Lower Ball Joint Location
Ball Joint: | 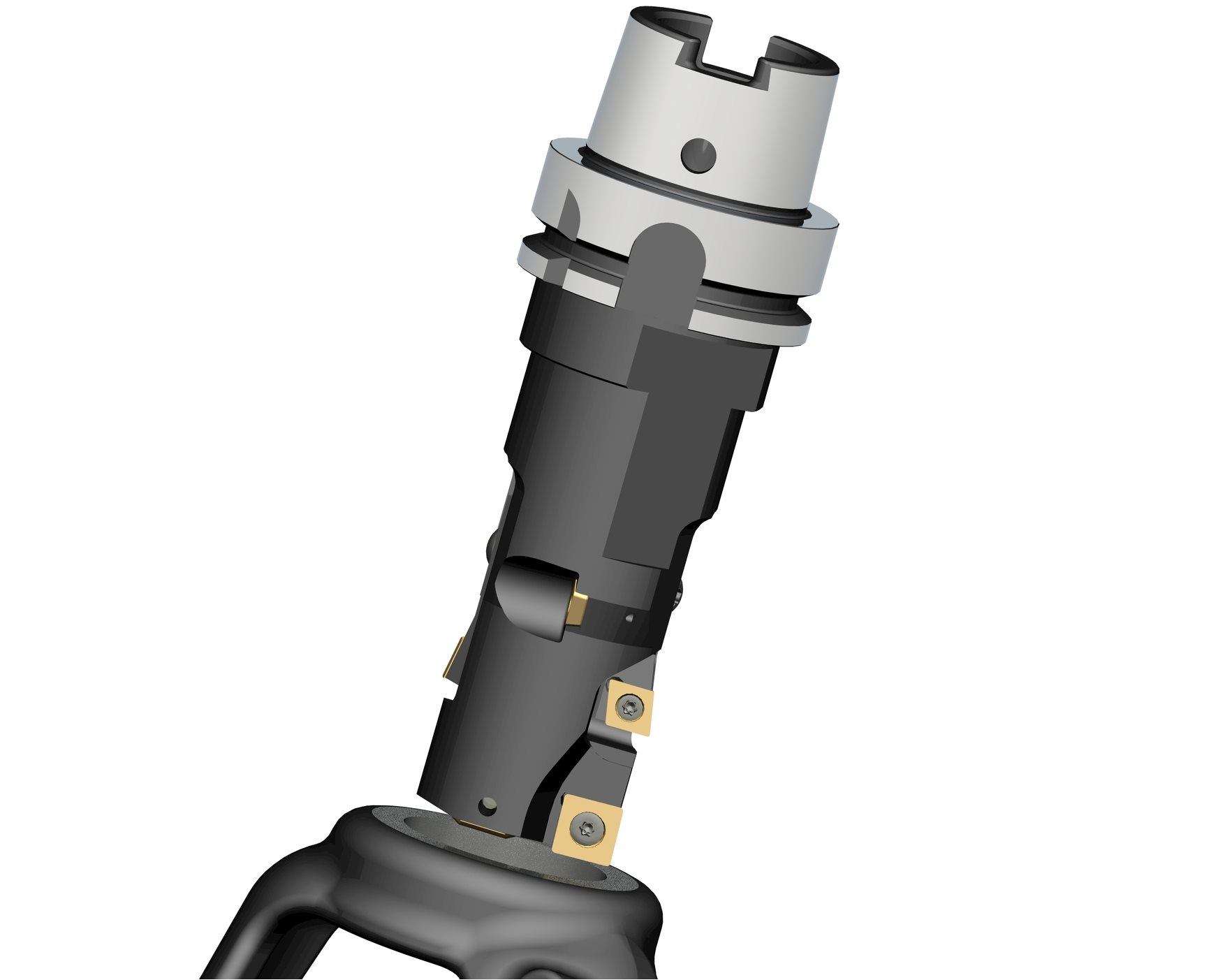 |
Your Challenge: | Increase productivity by reducing cycle times and tooling CPU (cost per unit). |
Our proven Solution: | Custom multi-step boring bar that roughs, finishes and chamfers using ISO / ANSI positive inserts. To achieve the best possible results, Seco has developed a complete range of new Duratomic® grades that allows application of high cutting parameters in forged steel with TP grades and