WHY MAKING AN AEROPLANE PYLON IS A TRUE COLLABORATIVE PROCESS
Aeroplane pylons keep the aircraft’s engines attached to its wings. Today, the development of such a critical component involves a collaborative chain of different specialists and suppliers, with Seco Tools playing a central role. Joe Gooding and Gary Meyers explain more.
Pylons are not the most noticeable part of an aircraft, but they are critical to keeping it off the ground and to keeping its passengers safe, because they are the components that attach the aircraft’s engines to its wings.
“There’s often one engine per wing, with four pylons per wing to attach the engine to it,” explains Joe Gooding, a UK-based Development Engineer for Seco Tools, who supports our customers in their projects, providing them with tooling and strategy suggestions on how to machine components. “The pylon itself is made from titanium that’s often forged and then machined down to the required size.”
“The aeroplane manufacturers are using titanium structural components as it’s the best material that gives them the safest option for those parts to be on an aircraft,” adds Joe’s colleague, Gary Meyers, Global Product Manager for Solid Milling, who’s based in Sweden.
“There are a lot of different Seco Tools product areas involved in making a pylon,” he continues. “From face milling to copy milling strategies, indexable tools versus solid carbide, drilling, reaming, and lately new barrel machining developments for the finishing of these components. These are tough parts that often have inconsistencies because they’ve been forged, plus deep pockets that are hard to reach. It’s safety-critical, so there are also very tight tolerances and finishing requirements too.”
