Aerospace Pylon
Wing pylons raise complexity to new heights, with forged titanium, complex geometry and tough standards. Meet these challenges with enhanced productivity.The increased importance of sustainability has pushed aerospace manufacturing to create new aircraft designs with more-efficient materials, fuel consumption and carbon footprint. At the same time, customers pressure aerospace component manufacturers to boost their output volume and reduce costs. Harder, highly heat-resistant, difficult-to-machine lightweight materials increase production challenges.
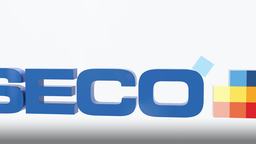
Take wing pylons, for example, designed in pairs that must bolt together perfectly to form finished parts, with intricate shapes that complicate workholding and rigidity. When these titanium forgings ship to manufacturers, part batches can display 5-10 mm dimensional variances. Programmed machining processes rely on consistency, which makes it difficult to finalize production sequences, select tooling, set up machines and begin to cut parts.
Machine tools must make extensive use of onboard metrology to adjust for variable dimensions. These measurements can raise cycle times by between 5%-10%, but without them, manufacturers risk vibration, overloaded tools and expensive scrapped parts.
To meet these cascading challenges, wing pylon manufacturers must rely on their tooling suppliers for durable, optimized cutting tools that produce these parts efficiently. A tooling supplier with extensive industry experience and part expertise can partner with manufacturers to offer sound advice that helps optimize machining and increase output.
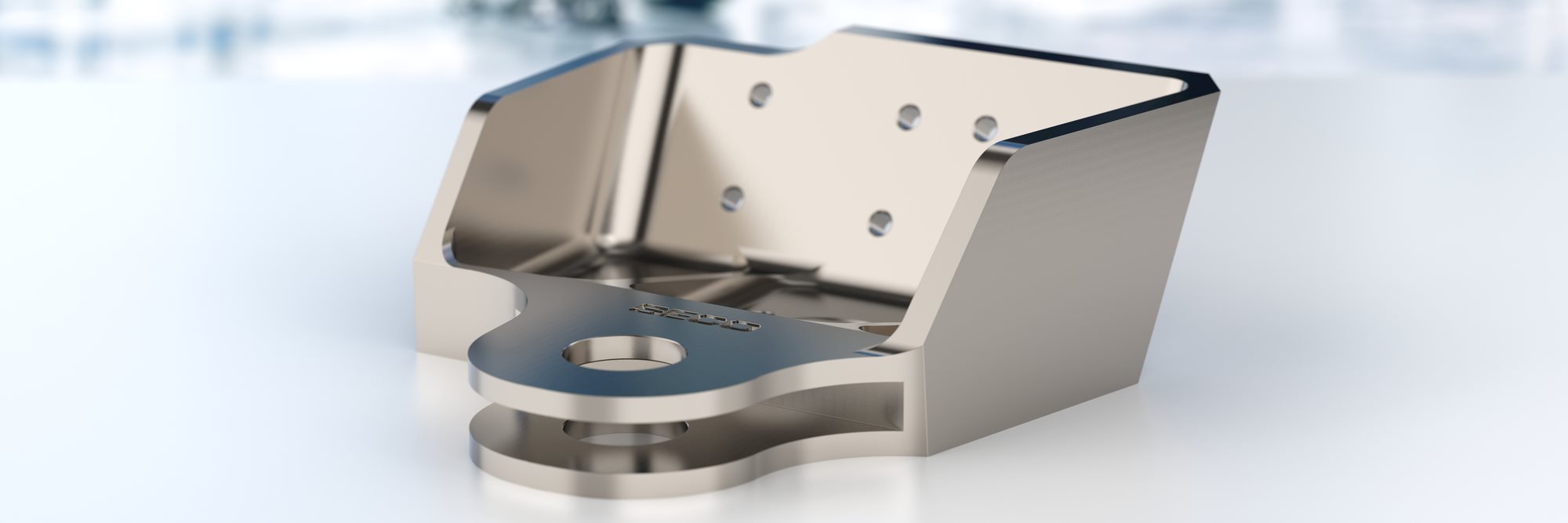
Just as axles, brakes, rearview mirrors and door locks differ from one vehicle model and manufacturer to another, so do wing pylons from one airframe and aircraft manufacturer to the next. These parts originate as titanium forgings, and although every supplier of a specific pylon uses the same 3D part model, each die is different. The dimensions of a finished forging may vary by 5-10 mm from one workpiece to another and one batch of parts to the next, even when a die functions ideally. Because of the unpredictable dimensions of these parts and their faces, manufacturers need onboard metrology to match demanding specifications. These variances also make it more difficult to select tools and finalize machining programs.