in nodular cast iron with the TK grades. For aluminium steering knuckles, we recommend use of the AL-KX geometry and grade for roughing, or grade PCD20. |
Lower Arm Ball Joint Location: | 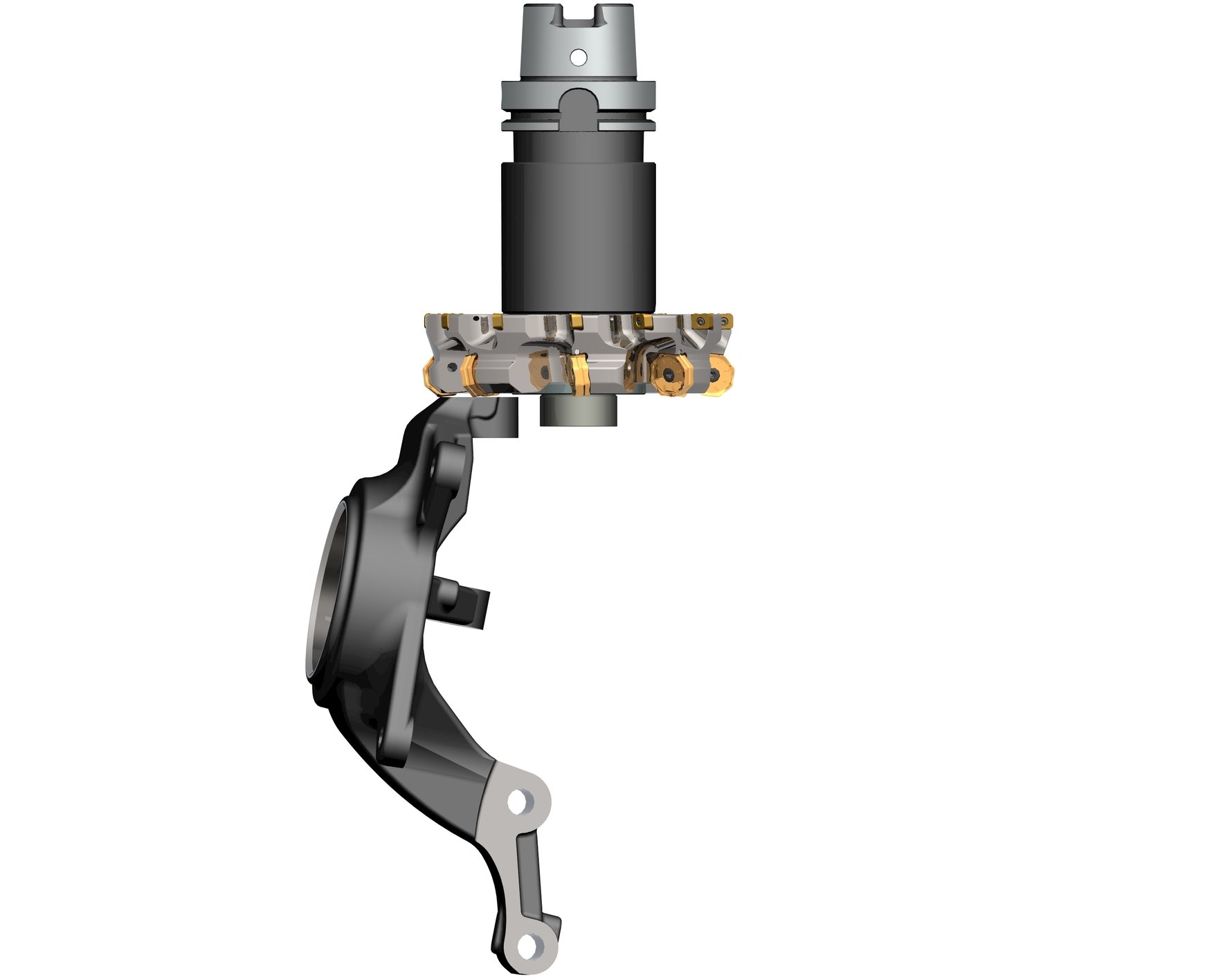 |
Your Challenge: | Achieve the best performance in terms of productivity and cost. Reduce cutting forces on lessrigid clamping fixture, obtain the required surface finish. |
Our proven Solution: | A custom double disc milling cutter combining Double Octomill