Differential Housing
Machined from nodular cast iron and housing the vehicle differential gear assemblies, differential housings present difficulties in terms of interrupted cuts during roughing passes. Surface finishes and tolerances must be held to customer standards, and machining operations involve custom combination tooling such as turning heads, drills and reamers.
YOUR MANUFACTURING CHALLENGES
- Drilling numerous holes with minimal cost and time.
- Efficiently and securely turning the internal diameter and face.
- Ensuring high productivity during turning of the outer diameter and face.
- Drilling numerous holes with low cycle times, high quality and reliability.
- Reaming precise holes with perfect surface finishes.
- Productively turning the internal diameter and back facing.
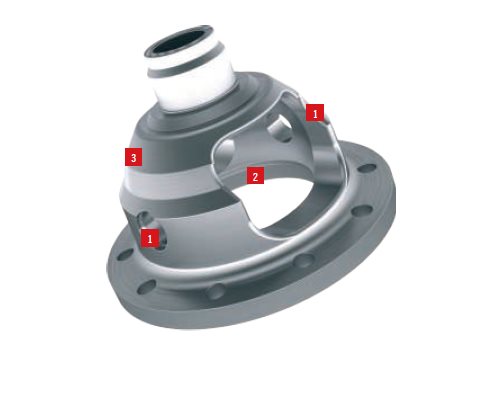
1 - Drilling numerous holes
Your Challenge: | | Drilling numerous holes with minimal cost and time. |
Our Solution: | | By offering the ability to chamfer a hole by plunging after drilling, the custom Perfomax Chamfer Drill combines operations to increase productivity. A unique flute design optimises chip removal, and the use of Perfomax drilling inserts allows for a very cost-effective process. Your benefits include reducing expenses while maintaining high process stability |
Product: | | Perfomax® Chamfer Drill |
| 2 - Turning the internal diameter and face |
Your Challenge: | | Efficiently and securely turning the internal diameter and face. |
Our Solution: | | The flexible Seco-Capto quick change turning head system reduces tool change times and can be error-proof modified for mass production applications. Offering highly rigid and accurate performance, the system also enables full automation of presetting by adding electronic data chips to the toolholders. Additionally the chip removal rate for this application can be maximized by using ISO/ANSI Duratomic® inserts, specifically the TK grades. Your benefits include reliable accuracy and increased efficiency. |
Product: | | Seco-CaptoTM Boring Tool |
3 - Ensuring high productivity
Your Challenge: | | Ensuring high productivity during turning of the outer diameter and face. |
Our Solution: | | The flexible Seco-Capto quick change turning head system reduces tool change times and can be error-proof modified for mass production applications. Offering highly rigid and accurate performance, the system also enables full automation of presetting by adding electronic data chips to the toolholders. Additionally, using ISO/ANSI Duratomic® inserts maximizes chip removal rate for this application. Your benefits include reliable accuracy and increased efficiency. |
Product: | | Seco-CaptoTM Turning Tool |
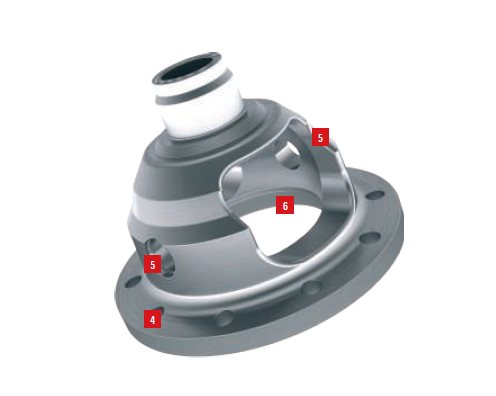
4 - Drilling numerous holes
Your Challenge: | | Drilling numerous holes with low cycle times, high quality and reliability. |
Our Solution: | | Providing high performance when dealing with angled exits or intersecting holes, the Seco Feedmax Chamfer Drill utilises the light-cutting geometry and a special edge preparation to increase process security and tool life. The tool also incorporates a low-friction coating, and uses four land margins to increase stability. Your benefits include maintaining productivity in challenging, high-tolerance holes. |
Product: | | Seco-FeedmaxTM Chamfer Drill |
5 - Reaming precise holes
Your Challenge: | | Reaming precise holes with perfect surface finishes. |
Our Solution: | | An interchangeable head reamer, Precimaster™ Plus minimizes cost per hole while providing excellent results. Additionally, our Nanofix™, Precifix™ and Xfix™ lines fill out our range of reaming products, guaranteeing a productive and high quality solution for holes ranging from 2.97 mm to 155 mm in diameter. Your benefits include reducing costs while maintaining exacting tolerances and surface finish requirements. |
Product: | | Seco Reaming Solutions |
6 - Productively turning
| Your Challenge: | | Productively turning the internal diameter and back facing. |
| Our Solution: | | The custom Seco-Capto quick change turning head system reduces tool change times and can be error-proof modified for mass production applications. The system also enables full automation of presetting by adding electronic data chips to the toolholders. Additionally, using Duratomic® TK insert grades that were specially developed for cast iron machining will maximize metal removal rates for this application. Your benefits include reliable accuracy and increased efficiency. |
| Product: | | Seco-CaptoTM Turning Tool |