Production economy: Global optimization of a metal cutting process (part 1)
The manufacturing industry uses various production processes, including metal cutting, to produce workpieces with specified dimensions, shapes, tolerances and surface integrity. Metal cutting typically uses many different cutting tools from suppliers that offer big tool programs. This raises some questions. First, are all those tools really necessary? Second, are they used at the peak of their performance potential?
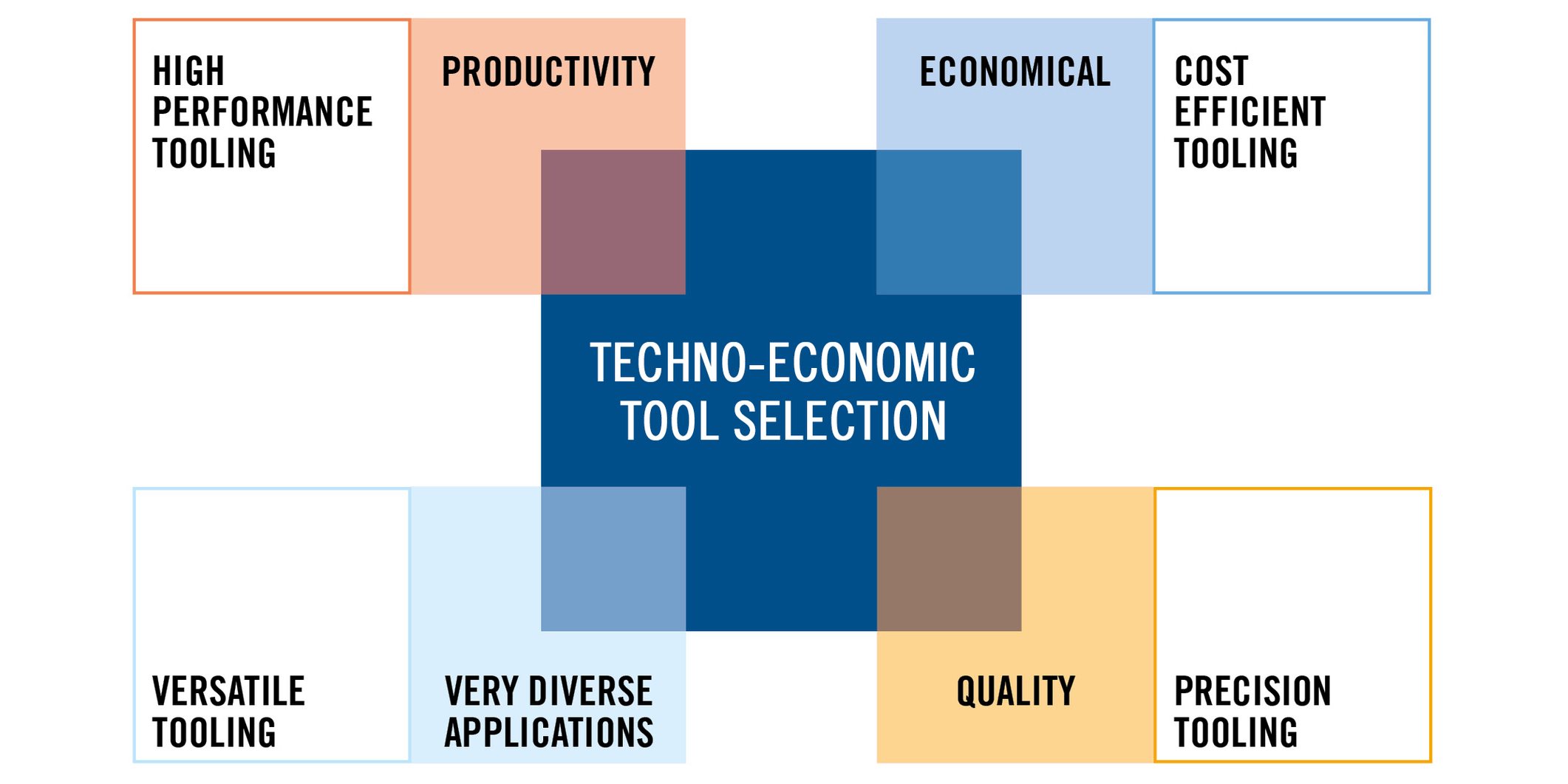
Metal cutting processes always include situations that can be improved. These often become bottlenecks that inhibit manufacturing companies from reaching their ultimate goal of efficiency and effectiveness.
TABLE OF CONTENT
Bottlenecks can affect productivity (the need to produce faster), cost efficiency (the need to produce at a lower cost), quality (the need for higher-quality finished workpieces). But manufacturers often overlook or forget about a fourth bottleneck: The ability to simplify and use fewer "different" cutting tools to achieve the final product. In this first article of a series of two, we concentrate on the first three bottlenecks. We cover the fourth one – rationalization and simplification – in the second article of the series.