and R335.18 cutters. To machine the top face, the economical choice is the Double Octomill, with double-sided inserts that feature 16 cutting edges and a positive chip groove in order to reduce cutting forces and limit the risk of vibration. |
Lower Arm Ball Joint Location: | 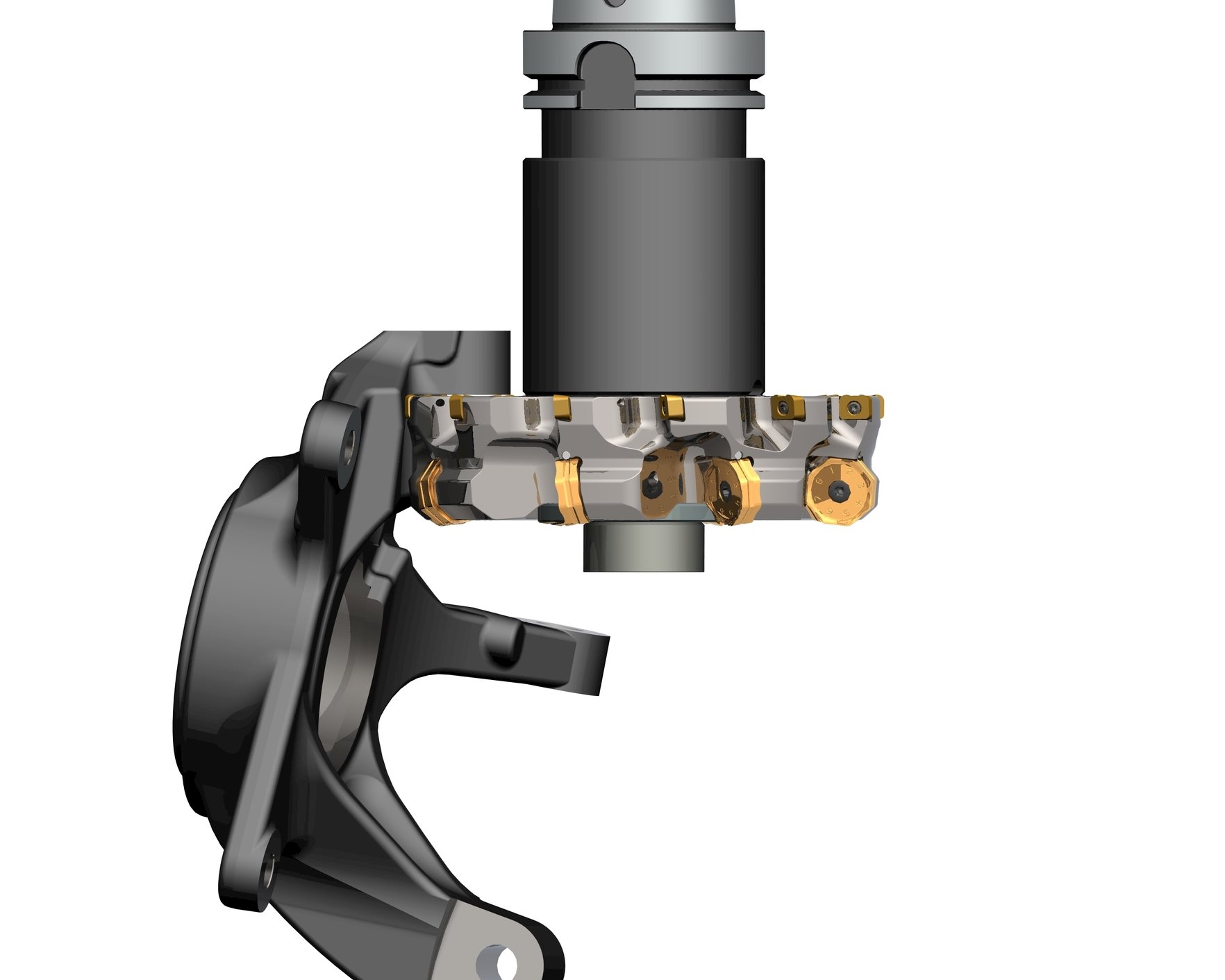 |
Your Challenge: | Achieve the best performance in terms of productivity and cost. Reduce cutting forces on lessrigid clamping fixture, obtain the required surface finish. |
