Gear
Many gear sizes and types are used in vehicle production. Most gears are carbon steel, and chip control can be an issue when machining non-heat treated gears in fully automated production lines. Hard machining tooling is required when gears are machined after heat treating to eliminate grinding operations and reduce production costs.
YOUR MANUFACTURING CHALLENGES
- Maintaining efficiency through effective chipbreaking when roughing the outer diameter.
- Productively turning the internal diameter and undercut groove.
- Productively turning the internal diameter and back facing.
- Maximising productivity when milling teeth entries.
- Maintaining hard-turning productivity when plunging the back face and finishing the bore diameter.
- Minimising cycle times while reliably grooving in an interrupted cut.
- Reliably hard turning the finishing interrupted cut on the outer diameter.
- Ensuring hard-turning efficiency when finishing the face and synchromesh taper with interruption.
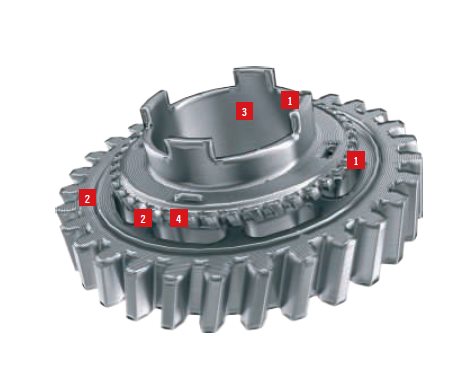
1 - Roughing the outer diameter
Your Challenge: | | Maintaining efficiency through effective chipbreaking when roughing the outer diameter. |
Our Solution: | | Jetstream Tooling delivers a high-pressure jet of coolant to the optimum position close to the cutting edge. In addition to eliminating heat build up, this lifts the chip away from the rake face to increase chip control and maximize tool life. Seco-Capto systems can be errorproof modified for mass production applications, and allow for full automation by adding electronic data chips to the tool holders. Your benefits include increased process reliability and productivity. |
Product: | | Seco-CaptoTM Custom Jetstream Tooling® Turning Tool |
