Overcome stainless steel supply challenges
Efficient machining of ISO M stainless steels focuses on waste reduction and sustainable production. Plan ahead to make every part successfully.Manufacturers and machine shops define efficiency in many ways, such as a well-defined production workflow with no unplanned downtime or a production floor filled with the right machine tools. Additionally – and most importantly – efficiency is production without scrap or waste. When every workpiece passes quality control on schedule and every customer is satisfied with each job, that's success.
Successful part production with stainless steel requires some special considerations. Stainless steel alloys are critical to production in many industries, including medical, oil and gas, aerospace and even construction. As material prices rise and customers demand lower costs on increasingly complex parts, manufacturers must find ways to increase efficiency and reduce waste in their production processes.
Some of the problems that limit efficiency in stainless steel production come from beyond the shop floor. To reduce environmental impacts and meet sustainability targets, many steel-producing nations have closed smelting facilities. New facilities open in other nations, but the supply chain must stretch to reach the customer from a new location. This can delay material availability and force shops to place orders much earlier than is convenient.
Castings and forgings may be more precise today, with less material to remove in machining, but overall material consistency varies from one supplier to another. Problems with stainless steel supply force shops to look for new suppliers. The same stainless steel purchased from a different source may not behave the same way as products from other sources. To produce bar stock, suppliers may roll or extrude larger diameters down to smaller diameters. These additional production processes yield harder material than expected or desired.
Customers want quicker delivery of better and less-expensive parts. Those demands don't change – but the parts and alloys do. Today's customers order more complex parts than ever before, often from new stainless steels that pose new machining challenges.
But productivity often runs lower in stainless steel because jobs can't use the high speeds and feeds that work with other materials. The alloying elements in stainless steel – chromium, nickel, and molybdenum – accentuate thermal conductivity that keeps heat in the cut, not in the chips. Inserts wear out much faster because of that heat.