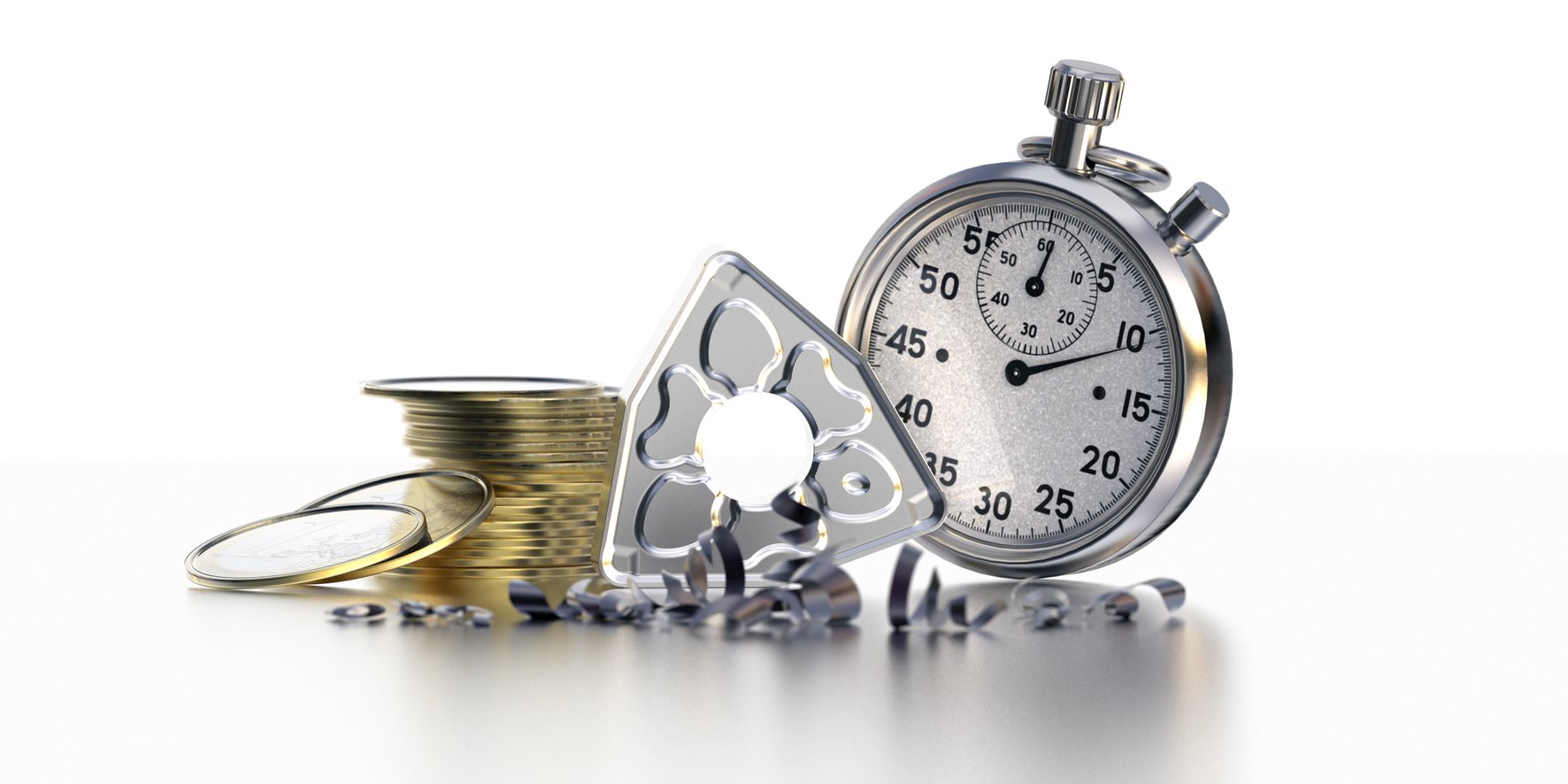
"Production economy" describes all the actions taken to optimize a metal cutting production process. The optimization goals can be multiple: higher productivity, lower process cost, greater predictability, broader application of production tools, better workpiece quality.
Stated more specifically, these goals represent maximum tool life, maximum number of workpieces per cutting edge, fixed cycle times, maximum profits, minimum tool and process costs, maximum production and coordinated tool indexing.
GLOBAL PRODUCTION ECONOMY IS DEFINED AS “ASSURING MAXIMUM SECURITY IN AND PREDICTABILITY OF THE PROCESS, WHILE MAINTAINING THE HIGHEST PRODUCTIVITY AND LOWEST PRODUCTION COSTS.” THIS DEFINITION LEADS THE WAY TO ACHIEVE THE FINAL GOAL OF EVERY MANUFACTURING PROCESS: PRODUCE CORRECT AND FINISHED WORKPIECES WITH MINIMUM EFFORT, IN THE SHORTEST TOTAL TIME AND AT THE LOWEST POSSIBLE COST.