Gooding and Meyers have been working closely together for the past couple of years, though due to the pandemic they still haven’t met in person. Where they do meet is in their shared belief in the value of a collaborative, cross-industry approach. Especially seeing as customers, often having fewer resources to maintain in-house skill levels, are increasingly looking for complete solutions that cover the development of the tooling, the planning of the machining, training the staff and giving programming support.
There are two aspects to this new reality – Seco, its customers (both Tier One suppliers and the aircraft OEM itself) and other sub-suppliers need to collaborate to develop the right solutions. The other is the constant need for innovation and partnerships to keep one step ahead, which led Seco to establish its UK-based Innovation Hub.
“If you look at the machining of the pylon, Seco is of course making the tools to machine parts. But what makes us different from our competitors is the people we have sitting in the UK at the Innovation Hub, who have the background and contacts with the cam manufacturers, the coolant suppliers and the companies making the work holding. We even have relationships with universities that are doing studies on the machining of these materials,” explains Gary Meyers.
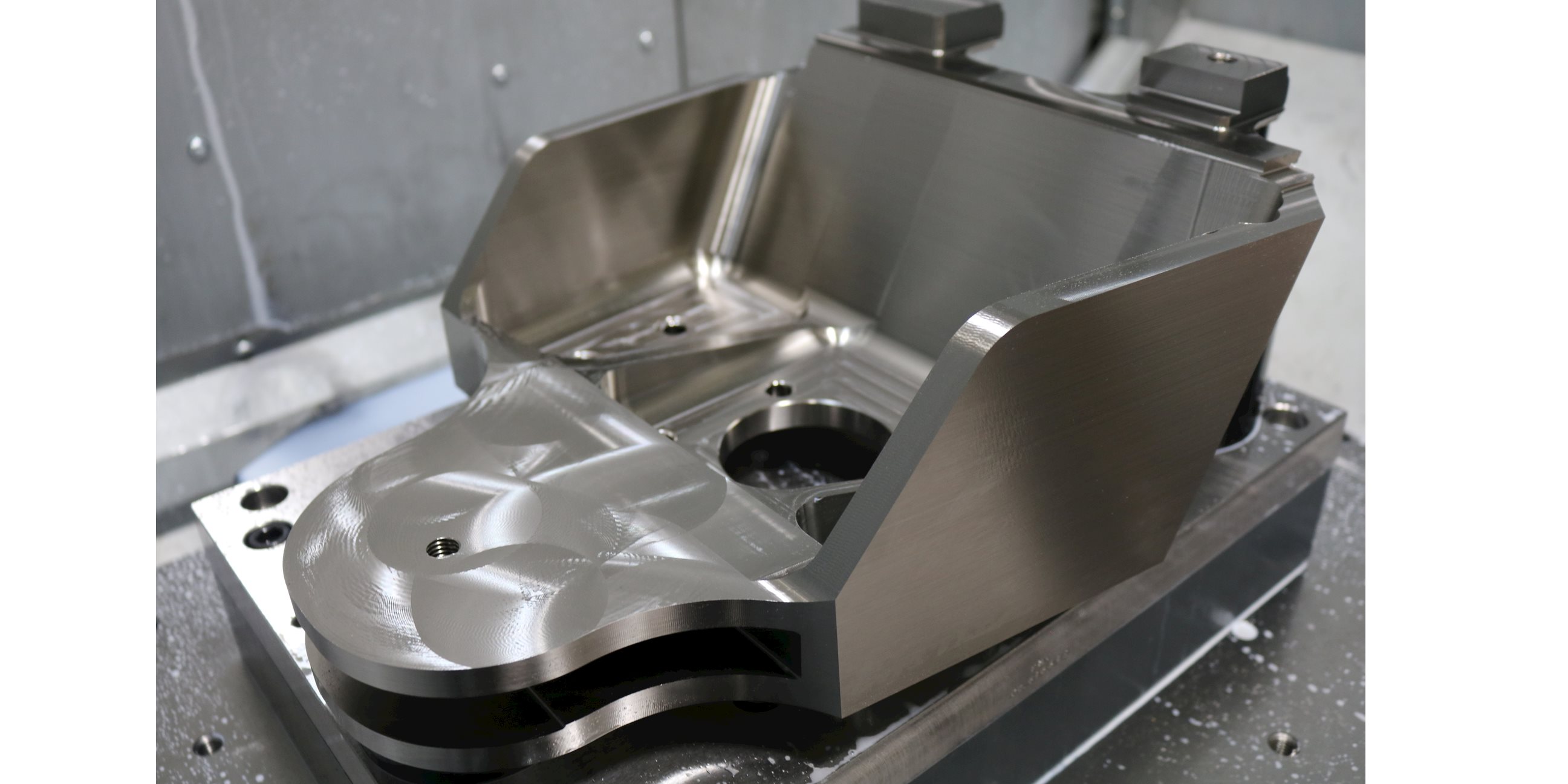
“So we have a great portfolio, and there’s nothing on the pylon that we can’t machine. We’re competing at a world-class level. And it’s not just the tool. We have people like Joe and Innovation Hub colleagues who know how to apply the processes and how to apply the tools. They really know the customers’ needs, and that gives us the edge in terms of these types of components.”
In turn this drives quality. Rather than Seco coming in cold to a project with a tool for an already defined application, it’s involved at the earliest possible stage.
“We look at the titanium structural components to see what customers need, what we have in our portfolio, and what we can develop to increase tool life and boost the customer’s productivity,” says Meyers.
