Production economy: Global optimization of a metal cutting process (part 2)
A metal cutting process produces workpieces with specified dimensions and shapes, tolerances and surface integrity. This process typically uses many different tools. Are all those tools really needed – and are they used at their peak performance? Metal cutting processes always include situations that can be improved. These often become bottlenecks that inhibit manufacturing companies from reaching their ultimate goal of efficiency and effectiveness.
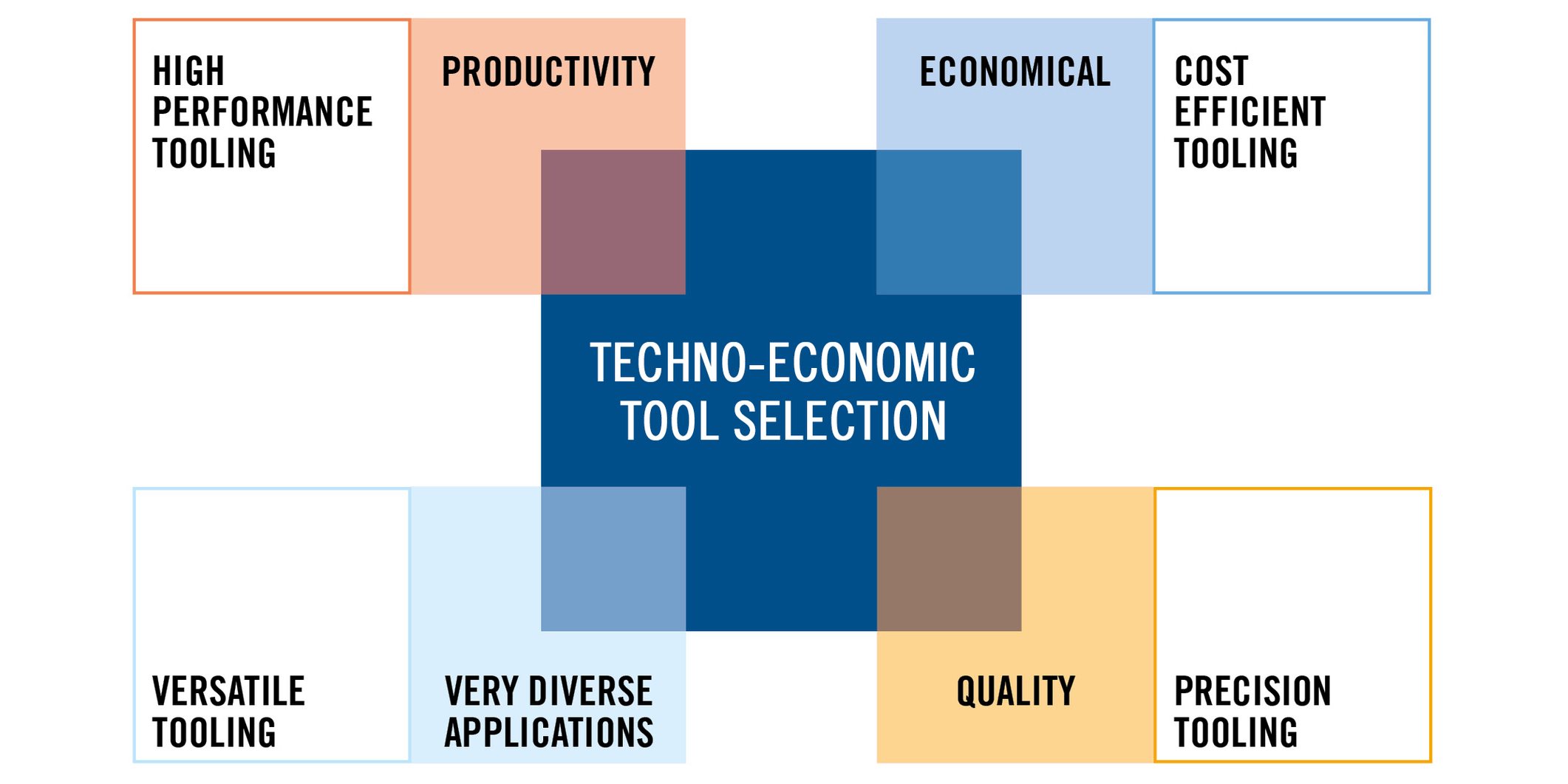
Bottlenecks can affect productivity (the need to produce faster), cost efficiency (the need to produce at a lower cost), quality (the need for higher-quality finished workpieces). But manufacturers often overlook or forget about a fourth bottleneck: The ability to simplify and use fewer "different" cutting tools to achieve the final product. In the first article of this series, we concentrated on the first three bottlenecks. The fourth bottleneck – rationalization and simplification – is the subject of this second article.
