Lift-off for Mettis Group
This UK company manufactures and assembles precision-forged and machined components for a variety of industries, but it’s the post-Covid ‘bounceback’ in the aerospace sector which is propelling its rapid growth. A key challenge for the company is to recruit enough manpower to keep up.
The past three years have been a turbulent time for the global aerospace industry. At the start of 2020 business was booming. Then, almost overnight, the Covid-19 pandemic left many airlines struggling to survive; original equipment manufacturers’ order books for new aircraft dried up. But after the world emerged from its enforced hibernation, demand for air travel soared and the aerospace business started flourishing again.
As a key manufacturer and assembler of 600 different parts to aerospace OEMs such as Rolls-Royce, Airbus and Boeing, British company Mettis Group has felt every one of those sudden changes in altitude. After Covid hit Mettis was forced to lay off around 200 people, but in 2022 business was so good that it took on 200 new employees.
The main reason for the company’s excellent recovery is a rapidly filling order book. However, there are also favourable trends in global aerospace at work, including a move towards lighter, smaller planes in a bid to reduce fuel consumption and meet mandatory sustainability targets.
“Traditional engine blades form a part of our ‘bread and butter’ business, but we’re now seeing a different type of blade to increase the efficiency of an engine lifespan,” says Rothwell. “We’re transitioning with that trend and seeing exponential growth as a result.”
With business going so well one of the biggest challenges is finding enough workers to meet productivity requirements. In Mettis’ case this is amplified by the heavy-duty nature of the hot forging process. The most powerful forge unit weighs 12,000 tonnes and the factory is a dark, smelly and dirty environment, where employees can be left with coal-black faces when they finish their shift.
“It’s very heavy manual work. Most of the workforce on the factory floor is male; not by choice – we want to see more women and diversity - but because of the physical demands of the roles,” explains Lenka Price, Senior HR Operational Lead.
“On a daily basis they are manoeuvring parts that are 40-odd kilos and the size of a table. Even with the equipment to help them do that, it’s very heavy, physical work that’s typically seen as being more suited to men. And most of those men at the forge are of the same bulky shape. We do see people who don’t stay here long due to the demands of the job.”
One of the main ways to help Mettis meet productivity and talent demands is outreach to local schools and the local community in and around the factory site in the English West Midlands town of Redditch. That’s something Price and her HR colleagues are doing, with the help of rising talents such as James Thornton, a recent graduate of the company’s apprenticeship programme (see sidebar).
Another smart way to adapt with the changing aerospace industry is the creation of strategic partnerships with suppliers such as Seco Tools.
“The old transactional relationship no longer applies,” says Emma Rothwell.
“We understand the value that Seco Tools can bring to Mettis, in terms of different expertise, new information and new technologies that can be integrated into moving forward a particular project or part, such as an aeroplane turbine blade.
“We have expert engineers on site, but they may not have everything at their fingertips. The benefit of the Seco collaboration is that we can understand what’s available out in the wider market. This is complemented by Seco Tools’ vending solutions as well as its innovation hub, which allows Mettis to put different materials to the test. We can do that with different stakeholders around a machine getting first-hand experience with different materials that we can then present to our customer.”
As a young engineer on the ‘shop floor’, James Thornton certainly sees the benefits of Seco Tools’ input.
“We get cutting tips from Seco on the tungsten carbide end mills and on the ball-nose drills. We also use their expertise in welding, the cutting before the welding and, after the welding and machining, we get an overall impression of the actual job itself,” he explains.
“That expertise makes the job a lot smoother and for me I get that pride of seeing that part get made. It’s great when you see that final product and think: ‘Wow! I was involved in making that’.”
Founded: 1939.
Location: Redditch, England.
Number of employees: 500.
Business: Hot forging specialist with three forges, working with aerospace, automotive and defence industries. ‘One-stop shop’ capability with hot forging, machining, finishing, spray painting, bolting, sealing ready for OEM to fit. Or forging parts to let customers do the rest.