Forged titanium forms a difficult-to-machine outer skin. Additionally, the material can self harden during the machining process, increasing the risk of tool breakage, which makes it essential to choose and maintain the right coolant. Along with the material itself and its machining properties, the pockets involved in this part design require the use of long tools that can be difficult to select, let alone stabilize. Depths of cut and uneven or interrupted cuts further complicate the quest for ideal results.
The lengthy process of producing a wing pylon includes up to five setups, each with an associated clamping, to accommodate the slots and pocket depth of the design. This complex machining sequence challenges aircraft parts manufacturers to maintain accuracy and repeatability. Part geometry makes workholding difficult, especially on the 5-axis machine tools typically used for wing pylon production. Given the precision required for these parts, and the fact that each pylon consists of a pair of halves that must bolt together perfectly, aircraft parts manufacturers need machines equipped with onboard metrology to ensure consistency throughout production.
When aircraft parts manufacturing companies can make more parts with fewer machines, they reduce costs per part and raise production volumes for increased profitability. To achieve meaningful efficiency, they need a reliable process that produces consistently high-quality parts. These large, high-value parts require hundreds of dollars of tooling and 20-30 hours of machining, making scrap a costly waste. As a result, when manufacturers look to automation for a production boost, they must factor in an increase of 5%-10% in cycle time for metrology because of part variances.
The airplane wing pylon roughing stage involves many challenges, including production trade-offs to achieve high material removal rates (MRR) without stressing the metal unnecessarily. The pocket includes many features that require long tools to reach. These tools can cause vibration, which in turn reduces part quality and tool life. Because of the workpiece-to-workpiece variance of forged parts, manufacturers may encounter unfavorable cutting conditions that can cause scrapped parts and damaged tools.
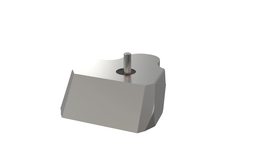
The Seco solutions:
The JS720 end mill series offers stable milling and optimal MRR during the complex process of pocket roughing. This tool series provides an excellent choice for dynamic milling. To create the many mounting and part mating holes in the pocket, Performax® indexable insert drills provide an optimal choice.
To remove a large amount of material on a radial axis and achieve precise slot dimensions with an outstanding surface finish, the unique design of the 335.25 adjustable pocket disc mill cutter uses inserts with up to four cutting edges, various corner radii and insert grades. For flexibility, this disc mill cutter series is available in a range of diameters. Even while cutting titanium, XNHQ carbide inserts achieve optimal tool life.
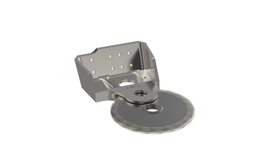
The Seco solution:
Success in helical milling operations demands excellent part geometry and surface quality, combined with fast cuts even in the inconsistent cutting conditions of complex forged parts. TURBO helical end milling cutters can achieve high feeds, large depths of cut and high MRR. To accomplish these results with long tool life, excellent precision and stable operation, the tool design creates optimal contact between tool body and insert. The R220.69 single-cutting edge single-sided inserts use a strong center screw aligned with cutting forces and include a wiper flat for surface optimization. The XOEX1204 inserts offer an additional option.
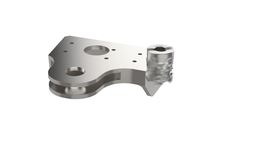
The Seco solution:
High-performance solid carbide square shoulder end mills provide high productivity throughout long tool life. The outstanding price/performance ratio of the JS522 universal two-flute end mill produces flexible machining on large batches of parts so manufacturers can optimize processes and reduce cycle times. This improved end mill design matches up precisely with the machining challenges of forged titanium.
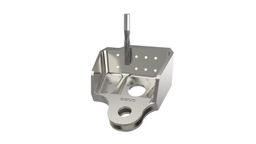
The Seco solution:
A tooling supplier with long experience and a deep understanding of the aerospace industry can guide manufacturers toward better results with deep expertise and great tooling. Beyond machining processes themselves, a supplier can offer additional services that help manufacturers improve their efficiency and productivity, including consulting expertise, professional training, tool recycling and more.
Contact us here