Increased productivity requires high-performance tooling and optimized cutting conditions. If cost efficiency is the target, tooling should be selected based on low cost per cutting edge and the choice of cutting conditions must be "in balance" with that selection. If workpiece quality is the priority, precision tooling is the correct approach. Whatever the target, each approach leads to different tools, and that also increases the risk of a too highly focused result.
In the quest for productivity, we must be careful not to pay too much attention to details (individual operations) and not enough to the total picture, namely the total floor-to-floor time required to produce the workpiece. If we introduce an extra cutting tool to gain 10 seconds in cutting time but we lose 10 minutes in setup and indexing time, are the time savings really advantageous to the total result?
TO SAVE HIDDEN COSTS, MAXIMIZE THE USE OF VERSATILE TOOLS AND ONLY USE SPECIFIC APPLICATION TOOLS WHERE THEY PROVIDE A MEASURABLE MAJOR COST OR PRODUCTIVITY BENEFIT.
To maximize cost efficiency, over emphasis on naked tooling cost (purchase cost, pure cutting cost) could lead to increased production costs (including all production and machine-tool costs).
Reduced cutting speeds increase tool life but also increase cutting time. This could endanger the tool utilization ratio (the number of operations performed with a specific number of cutting edges in a specific length of time). When we talk about costs, it is better to concentrate on tool utilization ratio than on tool life measured in minutes.
Additionally, overly high ambitions for workpiece quality (and technicians strive always for the best possible) put serious strains on costs and production times. One could ask, “How long would it take and how much would it cost to produce the worst workpiece possible that is still functionally acceptable?” Such an approach could well lead to serious productivity increases and cost reductions.