As machining productivity drops, shops' material costs climb, in part because of costly elements in stainless steel alloys. Nickel production is expensive, and austenitic stainless steels contain more nickel than other alloys do. Shops turn to duplex stainless steels because they contain less nickel and more molybdenum. However, duplex stainless steels cut differently from other stainless steels in the SMG M material group. Shops must revise their production strategies to use different alloys.
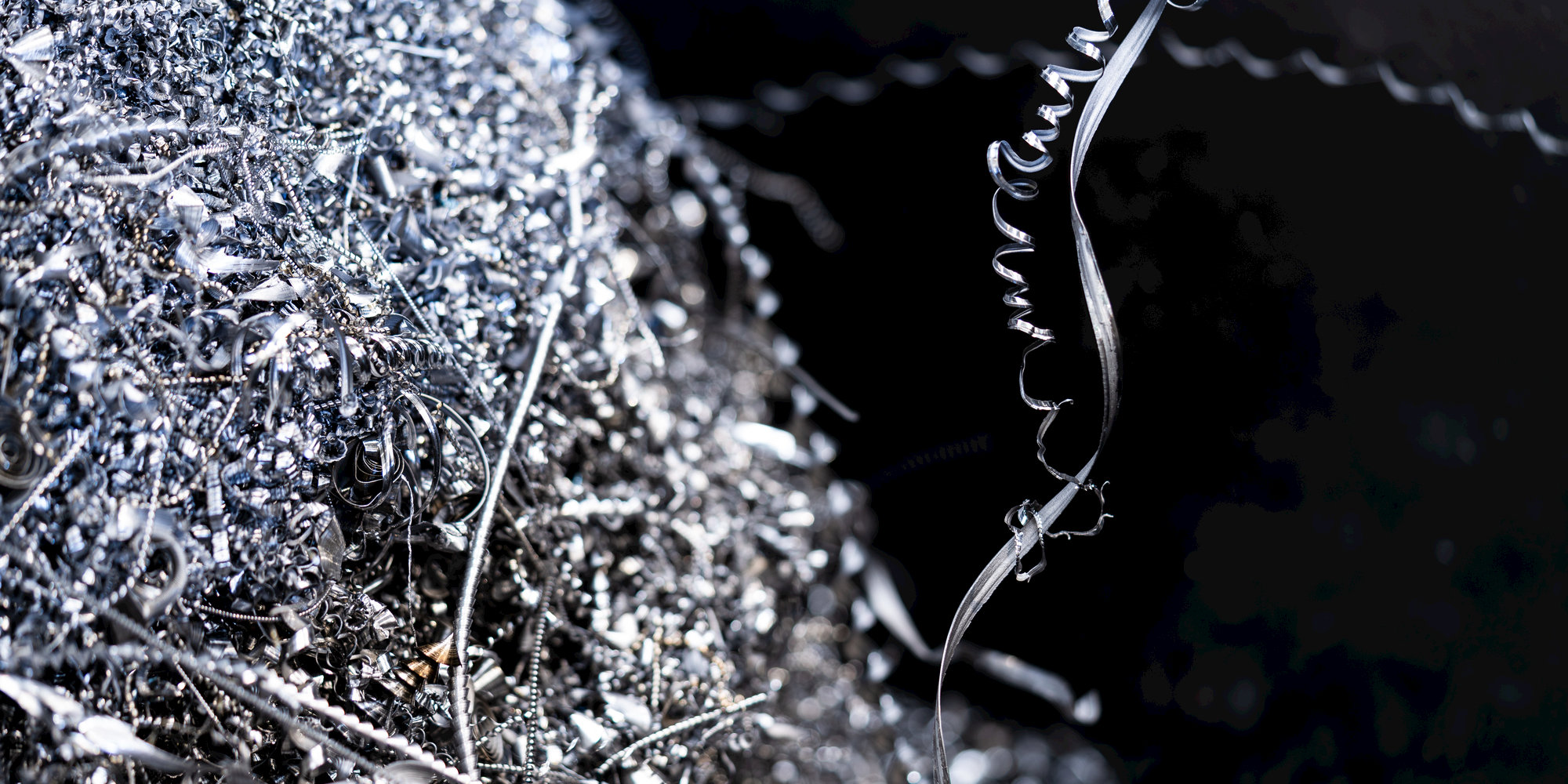
For that matter, duplex stainless steel is very demanding to cut and requires specifically designed inserts. Like many of today's stainless steel alloys, it creates swarf and chip problems, including longer chips and bird's nest configurations, especially in finishing operations. Stainless steel complicates surface finish work because of ductility, especially with austenitic and duplex stainless steels. Alloying elements cause built-up edge, which rubs and damages the finished surface. Strain or work hardening also causes chips to fly back and mar part surfaces.
Swiss-style machining uses small lathes for tiny, slender parts. Machining these parts typically involves small part diameters, weak lathes, high deflection risks, low depths of cut and small feedrates. These jobs require small positive indexable ISO-turning inserts, narrow parting off/grooving tools or specially adapted tools with PVD grades. Most smeary materials need uncoated, polished, positive inserts.
The right tooling helps avoid waste and make machining more efficient. General-purpose grades and tooling cut all materials proficiently. Universal tooling works well for most short-run and one-off jobs. Some shops want to optimize their machining or specialize in machining stainless steel. For them, dedicated grades and tooling specifically designed to machine stainless steel will provide a competitive advantage in tool life and performance.
Today's job shops may need to stock more tool inventory to apply the right tools to varied workpiece materials. Shops that work on aerospace parts such as landing gear, jet engines and engine shafts definitely need more adapted tools for high productivity and quality.
Shops adjust their concept of productivity to meet new realities. To prohibit scrapped parts, they take a more-measured approach to production, with greater consciousness of thermal conductivity and a focus on safety. Shops with a high-mix, low volume (HMLV) workflow want to move jobs through production as quickly as possible. However, with more component complexity, more production – and more multi-tasking – on fewer machines, shops will slow down their processes by 5% to ensure high-quality output and avoid scrap. To maximize profit and minimize scrap, stainless steel also needs a higher coolant supply volume.
