The Importance of Cutting Fluids in Metal Cutting
Cutting fluids, commonly known as coolants, play a vital role in machining. Understanding the central role of cutting fluids and their effective utilization is fundamental for optimizing machining performance.Cutting fluids, commonly known as coolants, play a vital role in machining. They assume multiple essential functions, such as enhancing the machining operation, swarf evacuation efficiency, and elevating the quality of machined parts. In this article, we will explore the critical roles of cutting fluids in machining, examine the various types of cutting fluids available, explain the diverse delivery methods, and underscore the importance of pressure, flow, and direction. Understanding the central role of cutting fluids and their effective utilization is fundamental for optimizing machining performance.
- Lubrication:
Cutting fluids reduce friction between the cutting tool and the workpiece, which is crucial for tool longevity and precision cutting. This lubrication minimizes wear on the tool and workpiece, extending its lifespan and improving cutting accuracy.
- Heat Dissipation:
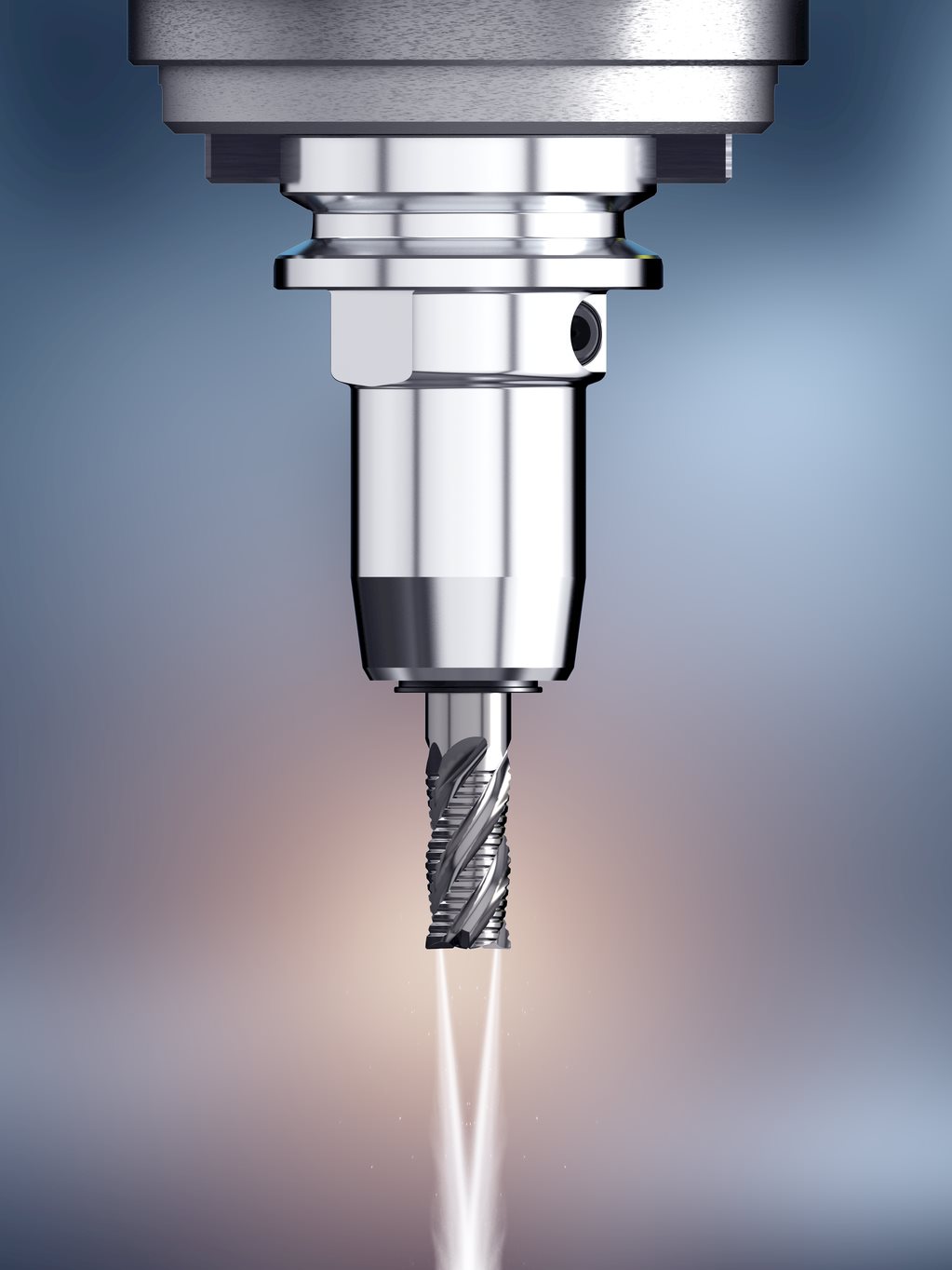
Metal cutting generates substantial heat due to material deformation and removal. Cutting fluids help dissipate this heat, preventing the workpiece and cutting tool from overheating, which can lead to tool wear, reduced tool life, and workpiece deformation.