2 - Turning the internal diameter and undercut groove
Your Challenge: | | Productively turning the internal diameter and undercut groove. |
Our Solution: | | The custom Seco-Capto quick change turning head system combines boring and grooving operations and can be error-proof modified for mass production applications. The system also enables full automation of presetting by adding electronic data chips to the toolholders. Additionally, using ISO/ ANSI WNMG 06 inserts in a Duratomic® grade provides the most economical solution for this application. Your benefits include reliable accuracy and increased efficiency. |
Product: | | Seco-CaptoTM Turning Tool |
3 - Turning the internal diameter and back facing
Your Challenge: | | Productively turning the internal diameter and back facing. |
Our Solution: | | The flexible Seco-Capto quick change turning head system reduces tool change times and can be error-proof modified for mass production applications. Offering highly rigid and accurate performance, the system also enables full automation of presetting by adding electronic data chips to the toolholders. Additionally, using ISO/ANSI Duratomic® inserts with new positive chipbreaking geometries maximizes chip removal rates for this application. Your benefits include reliable accuracy and increased efficiency. |
Product: | | Seco-CaptoTM Turning Tool |
| 4 - Milling teeth entries |
Your Challenge: | | Maximising productivity when milling teeth entries. |
Our Solution: | | Right-handed and left-handed versions of this custom tool are applied simultaneously to chamfer opposite sides of the tooth entry and eliminate potential burrs. With a center-lock clamping system and precision ground inserts, the cutter achieves impeccable