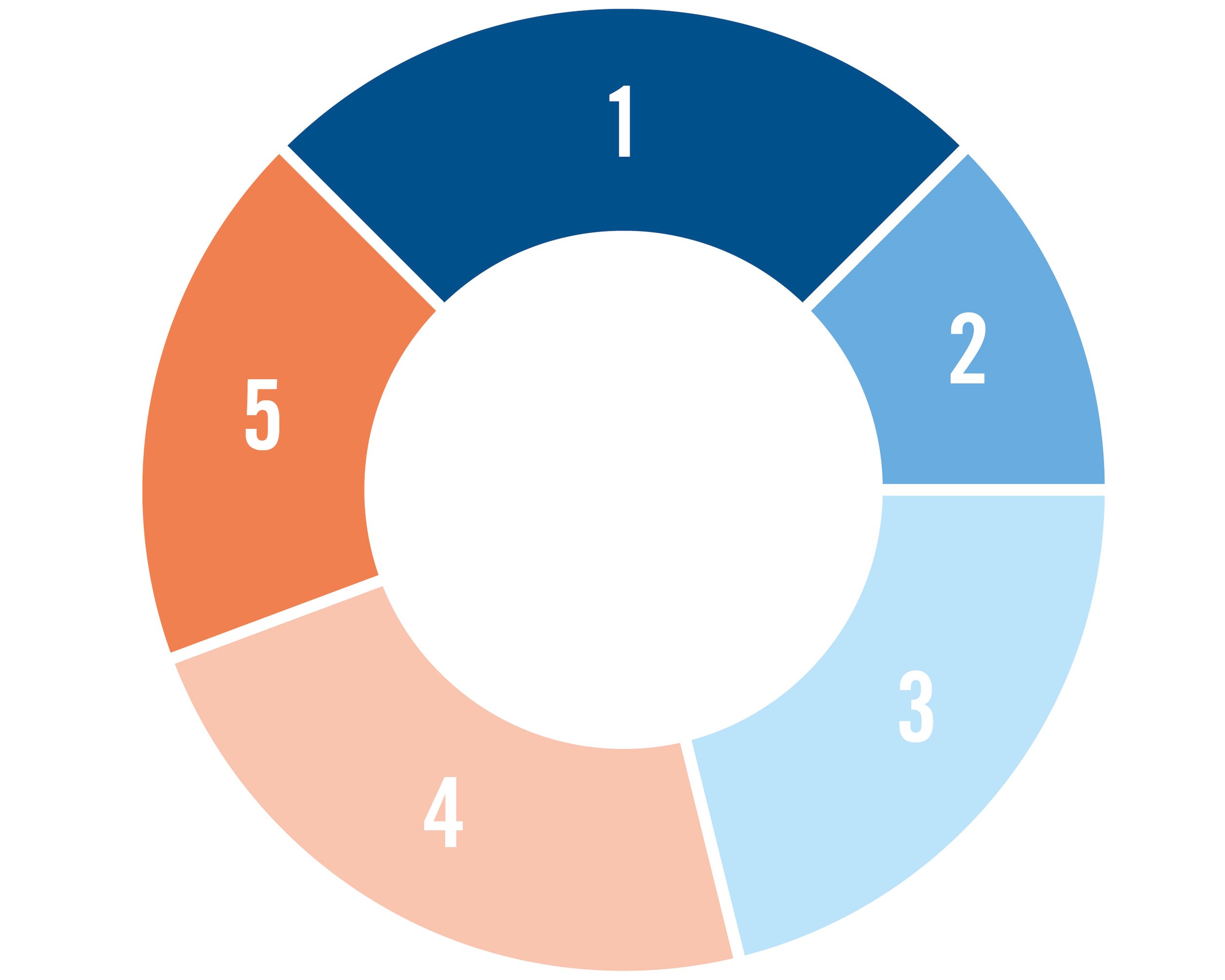 | 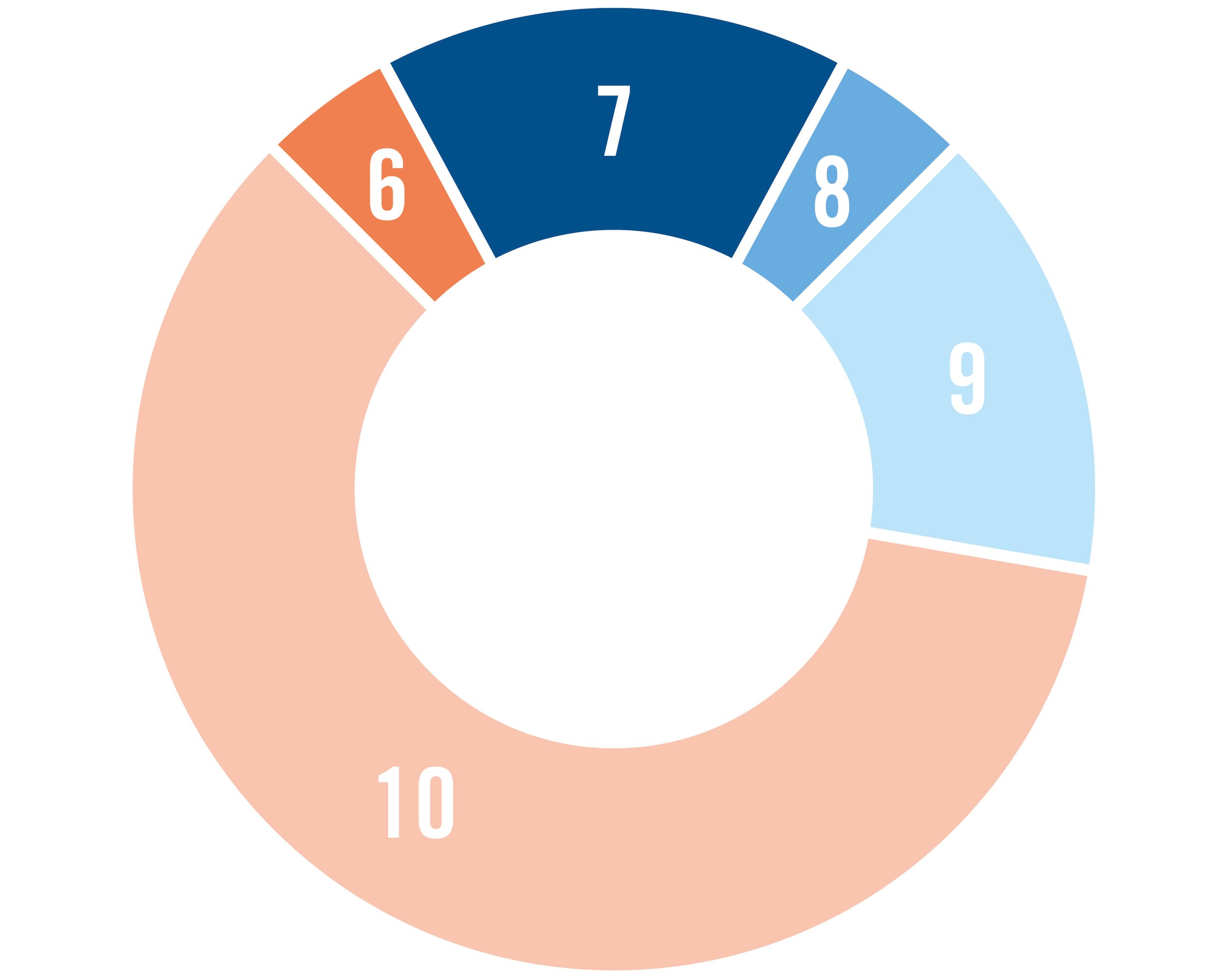 |
- Productive Time
- Tool Handling
- Problem Solving
- Workpiece Handling
- Machine Set-up
| 6. Cutting Tools 7. Coolant 8. Other tools 9. Overhead 10. Machine Labour |
Microeconomic analysis of costs and time in metal cutting production illustrates several points.
- The overall production process spends a large amount of time on machine setup, tool handling and problem solving. Easy-to-use, versatile tooling minimizes this and increases the time available for effective production.
- Once setup is complete, the next priority should be to use the available productive time as efficiently as possible.
