Aircraft Aluminum A-Frame in one shot
Process an Aircraft Aluminum A Frame in one operation with 5-axis cutter compensation, dynamic pocket milling and 5-axis wall finishing.
Watch us machine A-frame components in a single operation using advanced five-axis cutter compensation.
To watch the demo, fill in this form now and instantly get 5 additional machining demos
Inline Content - Sugar Form
Sugar Form url - https://info.secotools.com/acton/fs/blocks/showLandingPage/a/45194/p/p-00dc/t/page/fm/0
Frame height - 650 px
Aluminum A frames provide stability for wing components in commercial aircraft. Machined from 7074 or 6082 aluminum, these structural parts include complex radial wall features and require tight tolerances. The typical production approach uses two operations – one for each side – with the workpiece mounted on tombstone fixtures.
Our customers have expressed a desire to produce the component in one operation.
Reduction of this process to one operation on a 5-axis machine tool would increase throughput and optimize production of this high-volume, high-value part. However, the demanding features of this part and the high amounts of material removal required to produce it make it difficult to fixture and machine on multi-axis equipment. Additionally, a one-operation approach would reduce tooling use if the process can compensate for the size of reground tools.
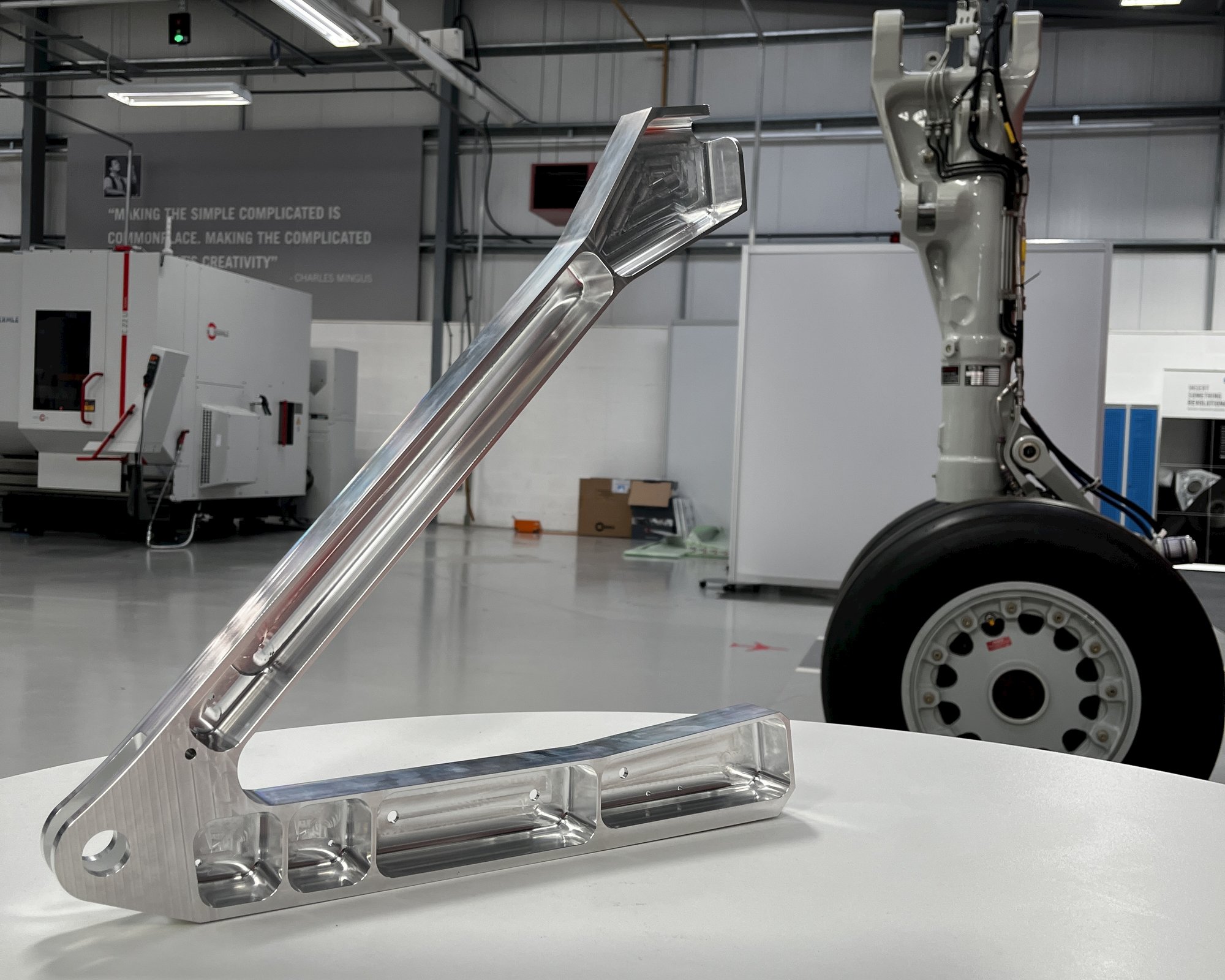
In collaboration with trusted partners, Seco developed and demonstrated a one-operation approach that machines this part on a multi-axis machine tool with a single fixture and 5-axis compensation. The process adds sustainability, with the ability to regrind and reuse tools up to four times. Reduced cycle times and energy use also promote sustainable production. Automation and advanced programming make dynamic pocket milling and 5-axis wall finishing easy to accomplish with fewer tools. Simulation through digital twins provides proof of concept prior to the cut.
The ability to control cutting diameter for circumferential finishing enables this process to achieve repeatably accurate geometric tolerances. This is essential to meet part specifications and set up automated production for potential lights-out manufacturing.
- Collaborate with partners to demonstrate one-operation production before prove-out for aerospace manufacturing.
- Use virtual design and operation simulation to verify demonstration part before the cut.
- Produce high value, high-complexity aerospace component in one operation with 5-axis machining.
- Collaborate with partner to develop a fixture that provides access to both sides of the part for 5-axis machining.
- Design part with snap-off tabs so it removes easily.
- Reduce cycle times with single-operation machining to increase sustainability.
- Increase material removal rates to boost part output.
- Meet demanding specifications with reground tooling.
- Enhance production efficiency for high-volume durable aluminum aerospace component.
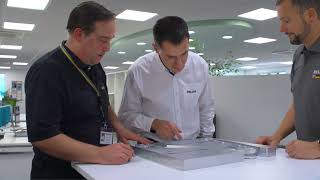
- Maintain tolerances on radial geometry of 5-axis wall features.
- Increase production efficiency and accuracy.
- Minimize human intervention in production.
- Produce precise aircraft part with reground tooling.
- Compensate automatically for size of reground tools through on-machine probing and CNC software.
- In partnership with Siemens, 5-axis cutter compensation adds circumferential finishing with repeatably accurate tolerances, even with reground tools.
