Why gear skiving can be good news for jet turbine disc manufacturers
If the gear skiving process can take place on a single, dedicated machine or a multi-tasking machine center, it can reduce manufacturing cycles for large batch production, addressing aerospace industry costs, safety, material and sustainability needs.Gear skiving, also known as power skiving, is where a cutting tool gradually engages with a workpiece to create gear teeth through a shaving or slicing action. It is not a new process and was actually patented in Germany way back in 1910.
Yet for many years gear skiving tended to be used much less often than gear hobbing, due to many five-axle machines not possessing the right hardware to enable enough revs per minute to carry out the skiving process in a fast and stable manner, and at the right level of tolerance. The process also suffered from wear and tear, as well as the precision and reliability of the machine.
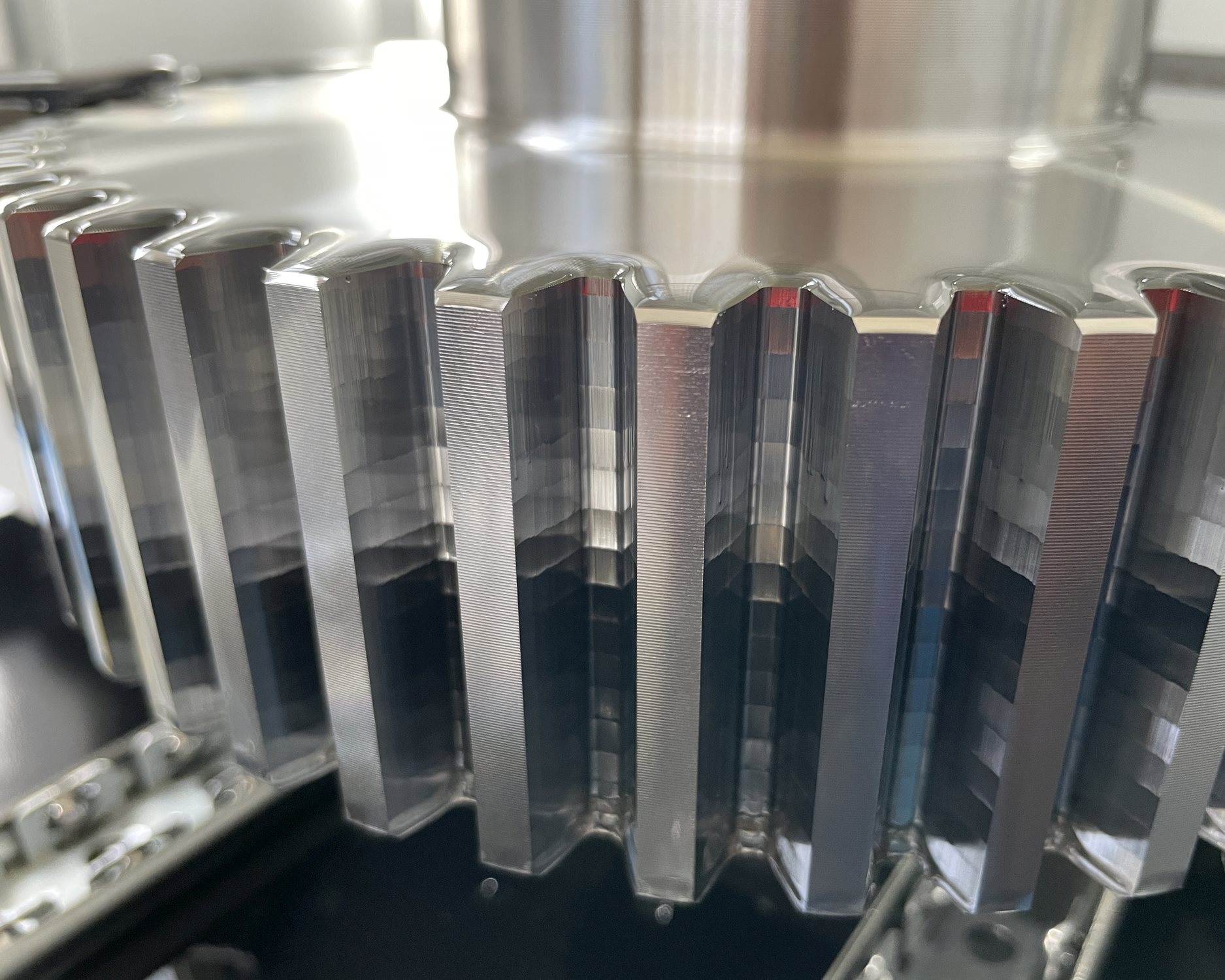
However, over the past decade gear skiving has been enjoying a renaissance.
Firstly, the rise of dedicated and programmable CNC machines and multi-tool centers with direct drive torque motors have helped address the speed and precision issues. Today, the use of carbide tools improves tool life and speed, while coating technologies are also better.
