Seco makes all tools traceable with new scannable codes
Production markings that encode tools as a batch cannot identify an individual tool. For industries that prioritize traceability – aerospace, automotive and medical, for example – batch identity is not enough. Seco needed a way to make each tool identifiable as an individual product, and Data Matrix codes provided the solution.
Gerrit Kremer pulls out a box of inserts for the Seco Turbo 16 family of milling cutters. All six look identical. "It is difficult to differentiate one tool from another," said Kremer, global product manager for digital product service at Seco.
Production markings that encode tools as a batch cannot identify an individual tool. For industries that prioritize traceability – aerospace, automotive and medical, for example – batch identity is not enough. Seco needed a way to make each tool identifiable as an individual product, and Data Matrix codes provided the solution.
"We looked at how we can scan Data Matrix codes with the Seco Assistant app, and we began to see a new way to create customer value," Kremer noted. With Data Matrix codes, Seco now makes each tool fully traceable on its own.
Data Matrix codes look like small QR codes. Their square or rectangular pattern of black and white cells can encode a 50-digit number that remains readable reliably down to 4 mm2. A Data Matrix system can support 10 billion codes.
In September 2021, Seco began laser marking its popular Turbo 16 family of milling cutters with new Data Matrix identification codes. Now, shop floor workers can scan these codes with the Seco Assistant app and identify an individual Turbo 16 insert.
With round tools, Seco includes paper instructions that often disappear before the tools go into use. As Anton van Oeffelt, director of solid milling, observed, "Before the person behind the machine can start programming and using the tools, that information is already gone."
Seco added the JSE510 series of solid end mills as the second product line to receive laser-marked Data Matrix identification codes. Now a quick scan in Seco Assistant can access essential information about these tools in seconds.
Since then, the number of products with individual Data Matrix codes significantly has increased and a majority of tools within all product lines are marked when produced.
Data Matrix codes themselves are not new. The U.S. Department of Defense has required them on much of its equipment since 2005. The technology is well-established in the automotive, aerospace, medical equipment, computer, food and logistics industries. The machine tools industry has not yet adopted the codes widely.
Because the codes are small, Seco can laser print them on smaller tools such as inserts, or on the back surfaces of larger round tools, instead of on the shank. Now that the codes make tools and inserts easy to identify, shops can avoid wasting expensive inventory. In seconds, operators can verify correct insert or round-tool use and their associated machine tool settings. With the information in hand, shops can avoid up to 58% of production errors.
Data Matrix codes also can do much more. They can identify each individual product among the millions of units that Seco produces each year. This creates tool-setting, traceability, data-collection, reconditioning and recycling opportunities across all phases of a tool’s life.
Early in the manufacturing process, Seco measures the precise individual dimensions of each tool and prints the code on it. The information goes into a database, linked to that individual code. Now, customers no longer need to measure inserts minutely to control for small variations in tool size. A quick scan identifies the exact dimensions of each tool. The codes will enable automatic tool calibration on any machine that can read them.
Similarly, when customers receive resharpened or reconditioned larger tools, they can access renewed dimensions through each code and calibrate their machines – manually or automatically – with no need to remeasure a tool.
The aerospace, automotive and medical sectors make traceability a focus. With individualized tool identification through Data Matrix codes, shops can remove a single tool from service rather than reject an entire batch. The codes also help assess and determine liability. "All these manufacturers want this level of traceability, so if something happens in their production environment, they can find the problem," explained Van Oeffel.
Additionally, the codes could help Seco and its customers advance their recycling efforts. Most of the material in a worn-out cutting tool remains recyclable. Under Seco's buy-back program, Data Matrix codes will record recycling rates automatically for customers and for Seco. This facilitates sustainability reports.
Likewise, the codes will enable Seco recycling facilities to scan worn-out tools and learn their exact material composition. "Just as with plastics, metals vary in composition," said Kremer. "The better we can trace these alloys, the better we'll be able to recycle them."
Through Data Matrix codes, Seco will be able to track various aspects of customer usage. How long do tools wait on customers' shelves? How often are they used in a day or month? How do they perform on different machine tools? The answers can help Seco predict orders and tailor production to customer needs.
By 2025, Seco will mark more than 90% of its tools with Data Matrix codes. The innovation will not be exclusive to Seco. Access to the codes and their data will be shareable between customers and their partners allowing full collaboration in such efforts as the Industrial Internet of Things (IIoT), automation and sensor technology. With shared data and sustainability goals, the possibilities for better tool usage – and better tools –will continue to increase.
Download the Seco Assistant App for Android
Download the Seco Assistant App for iOS
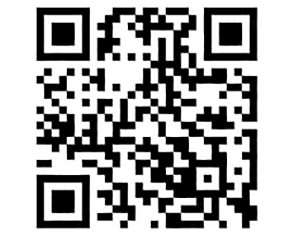