Our proven Solution: | A custom double disc milling cutter combining Double Octomill and R335.18 cutters. The R335.18 cutter uses LNKT standard inserts that feature a positive chip groove to perform the back face milling operation and achieve the required radius value on the bottom face of the lower ball joint. |
Lower Ball Joint Location: |  |
Your Challenge: | Achieve the best performance in terms of productivity and cost. Reduce cutting forces on lessrigid clamping fixture, obtain the required surface finish. |
Our proven Solution: | To improve productivity and reduce the number of tools in the tool magazine, Seco has developed a combination of disc milling cutters, using R & L 335.29 cutters itted with RPHT 1204 inserts to achieve the required radius on the component plus a 335.10 slotting disc milling cutter to split the locking nut. By changing the geometries and grades, this coniguration permits machining of diferent workpiece materials including aluminium, ductile cast iron, and forged steel. For aluminium Seco also ofers PCD brazed cutters as an alternative. |
HOMERelated content
Case Studies: Lower Ball Joint Location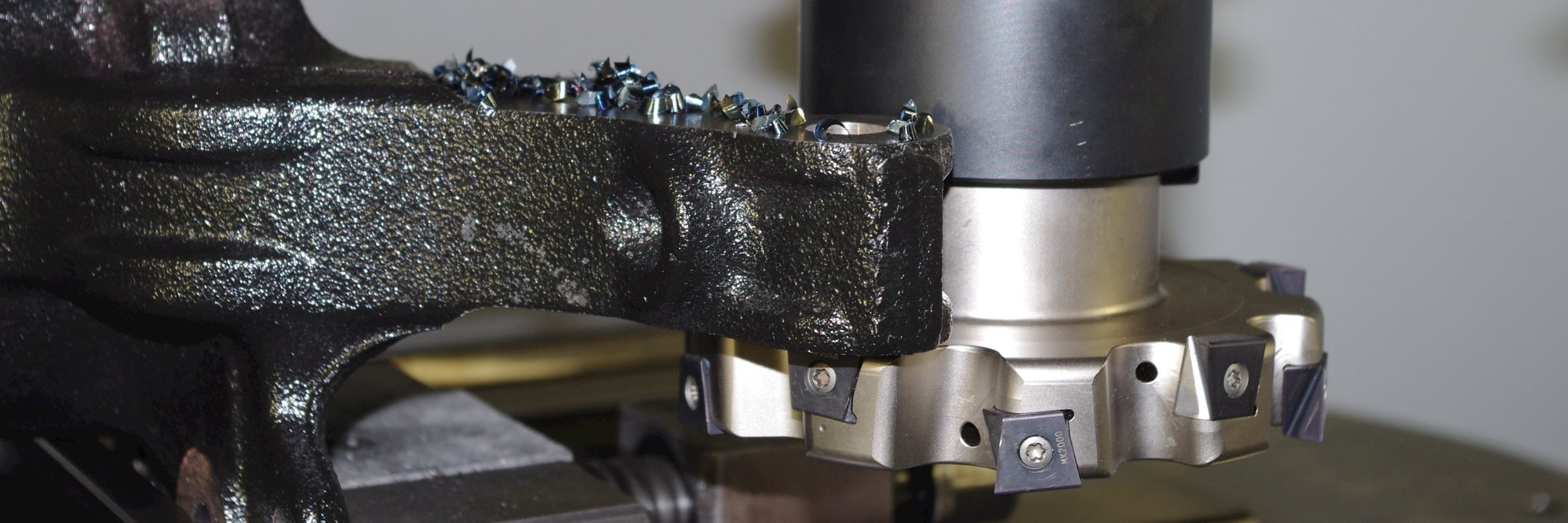
Inspiration through Innovation 2020 – Aerospace Manufacturing Best-Practice Virtual Event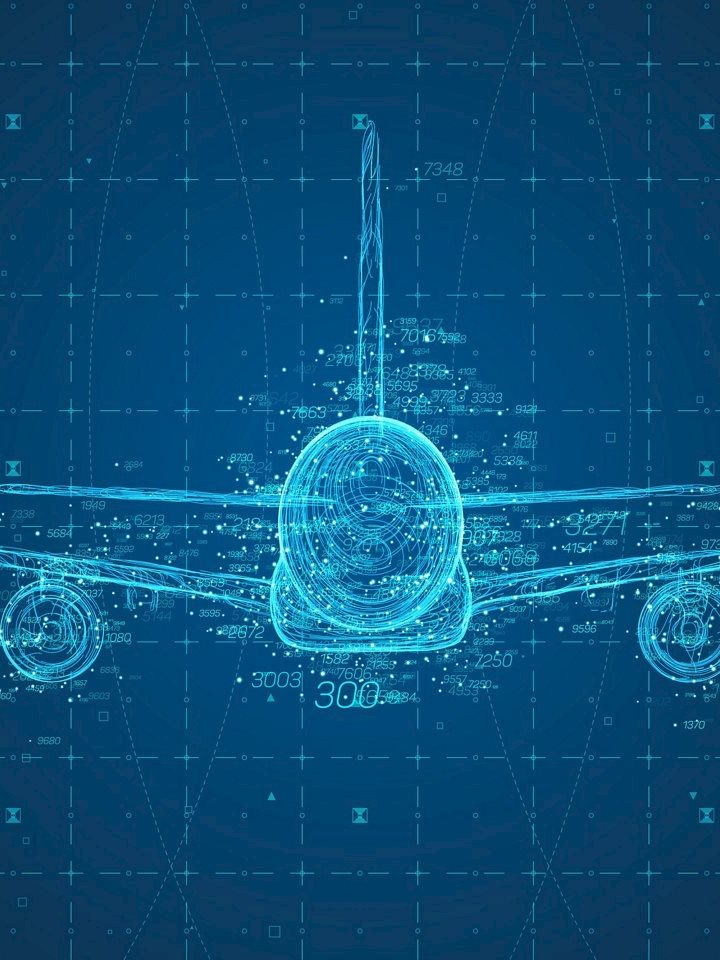
Truck And Bus Applications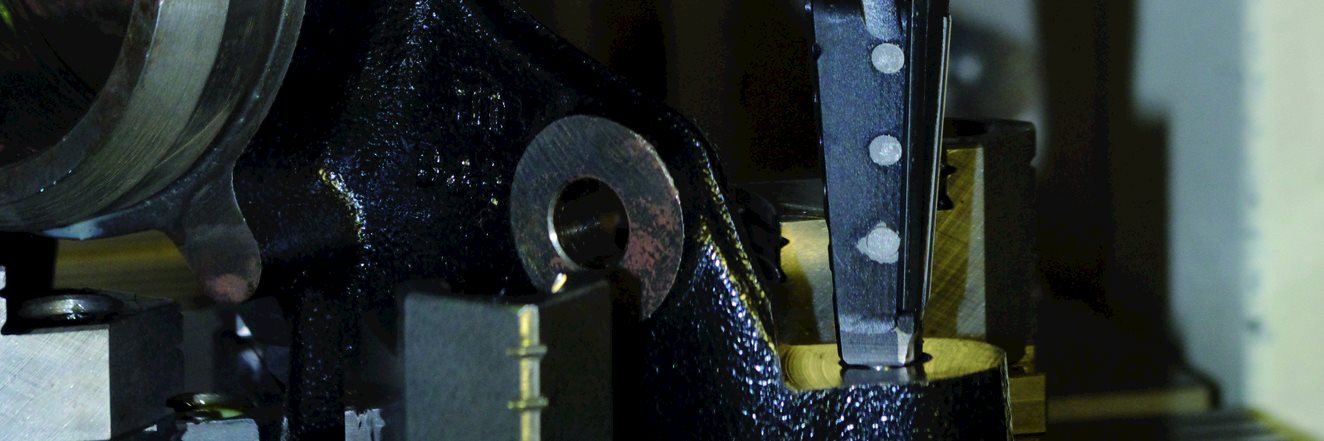
Ball Bearing Location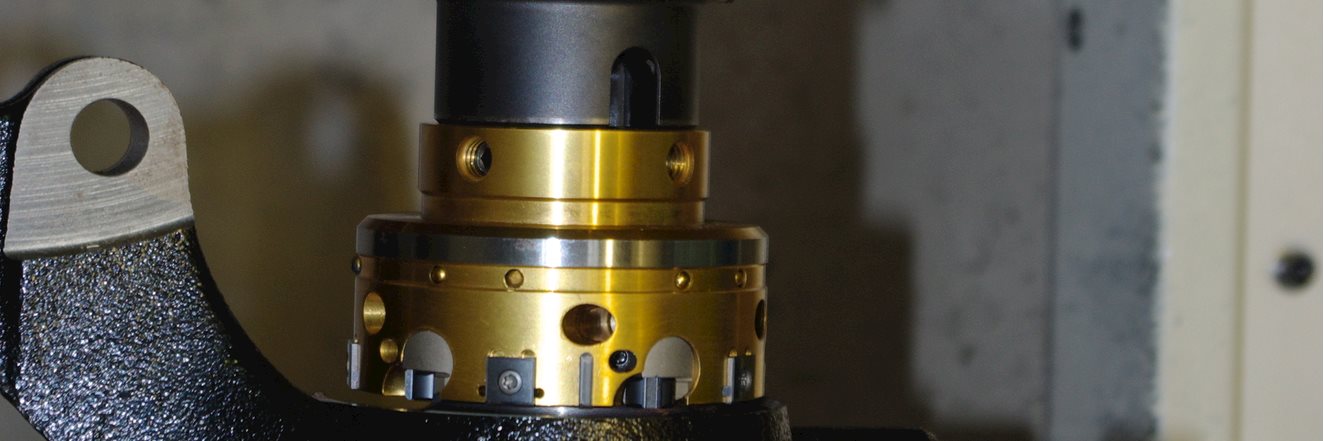