- Tooling represents a relatively low percentage of the total cost picture. A well-used and functioning tool costs less than a non-working tool that halts production and thereby costs a fortune.
From a macroeconomic perspective, analysis of the total production process reveals more important elements. Prof. Stahl, Lund University Sweden, has done fundamental research in this field. Some observations:
- Many costs hide in the intermediate stocks of semi-finished workpieces. This teaches us that a microeconomic approach needs to be done very carefully. For example, optimized cutting times on machine tool A don't help if machine tool B forms the productivity bottleneck. This only creates extra costs in the form of semi-finished workpieces between the two machine tools. In this example, it would much better to optimize cutting costs on machine tool B This would mean lower productivity on machine tool A, but in the total process, machine tool B is the limiting factor on productivity.
- Additional dangers lurk in tool setup and tool indexing (and test runs related to them). These form an extra source of process unreliability. More importantly, however, tool setup and indexing are a major cause of workpiece quality losses. Many workpieces are scrapped for unacceptable quality directly after tool setup or indexing.
These observations help us define the steps to take toward our final target, an efficient and effective production process.
- Select the best possible production environment or working conditions (CAM, machine tool, work holding, coolant, etc.). These elements could become constraints later in the optimization process.
- Decide on a 1:1 optimization (microeconomic, with non-productive time already minimized) or a more global approach (macroeconomic, which does not concentrate solely on machining costs and times, but rather on total process costs and times). Include minimization of non-productive time in the optimization process.
- Select the best possible tooling adapted to the situation and the target (versatile, safe, best performing, etc.).
- Select the largest possible depth of cut for each operation (the minimum number of passes), based on the constraints of available machine power and torque, stability of workpiece fixturing and tool clamping.
- Select the highest possible feed for each operation. Consider constraints based on workpiece quality and the risk of tool failure.
- Calibrate depth of cut and feed for operational safety, considering chip formation and evacuation, vibration, fixture security and stability, workpiece deformation, etc.