- Siemens control system command "CUT3DCD" activates 5-axis cutter compensation in programming for accurate part geometries.
- Tool reuse through up to three regrind cycles cuts costs and boosts sustainability.
- Accurate measuring tools from partner Zoller keep tool usage consistent for automated processes.
- Multi-tasking production in one operation reduces the manual intervention and error likely with multiple setups.
- Leading Seco regrind capabilities ensure proper dimensionality of finishing tools for demanding application.
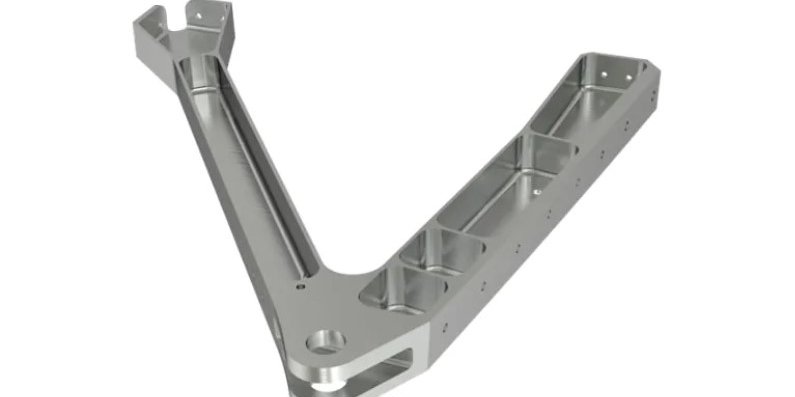
- Heller
- Siemens
- Renishaw
- Zoller
HOMERelated content