angular positioning accuracy and surface finish. Your benefits include an easy-to-apply solution for achieving high quality requirements. |
Product: | | Chamfering Tool |
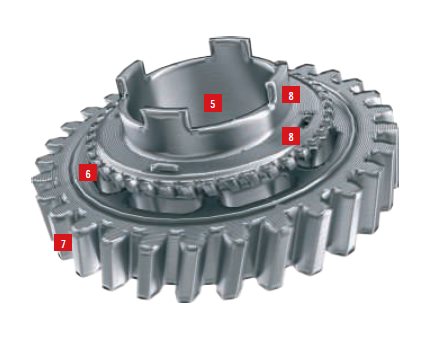
5 - Copy turning the flange diameter
Your Challenge: | | Maintaining hard-turning productivity when plunging the back face and finishing the bore diameter. |
Product: | | Seco-Capto™ Turning Tool |
6 - Reliably grooving in an interrupted cut
Your Challenge: | | Minimising cycle times while reliably grooving in an interrupted cut. |
Our Solution: | | The flexible Seco-Capto quick change turning head system reduces tool change times and can be error-proof modified for mass production applications. Offering highly rigid and accurate performance, the system also enables full automation of presetting by adding electronic data chips to the toolholders. Additionally, using ISO/ANSI Duratomic® inserts maximizes chip removal rate for this application. The wide variety of available geometries guarantees optimal chipbreaking efficiency. Your benefits include reliable accuracy and increased efficiency. |
Product: | | Seco-Capto™ MDT Grooving Tool |
7 - Reliably hard turning
Your Challenge: | | Reliably hard turning the finishing interrupted cut on the outer diameter. |
Our Solution: | | The flexible Seco-Capto quick change turning head system reduces tool change times and can be error-proof modified for mass production applications. Offering highly rigid and accurate performance, the system also enables full automation of presetting by adding electronic data chips to the toolholders. Additionally, fine grain CH2540 inserts provide exceptional toughness in interrupted finish machining of hard steels rated 55 HRC – 64 HRC. Your benefits include reliable accuracy and increased efficiency. |