- Select appropriate machining optimization criteria (minimum cost or maximum productivity).
- Use cutting speed to calibrate optimization criteria.
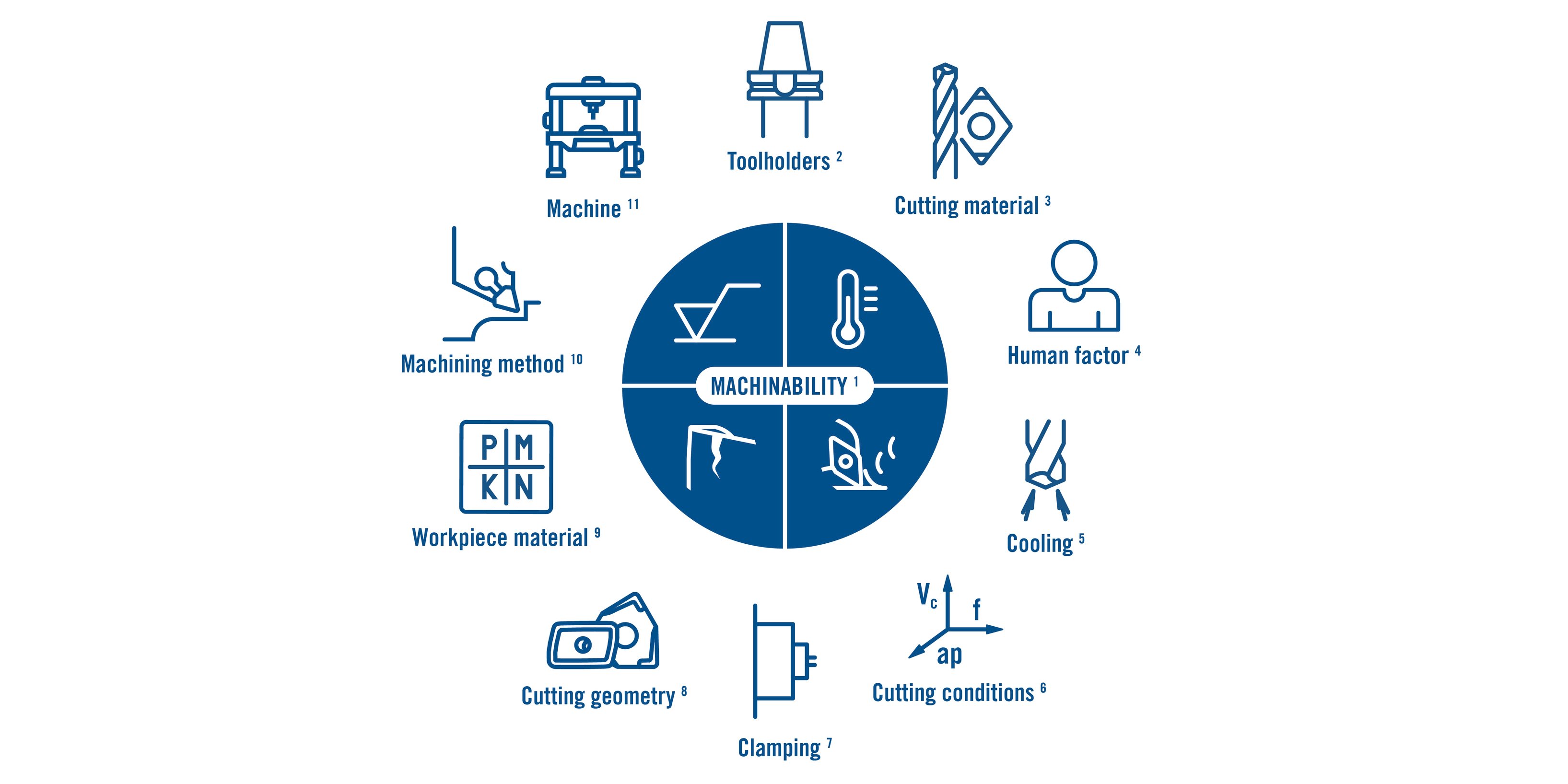
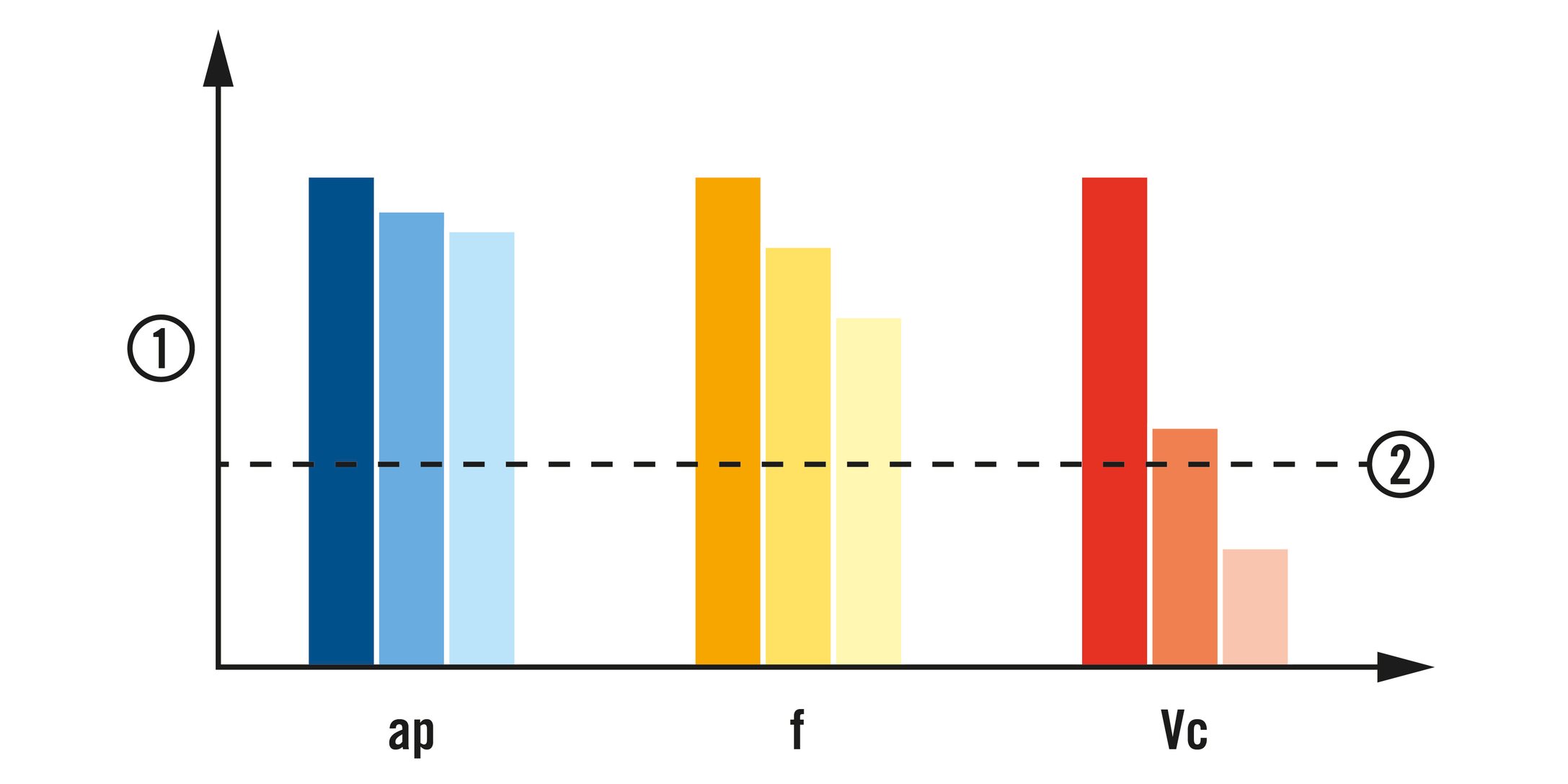
1. Tool Life
2. Minimum Security level
ap for 5 / 5.5 / 6 mm
f for 0.50 / 0.55 / 0.60 mm/rev
Vc for 200 / 220 / 240 m/min
As an example, increasing cutting conditions by 10% increases metal removal rate (productivity by 10%. But costs and security?
THROUGHOUT OPTIMIZATION, THE PRIMARY CONCERN ALWAYS MUST BE TO KEEP THE PROCESS SAFE AND RELIABLE. NO ONE IS INTERESTED IN FAST PRODUCTION OF CHEAP BUT DEFECTIVE WORKPIECES. MAXIMUM SECURITY AND PREDICTABILITY OF METAL CUTTING CAN BE ACHIEVED ONLY THROUGH A PROFOUND UNDERSTANDING OF THE PROCESS AND THE INTERACTION AMONG ALL ITS VARIABLES.
For example, which cutting condition should we increase to reduce machining time? We could work with depth of cut, feeds or cutting speeds. All three would help us achieve our target of reduced machining time, but the impact on process reliability is dramatically different depending on the cutting condition we alter. Depth of cut has no serious impact on tool life (security and costs, but stability can be an issue), but cutting speed makes a very big difference. High cutting speed influences cutting tool costs considerably, as well as process reliability.
The goal is to produce more effectively and efficiently, so all the different elements in the process should be well evaluated and weighted for their potential to endanger process reliability. If that risk is too high, these elements should be changed or modified, or their impact correctly considered, in the further optimization process.
Tooling Elements to Evaluate to Produce more effectively and efficiently
Tooling elements to evaluate | Risks of incorrect evaluation and application |
Tool selection criteria | Wrong tools for the wrong application |
Tool stock keeping | Tools missing where and when needed |
Tool maintenance | Higher tool consumption |
Chip formation and evacuation | Production stops for extra chip removal |
Cutting forces | Vibration and broken tools |
Tool wear | Production stops because of sudden breakage Bad quality of machined surfaces |
Heat generation | Short cutting-edge life |
Depth of cut and feed | Dangerous chip formation |
Cutting speed | Uncontrollable tool wear |
Now we focus on a situation in which all non-productive times have been minimized as much as possible, with tooling selected in line with a correctly defined global achievement goal. In other words, we enter the aforementioned optimization system at point 4.
