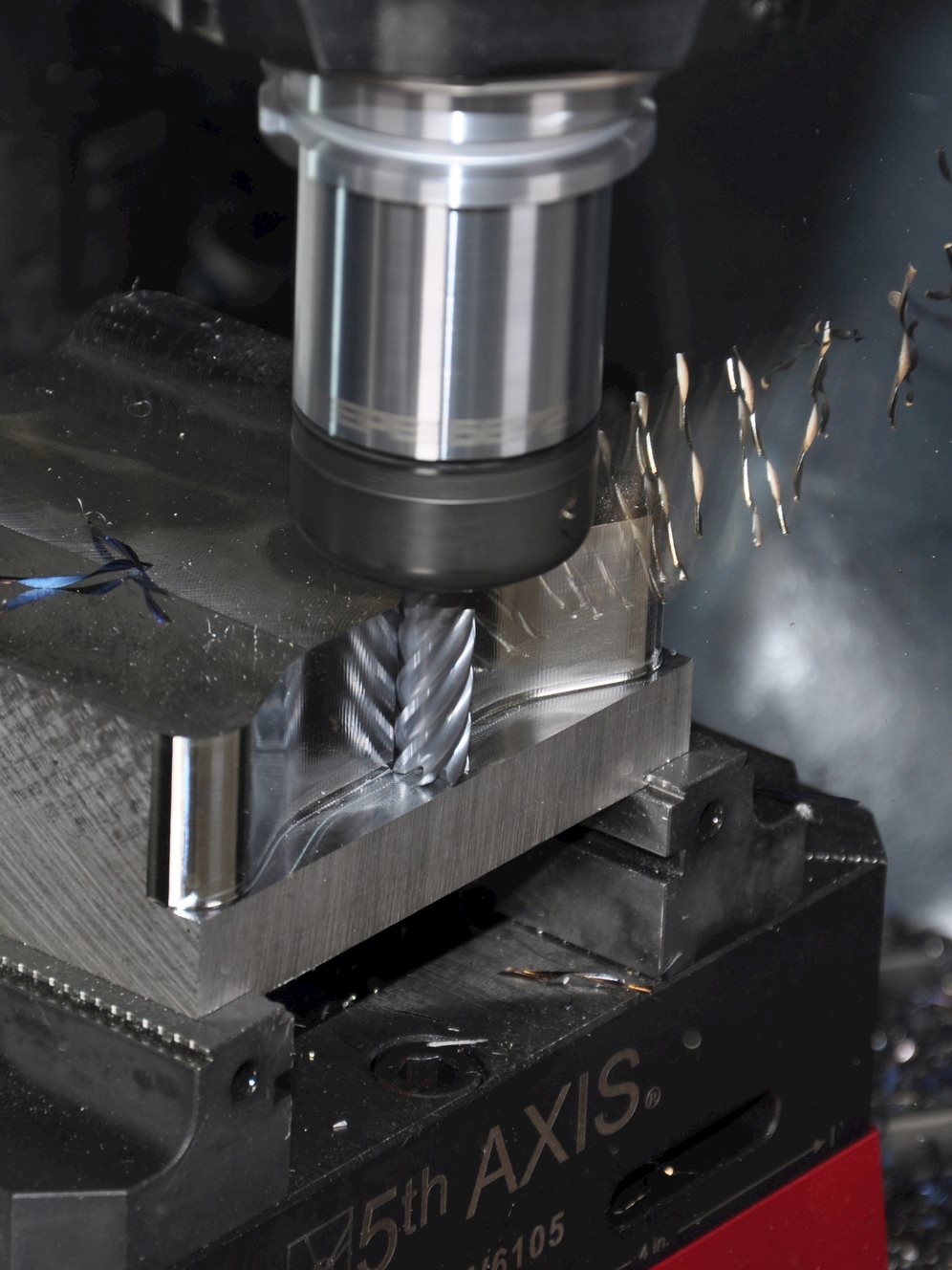
Video: Niagara Cutter Stabilizer 2.0 Product Introduction