The rise of MMCs: Advantages, challenges, and solutions in using Metal Matrix Composites
With their lightweight yet robust properties, Metal Matrix Composites are beginning to transform industries, especially in aerospace and automotive component applications. Here are some pluses and minuses of using MMCs, and how best to machine them.
If there’s a holy grail for today’s engineering manufacturers in the aerospace and automotive industries, it’s how to create products which are lightweight but durable.
It is such a big preoccupation for these two industries because they are dealing with the twin pressures of sustainability (through regulation and rising customer demands), and cost efficiency.
“You need to design a material and component that is not too heavy, so as to reduce the overall fuel consumption of a plane or car, yet also still have a great amount of strength, wear resistance and durability,” explains Rachid M’Saoubi, Senior Expert, Machining Research at Seco Tools.
MMCs are a class of materials that achieve the difficult balancing act between weight reduction and mechanical resilience. They are essentially an amalgamation of softer materials with harder, reinforced elements. Common examples include the softer aluminum alloys being infused with the more robust silicon carbide or titanium silicon carbide.
Rather like a chef working on a recipe, manufacturers seek to achieve a delicate blend that manages to enhance wear resistance, mechanical and thermal strength, while minimizing weight, a crucial factor in modern automotive and aerospace component design.
“In the aerospace industry, the rise in operating temperatures and operating efficiency in airplane engines means the materials used in them have to withstand even greater stresses,” says M’Saoubi.
Aluminum metal matrix composites such as Al-Silicon carbide and Al-Al2O3 are to be found in the automotive industry, where their excellent wear resistance and thermal stability make them suitable for engines, brake systems and suspension systems.
Titanium Silicon Carbide used in high-temperature applications in engines. These composites feature titanium as the matrix material reinforced with ceramic particles or fibers. They offer excellent strength-to-weight ratio, high temperature resistance, and corrosion resistance, making them suitable for components like turbine blades, combustion liners, and exhaust ducts.
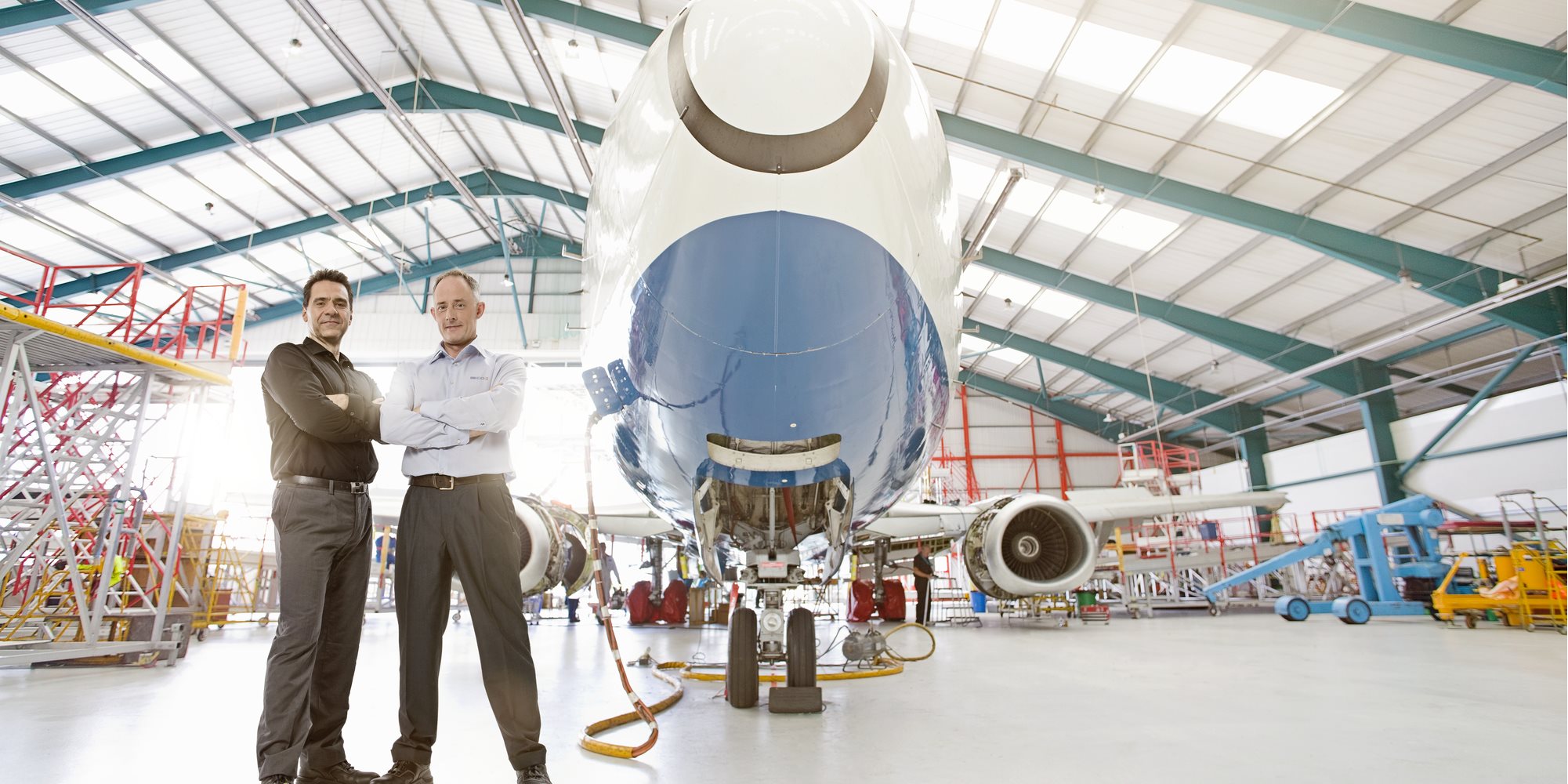
Other MMCs include magnesium-based composites, whose stiffness, corrosion resistance and strength are good for using in body panels, chassis components, and transmission cases; and hybrid and advanced MMCs used in body panels, wheel hubs and powertrain components.
While MMCs may promise a new era of material excellence, the actual machining of them throws up specific obstacles. In some way their strengths also contain their weaknesses.
“Because they are lightweight in nature, they tend to be prone to deformation during the machining,” explains M’Saoubi.