Product: | | Seco-Capto™ Turning Tool |
| 8 - Ensuring hard-turning |
Your Challenge: | | Ensuring hard-turning efficiency when finishing the face and synchromesh taper with interruption. |
Our Solution: | | The Seco-Capto with two seat pockets reduces turret revolutions and can be error-proof modified for mass production applications. Offering highly rigid and accurate performance, the system also enables full automation of presetting by adding electronic data chips to the toolholders. Fine grain CH2540 inserts provide exceptional toughness in interrupted finish machining of hard steels rated 55 – 64 HRC. CBN060K plunging inserts offer short cycle times and surface finishes below Ra 0.4. Your benefits include reliable accuracy and increased efficiency. |
Product: | | Seco-Capto™ Turning Tool |
HOMERelated content
Gearing up for the win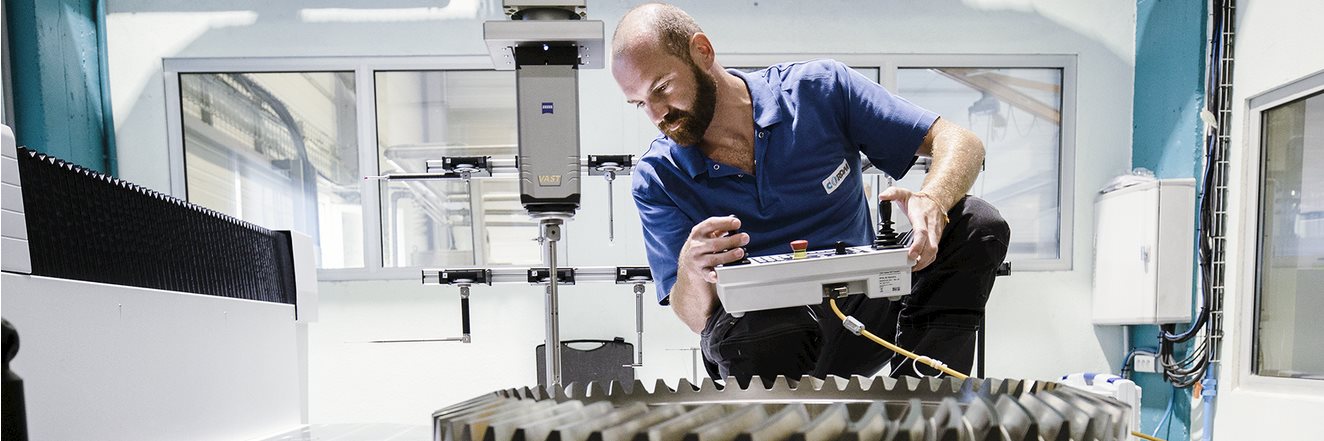
Video: High-Speed Gear Hobbing with a Seco Indexable Hob Mill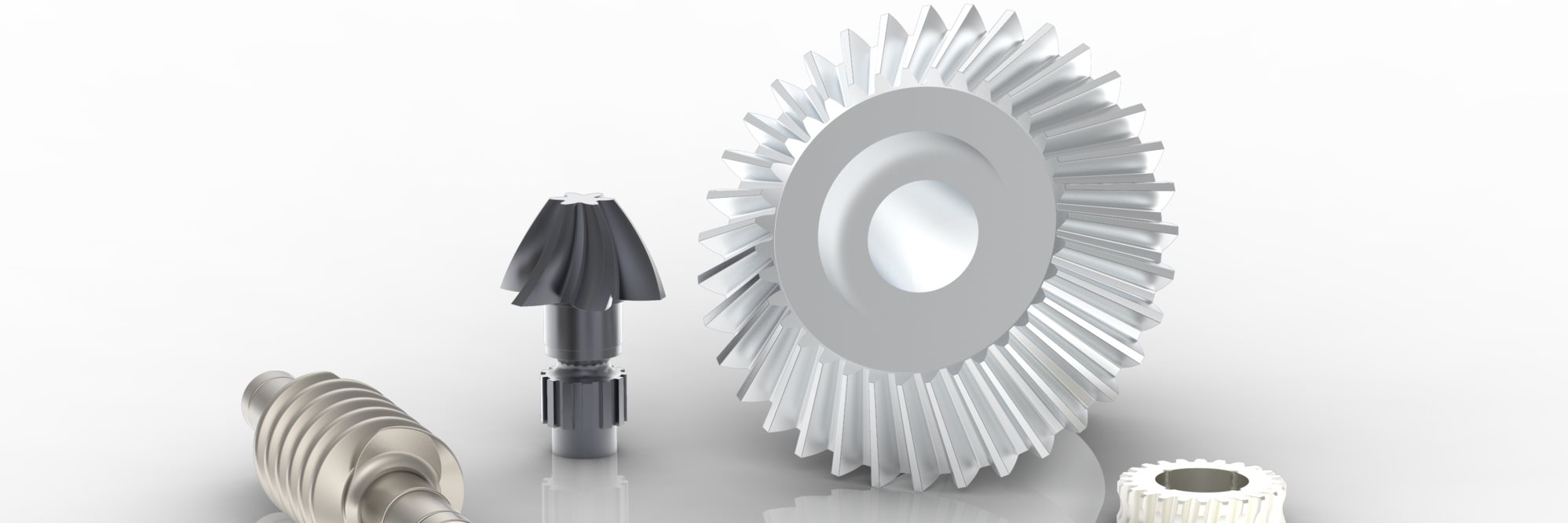
Case Studies: Gear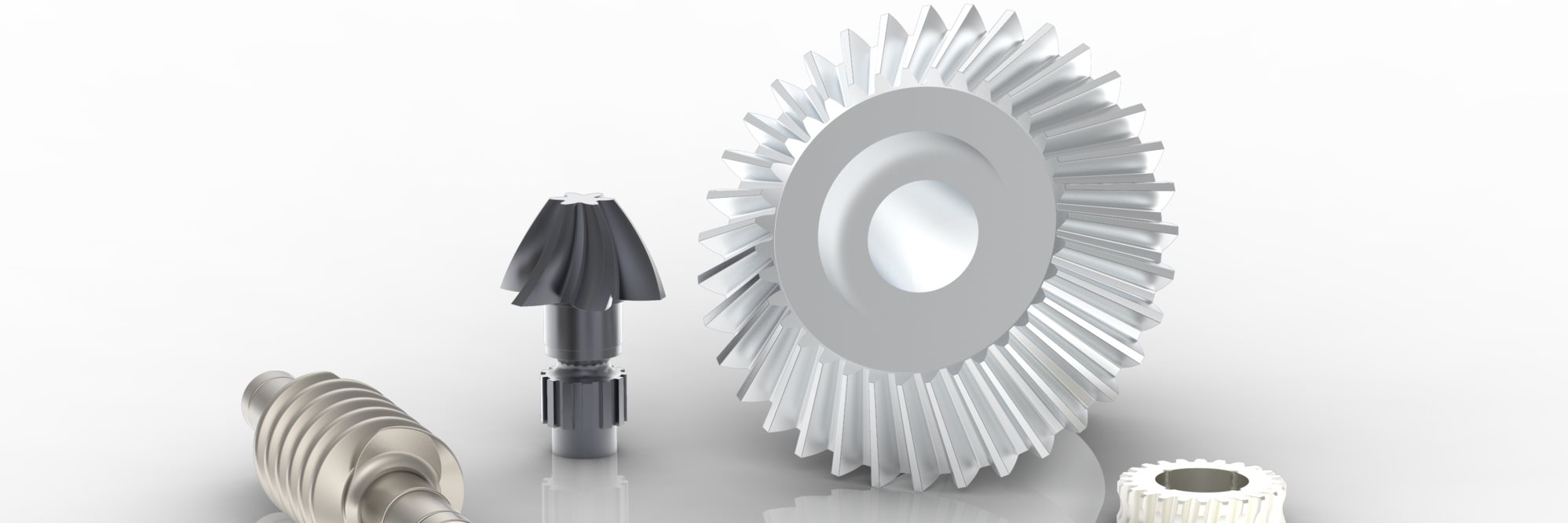
Video: Indexable gear skiving M5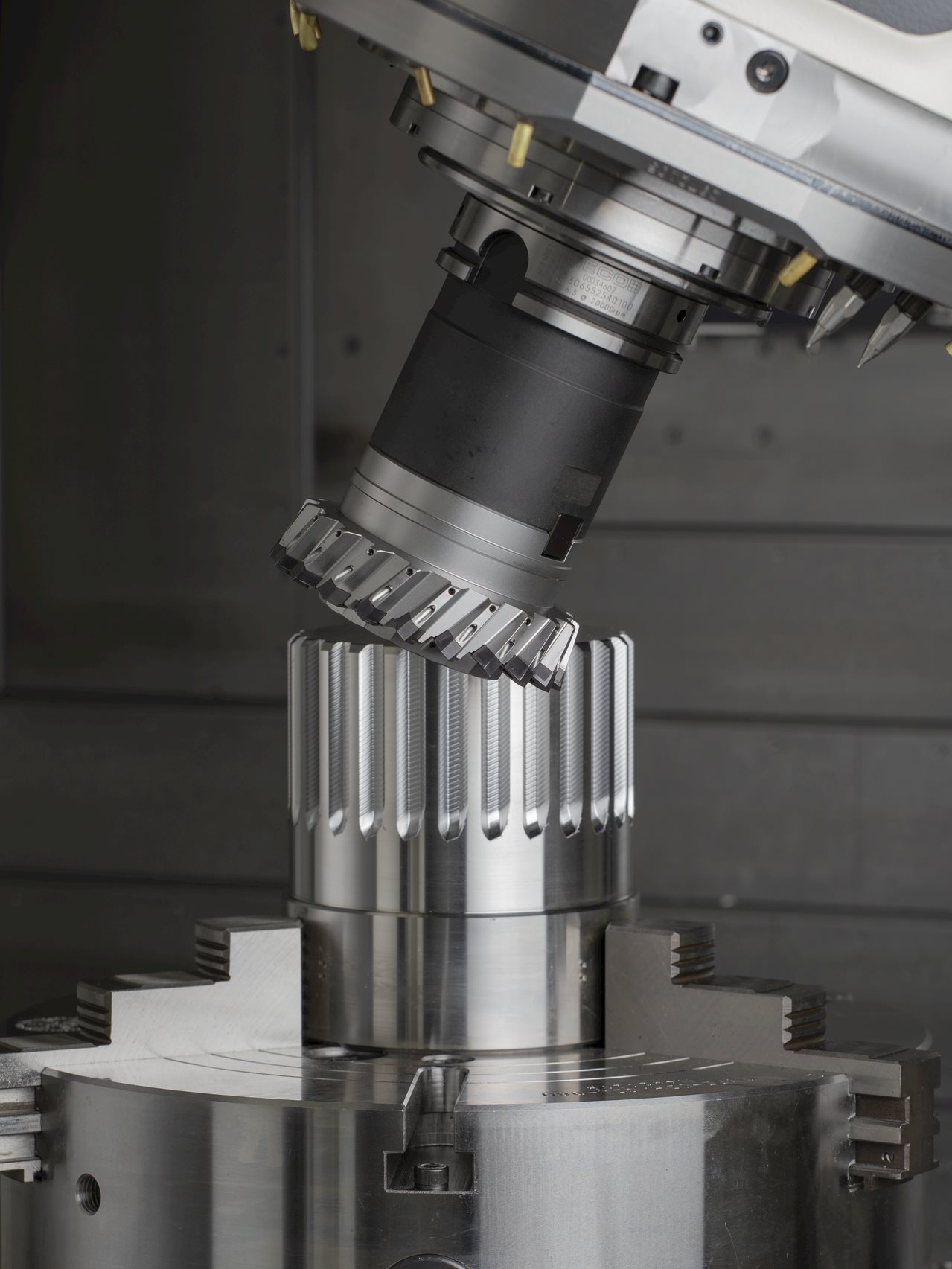
Video: Boosting Gear Production: Custom Hob Cuts Time & Increases Efficiency | Seco tools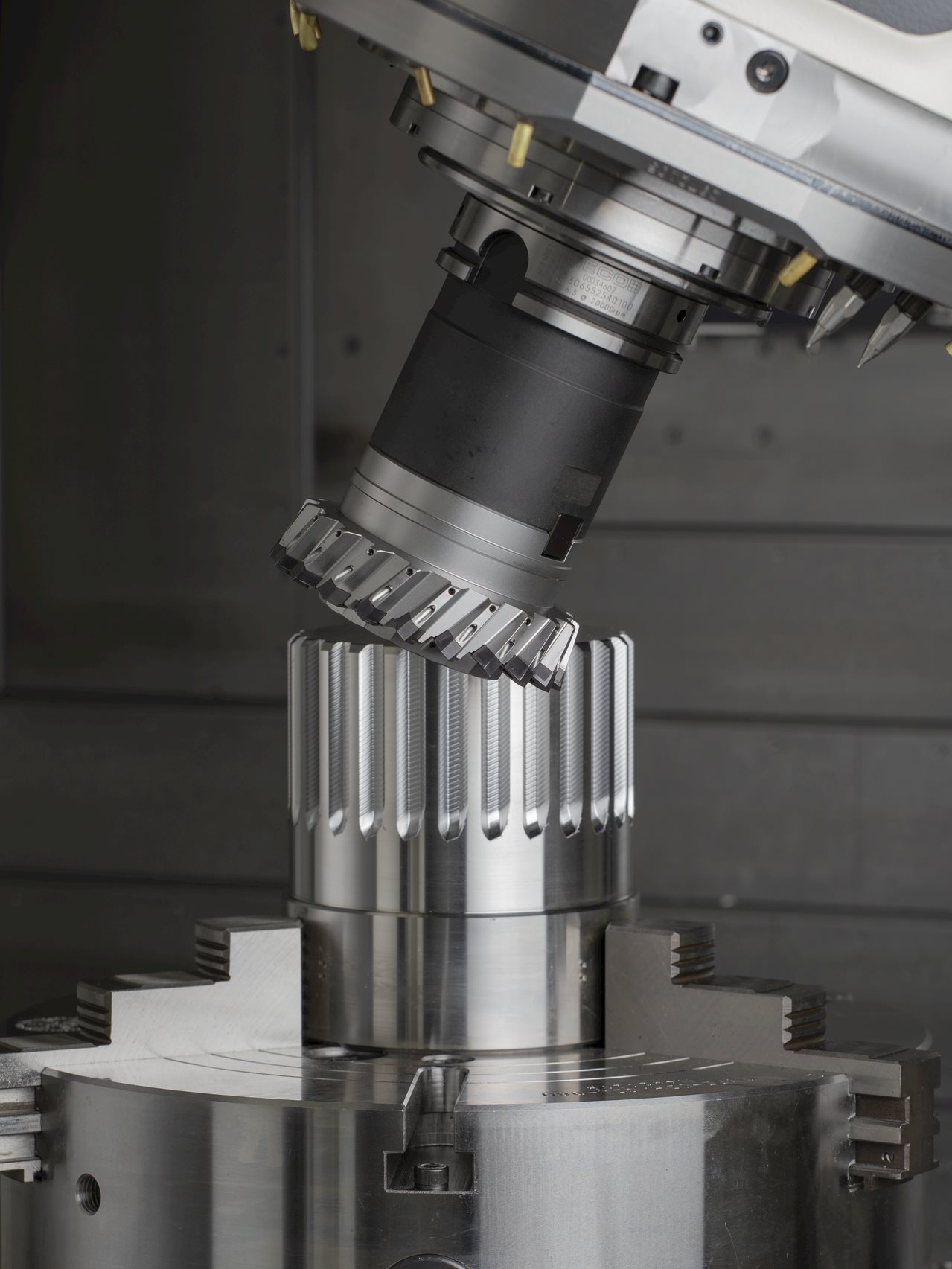
Video: Advanced Tooling for Aerospace Disc Manufacturing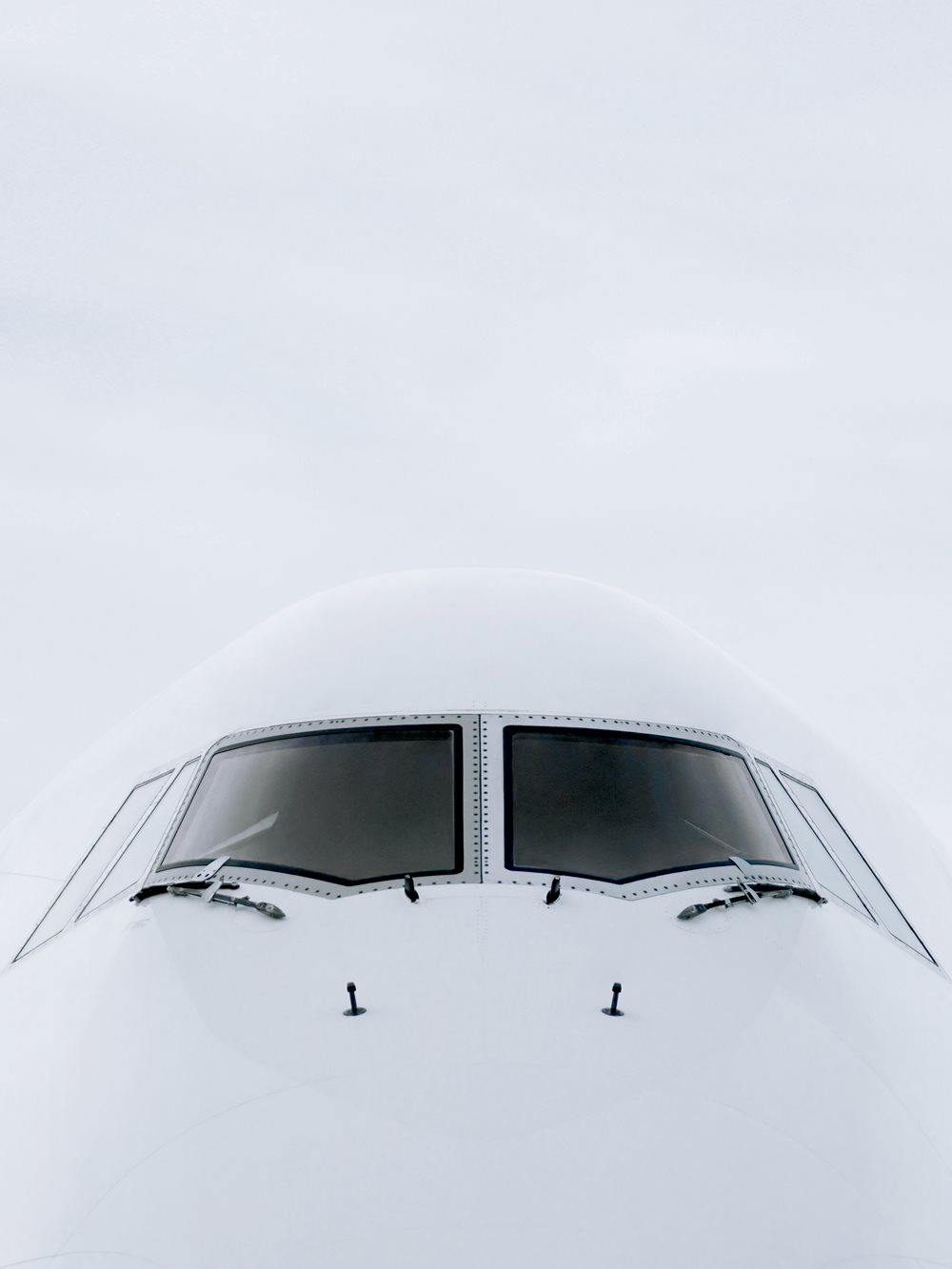
Video: Power Skiving – Machining of a spur gear M3.5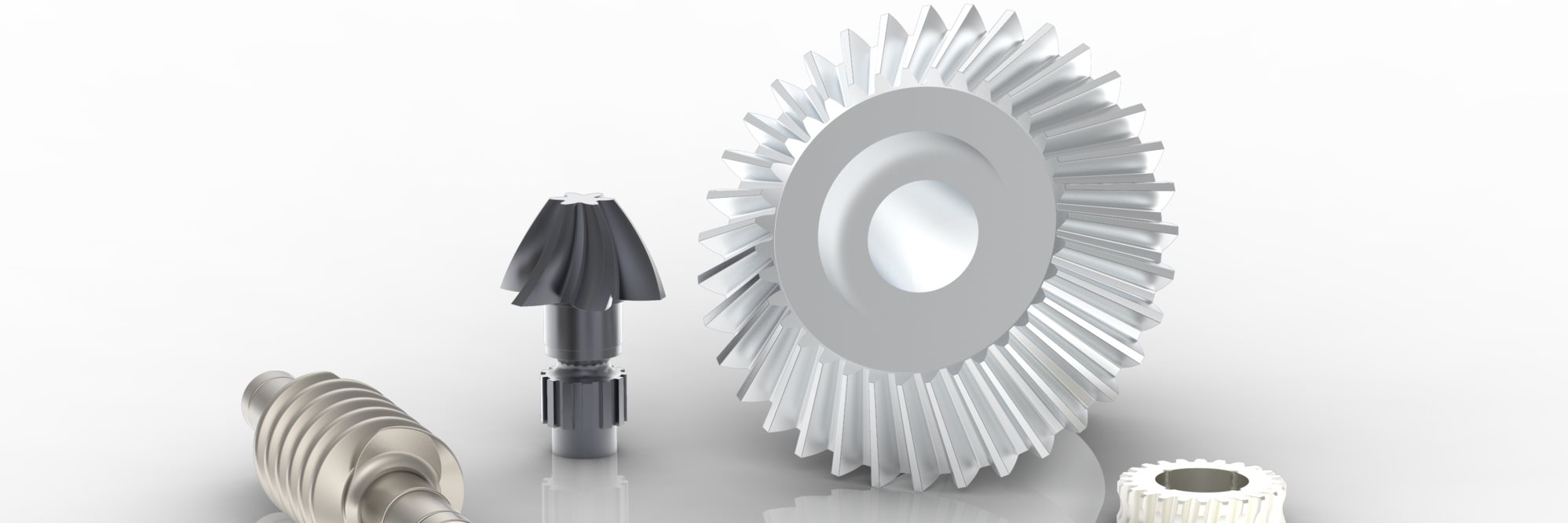
Why gear skiving can be good news for jet turbine disc manufacturers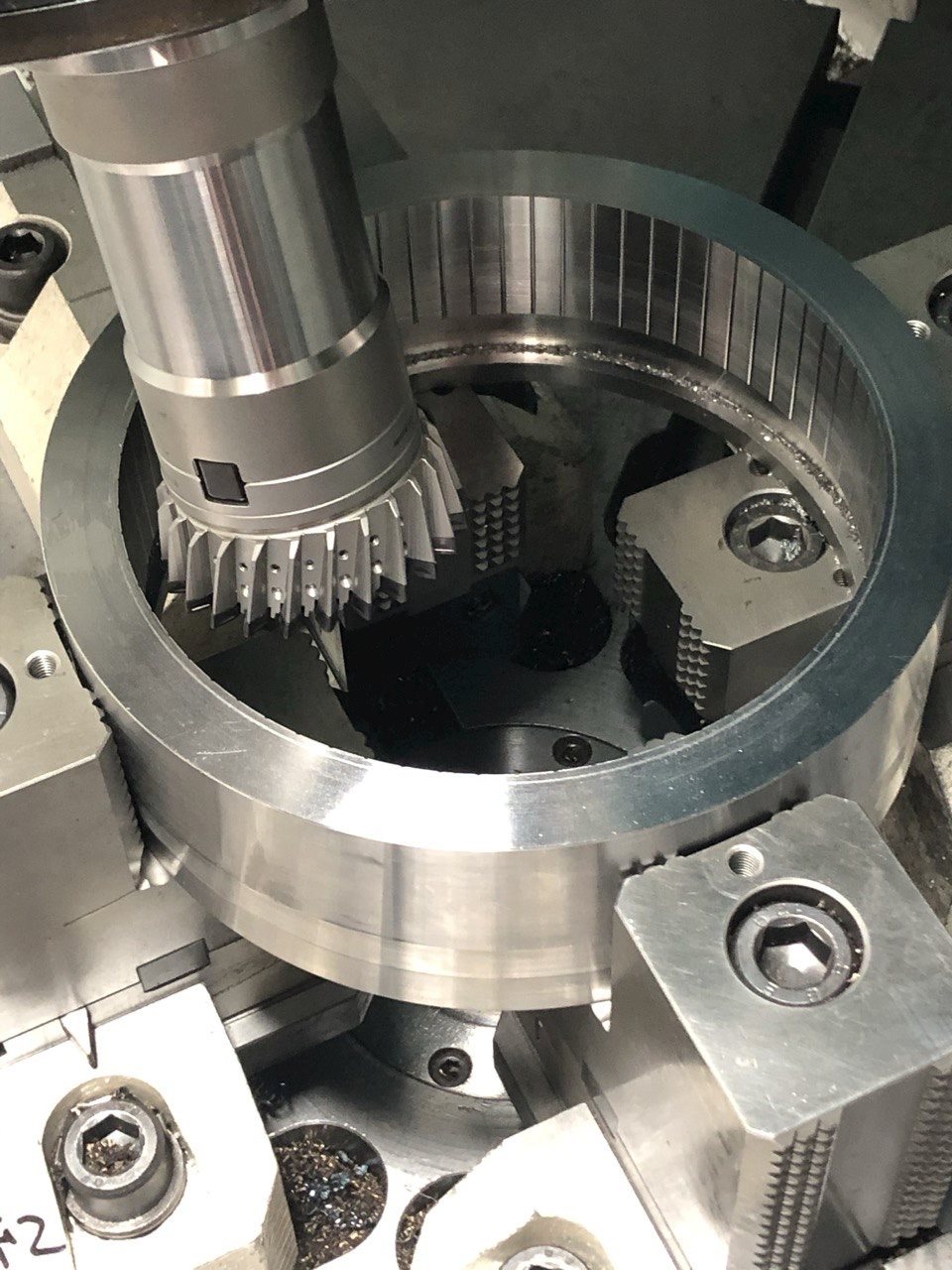
Differential Housing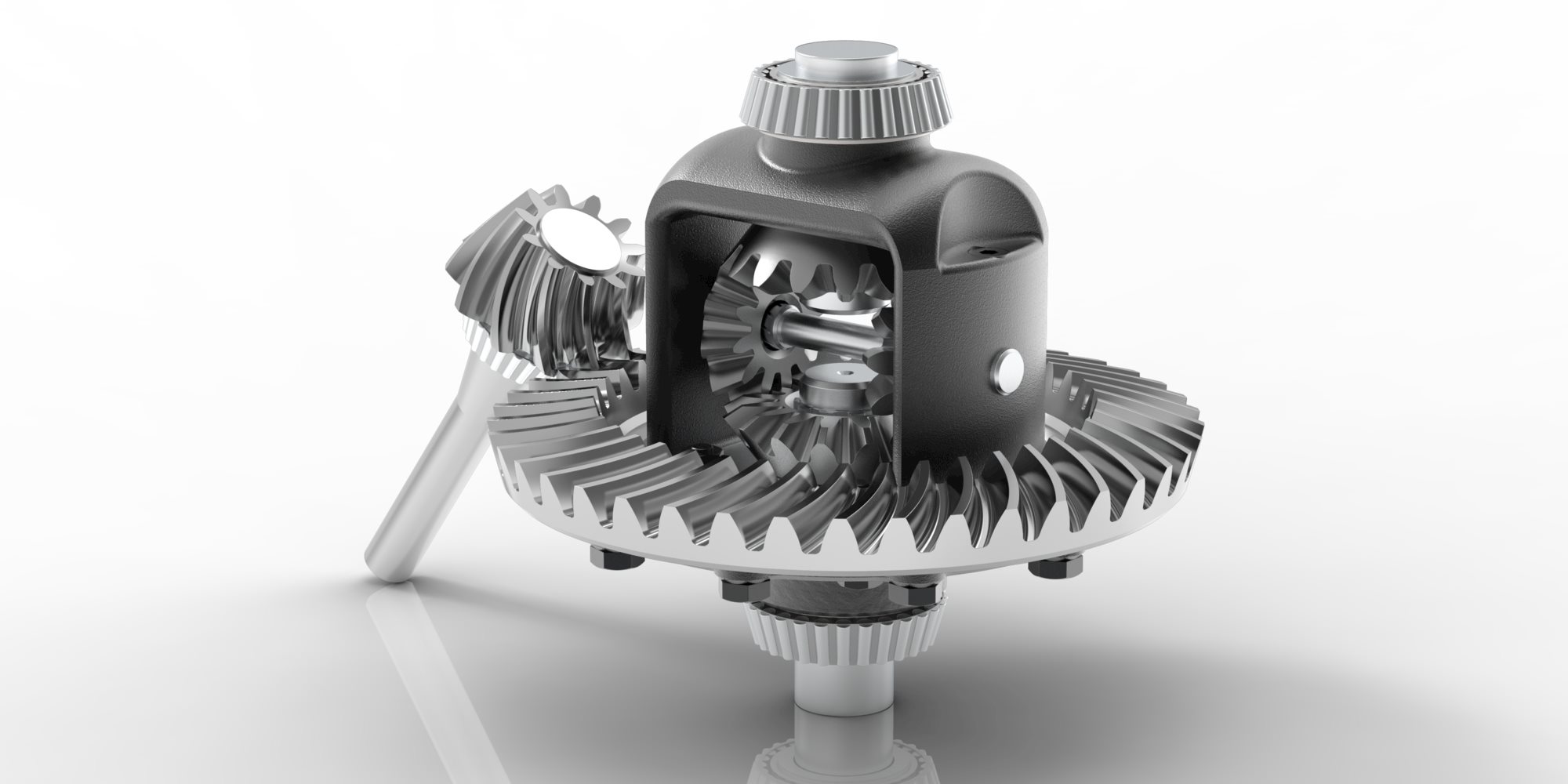
Axle Shaft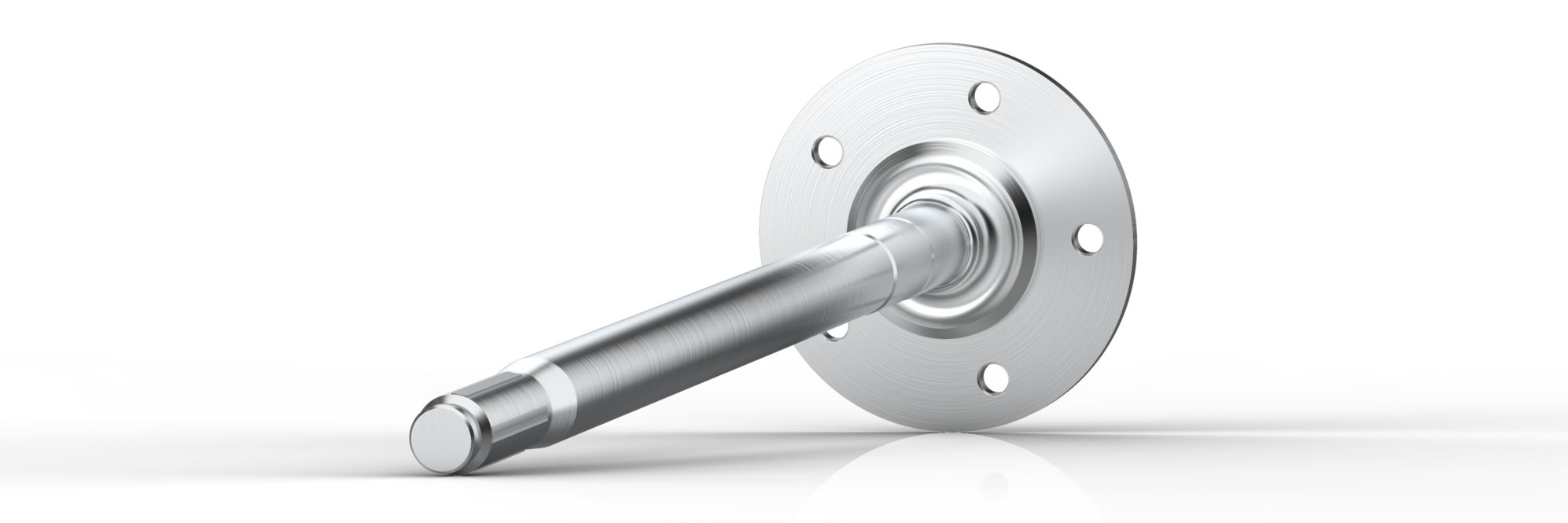