4. Select the largest possible depth of cut for each operation (the minimum number of passes), based on the constraints of available machine power and torque, stability of workpiece fixturing and tool clamping.
5. Select the highest possible feed for each operation. Consider constraints based on workpiece quality and the risk of tool failure.
6. Calibrate depth of cut and feed for operational safety, considering chip formation and evacuation, vibration, fixture security and stability, workpiece deformation, etc.
7. Select appropriate machining optimization criteria (minimum cost or maximum productivity).
8. Use cutting speed to calibrate optimization criteria.
An individual metal cutting process should create high Metal Removal Rates (MRR = productivity) at the lowest possible cost. To achieve this, we work with the three cutting conditions.
- High feed and depth of cut
- Low or moderate cutting speed
- Maximum security and predictability, whilemaintaining highest productivity and lowest production costs
- Only if feed and depth of cut are low, this offers productivity and cost savings.
We already know that we have the highest interest in maximizing depths of cut and feeds to create higher MRR (steps 4, 5 and 6) for the highest possible process reliability. With that said, however, we must understand that this requires stable working conditions (stable tool clamping, good workpiece fixturing, machine tool stability and available cutting power). Once we reach these limits, we can switch to cutting speed for further fine tuning (steps 7 and 8).
When we evaluate the impact of cutting speed on a specific metal cutting process, we observe that higher cutting speeds increase productivity (MRR) but also increase costs (shorter tool life), whereas lower cutting speeds have the opposite effect: They lower costs but reduce productivity.
Production costs represent the sum of tool costs and machine costs
When we evaluate these costs, we observe increased cutting speeds produce lower costs, but that at a certain point, costs begin to increase again. At a certain cutting speed, tool life becomes so short and cutting edges must be replaced so often that decreased machine cost has a smaller effect on the total picture than fast-increasing tool cost. The goal is to find the cutting speed at which the sum of the two costs balances to the minimum total cost. This is called the economical cutting speed, and the accompanying tool life is called the economical tool life.*