Distortion issues, particularly prevalent in thin-walled structures, require meticulous attention during both machining and heat treatment phases.
“You really need precise fixturing and specialized tooling to enable them to be machined successfully without them deflecting or bending,” he adds.
Additionally, the near-net shape of most MMCs demands the machinist to be very precise. The less material there is, the less margin for error there is in shaping it compared with a raw material block. “What usually happens is that the near-net shape material is lightweight, so there is a low level of elasticity and the part can bend easily,” says M’Saoubi.
“The less material you need to remove, the more attention you need to pay to the geometry of your tooling, so the micro geometry of your tooling is important.”
Selecting the right cutting inserts is especially crucial when machining MMCs. The general preference is for materials that have high abrasive wear resistance, such as fine-grain cemented carbide or polycrystalline diamond tooling, as they maintain a sharp edge to reduce built-up edge.
However, the emergence of novel MMC compositions, such as titanium alloys with long-fiber reinforcements, means the machinist needs to take a more nuanced approach.
“Long fiber materials can exert certain properties in certain directions, such as anisotropy, where there are different behaviors in different directions because the fibers only align in certain directions,” says Rachid M’Saoubi.
“In composite materials that’s quite often the case. For example, carbon-fiber reinforced plastic has fibers that are oriented in certain ways. That means you have to modify the orientation so that they give you an overall good mechanical property in multiple directions.”
M’Saoubi says short particles are less of a problem in MMCs (with a volume fraction of five up to 40%). But understanding their size and distribution in the material becomes paramount for achieving the best possible machining outcomes.
As pioneers in cutting tool technology, Seco Tools are continuously innovating cutting strategies and embracing flexible machining approaches, as well as working cross-industry and academia with partners who have issues such as MMCs in sharp focus.
Discover the THERMACH case story
“We have to look into not just the challenge raised by these new and emerging materials, but also the opportunities that arise with the development of machine tools,” says M’Saoubi.
“Machine tools are being developed to make better use of tooling solutions, and there the cutting strategies are very important to consider when we machine those materials due to the issues with lightweight and near-net-shaped materials.
It’s an area that is evolving all the time, with new machining challenges coming up, but Rachid M’Saoubi feels that these lighter, more resilient MMCs have great potential.
“They offer increased performance, efficiency and sustainability,” he says.
Inline Content - Survey
Current code - 5fce8e61489f3034e74adc64