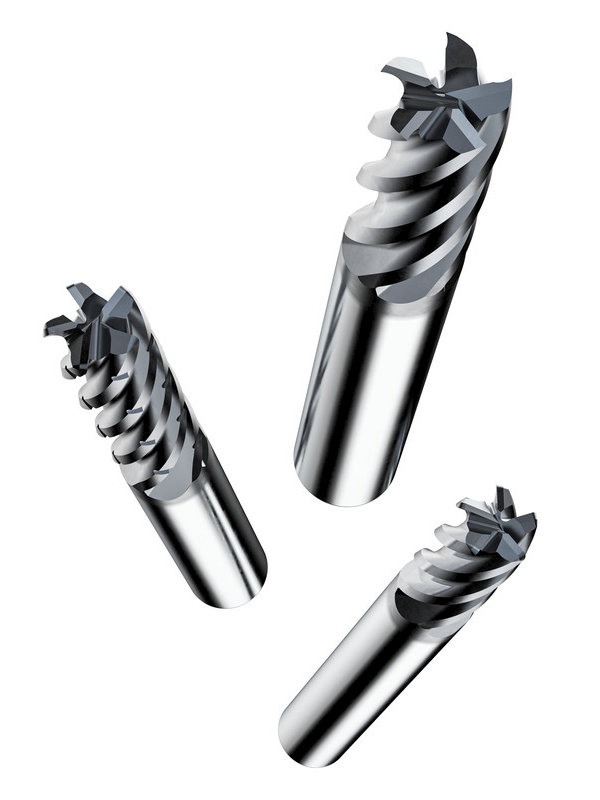
ACS540 / ACS540R End Mills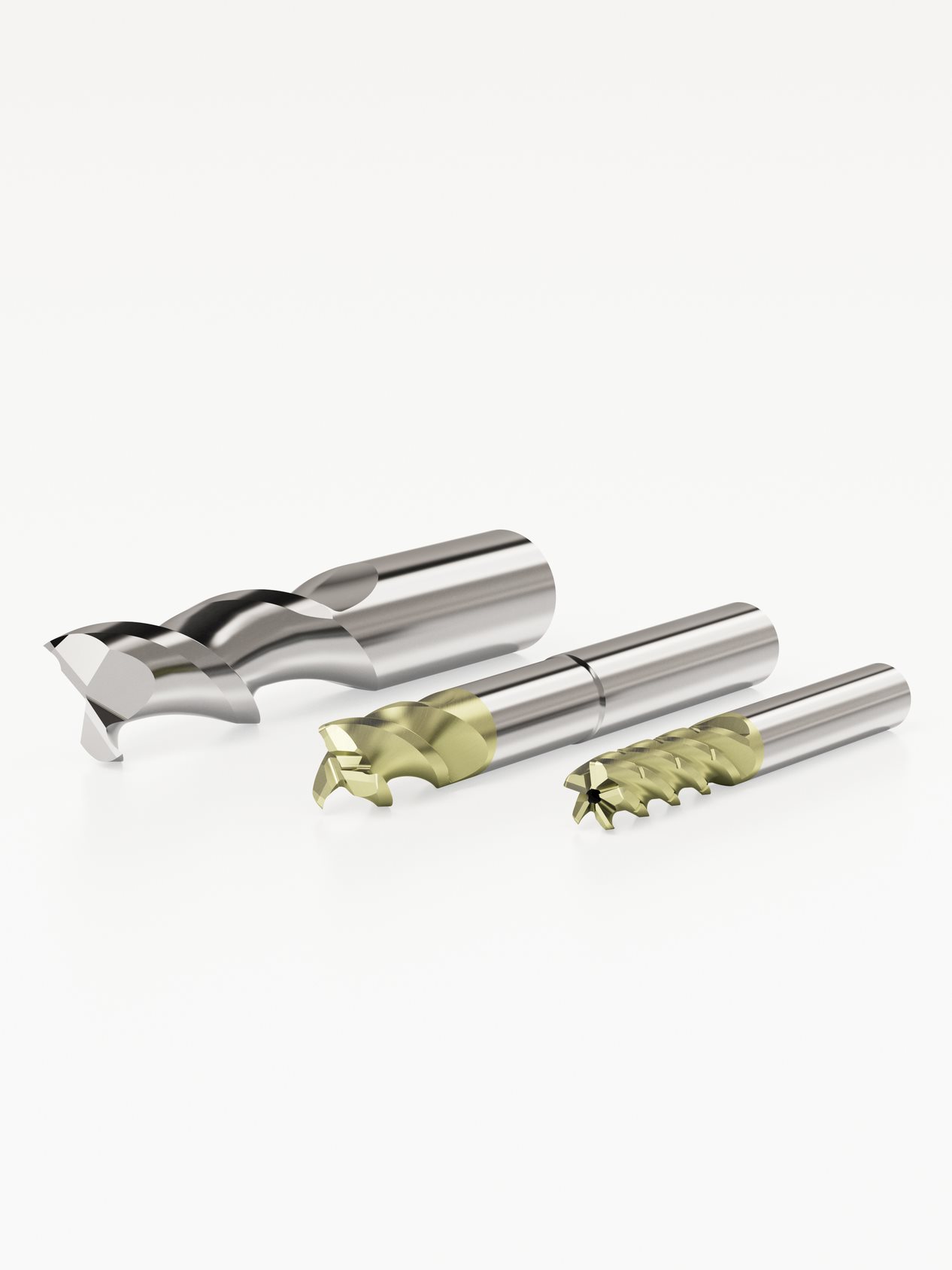