- Chip Control:
Proper chip control ensures that chips are removed from the cutting area, reducing the risk of chip buildup, tool damage, and workpiece surface defects. Cutting fluids help in this regard by aiding in chip evacuation.
- Surface Finish Improvement:
Cutting fluids contribute to a smoother surface finish on the workpiece. By reducing heat-induced deformations and vibrations, they help achieve better surface quality, which is critical for finishing machining operations.
- Tool Cooling:
Keeping the cutting tool at an optimal temperature is vital for its longevity and performance. Cutting fluids aid in cooling the tool, preventing it from overheating and losing its hardness.
- Rust Prevention:
Some cutting fluids contain rust inhibitors that protect the workpiece and machine tool surfaces from corrosion. This is especially important in environments where moisture is present.
- Improved Machinability:
Cutting fluids can enhance the machinability of certain materials, making it easier to cut hard or challenging materials like stainless steel, titanium, or high-temperature alloys.
- Environmental and Health Benefits:
Cutting fluids can be formulated to be environmentally friendly and safe for operators. They reduce airborne particles, fumes, and dust, improving the working environment.
- Reduced Tool Wear:
By reducing friction, heat, and wear on cutting tools, cutting fluids extend the tool's life and reduce the frequency of tool changes, improving overall machining efficiency and cost-effectiveness.
Cutting fluids are delivered to the cutting zone in various ways, depending on the machining operation and the machine tool in use:
- Flood Cooling:
In flood cooling, a continuous flow of cutting fluid is directed onto the cutting tool and workpiece from various nozzles or channels. This method is commonly used in operations like milling, drilling, and grinding, where a substantial amount of coolant is needed to maintain tool and workpiece temperature and to flush away chips.
- Mist Systems:
Mist systems atomize the cutting fluid into tiny droplets, creating a fine mist that is directed toward the cutting zone. These systems are commonly used in machining operations where controlled and minimal coolant is required, such as in high-speed machining.
- Through-Tool Coolant:
Some machine tools have through-tool coolant delivery systems. This system delivers cutting fluid directly through the tool, typically through the tool's internal channels, directly to the cutting zone. It is effective for deep-hole drilling and other precision applications.
- External Coolant Nozzles:
External coolant nozzles are positioned close to the cutting tool and workpiece to deliver coolant with precision. These nozzles can be adjusted to direct the cutting fluid to specific areas on the tool or workpiece.
- Minimum Quantity Lubrication (MQL):
MQL is a technique that delivers a minimal amount of cutting fluid directly to the cutting zone in the form of a fine mist or droplets. It is used in eco-friendly machining for minimal fluid application.
