Laser-assisted thermal machining: the solution for manufacturing with MMCs?
Could laser-assisted machining be the solution to the difficulties of manufacturing parts made from metal matrix composites? An exciting UK-based project involving Seco has been finding out.
In recent years, metal matrix composites (MMCs) such as titanium and aluminum silicon carbide have emerged as materials that provide the ideal blend of lightness and strength which traditional metals are missing. The aerospace and automotive industries are starting to explore these composites for making components that reduce fuel consumption, boost sustainability and control costs.
But MMCs are very difficult to machine. They’re abrasive because they often contain hard reinforcement materials such as ceramic particles or fibers. They contain hard material surrounded by the softer matrix, so that makes them difficult to machine evenly, meaning poor surface quality. That’s no good for such valuable, high-performance materials. And they’re prone to intense heating in localized areas, leading to thermal distortion and tool degradation.
With a high rate of tool wear and poor machining results, conventional tooling methodologies just don’t cut it. Polycrystalline diamond cutting inserts can handle MMCs, but they wear out after less than a handful of passes. That’s expensive and wasteful.
The answer could lie with laser-assisted machining. That is the hope of an exciting UK-based research program involving Seco, the University of Nottingham, advanced materials company TISICS, laser specialists Optek and Attenborough Medical, under the auspices of the European THERMACH (thermal machining) project.
THERMACH is a research consortium involving the UK, Sweden, Austria and Canada, which over the past four years has been looking at different aspects of laser and induction-assisted machining techniques. But it’s the laser aspect that is especially promising.
“Using thermal machining, a laser heats the material in front of the cutting tool, which allows that material to plasticize or melt, making it easier for the cutting tool to pass through,” explains Mark Walsh, R&D Technical Lead at Seco, which has been contributing its expertise with tooling and machining strategies to the project.
Nottingham University is the research hub for this project, which is funded by the UK state’s investment arm, INNOVATE UK. Associate Professor Dr Zhirong Liao and Omkar Mypati are key members of the university’s team. Nottingham has been researching MMCs for more than a decade, including on behalf of major players in the aerospace industry, and they have a longstanding cooperation with Seco.
“We have previously used laser-assisted machining for nickel alloy, which was successful for aerospace industry clients,” says Zhirong Liao.
“We’ve developed a strategy to control laser beam and focus it at the same temperature and distribution. This was so successful that we decided to extend it to material that’s more difficult to machine.”
The catalyst for this particular research was TISICS, a UK company that specializes in metal composites. Managing Director Stephen Kyle-Henney, who is also the project manager of the UK research arm of the THERMACH project, takes up the story:
“We’ve been developing titanium composites for a variety of high-performance applications in aerospace, such as landing gear,” he says.
“With our fiber silicon carbide reinforcement in the titanium, we can make it as stiff as steel but much stronger than titanium. And for landing gear applications it’s actually both lighter and much stronger than steel because of the compression qualities of the ceramic fibers.
“It’s great because it’s so strong and stiff, but it’s a challenge to net shape it to the final component. You can’t forge it and bend it once you’ve made it because the fibers are too stiff and will break off if you move them.”
Kyle-Henney adds that the hardness of silicon carbide means that even if you use hard cutting inserts from Seco, the wear rate is very high because although the material is being cut, so is the cutter tip, which is not economically viable. TISICS’ initial answer to this issue was to have the fibers embedded into the material so that it doesn’t need machining, but that has reduced the flexibility of manufacturing and repairs.
“Nottingham University has a tremendous history of advanced machining technology, whether it is working with the aerospace industry on machining techniques or working with Seco to get tooling techniques to match the machining techniques to optimize for speed, efficiency and quality,” he says.
“We might have thrown a curveball with our request, but the team has truly responded. Historically, when we’ve tried to machine it, it looks like something you’d tried to machine with a garden rake, not an engineered surface! Now it looks like it is actually machined.”
The project is soon reaching its final phase, but there is still some work to do before the solution becomes scalable in the years ahead. One aspect now being looked at by Jensen Aw at Attenborough Medical is the mapping of thermal profiles. Aw is analyzing how the laser heats the material, and how the ceramic fibers heat differently to the metal. Ceramic silicon carbide fibers have a melting point of 3,000 C, while titanium melts at 1,600 C.
“You’re trying to heat something uniformly that doesn’t want to be heated uniformly,” says Kyle-Henney. “The modeling to enable that is phenomenal. It’s amazing work.”