And secondly, the high production efficiency and significantly shorter cycle times are godsends for jet turbine disc manufacturers, who have to produce gears that meet stringent surface finish requirements, while minimizing scrap through repeatable quality and achieving challenging cost efficiency targets, among other things.
Gear hobbing is probably the most well-known method for manufacturing and machining gears, due to its versatility making it suitable for both small and large production runs. It certainly has its benefits with regard to producing gears with high accuracy, excellent surface finish and consistency.
However, the main drawback of gear hobbing is that it can only run on external gears or splines, making them unsuitable for internal gears and splines that are features of jet turbine discs. It also takes longer, sometimes a few hours, whereas gear skiving is like removing a small chip extremely fast, peeling away the layer by 0.5 to 0.6mm with each step. In fact, gear skiving’s alternative designation of power skiving is well named because it can be three to four times faster than gear hobbing, with cycle times of minutes instead of hours.

In addition to this, if you need a short exit – for example, if you have a wall like you have on a turbine disc – using gear hobbing can lead to a collision with the stock, which can cause deviations. In this sense, gear skiving has more maneuverability because the shape of the skiving head is like an ellipse and the exit distance will be less than half that of gear hobbing.
The benefits of gear skiving are:
Speed and flexibility: Gear skiving is a quick and flexible process that can be used to produce a variety of gear types, including helical, spur, and internal gears. Gear skiving offers flexibility that enables manufacturers to easily adapt the process to different turbine disc designs and specifications.
Producing more accurate components: Above all, gear skiving is highly accurate. It can produce gear shapes that are sufficiently complex and precise gear shapes to meet the exacting demands of airplane turbine disc manufacturers, where there is no room for error. Gears produced by gear skiving mesh together smoothly on the turbine disc and in turn that reduces wear and tear, as well as improving this crucial component’s overall performance levels.
Less risk of tolerance deviations: Because gear skiving is a continuous cutting process there are no interruptions during the machining operation, which avoids the risk of tolerance deviations. This and the lesser heat generation of gear skiving can result in smoother and more consistent surface finishes, improving the structural quality of the turbine disc. These smooth surface finishes help minimize friction on the turbine disc, which lessens the risk of the stress fatigue that causes dangerous cracks in parts. Again, this helps to address the aerospace industry’s ever-present reliability and safety concerns.
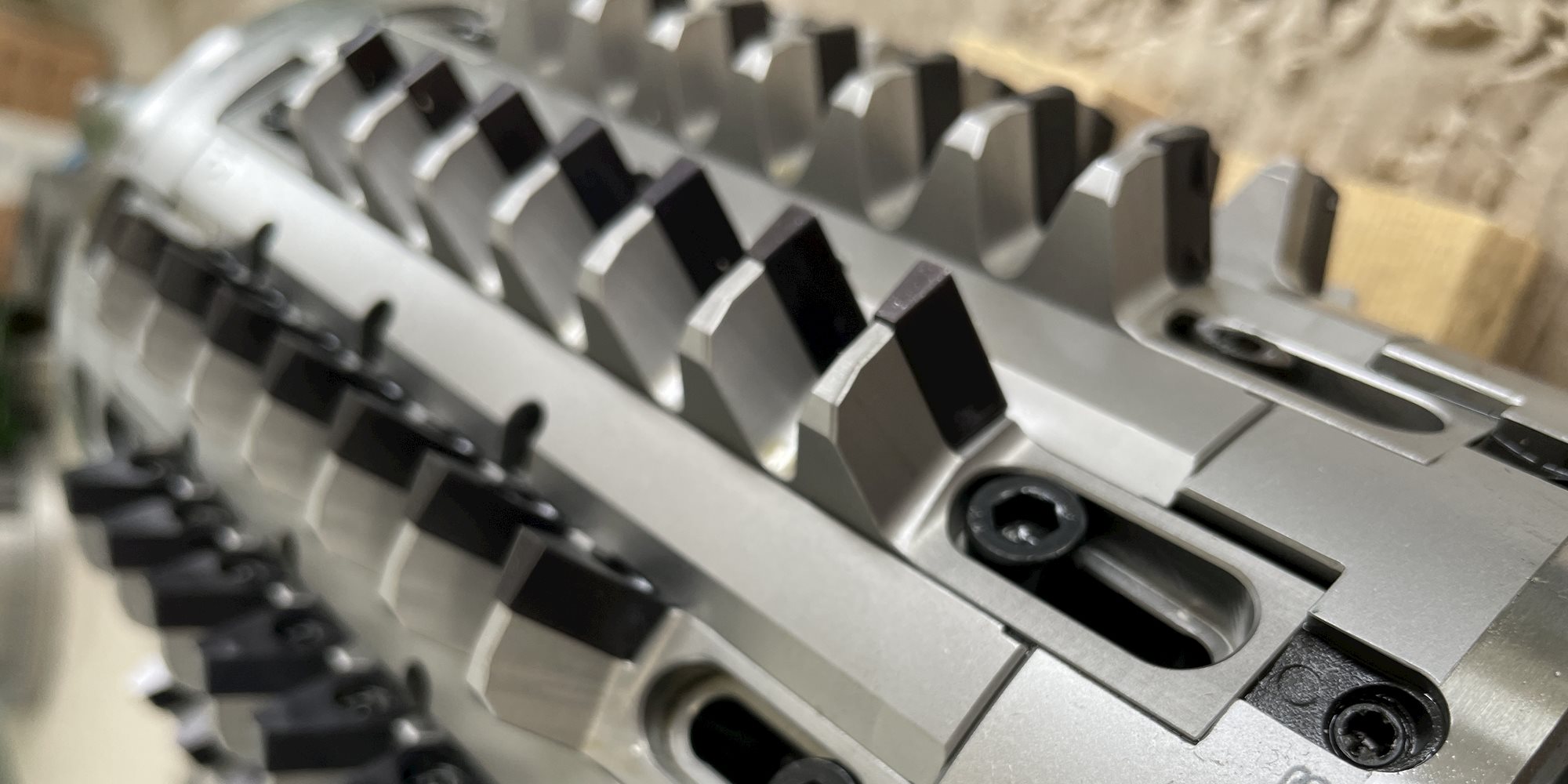
Less waste: The skiving process also generates less waste when compared to traditional methods like broaching. As material costs soar in the aerospace industry while cost pressures increase at the same time, this is particularly beneficial for aircraft turbine disc manufacturing. Precision and efficiency are also good news for lower energy consumption and shorter cycle times.
A closer process: There is also no need for a big exit with skiving. This means you can go closer to the bottom, get more length of spline or even a shorter component. As the aerospace industry chases weight reductions in a bid to reduce fuel consumption, flying costs and CO2 emissions, this is a vital attribute.