A245/A345 family of end mills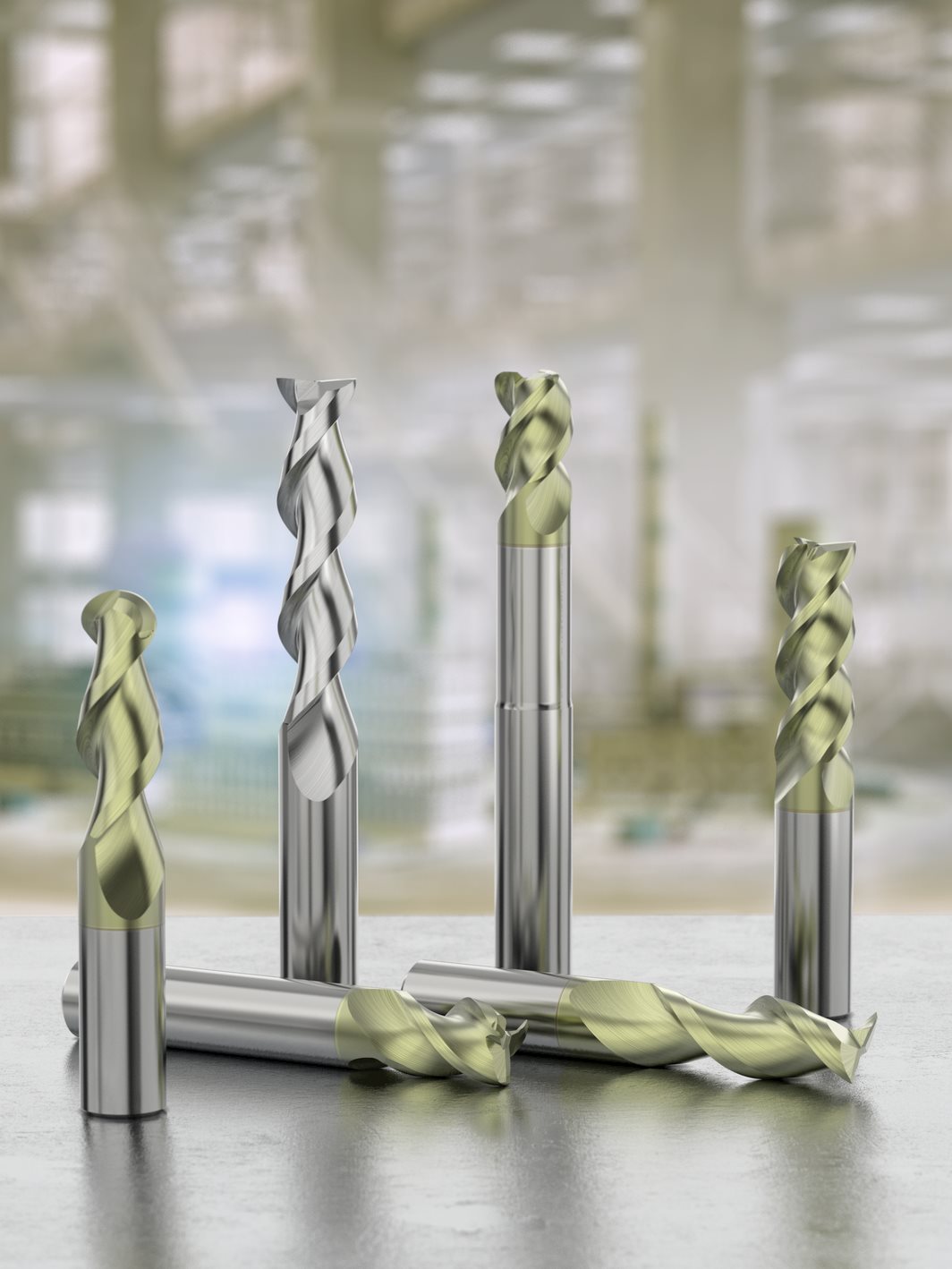
New Seco Niagara cutter™ 