There is also the possibility of having a laser that is not in a fixed position but which is instead moved by robotics, which would allow for the machining of more complex shapes. Here, Optek’s expertise with lasers and robotics is playing a vital role.
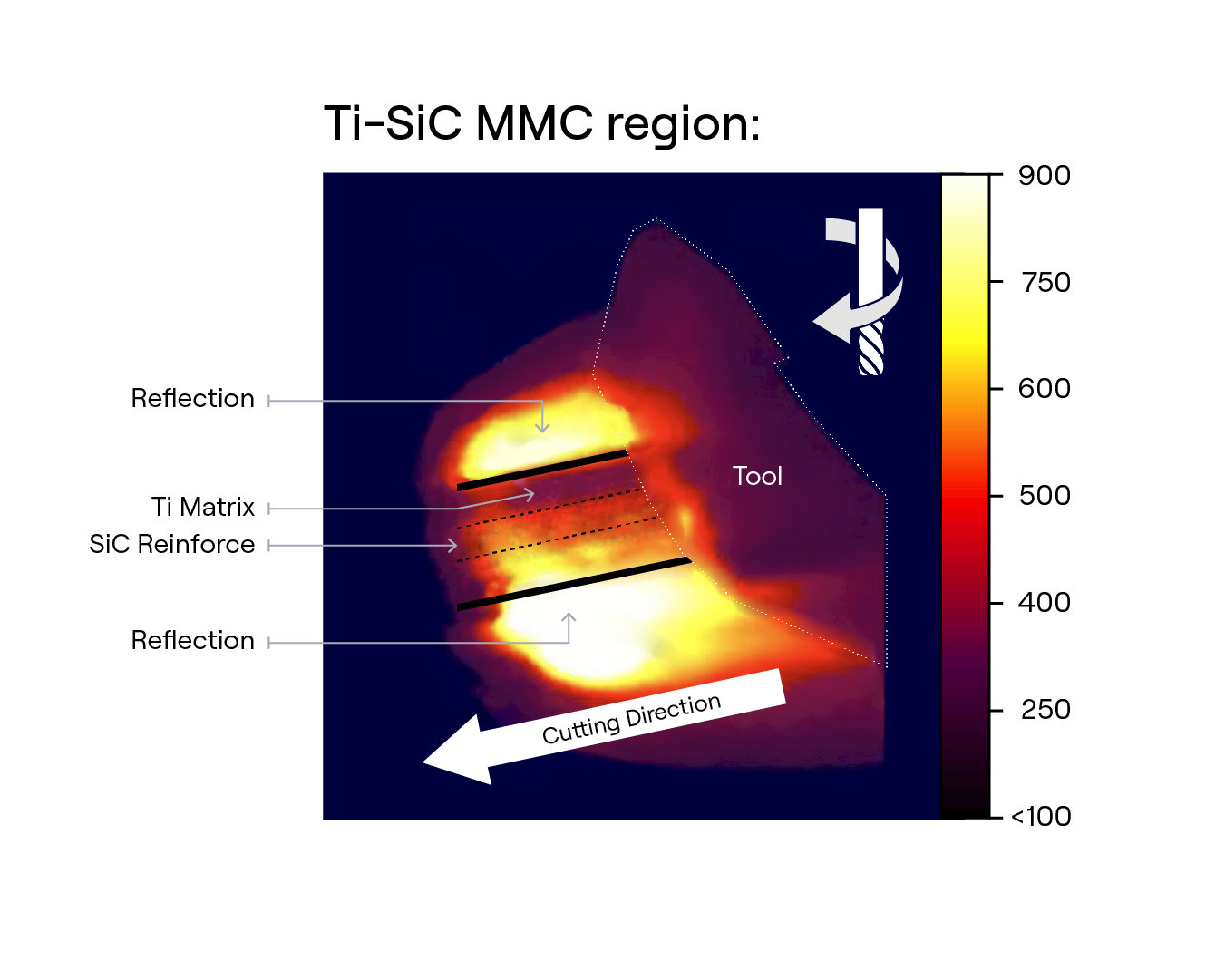
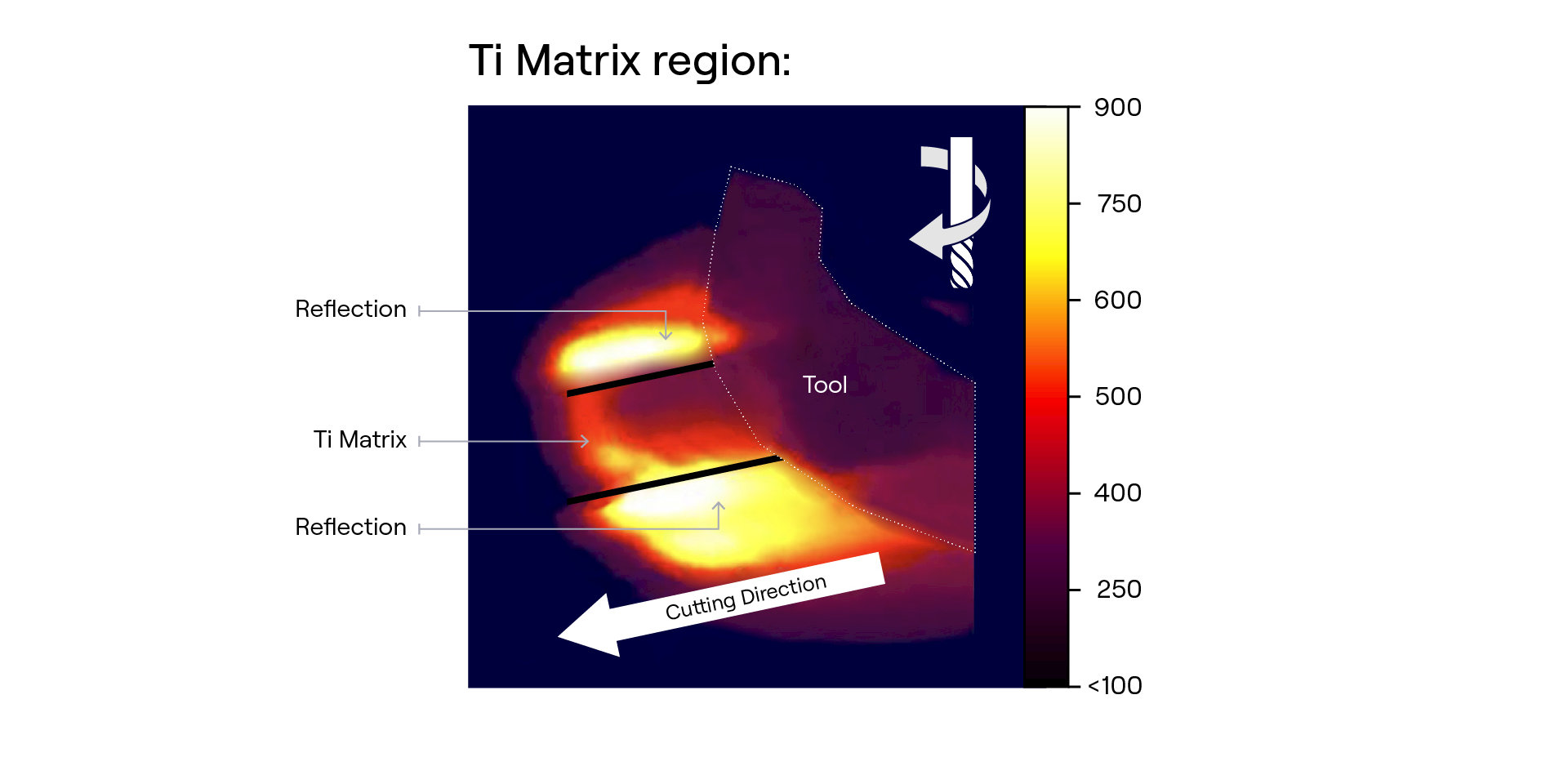
As always, research programs such as this need tangible benefits. And in this case, Kyle-Henney says that the Nottingham-based project certainly fulfills the brief:
“The material we can supply for aircraft landing gear is half the weight of steel. We’ve calculated that this saves 60,000 tons a year of CO2 emissions from just this one part. That equates to potential weight savings of 9 million kilotons across world aircraft fleets for landing gear alone. If you apply it across all the various parts, there are huge sustainability benefits. If we can make engines, aircraft structures and landing gear lighter, there are huge benefits regarding fuel efficiency.”
He adds, “At an operational level on aircraft the small delta in cost over the conventional material can be recovered in 12 to 18 months through fuel savings, and it will then continue to save airlines fuel costs for the next 20 years.”
The machining process itself is also more efficient, with much less waste than conventional machining.