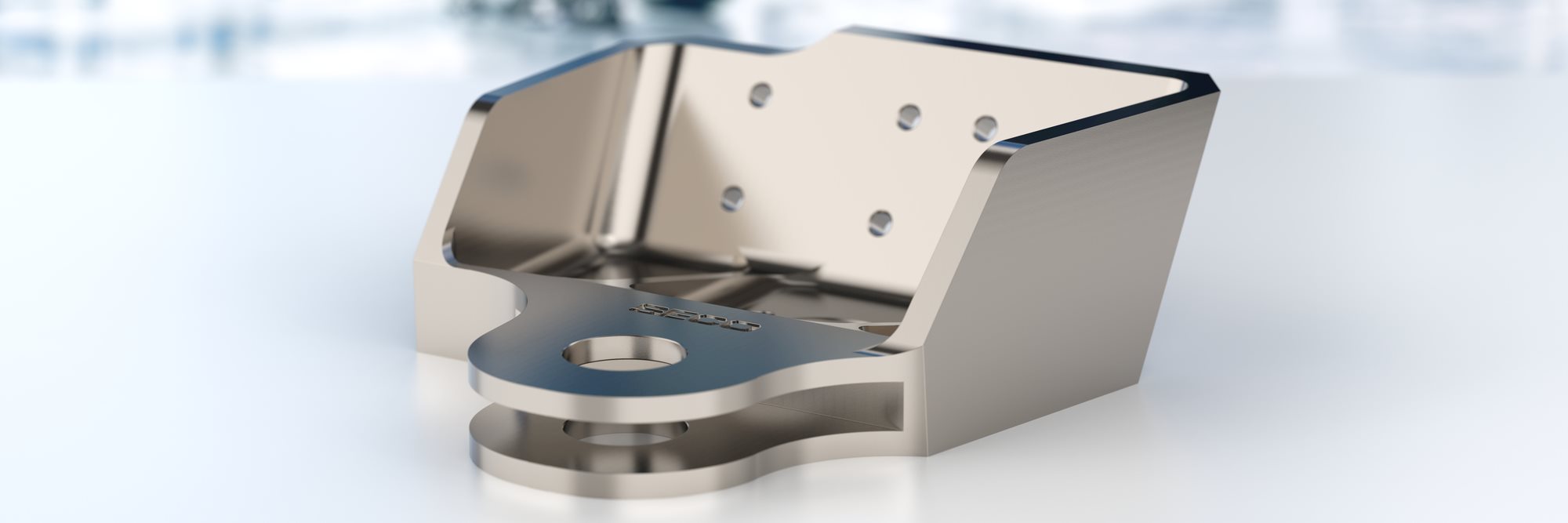
In his macroeconomic cost model, Professor Stahl of Lund University, Sweden* considers more global aspects alongside microeconomic elements (1:1 optimization). Such elements include, for example, production caused by "unforeseen" events such as tool failure (unreliable process, overly ambitious selection of cutting conditions, etc.), workpiece scrap rate (workpiece quality), setup times, and so on. Microeconomic models such as the ones described in the first article of this series need further development to take care of these and other elements.
In some cases, increased cutting speeds not only influence tool wear and tool life but also affect workpiece quality, which could lead to higher workpiece scrap rates. A microeconomic approach aims for the best performing tool (and cutting condition selection) for one application (a 1:1 optimization). A macroeconomic optimization strategy aims for the best performing tool that performs well over a broader application field. In doing so, it automatically reduces several important hidden cost factors and productivity reducers: Setup times, tool and cutting-edge indexing times, scrapped workpieces (e.g., because of test cuts), intermediate stocks of semi-finished workpieces, etc. In such an approach, versatile tooling very often provides the best solution to produce total productivity and cost efficiency.
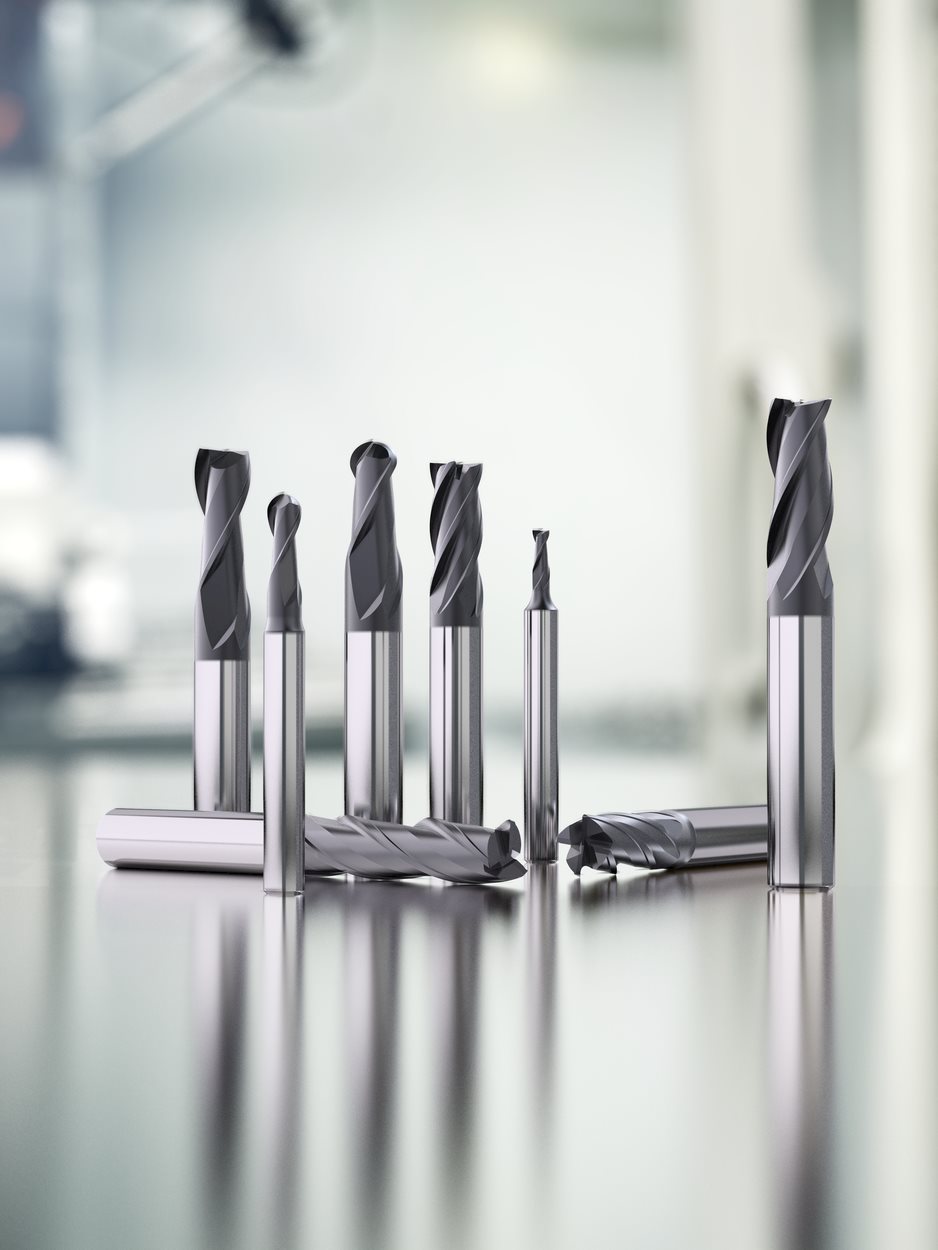
Of course, it would be advantageous to combine the two to create a productive and cost-efficient tool (1:1 optimization) that also can be applied to a broad range of applications (versatile approach). The Seco Turbo milling cutter range provides an example of such tooling.
These tools offer versatility and flexibility in a broad range of applications, combined with cost effectiveness and high performance. These cutters include technical features that lead to trouble-free production of high-quality finished workpieces.