5-flute End Mill delivers extreme versatility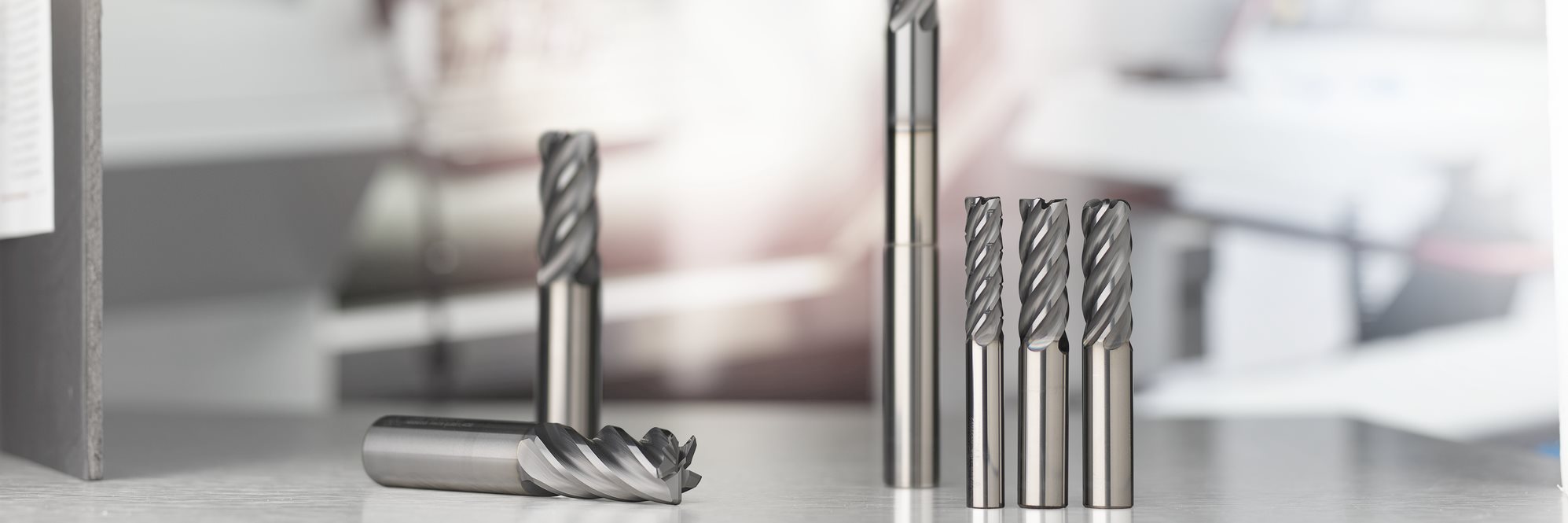
Multi flute solid