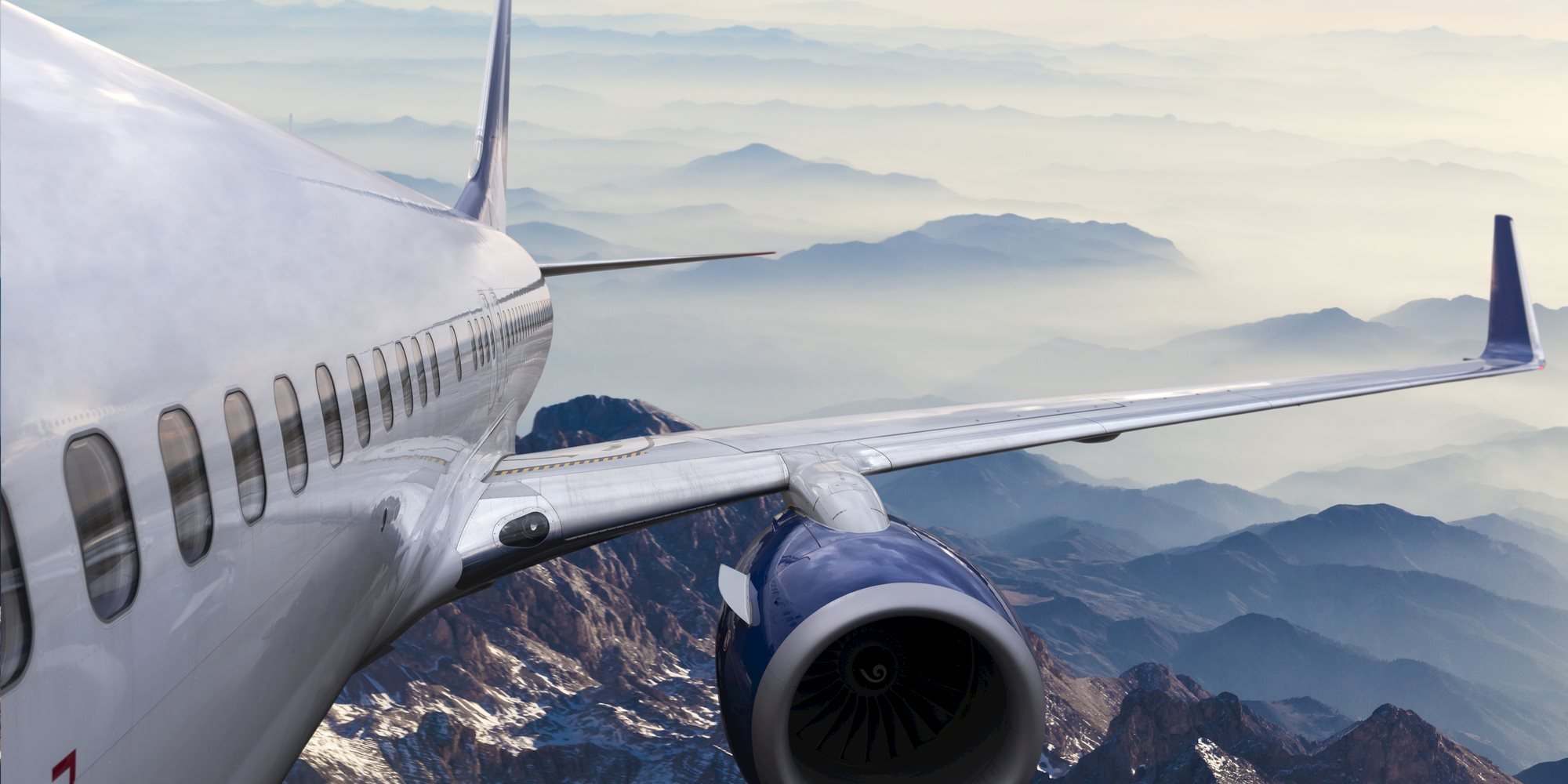
The aerospace industry is slower to embrace changes such as the use of alternative materials including 3D-printed parts, and sustainability is less of a consideration on a pylon, when there are so many safety tests to satisfy before anything can be introduced. Here, titanium still reigns supreme. Nevertheless, the industry is changing.
“Robotisation and other digital technologies are coming in, and we are developing our digital offer to respond to this,” says Joe Gooding. “Some companies are looking at minimum quantity lubrication and even oil-free CO2 methods in the cutting process. Wire Arc Additive Manufacturing, where the plate is welded with titanium wire arc to the shape in which you need to create with the template, is also starting to develop and may affect pylon manufacture in the future. But it all comes down to consistent part quality – that has to be the same every single time.”
And, adds Gary Meyers, “When it comes to being a tool supplier, if you’ve already heard about a new trend on the market, you’re already too late because it takes you years to catch up. The important thing is to have your finger on the pulse and understand what the customer needs are early on, so you can be part of the development. Then it’s your competitors who have to catch up with you.”
It’s clear then that Seco Tools has the critical skills and products needed to keep making this critical component for years to come.
Contact us here