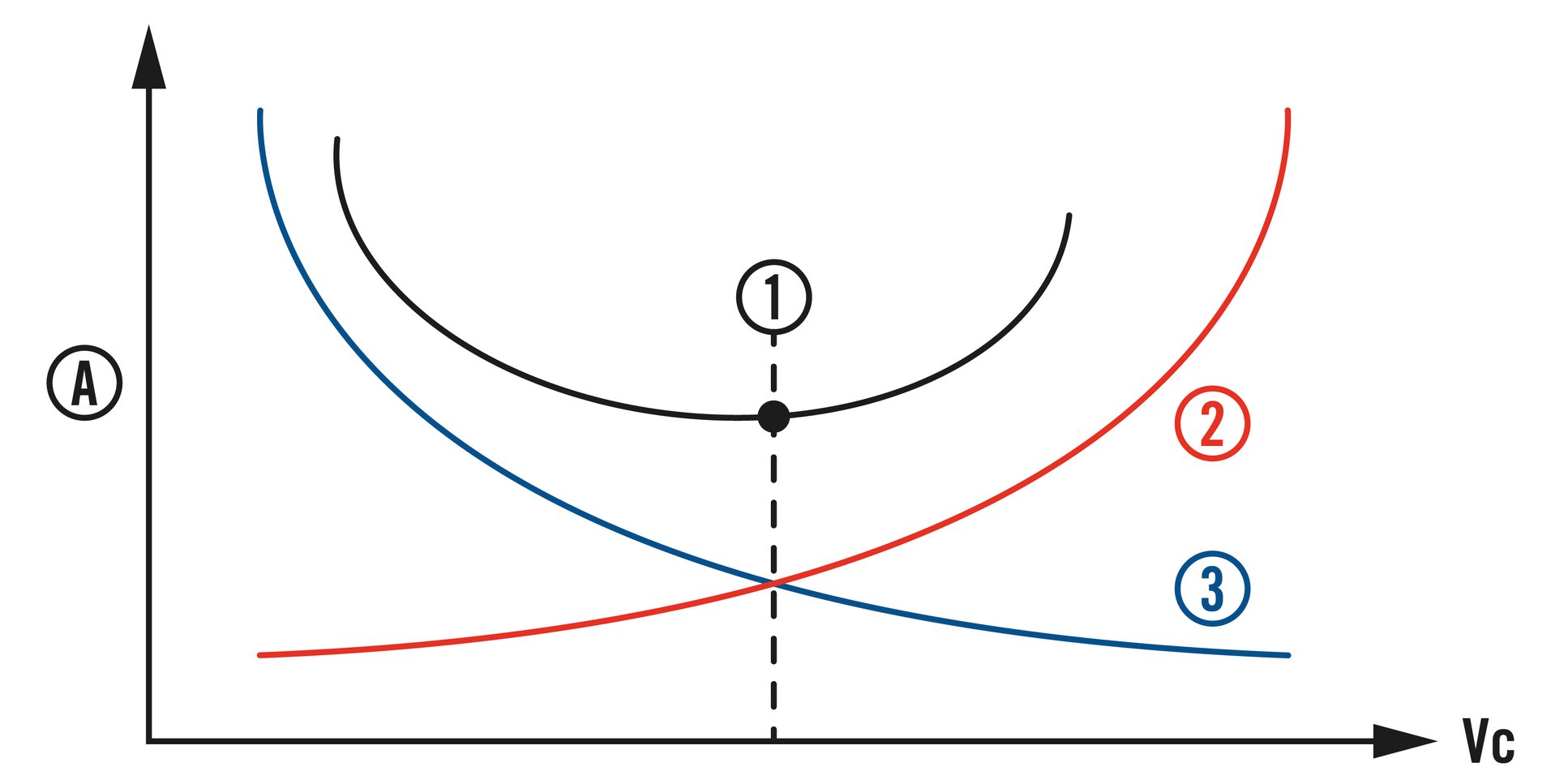
A. Machining Costs / workpiece
1. Economic Cutting Data
2. Tool Costs
3. Machine Costs
ECONOMIC CUTTING DATA FORMULA
1 Kg
TC = ( ___ - 1 ) ___________
m KL + CMT
m = Taylor constant
TC = Tool Life Minimum Cost
Kg = Tool Cost
KL = Machine Cost
CMT = Labour Cost
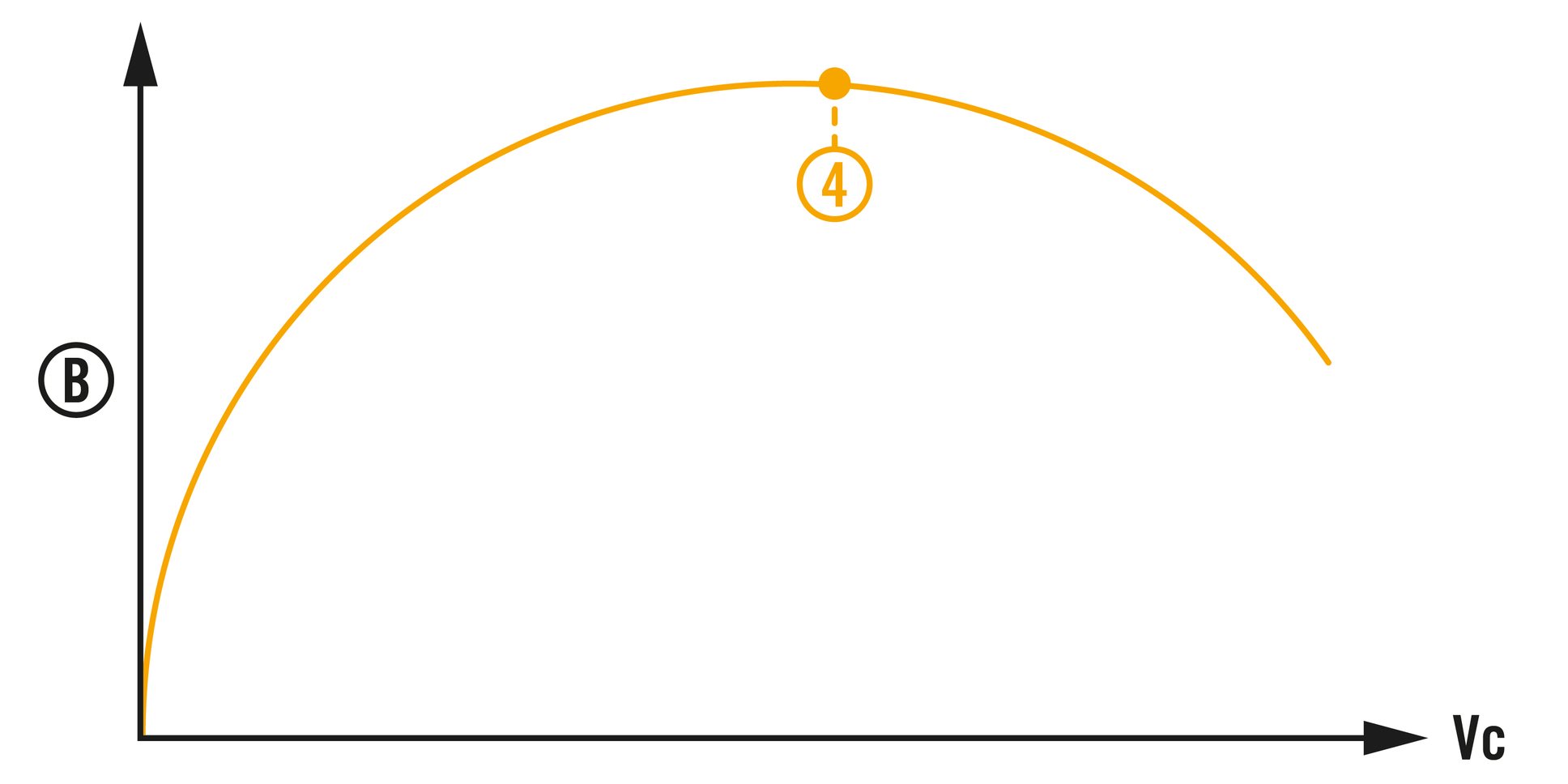
B. Productivity
4. Cutting Data for Maximum Production
ECONOMIC CUTTING DATA FORMULA
1
Tm = ( ___ - 1 ) TCT
m
m = Taylor constant
Tm = Tool Life Maximum Production
TCT = Time to Change the cutting edge
Production Economy - Minimum Cost and Maximum Productivity
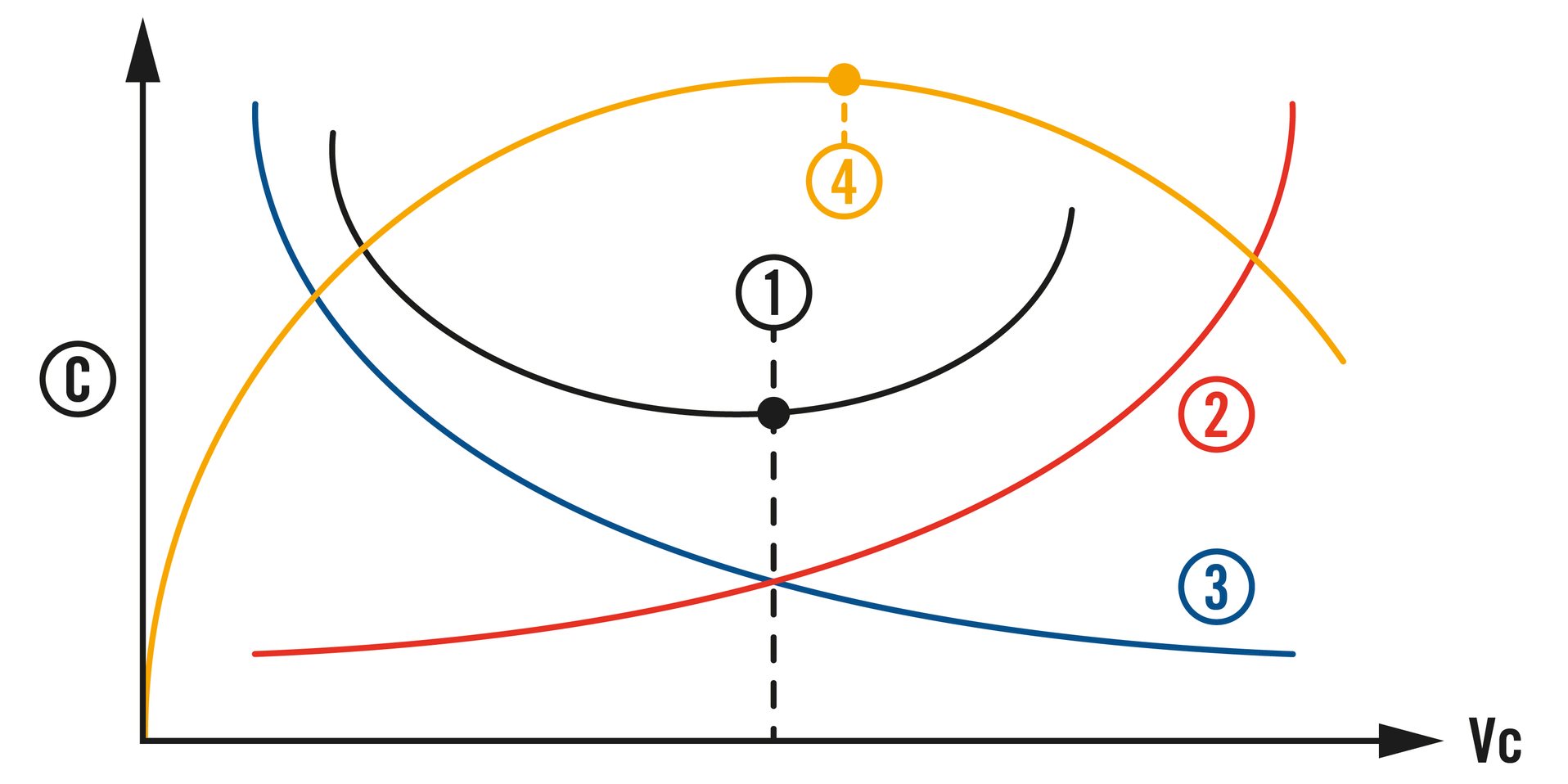
C. Minimum Cost and Maximum Production
1. Economic Cutting Data
2. Tool Costs
3. Machine Costs
4 Cutting Data for Maximum Production
We can take this same approach to productivity. When cutting speed increases, MRR goes up and productivity increases. At some cutting speed, however, this effect reverses. Tool life becomes so short that the time gained through faster cutting is less important than the time lost because of the indexing times of worn-out cutting edges. This balanced cutting speed is called the cutting speed for maximum production, and the corresponding tool life is the tool life for maximum production.*
WHEN WE BRING COST EFFICIENCY AND PRODUCTIVITY TOGETHER, WE CLEARLY SEE HOW TO DEFINE THE CORRECT CUTTING SPEED. WHEN THE SELECTED CUTTING SPEED APPROACHES BOTH THE ECONOMICAL CUTTING SPEED AND THE CUTTING SPEED FOR MAXIMUM PRODUCTION, THE CUTTING SPEED IS CALLED THE HIGH-EFFICIENCY CUTTING SPEED (THE HE CUTTING SPEED).
The principles described in this article will help the reader find the best possible combination of cutting conditions for a given application. This is referred to as a 1:1 optimization, meaning one application and one cutting tool. Without too much calculation, this approach makes it possible to achieve a better understanding of the impact of a changing production environment on cost and cutting time.
Observe that
- If machine costs go up (more expensive machine used), cutting costs also go up. Increased cutting speed can compensate for some of this.
- If tool costs go up (more expensive tools used), cutting costs also go up. Reduced cutting speed can compensate for part of this.
- Cutting costs go up with longer machine and tooling setup time, smaller batch sizes or greater amounts of material removal. Cutting speed modification cannot compensate for this.