carbide end mills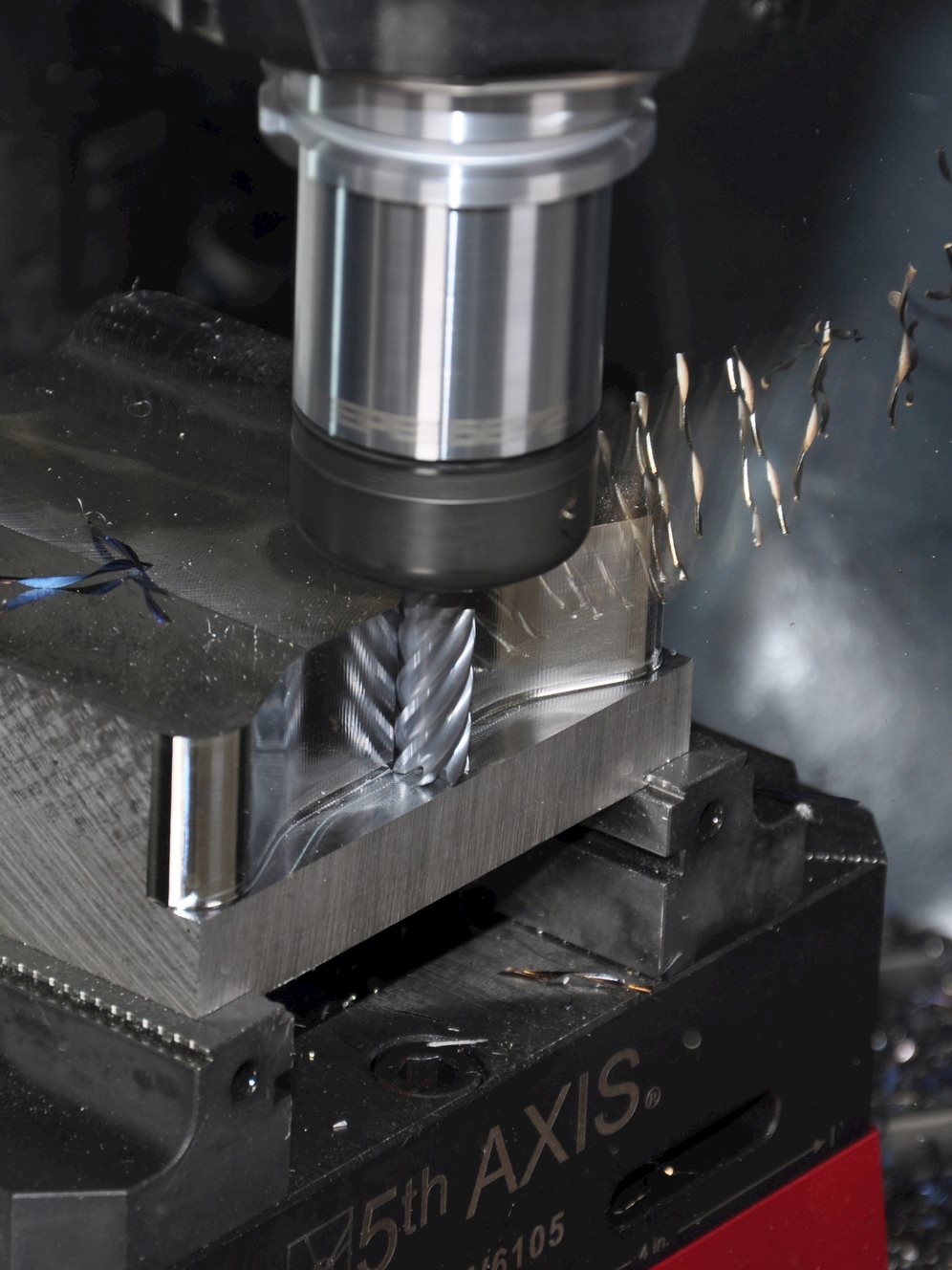
Niagara Cutter® HTA Coating Product Expansion