ITI 2024 | Aerospace A-Frame component machining demo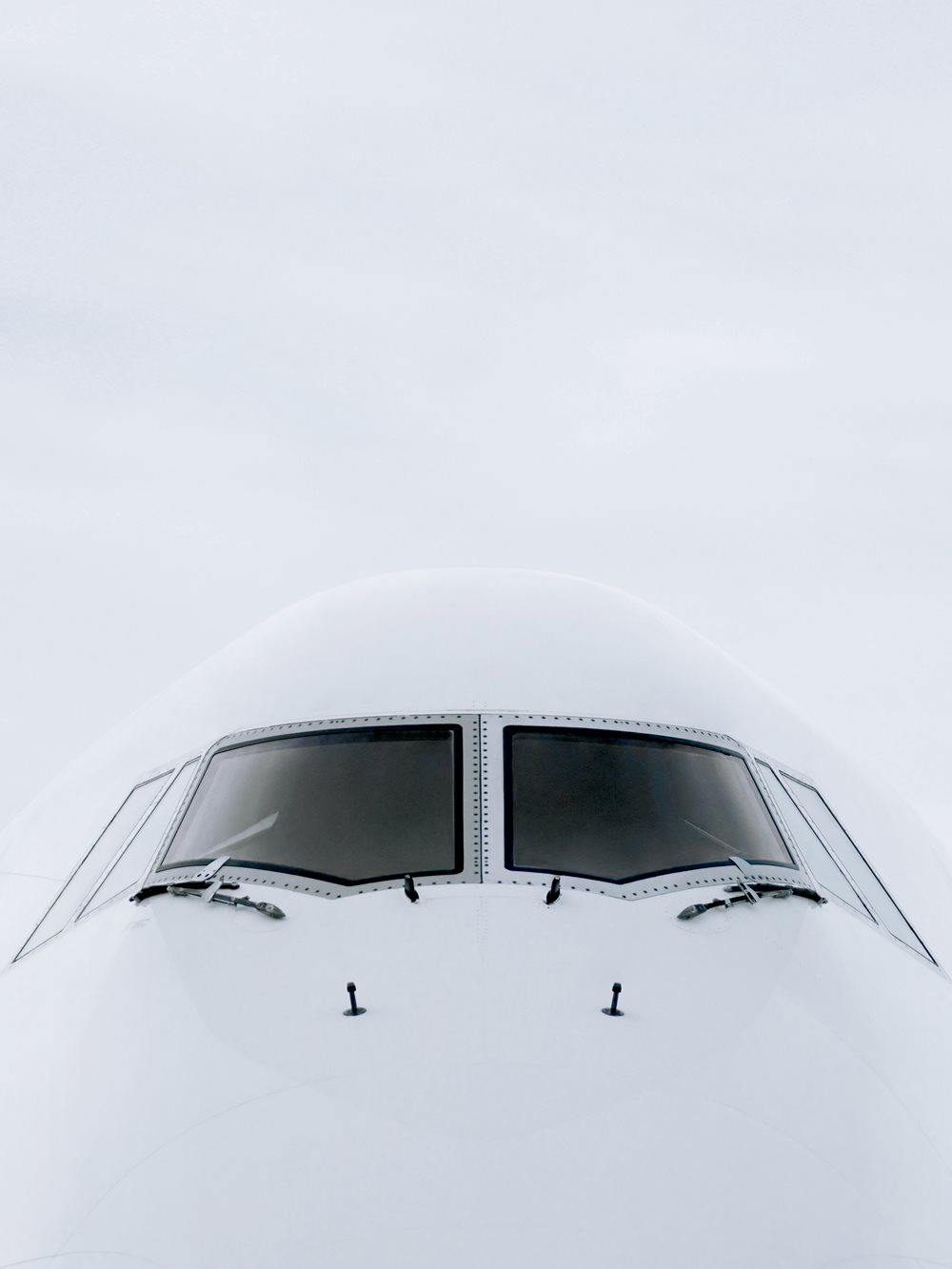
Aluminium A-Frame Demonstration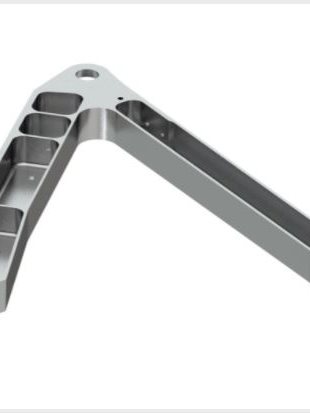
Inspiration Through Innovation 2024 Aerospace and Medical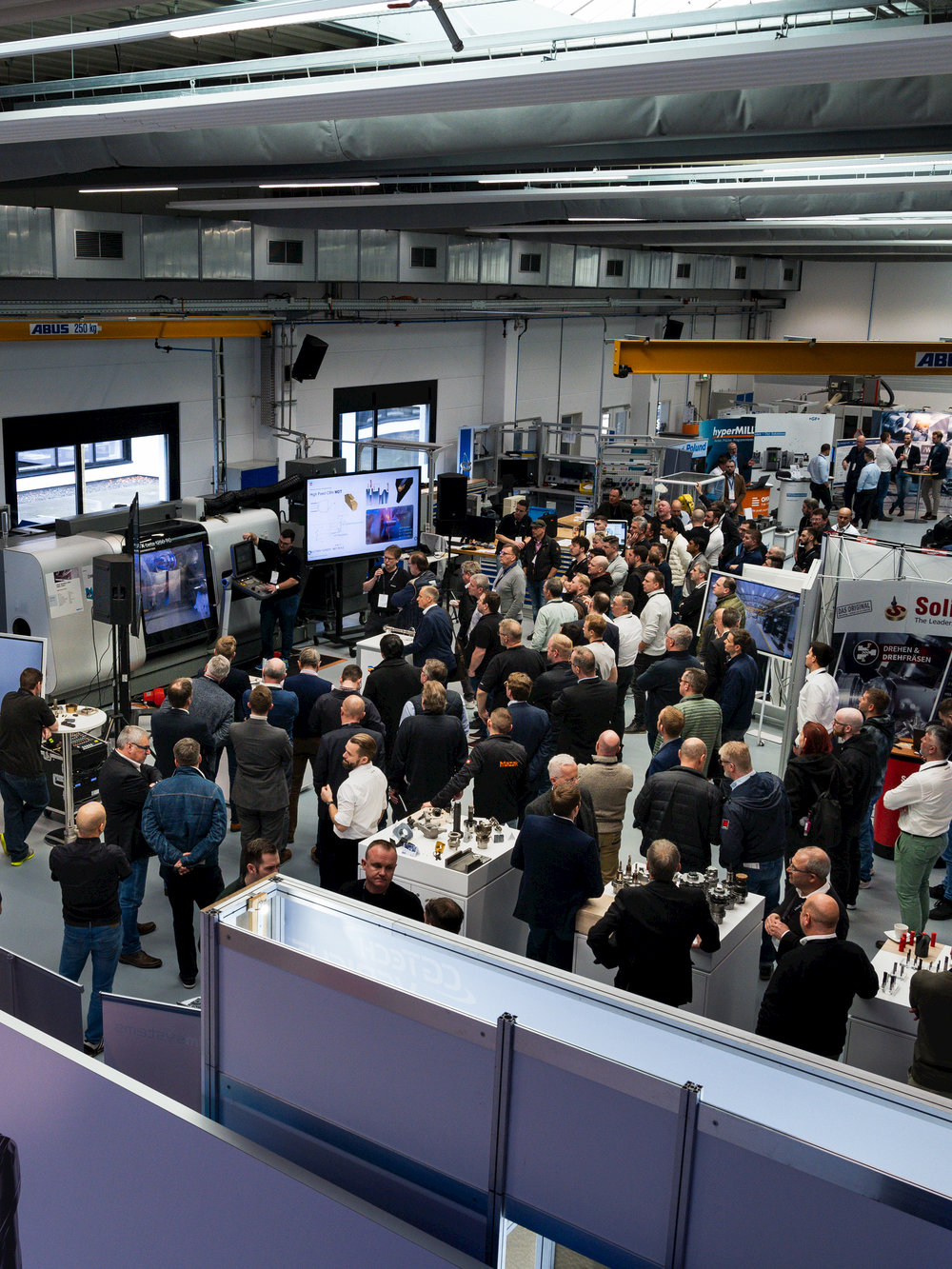
Inspiration Through Innovation 2024: Championing collaboration in the pursuit of manufacturing excellence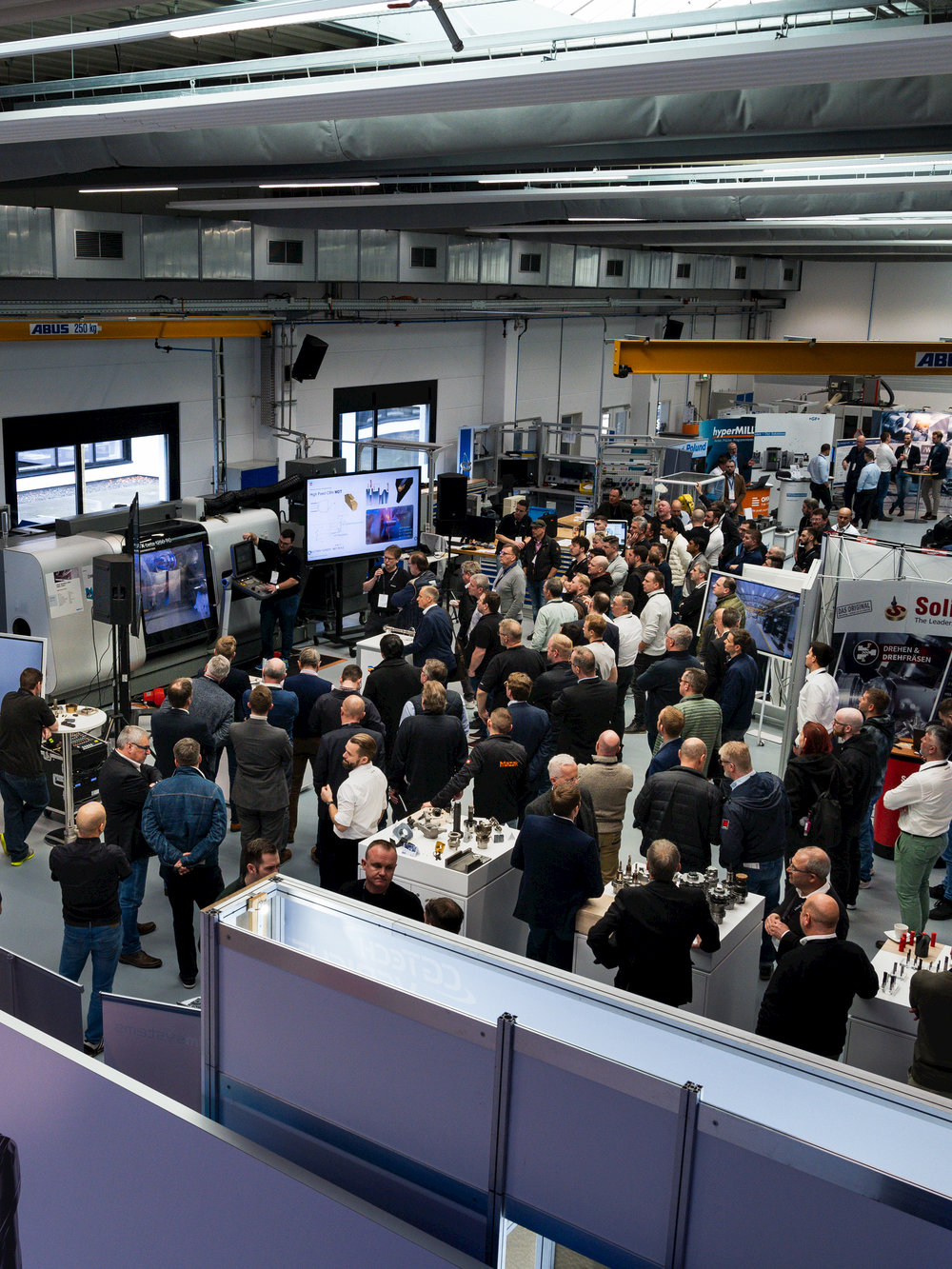