- If machinability of the workpiece material deteriorates, cutting costs go up and the HE zone becomes narrower. Observe how the cost curve steepens. This requires a lower, well-selected cutting speed.
- Finally, observe that increased depth of cut and or feed reduces costs, with further fine tuning possible through reduced cutting speeds.
This leads us to a clear conclusion that in the above-mentioned cases, it always is beneficial to work with the highest possible depths of cut and feeds. These are the first steps in a 1:1 optimization strategy.
This first article gives the reader a very brief description of optimization strategies for metal cutting processes and presents a general optimization strategy. The purpose of this article is not to describe to the reader all the mathematical tools* for putting this strategy into action. More practical tools, such as Seco PCA, are available for those who want immediate action. Our follow-up article provides a detailed consideration of the first steps in the general optimization strategy. Those first steps are of even greater importance than the ones described in this first article. When we optimize a wrongly selected tool, we ease the pain but do not cure the disease.
Inline Content - Gridded Links
Tags: 'production_economics_part2'
Max links: 1
The SECO STEP education programs also provide further in-depth information on these subjects. On a regular basis, SECO organizes educational sessions about these and other subjects. Contact SECO for more information or visit our STEP page.
Contact Us for more information
*Both the economical cutting speed and the cutting speed for maximum production (and the corresponding economical tool life and tool life for maximum production) can be derived mathematically from the general cost and time equations for a metal cutting process and the generalized Taylor equations (adapted as necessary with correcting factors and elements) for metal cutting. However, these calculations fall outside the scope of this article. A broad overview and detailed description can be found in Chapter 9 of the book Metal Cutting, Theories and Models from Prof. Stahl, Lund University Sweden, published in cooperation with Seco. Observe, however, that these methods require fulfilment of several prerequisites. See also steps 1 to 6 in the optimization strategy, described in this article and the research done by Prof. Stahl in this field.
Inline Content - Survey
Current code - 5fce8e61489f3034e74adc64