Longer tool life: Finally, modern gear skiving tools are built to last, often giving them longer tool life than some other cutting tools. Fewer tool changes mean more machining efficiency and less downtime, which also contribute to reducing the overall cost/production efficiency ratio.
The limitations of gear skiving are:

- Higher capital investment: When splining on dedicated gear machines, Seco gear-milling solutions can shorten cycle times significantly critical for large-batch production. However, such specialty machines for gear skiving involve higher initial capital investment and the inevitable production bottlenecks of installation.
- Set-up errors: The need to invest in new equipment also adds another machine to the overall disc manufacturing process, increasing the risk of set-up errors while consuming valuable production time.
- Challenges with lathe operating speed: Much also depends on the type of machine being used, and the revs per minute that can be achieved. Even today when using a CNC machine with direct drive torque motor, there can be challenges regarding the lathe operating speed. For gear skiving you need to control not only the speed but - millisecond after millisecond - the angular position of the component and the tool.
- Component size limitations: There is also a limit to skiving when you have large components (i.e. bigger than 800mm) with a small spline connection (i.e. smaller than 100mm). To reach the required cutting speed on a spline with a small diameter (like in turning), you need a highly synced RPM on the component (i.e. 1.000-2000 rpm), but large components require a large machine rotary table; and a large rotary table normally cannot rotate with a precise sync at high RPMs (300-800 rpm max). In this situation, shaping is the only way to machine them.
- Chip jumping and tilting: In addition, the chip can jump back and end up being re-machined, which is especially bad news if it goes onto the good part of the component. To combat this, the gear always needs to be cleaned. Finally, tilting can also be an issue because the groove clearance is larger compared with shaping.
There is no doubt that gear skiving has significant advantages when it comes to gear manufacturing for jet turbine discs, but these investment and gear skiving tooling challenges show that it is by no means a universal medicine.
To generate disc gear splines, aerospace manufacturers are increasingly using dedicated gear machines or opt for gear skiving on multi-tasking mill-turn machining centers.
If machine size, component size and exit distance are all okay, gear skiving offers enough speed and precision to make your machine available for other tasks.
And when splining on dedicated gear machines, Seco gear-milling solutions can shorten cycle times significantly critical for large-batch production. Gear skiving discs on multi-tasking machines with Seco gear skiving tools boosts part processing flexibility and eliminates the time-consuming setups required for multiple machine operations and cuts out related errors.
So if you have a modern encoder that’s fast enough then the machine is ready. Your CNC provider can open a sync option for you.
And of course, Seco Tools is there to help you assess your machining needs and how they relate to your business, to decide if gear skiving is the right option for you.
Contact a Seco expert for more information
Inline Content - Survey
Current code - 5fce8e61489f3034e74adc64