Brake Caliper Fastening Holes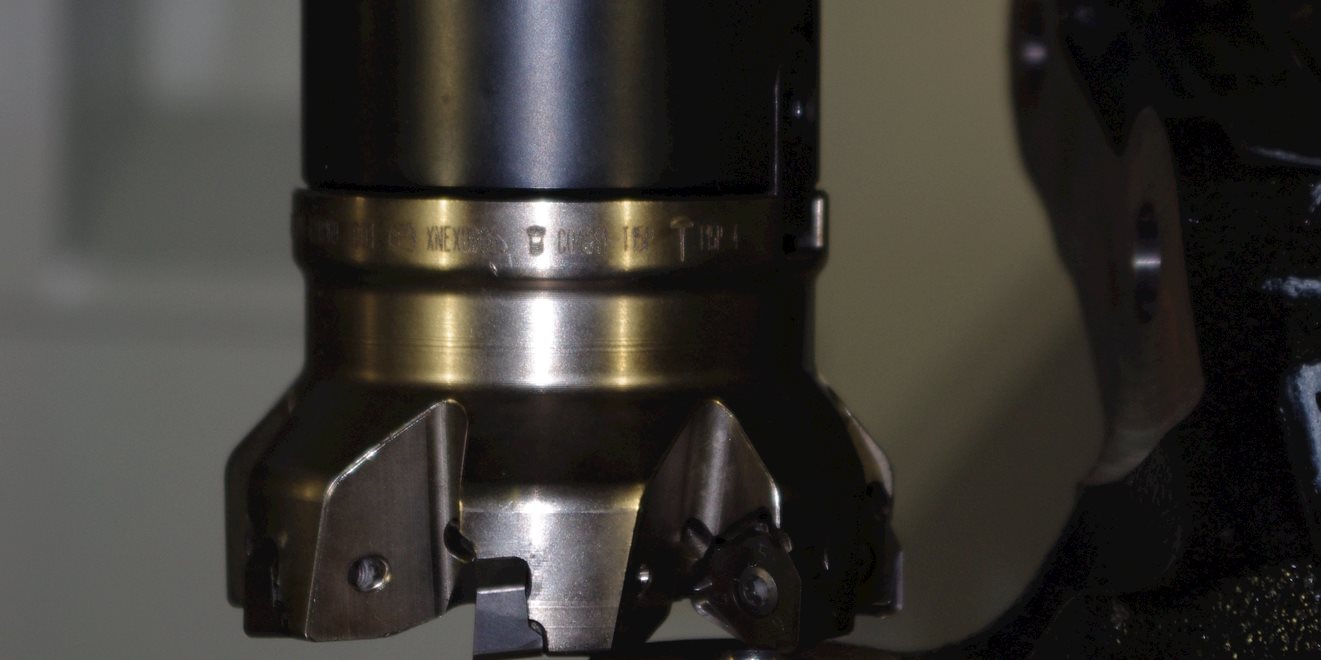
Steering Arm, Tie Rod Location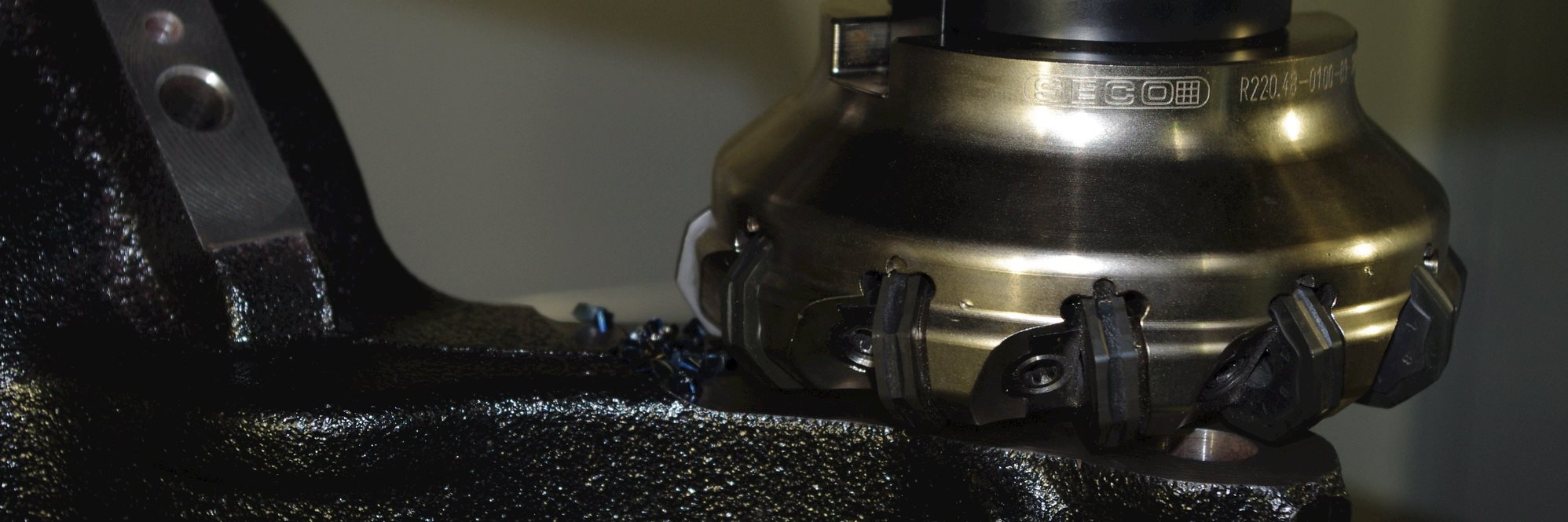
ABS/ ABR Sensor Location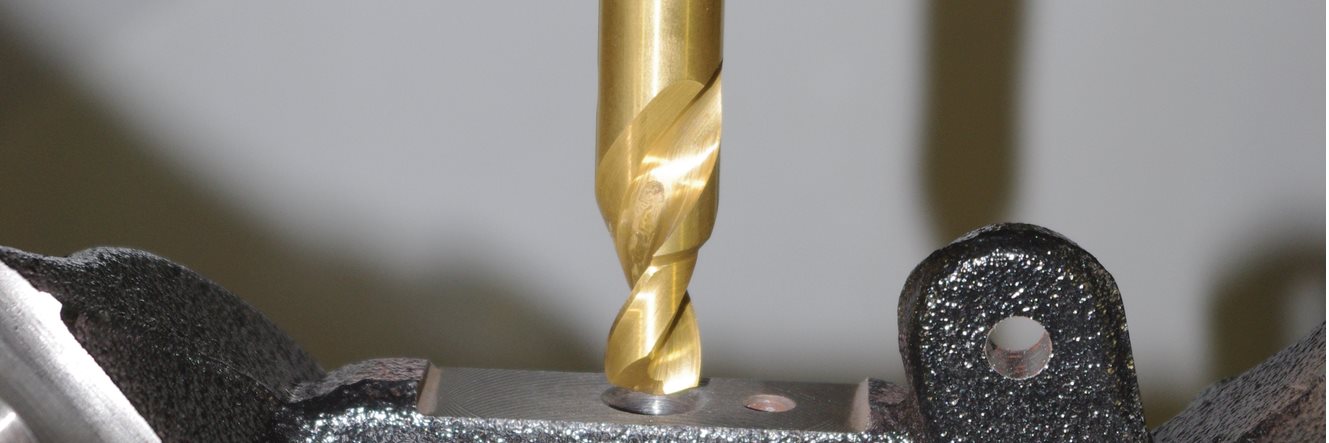
Strut Mount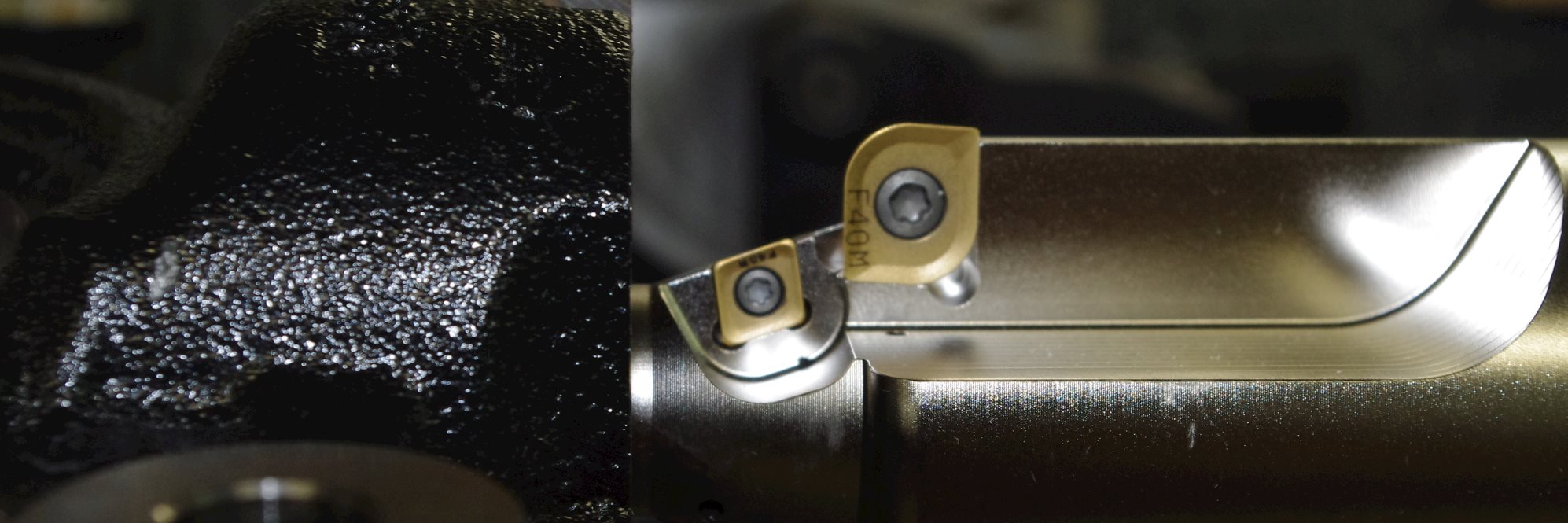
Video: 5 solutions to the main Steering knuckle machining challenges | Seco tools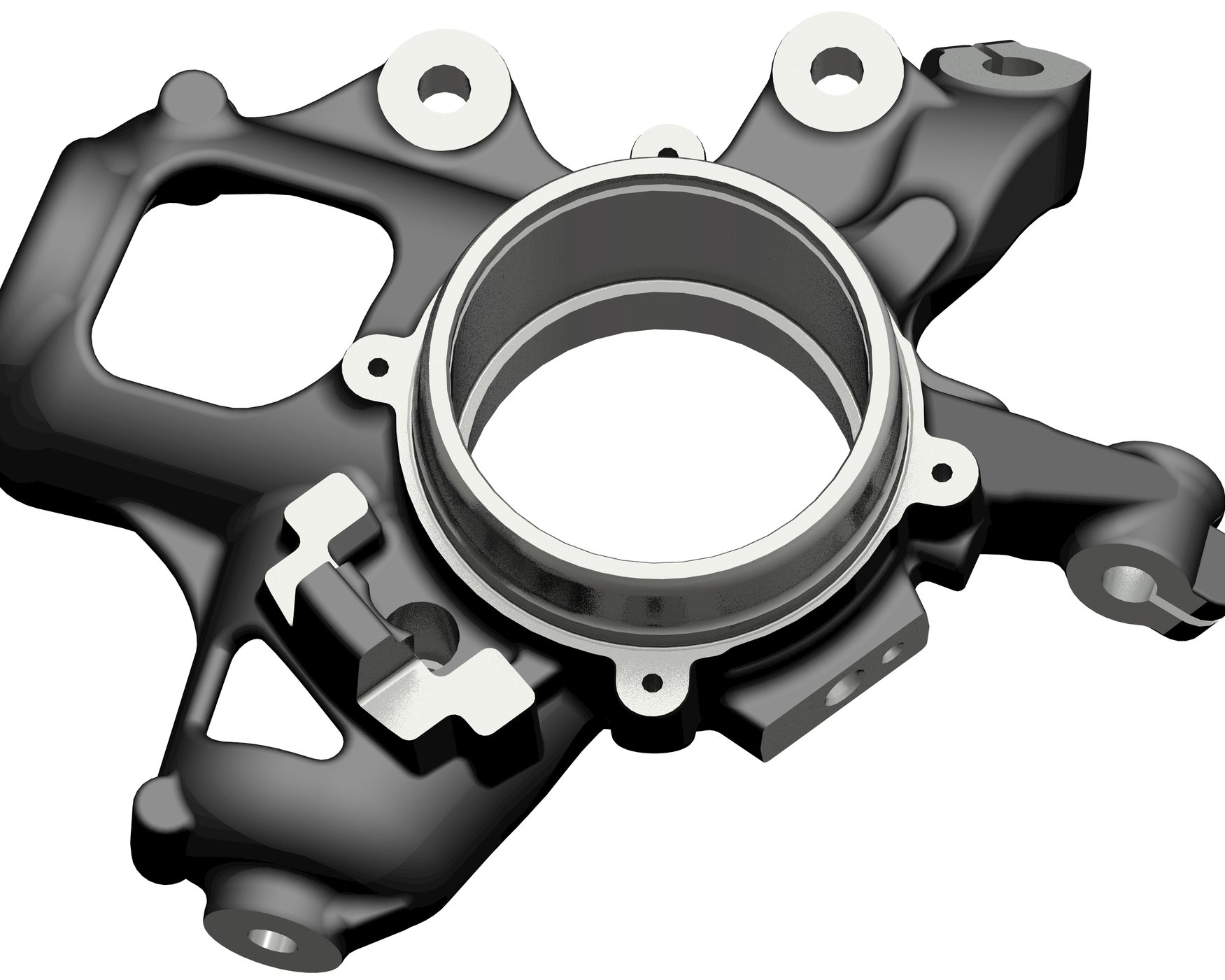
Thank You!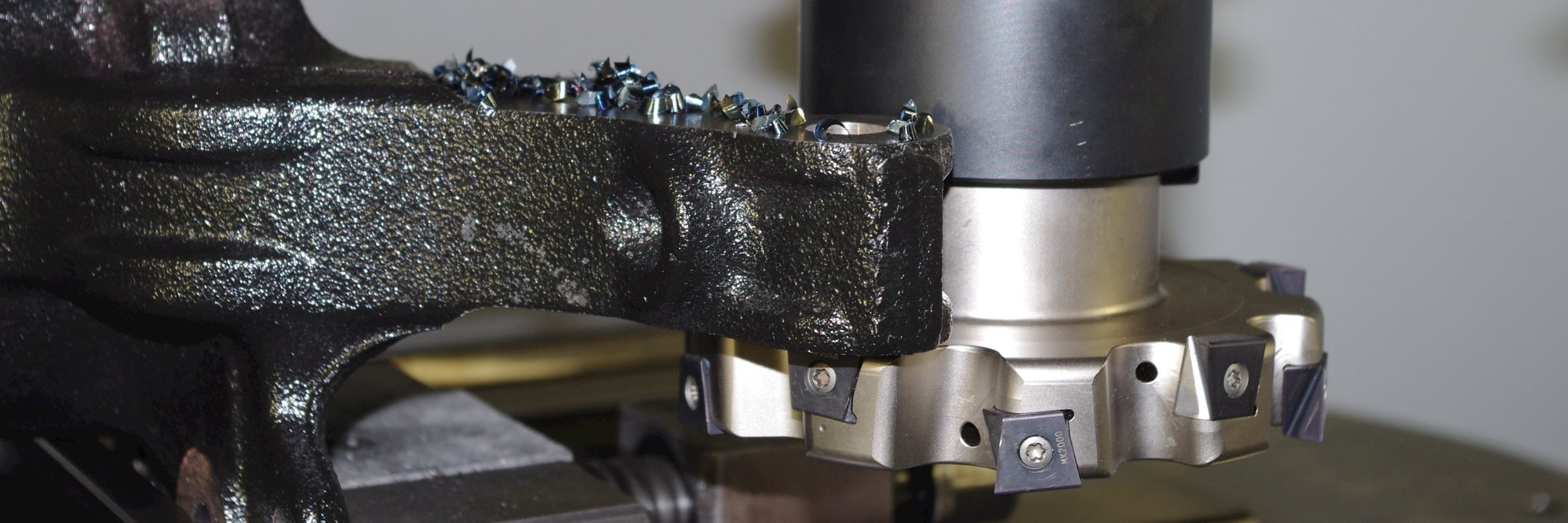
About Seco Tools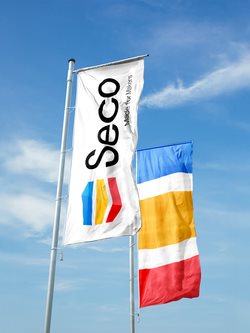