Medical Shoulder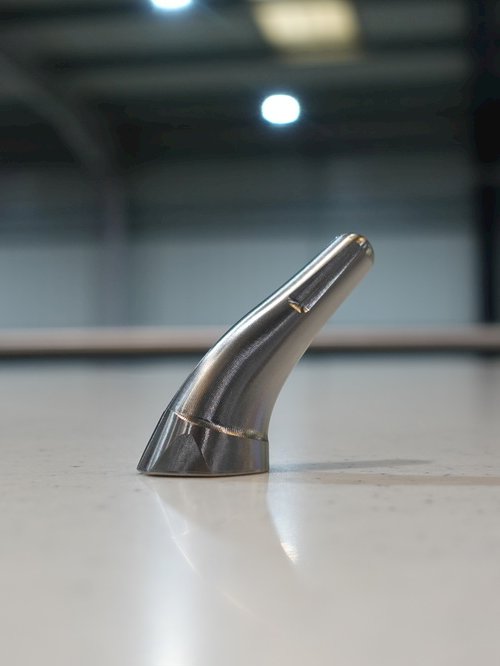
Titanium Hip Cup - Medical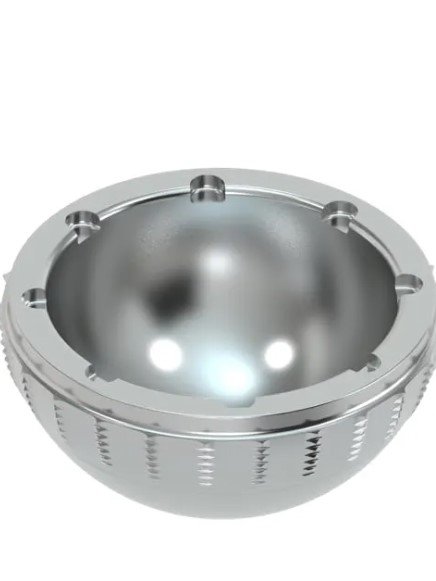
Machining a Titanium Disc - Aerospace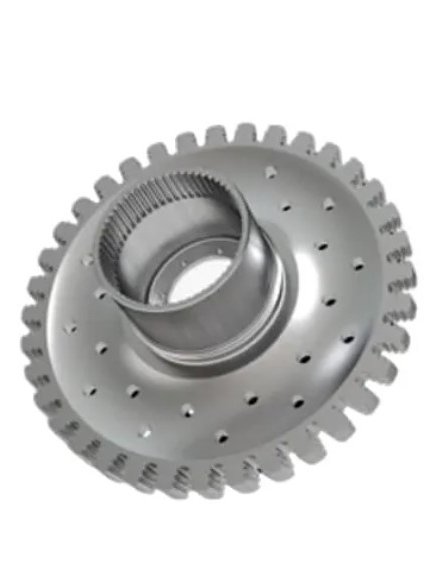
Manufacturing Processes - Digital Demonstration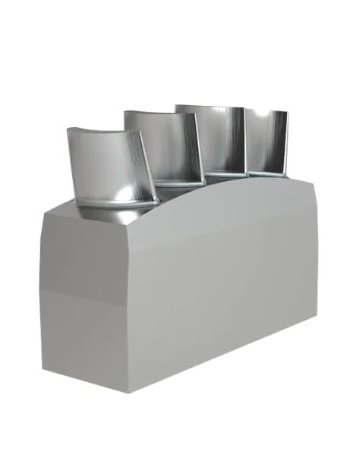