Positive cutting geometry reduces power consumption, leads to longer tool life and enables increased depths of cut and feeds. This achieves the first steps toward an overall best-optimized process (working with high depths of cut and feed rates – see the total optimization strategy described in part one of this article series).
Every production situation is different and deserves its own appropriate approach. The most logical optimization strategy begins with a macroeconomic evaluation to ensure achievement of the overall target: A totally optimized production organization. Such an approach needs well-selected tooling that offers versatility and flexible use over a broader application window. This approach enables the versatile use of fewer different tools. In the bottleneck model, this is the versatile approach. Direct advantages of this approach include easier ordering procedures and stock management, fewer different tools in the workshop, less idle time (shorter machine setup and tool indexing, fewer test runs) and fewer problems from tool misuse. If this approach is applied by skilled machine tool operators and programmers who can select the correct cutting conditions for tools used in different applications, the easiest applicable method for process optimization becomes a reality. A skilled and knowledgeable operator can make every tool work, but even the best tool will not perform well in the hands of a less-competent machine operator.
Once this step is introduced, if necessary, two paths provide further detailed optimization (microeconomic optimization).
- On one path, Custom Engineered Tooling (CET) provides a typical approach to large-batch production. Specially developed tooling for specific applications keeps the number of different tools low and offers possibilities for 1:1 optimization. But CET carries rather high purchasing prices, potentially long delivery times, and extra time and effort for startup runs.
