Material and machining trends in aerospace manufacturing
Aerospace manufacturers are chasing sustainability through lower fuel consumption while retaining performance and safety, making material science and machining increasingly significant. Advanced materials expert Professor Martin Jackson discusses the current trends.
SUSTAINABILITY AND NEW MATERIALS ARE HAVING PROFOUND EFFECTS ON AIRCRAFT MANUFACTURING
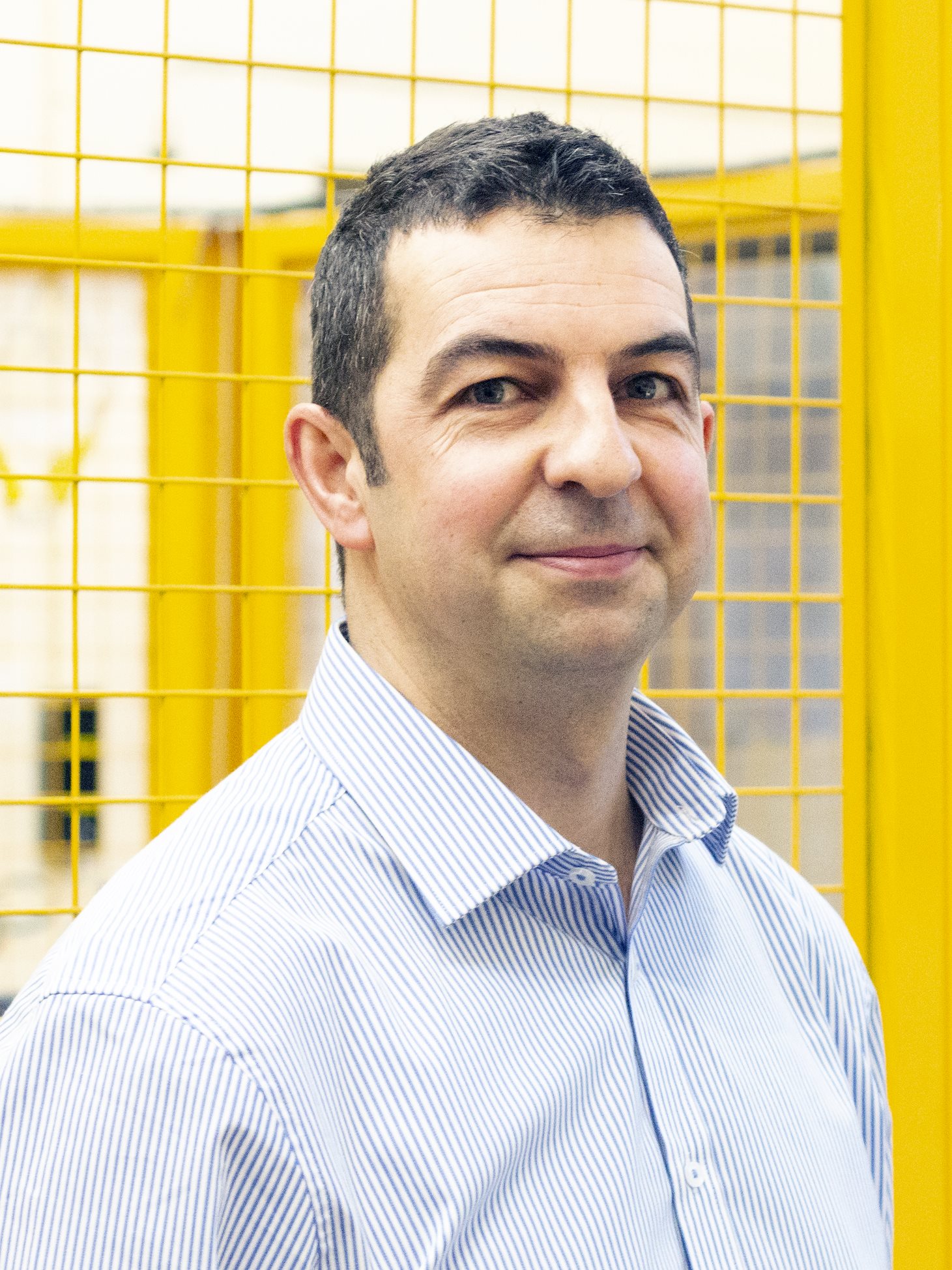
One person with an inside perspective on these changes is Martin Jackson, Professor of Advanced Materials Processing at the University of Sheffield, and a world-renowned expert in titanium alloys. He’s worked with the aerospace industry for more than 25 years, but as the industry works towards a net-zero-emission manufacturing goal he says: “There’s no better time to be a materials scientist.”
Here, Professor Jackson explains some of the current trends in aerospace manufacturing:
The aviation industry has targeted net-zero carbon emissions by 2050, but commercial electric-powered or hydrogen-fueled planes are still some way off. Aerospace OEMs must find ways to produce aircraft with lower fuel consumption, and that means lighter yet stronger materials, and that creates challenges.