Manufacturing Processes - Any Shape in a Day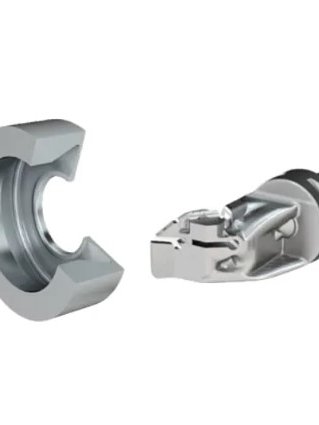
Manufacturing Processes - Automated best fit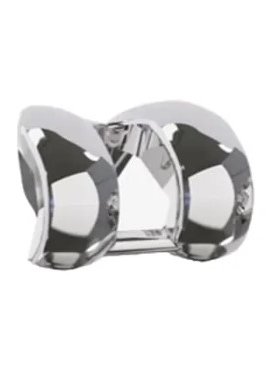
Inspiration Through Innovation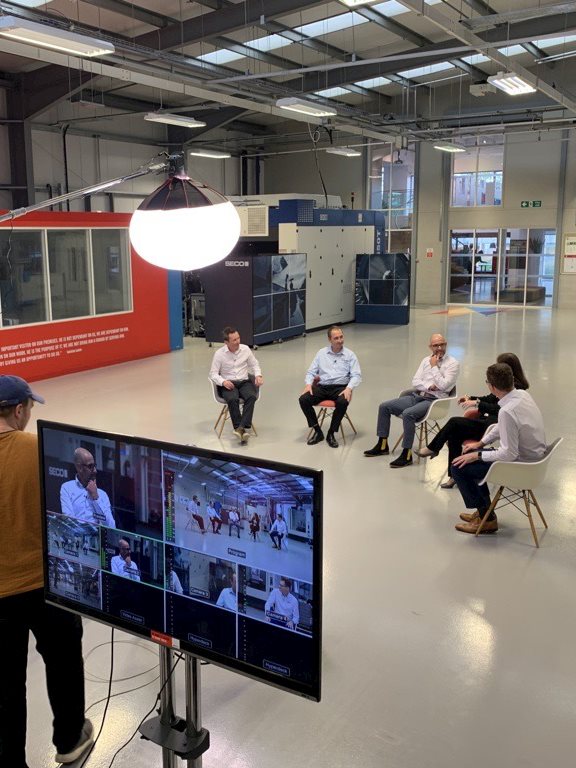
The new materials set to shape the future of the aerospace industry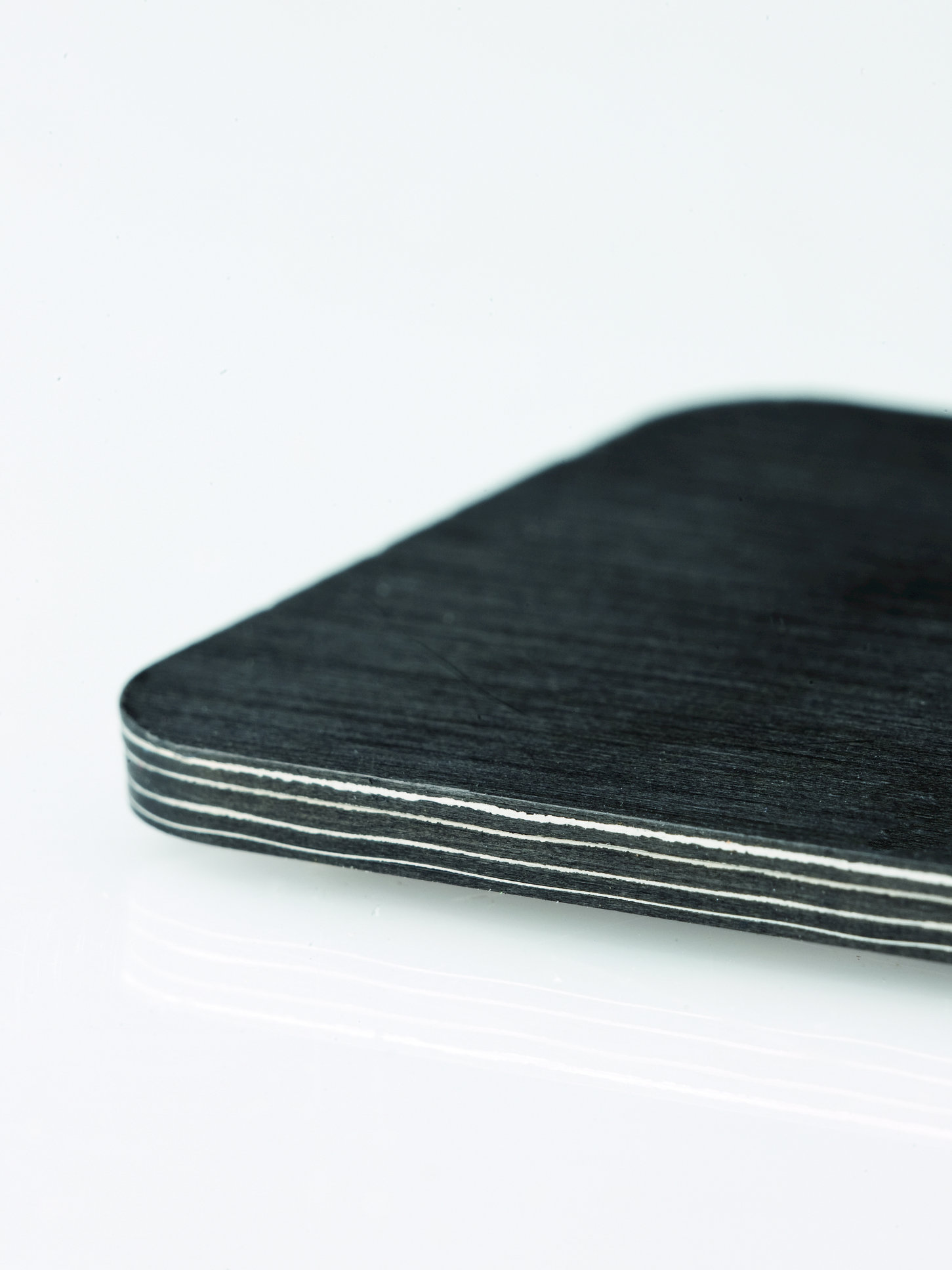