“The landing gear’s strength comes from forgings. These can be 1.5 meters long and up to 300 millimeter-wide pieces of titanium. Yet 90 per cent of it ends up being machined away and turned into swarf. It costs £60 a kilo, so if we are throwing 800 kilos or more that’s all waste.
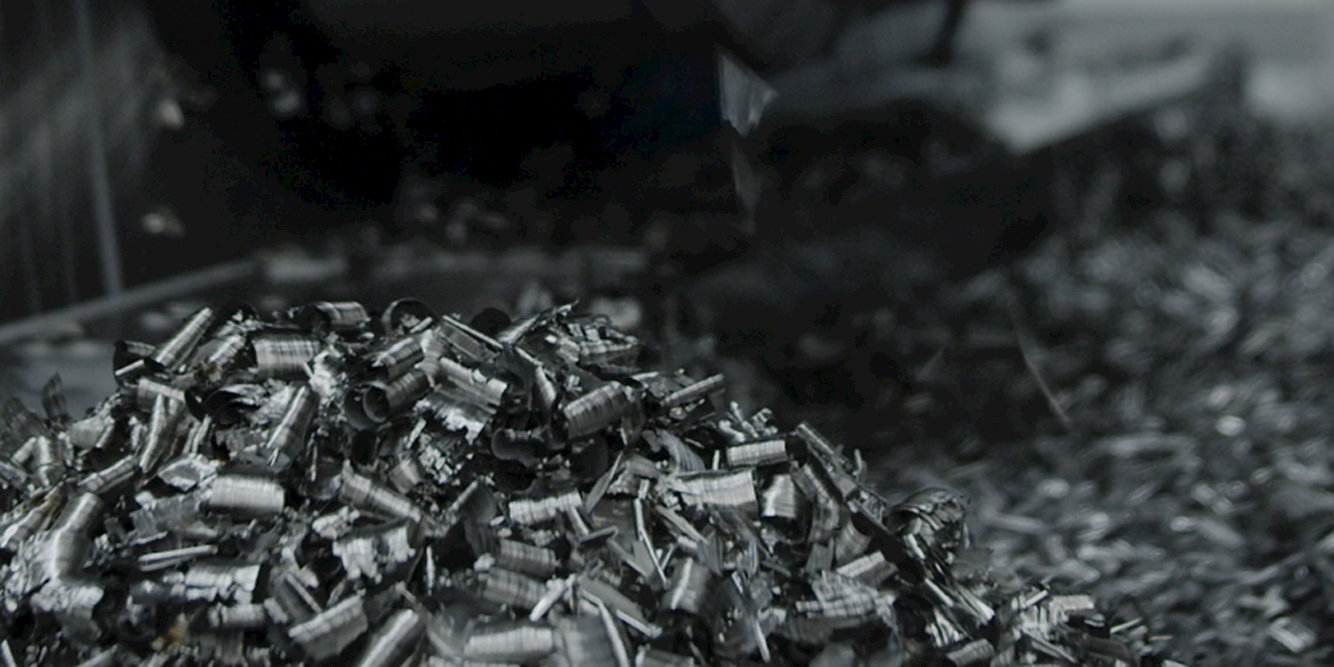
“With our part, it costs more to process and the ceramic fibers add cost, but you’re only throwing away 20 to 50 kilos so you’re offsetting that cost by not having as much loss. It’s just 10 to 20 per cent waste instead.”
Other potential applications for this material are steam turbines for the energy sector and even the medical industry (Attenborough makes ceramic fittings for medical devices).
Mark Walsh says that Seco is delighted to have been involved in this project. “Sustainability is one of our core values, and we want to help contribute to solutions that save energy and cut down on swarf waste, even if it does mean less machining. We want to maximize tool life.”
“And,” adds Stephen Kyle-Henney, “if there is an end-use for these high-performance materials that proves out the use and the economics, and that proves production efficiency of production and manufacturing cost, we can expand it to the market.
“In years to come, as we grow the volume of output, our material will become more standard, and so will the machining. There’s huge potential for this.”
If you want to know more about the products that were used during this project you can find them here:
Inserts
F40M (coated carbide)
CBN200 (PCBN)
PCD20 (PCD)
PCD05 (PCD)
The tests were carried out on a Hermle C32 machine tool platform which has a HSK-A63 spindle.
Inline Content - Survey
Current code - 5fce8e61489f3034e74adc64