- The other road to optimization uses standard tooling for applications in which 1:1 optimization contributes to the goal of totally optimized production. However, both these approaches require the utmost care to avoid sacrificing total gains in productivity or cost efficiency for individual profits. This risk is especially high when people who lack an understanding of the total production picture make decisions based on an overly narrow view of a complex operation.
Throughout history, the mechanical workshop has been the subject of many productivity innovations. A significant step forward came with the introduction of a scientific approach to production economics by F.W. Taylor (Taylorisme).
The idea of "customizing" total throughput is a fairly recent concept in the mechanical workshop. The introduction of numerical controlled machines with Automatic Tool Changers dramatically reduced machine setup and tool indexing times. Workpiece manipulation robots and automatic workpiece fixturing pallet systems likewise minimize workpiece manipulation times. For some reason, however, metal cutting specialists proceeded directly from these innovations to optimization of tool engagement time (time in cut), completely overlooking tool handling optimization and problem-solving time – especially in situations with many diverse applications. This means that concentration on optimization of a detailed operation often causes more harm than good.
Seco Selection is the Seco green line of cutting tools for versatile and flexible use. Selection products offer the best tools available on the market for trouble-free production with guaranteed good performance over a broad range of applications. Selection products guarantee our customers a secure metal cutting process with high productivity levels and the lowest total production costs. Selection products offer: - Lower stock levels and higher availability.
- Ease of use and flexibility in many different applications.
- Simple, straightforward selection of cutting conditions.
- Easy, straightforward optimization of cutting conditions.
- Easy problem-solving techniques and advice for optimization strategies.
|
In the early 1990s, Seco already had recognized this situation and responded with the introduction of the "Selection approach" to bring some order to the chaos. When we minimize the number of different tools in the workshop and use versatile and flexible tooling, we can minimize tool handling and problem-solving time. This creates big gains in both costs and productivity. With this standardization step in place, we can achieve further 1:1 optimization. This total approach first minimizes the time required for tool manipulation, tool indexing, setup and test runs so it maximizes available production time. In a second step, we optimize maximized available production time through 1:1 optimizations toward further productivity or cost efficiency increases (see the first article in this series).
*Prof Stahl from Lund University, Sweden states as follows in Metal Cutting, Theories and Models, published in cooperation with Seco: “The performance of cutting processes has a decisive effect on the overall costs and the part costs involved. Rejection rates and the occurrence of downtimes are the two major factors affecting part costs. In contrast, the effects on part costs that the tool engagement time has are often overestimated. Modern production philosophies place greater emphasis on having a reliably functioning processing system than on achieving a maximal production speed. Production disturbances can be analyzed by use of a production performance matrix in which the effects that different factors have on the result parameters can be assessed. Models of processing costs can be divided into two major groups, micro- and macro-models, the micro-models being those most commonly employed. These models consider cutting processes from a rather narrow perspective. A particular advantage they possess is that they link processing data, such as that concerned with cutting speed and with feed, directly to part costs. The macro-economic models, more comprehensive and less specific, consider processing from a broader perspective. In these models, the overall time required for the manufacture of a given part plays a more decided role.
One advantage of macro-economic models is that they do not tend to result in the overestimation of costs connected with the cutting tools and with engagement times or in the underestimation of other major expenses that determine the overall costs in the manufacture of parts or of a product as a whole.”
This article offers a short description of the first steps to take toward a totally optimized metal cutting process. The total productivity and cost efficiency picture must be balanced before we accept every individual application based on a detailed 1:1 optimization.
As we evaluate productivity and costs, significant costs and time losses result from non-productive activities (workpiece manipulation, machine setup, tool setup and indexing, etc.), and standardized, versatile, easy-to-use tooling can offer many advantages. Once we take this step, we can achieve further improvements through careful investigation of situations in which 1:1 optimization can be beneficial.
Contact Us for more information
Inline Content - Survey
Current code - 5fce8e61489f3034e74adc64