The rise of MMCs: Advantages, challenges, and solutions in using Metal Matrix Composites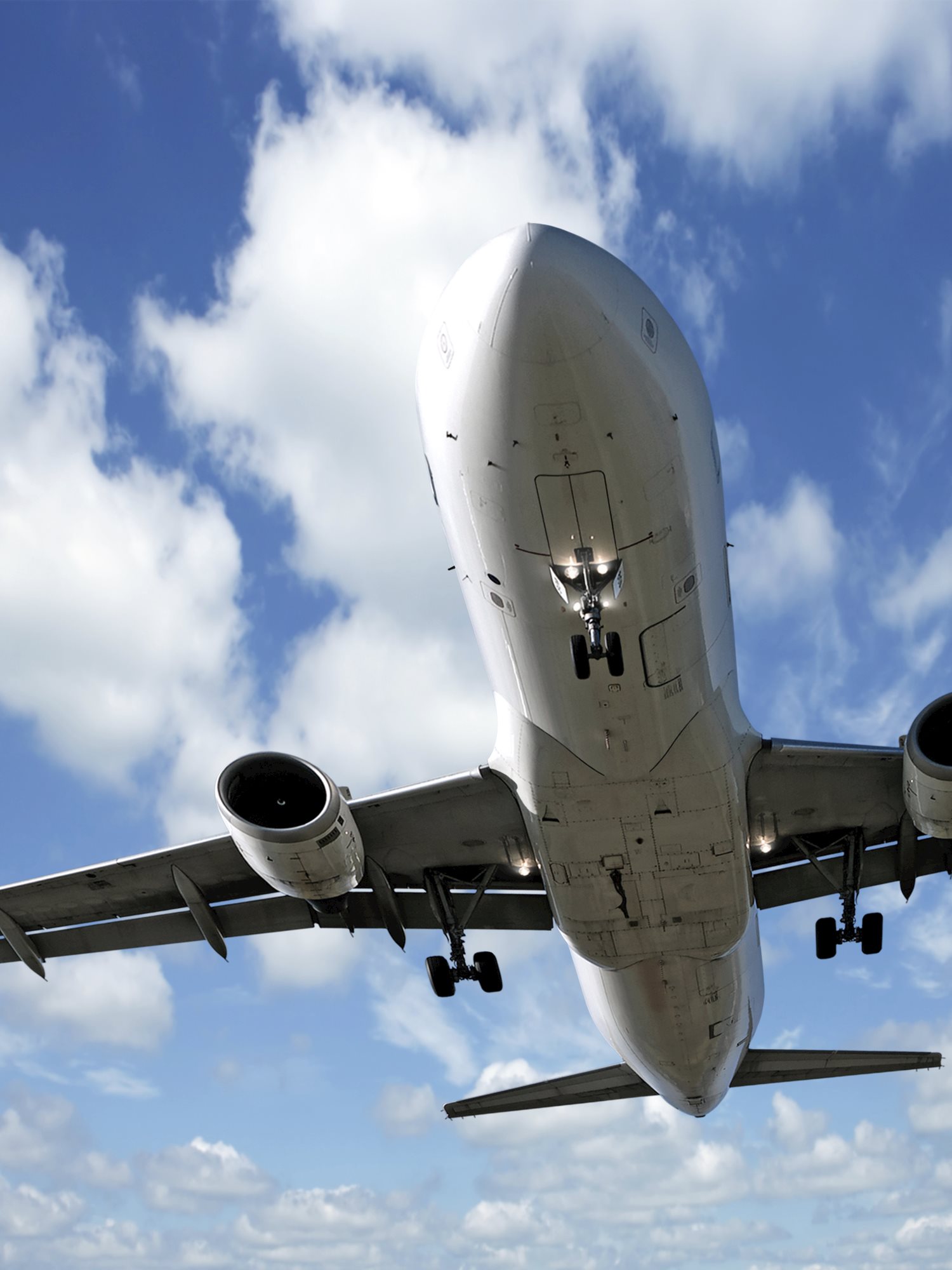
Non-Ferrous / ISO N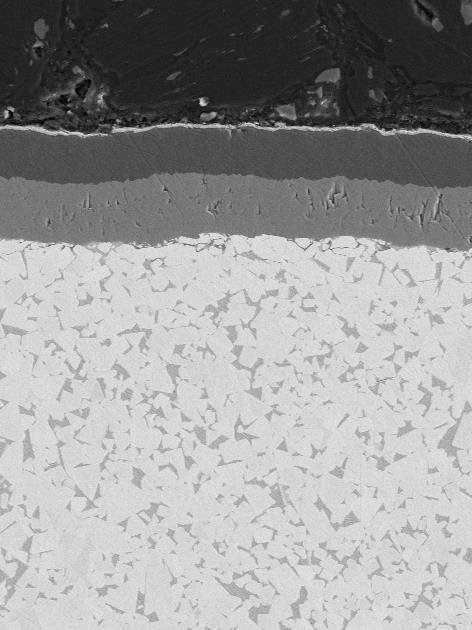
Factsheet - Seco Solid End Mills for Aluminum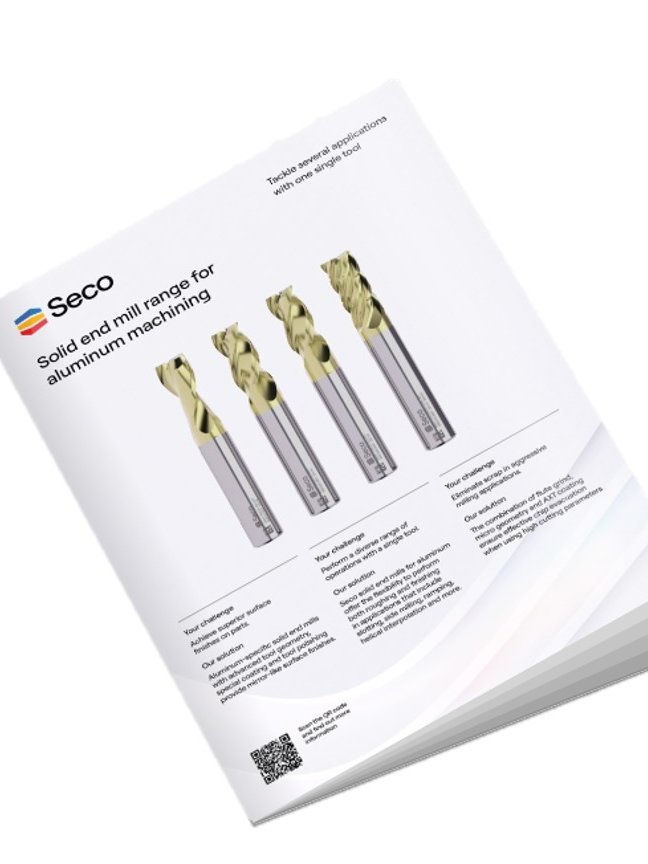
Seco S43/S45/S46 Solid End Mills for Aluminum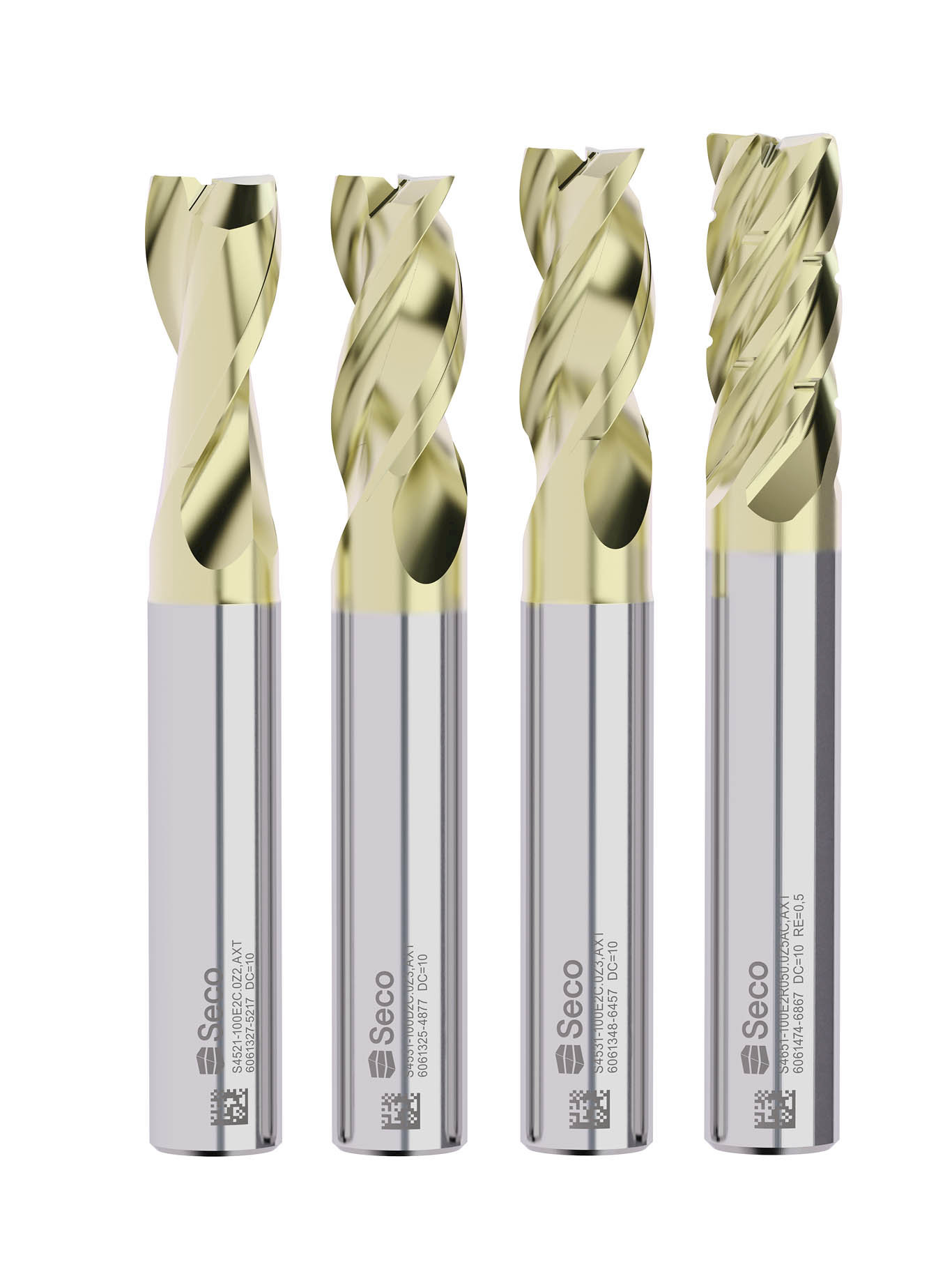