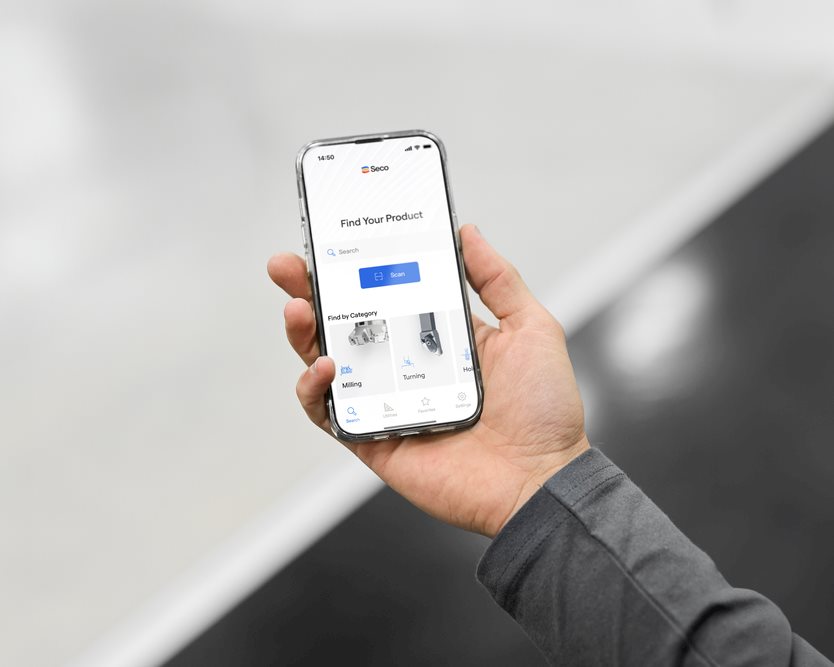
To produce stainless steel parts correctly the first time and every time, digital solutions and tools help reduce waste and scrap in production.
They enable shops to optimize the steps they take before a workpiece goes on a machine tool.
Simulation with digital twins is ideal for high-value parts. It may not be the ideal approach for routine parts, however, given the amount of programming and machine time involved.
Additive manufacturing can print parts with stainless steels, but the principal applications of AM typically involve super alloys and titanium. These challenging materials truly benefit from AM's ability to produce near net shapes and create parts that traditional machining techniques can't cut. Additionally, AM is ideal for complex parts such as medical implants that can't tolerate coolant or chip residue. These contaminants limit the human body's ability to integrate an implant into bone.
Successful shops set up and document basic standard procedures and protocols to achieve good tool life and productivity with stainless steel. They prioritize all the essentials of good machining, including proper workholding and fixturing, cutting parameters, chip control, coolant and lubrication, machine and tool maintenance and monitoring and inspection.
Among their workforce, these shops train new employees on successful approaches to tool selection, setup, programming, and software. They ensure that machinists know how to resolve common issues that may arise with stainless steel. They understand, monitor and troubleshoot tool wear patterns. They commit to continued use and continuous improvement of successful strategies. Above all, they prioritize high-quality results over everything else, including raw production speed. They know that the right approach may take a few minutes longer to complete, but it produces optimal parts.
Shops that optimize their production processes and output quality also build sustainability into their manufacturing practices. Any strategy that reduces scrapped parts has an immediate positive impact on environmental considerations. Likewise, strategies that eliminate wasted production cycles cut down on electrical and coolant use, machine wear and tool use. Any efficiency that limits the wasteful use of materials, equipment and resources contributes to a sustainable operation.
In some cases, customers change their orders and specify entire parts or components from alloys other than stainless steels. For example, some customers now require super alloys for piping jobs that need greater acid resistance than stainless steels can provide. Customers may replace stainless steel components, add super alloy coatings or weld in super alloy pieces through laser wire deposition. In jet engines, aluminum and carbon fiber replace stainless steel for weight reduction. Ironically, these replacement materials may be as difficult – or more difficult – to machine than stainless steels themselves.
In the past, big manufacturing plants employed full-time metal-cutting experts. Faced with complex parts and stainless steel alloys, today's often-smaller shops rely more on their suppliers for advice and for custom or customized tools. These shops look for ways to improve long-term approaches safely without risking scrap. To do that, they rely on tooling suppliers for research, testing and the latest tooling and parameters.
Instead of just cutters and inserts, tooling suppliers offer each customer a full solution that can include high-velocity coolant, tooling bodies, inserts, application strategies and more. Above all, a tooling supplier works as a trusted partner to help customers achieve the results they want in ISO M stainless steels – without waste and inefficiency.
Inline Content - Gridded Links
Tags: 'wp_guide_stainless_steel'
Max links: 1
Join our webinar about dynamic turning in stainless steel
Inline Content - Survey
Current code - 5fce8e61489f3034e74adc64