“We’re exploring the use of high-end alloys such as titanium, nickel-based super alloys and high-strength steels to increase the combustion temperature in the aero engine, making it more efficient,” Jackson explains.
“THAT’S EVERYTHING YOU WANT FROM AN AERO ENGINE IF YOU’RE FLYING, BUT YOU’VE GOT TO BE ABLE TO MANUFACTURE AND PROCESS THEM TOO. THESE MATERIALS ARE COSTLY AND HARD TO MACHINE. MACHINING IS PROBABLY THE MOST IMPORTANT AND EXPENSIVE PROCESS WHEN MAKING AN AERO ENGINE.”
The aerospace industry is now making more machinable alloys. These aren’t as strong but have better machinability, requiring fewer tools and resulting in better metal removal rates for a near-net shape.
“This is where Seco are very good,” says Jackson. “They’re developing great tools and great coatings to overcome these issues to machine those components into near-net shapes.”
High-pressure turbine discs now being produced from powder through additive manufacturing (3D printing). It’s a clever new approach to a longstanding problem of chemistry.
“The nickel-based superalloys in gas turbine engine disc components are very difficult to melt because the chemistry is so variable from center to edge,” explains Jackson. “To try and homogenize that through forging is difficult.”
“By using a powder, manufacturers can get more homogeneous chemistry and then center that powder through hot isostatic pressing.”
However, although titanium is costly to melt and forge, Professor Jackson says it won’t be rendered in powder form anytime soon.
“A powder version of titanium is no good due to the concerns over stray particles that would cause issues further down the line.”
In striving for sustainable aircraft, the aerospace industry shouldn’t forget sustainable manufacturing.
“We also need to make the manufacturing process and supply chain more sustainable, with fewer tools, more rapid machining with less energy and less cutting fluid used.”
The forging of a billet in aero engine manufacturing can see up to 90% cut away, with just 10% of the material used for the aircraft. The industry has traditionally given the swarf to scrap merchants but it’s now being pressed to recycle it more effectively. Safety and performance standards prevent it being reconstituted for aero engines, but it’s robust enough for use in other industries, including automotive.
“There’s a real drive now, especially in the UK, for better recycling. The industry has got to be part of that journey and help the supply chain recycle,” says Jackson.
One key area of research for Martin Jackson’s team is the effects of machining on the structural integrity of aircraft parts. The challenge lies with reconciling quick and effective machining to satisfy OEMs’ cost margins and ensuring component life for these safety-critical features.
“There’s a balance, and Seco are very good at this, of not just providing tools and walking away but being part of the whole journey,” says Jackson.
“I work a lot with Rachid M’Saoubi and his team at Seco and we are looking at the ideas of using technology to provide ‘digital fingerprints’ and ‘digital passports’ for materials. Seco wants to understand the effects on the component of their tools, in terms of microstructural and surface damage and the life of that component in service.
“IT’S ABOUT PROVIDING TOOLING SOLUTIONS AND NOT JUST THE TOOL AS A COMMODITY. HOW SHOULD YOU PROCESS THE PART? WE’RE LOOKING AT DIFFERENT METAL REMOVAL RATES, FEED RATES AND MACHINE SPEEDS; NOT JUST THE EFFECT ON TOOL LIFE.
“The tool insert may last 15 minutes rather than 10 minutes, but what does that leave behind on the component and how can you access that more effectively? We want to understand the structural integrity of that part when it goes onto the engine.”
Seco Tools is working very closely with the end users and the material providers to ensure they are provided with tools that are efficient at removing material in a cost-effective way but without creating damage.
“Aerospace OEMs spending £100m GBP (€112m) a year just on milling tools alone. By making small reductions in the amount of time you use a Seco tool, even a couple of minutes, that can have a massive impact over the course of a year.”
Martin Jackson says the past five years has seen a much more collaborative approach within the industry.
“There has been a realization at the early technical readiness levels that the tool manufacturer, tool provider, material provider and the end user must work together.
“There’s been great consortium building, there’s been no egos, and the research has accelerated due to that. For example, our team at Sheffield University have worked on various projects with Seco, Rolls-Royce and Timet, the UK producer of Titanium for aero engines.
“Different stakeholders come with different demands, and there’s always a healthy tension between the lifing engineer working with Seco to make sure the tooling doesn’t leave any damage on the part, versus the manufacturing engineer who’s under pressure to get as many of these high-pressure discs out the door as possible. But if you can manage that you can really accelerate the research and development.”
Gas turbine aero engines will be around for some years yet, and Martin Jackson believes Seco Tools can help keep steering the industry in more sustainable, cost-effective directions.
“I think Seco are ‘lean edge’ in terms of understanding the effects of tooling on structural integrity. I also think there’s an awareness of where the next processes will be, for example additive manufacturing. “They’re ahead of the game compared with other tooling providers because they seem to have an awareness of what’s on the horizon. Some of the projects they’re doing with us are looking at these emerging processes so they understand what the tooling needs would be.
“And Seco Tools is always part of the conversation when it comes to discussing and examining emerging processes for what would be the next aero engine powertrain.”