Challenges in non-ferrous materials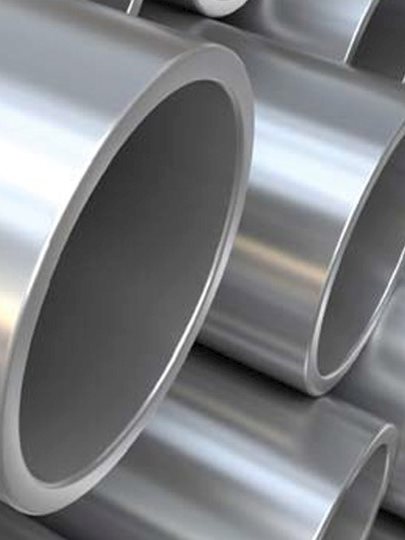
AM Titanium Blisk Demonstration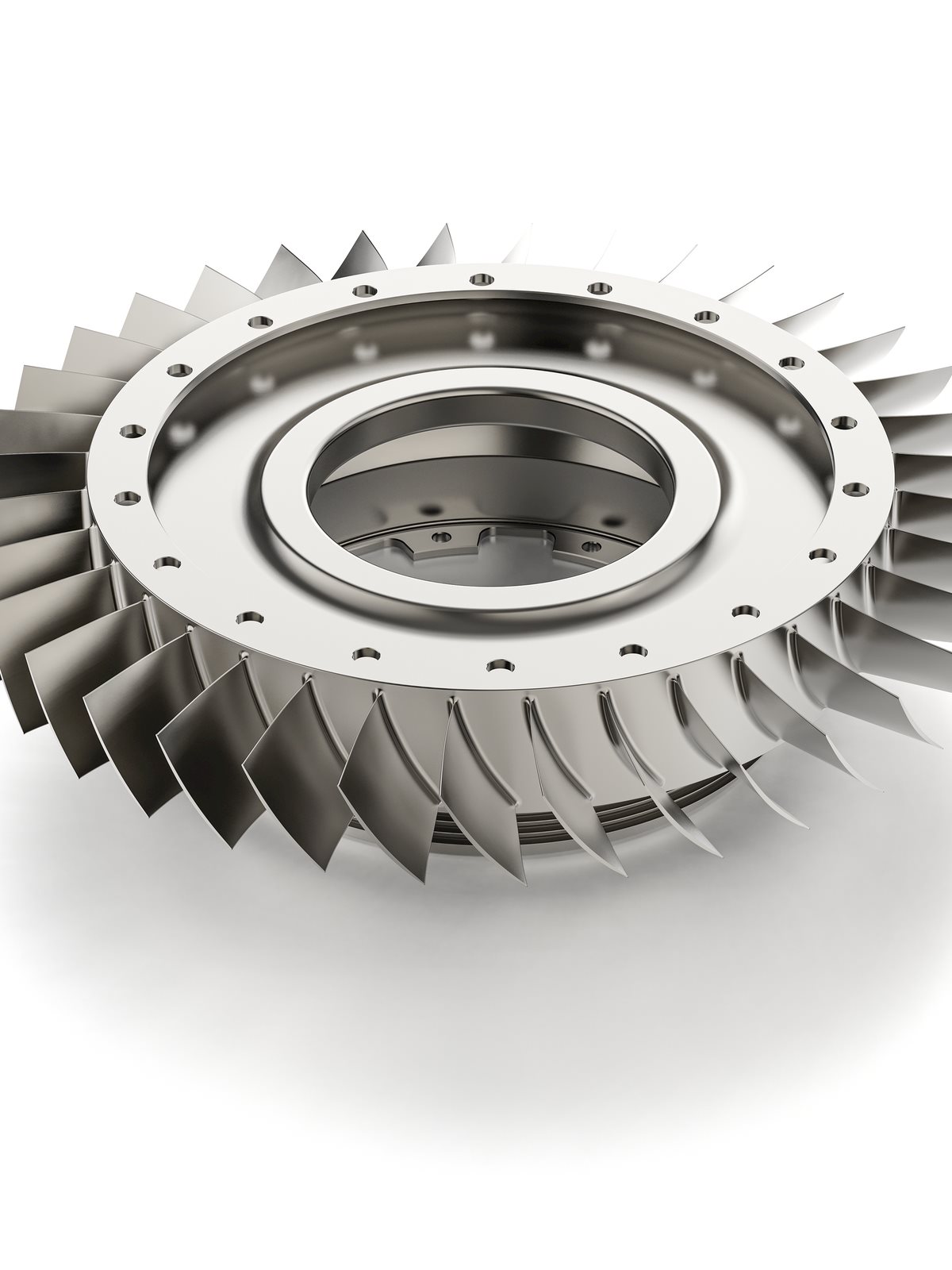
Finishing a Titanium Pylon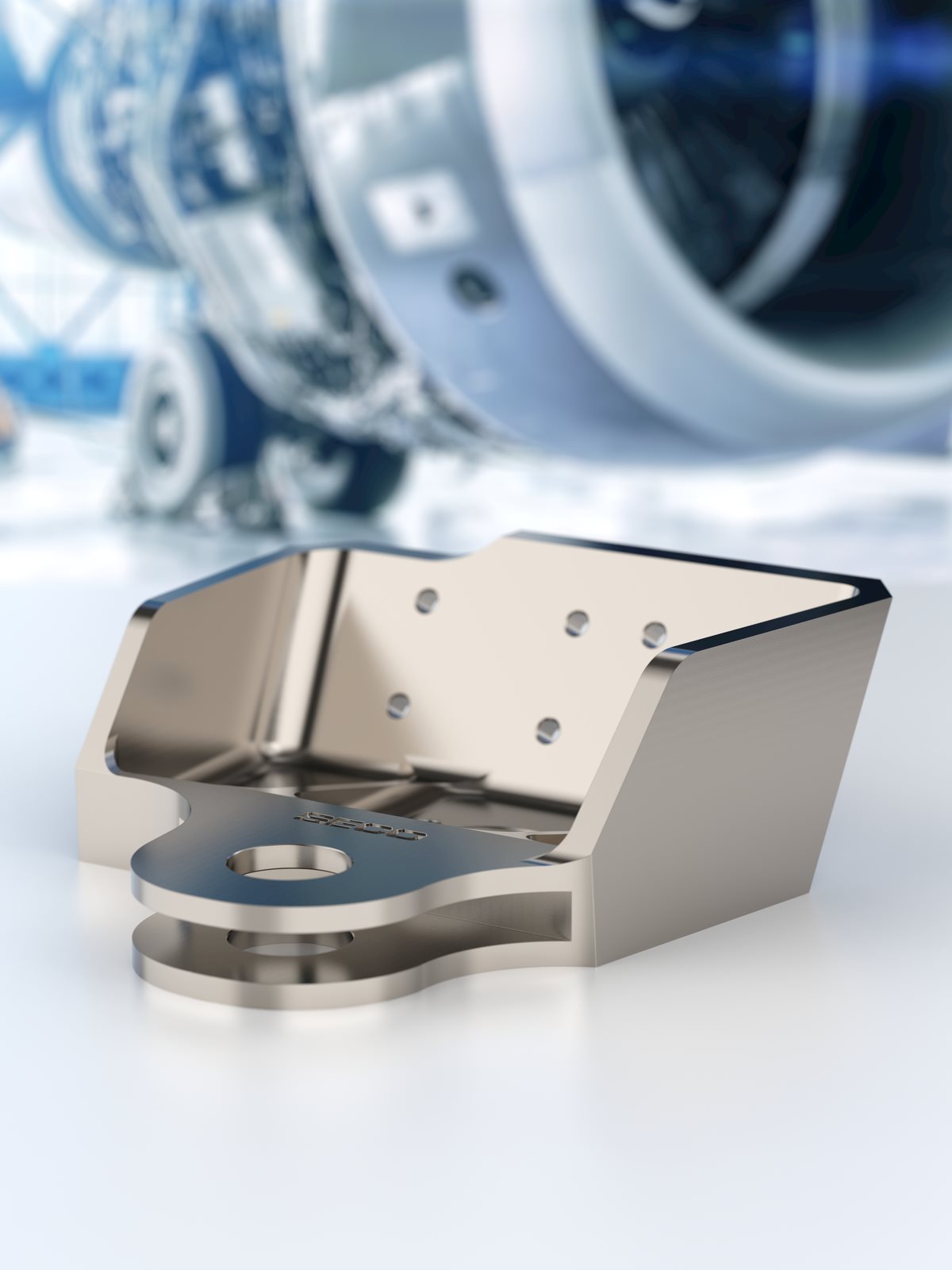
Video: Machining Demo shown at Mazak Technical days | Seco Tools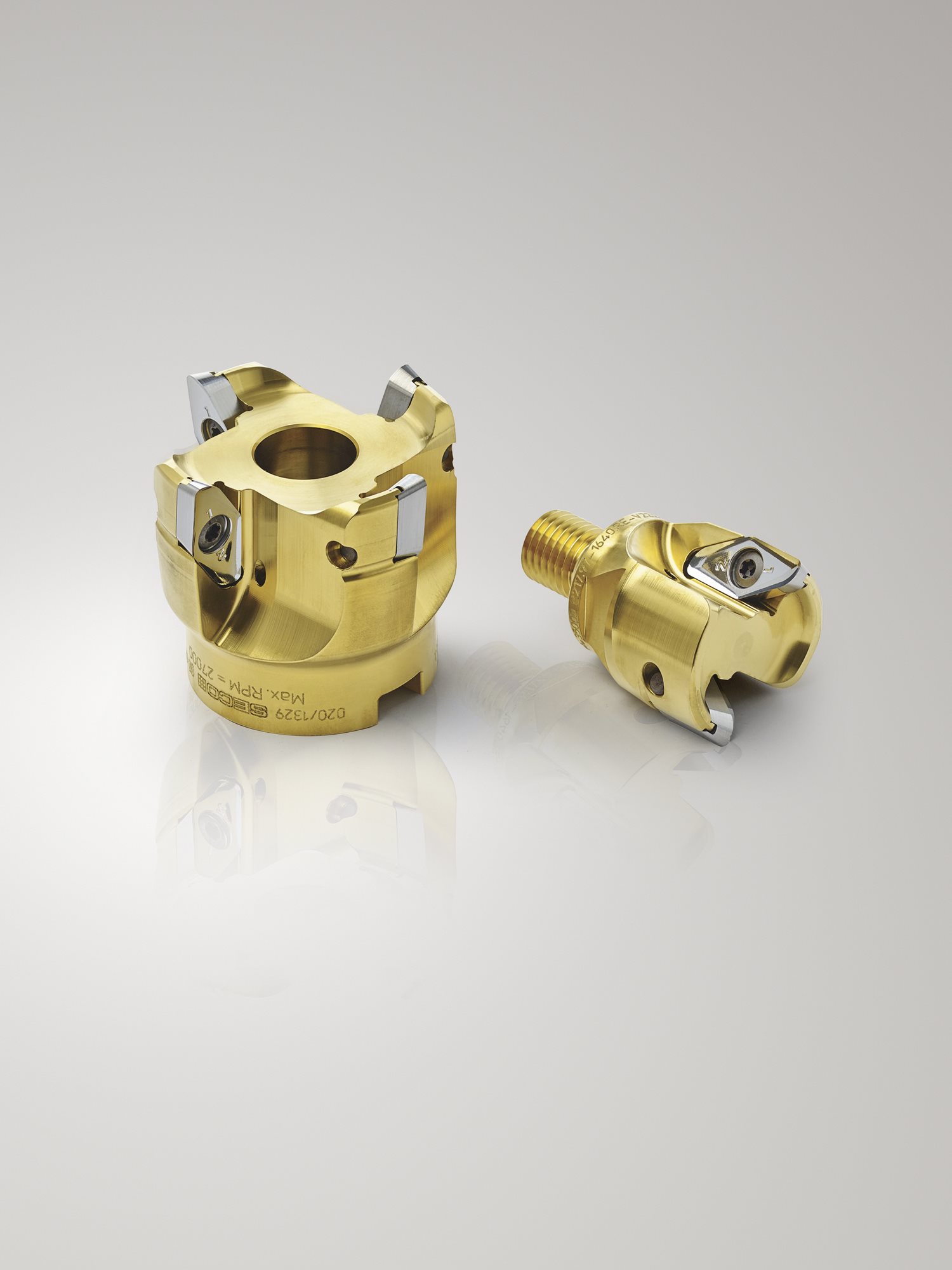