James Thornton is a recent graduate of the Mettis apprenticeship scheme, but the 22-year-old has had quite a journey to his dream job. 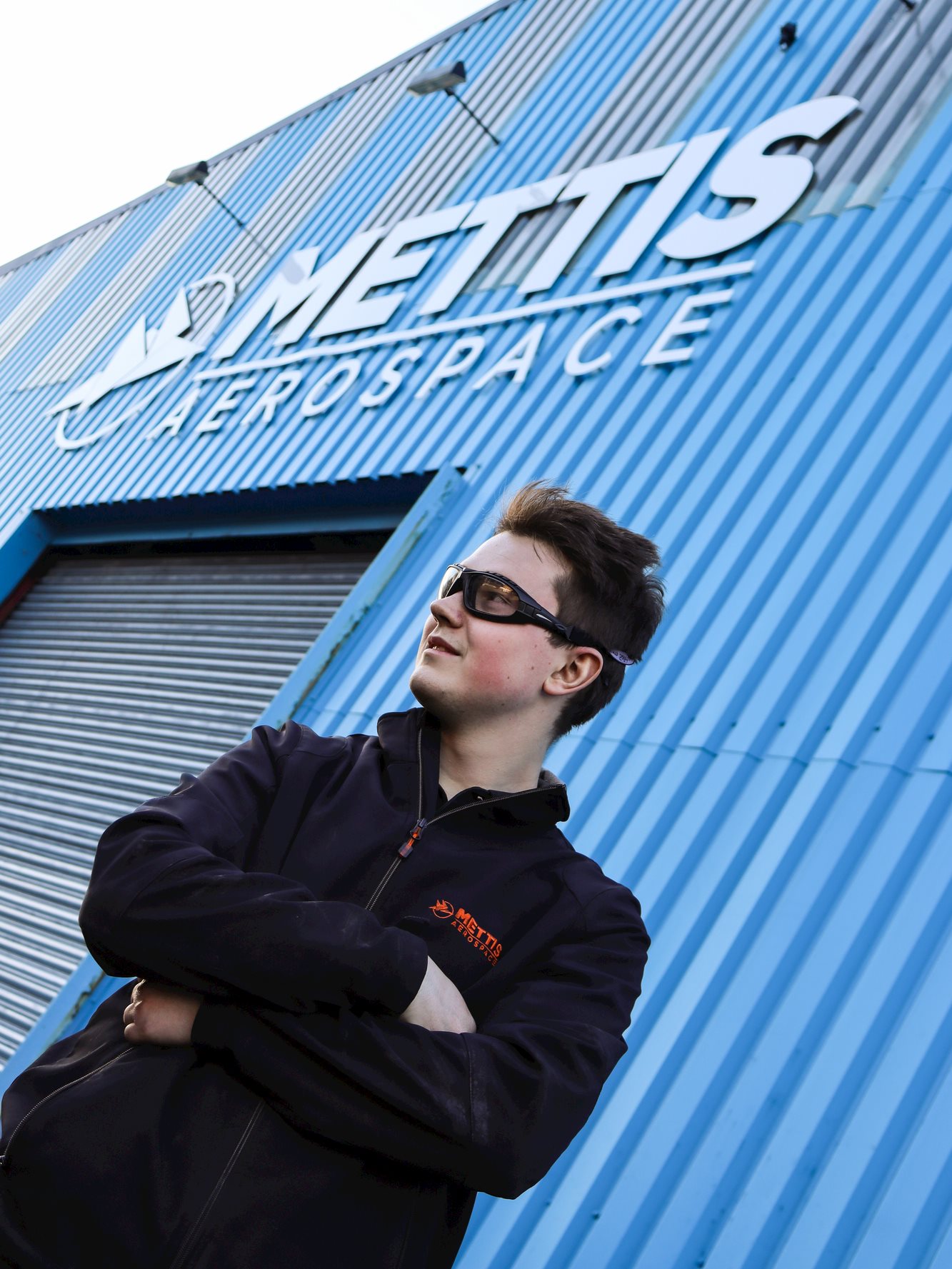
“I did a level two diploma in Manufacturing Technology at Dudley College. It covered different industries including aerospace, automotive, defence,” he says.
“While I was studying, I started my working career at McDonald’s. Then, once I got the level two qualification, I was offered an opportunity in maintenance engineering on the mechanical side, working in the sewage industry.
“I started that when I was 17, but it wasn’t really my thing, so I then went into the casting environment, making gravity casting dies and low and high-pressure dies.”
However, the pandemic intervened, with the resulting economic slowdown causing James to lose his job. He was only 19. Thankfully, he soon saw the advert for a toolmaking apprenticeship at Mettis Group.
“I jumped at it, handed in my CV, explained my experiences, and told them I was willing to learn. I got the job.”
Now James is enjoying life at Mettis.
“I always want to better myself every day when I come in to work. I’ve done three years of my apprenticeship here and have qualified. But now I feel like I’ve started again. Even though I’m qualified, I’m still an apprentice in a way because every day’s a school day!”
And, as someone who grew up in a family working in heavy industry, the demands of the job at Mettis hold no fears. “It is quite heavy-duty, but I don’t mind that because I like seeing a part, a piece of material made of steel and watch it going on the machine, and then seeing it finally made.
“I’m enjoying the job and I want to further my skills not only the shop floor but also on the actual software, with CAM work. I hope that maybe one day I can be a supervisor.”