- High Pressure Directed Coolant (HPDC):
High Pressure Directed Coolant systems use specialized nozzles and high-pressure pumps to deliver cutting fluid at very high pressure directly to the cutting zone. This method is particularly effective for heavy-duty machining operations and materials that require superior cooling and chip evacuation.
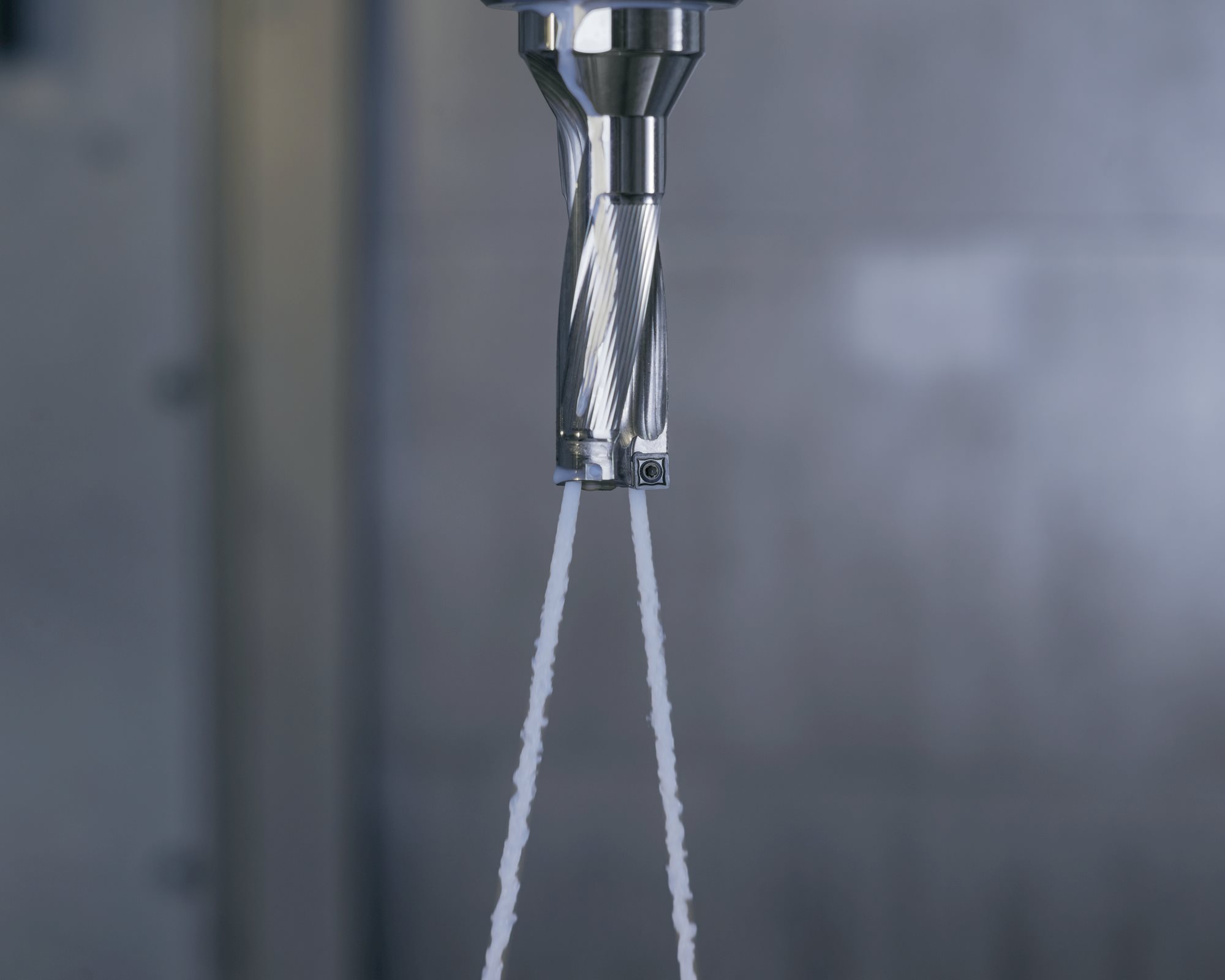
Cutting fluids come in various types, each with its own set of advantages and disadvantages.
The choice of cutting fluid depends on the machining operation, workpiece material, and tooling:
- Straight Oils (Neat Oils):
Straight oils are primarily composed of petroleum-based oils or natural oils like vegetable oils.
They provide excellent lubrication and are suitable for heavy-duty machining and materials that generate high heat.
- Emulsions:
Emulsions are a mixture of oil and water with additives.
They are versatile, offering good cooling and lubrication properties, and can be customized for different applications.
- Synthetic Cutting Fluids:
Synthetic fluids are formulated entirely from synthetic chemicals, offering excellent cooling and lubricating properties.
They are less likely to cause staining on workpiece surfaces and are suitable for a wide range of materials.
- Other Specialty Cutting Fluids:
Specialty cutting fluids are designed for specific applications and materials, including high-performance cutting fluids, water-based options, MQL fluids, and cutting fluids with additives.
Proper control of coolant pressure and flow is crucial to ensure effective cooling and lubrication in metal cutting operations:
Pressure:
- Adequate pressure is necessary to ensure that the cutting fluid reaches the cutting tool and workpiece effectively.
- The ideal pressure level varies based on the machining operation, tool, and workpiece material.
Flow Rate:
- Proper flow rate is essential for carrying away heat and chips generated during the cutting process.
- The flow rate depends on machine tool specifications, the cutting operation, and the type of cutting fluid being used.
Direction:
- The direction of coolant flow is critical to ensure that the cutting fluid is directed to where the cutting process is taking place. Effective direction ensures that the cooling and lubrication benefits are delivered precisely where they are needed, enhancing tool life and workpiece quality.
The specific pressure and flow rate required for a given machining operation depend on factors like the machining operation, tool and insert geometry, workpiece material, tool material, machine tool capabilities, and more.
Cutting fluids are indispensable in metal cutting operations, offering benefits ranging from improved tool life to enhanced workpiece quality. The choice of cutting fluid and control of pressure and flow rate are vital to optimize machining performance and ensure the longevity of tools and equipment. Proper selection and maintenance of cutting fluids contribute to efficient and cost-effective metal cutting processes.
Inline Content - Survey
Current code - 5fce8e61489f3034e74adc64