Standard Diamond Coated Drilling Solutions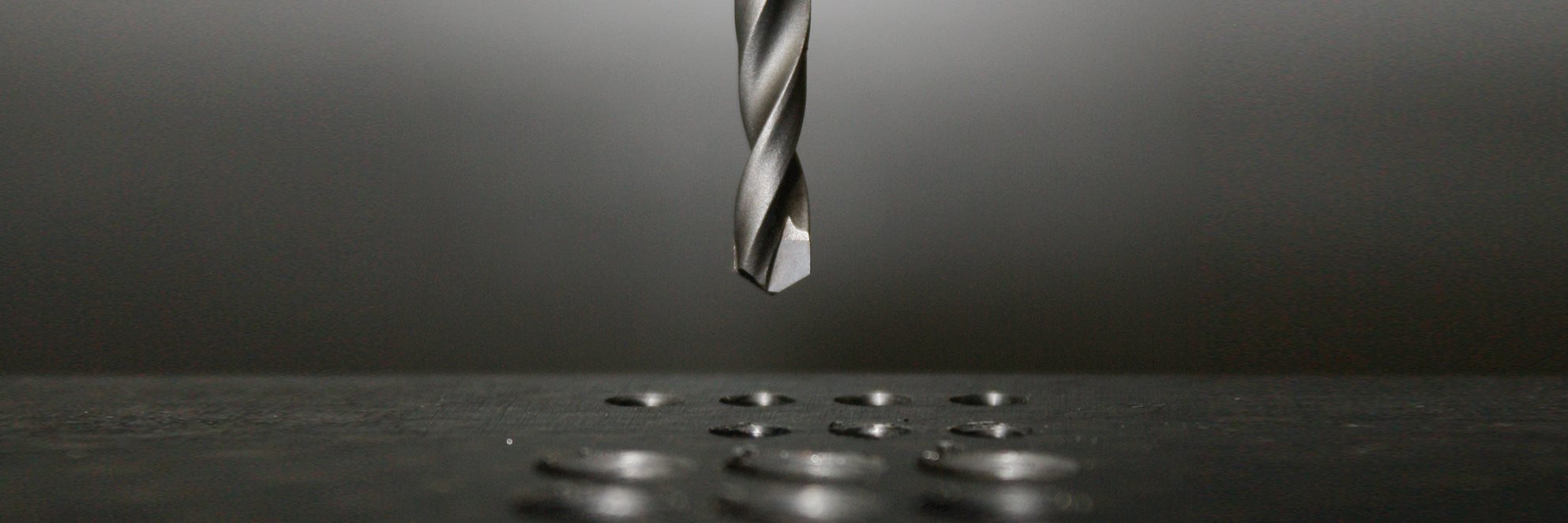
Seco Profile Milling Solutions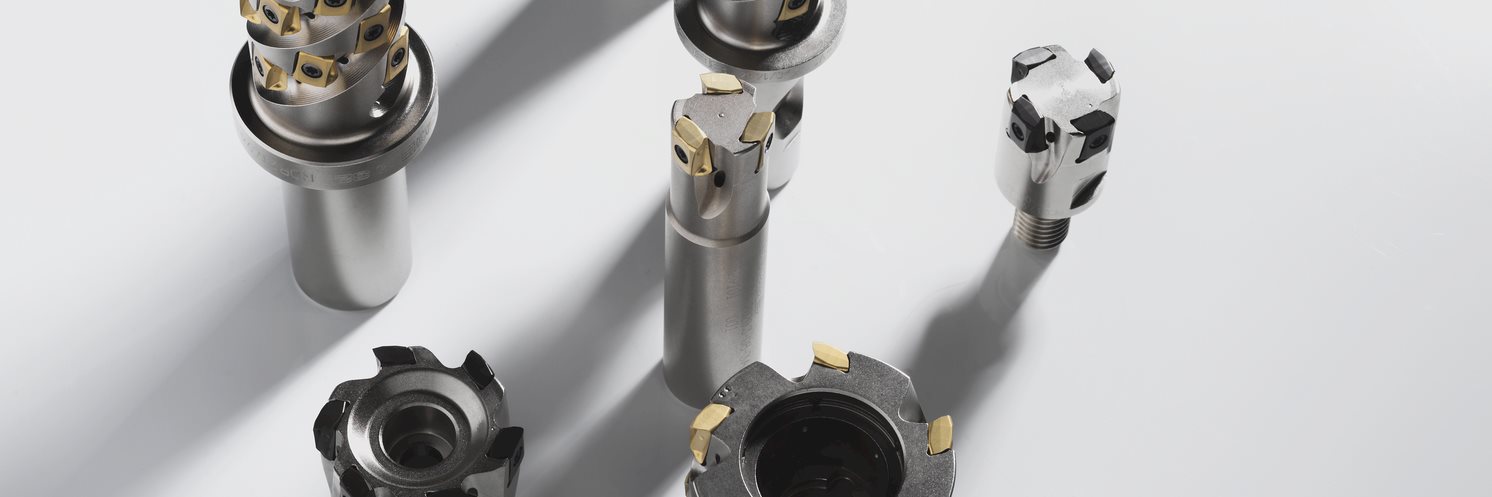
Jetstream Tooling® with MDT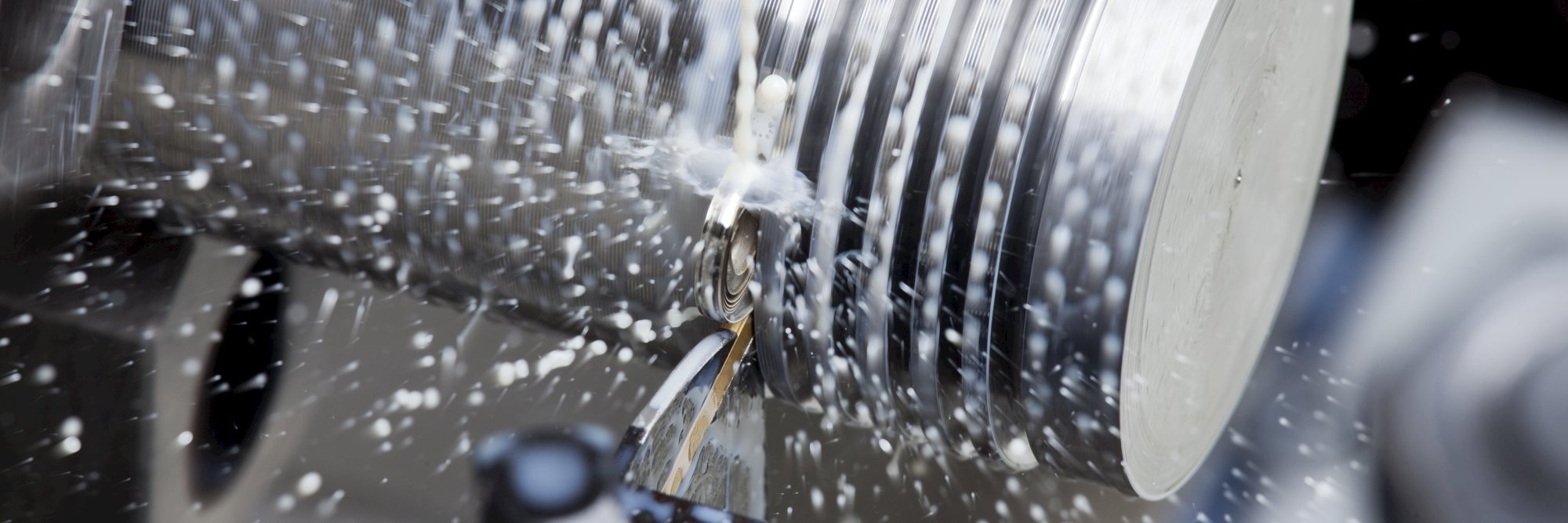
Threadmaster™ Thread Mills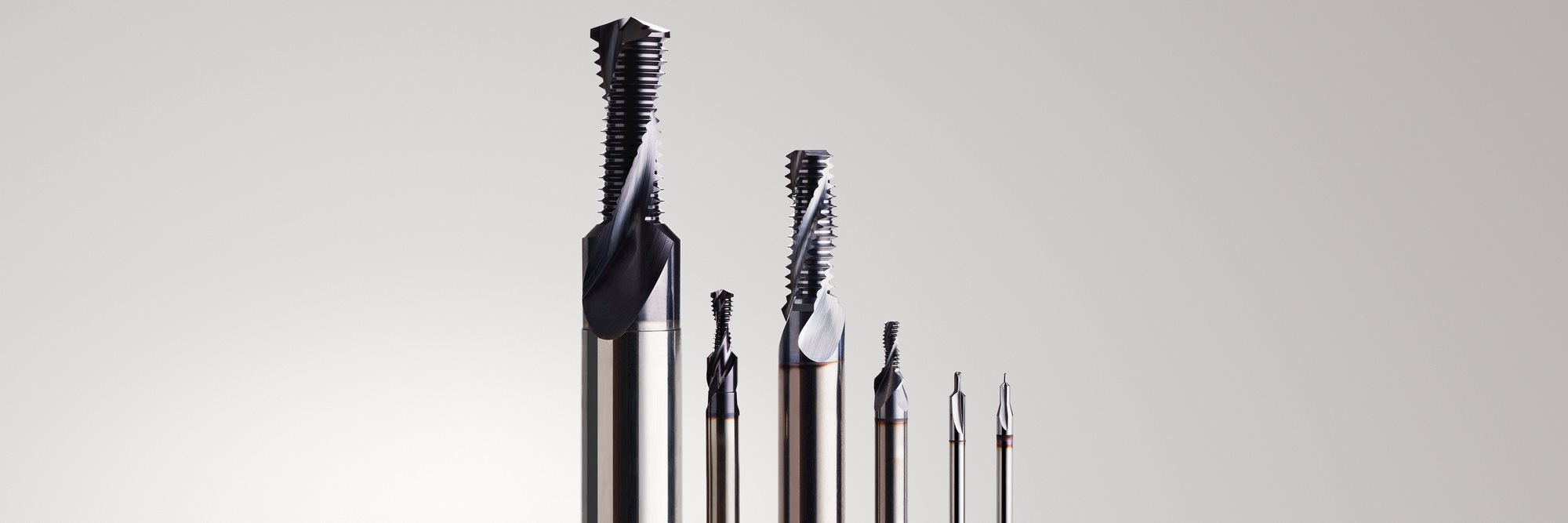
Jetstream Tooling® with MDT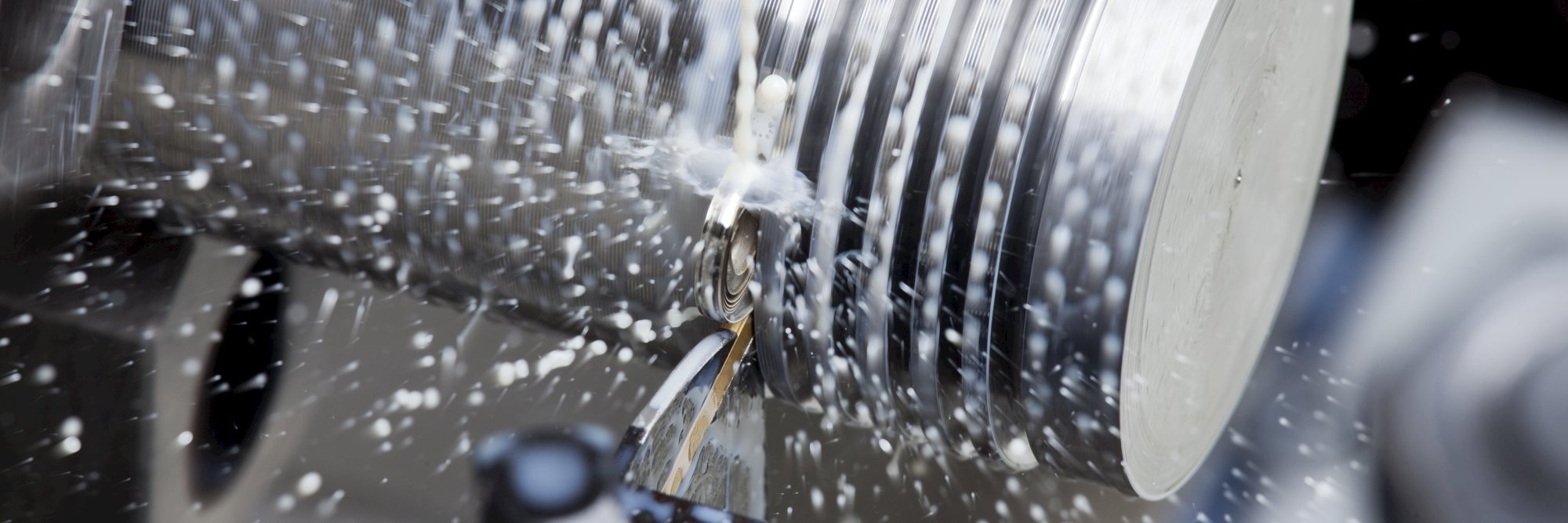
Seco Milling Solutions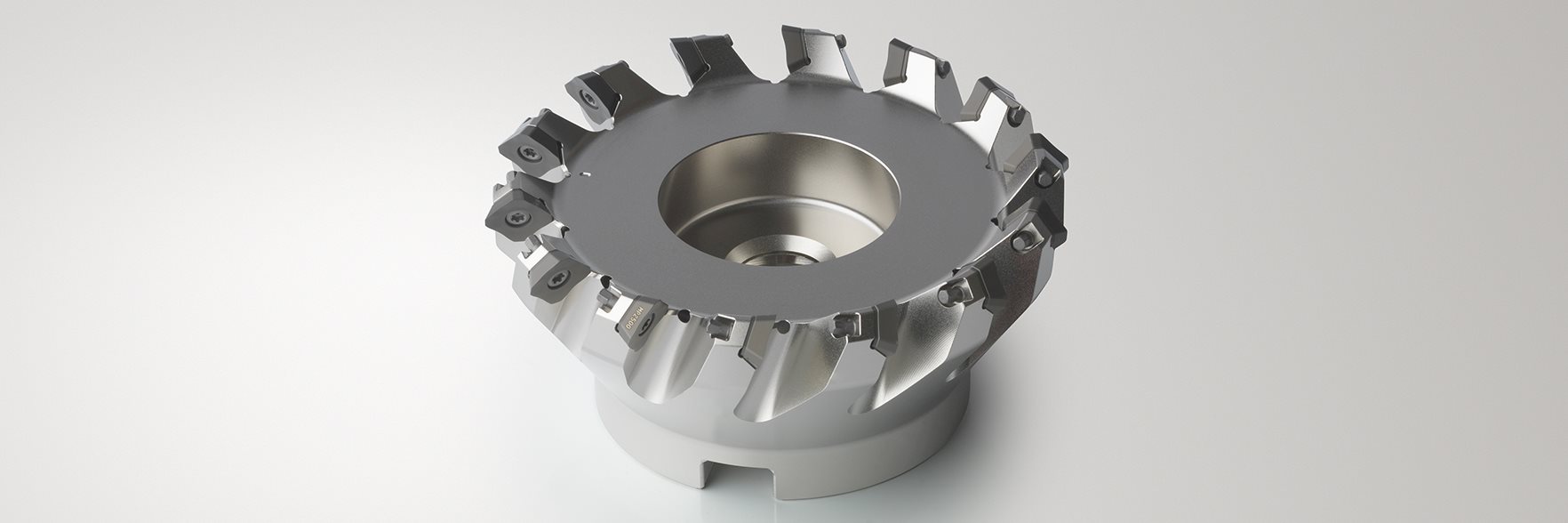
Seco Feedmax™ Solid Carbide Drills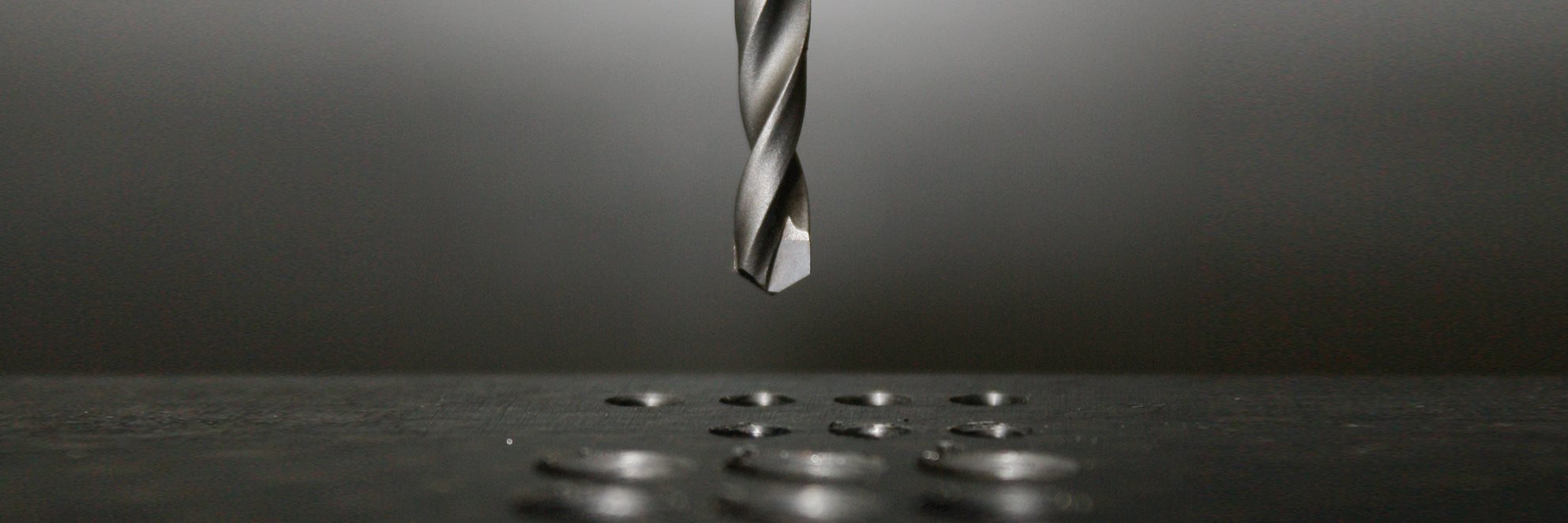
Secomax™ CBN170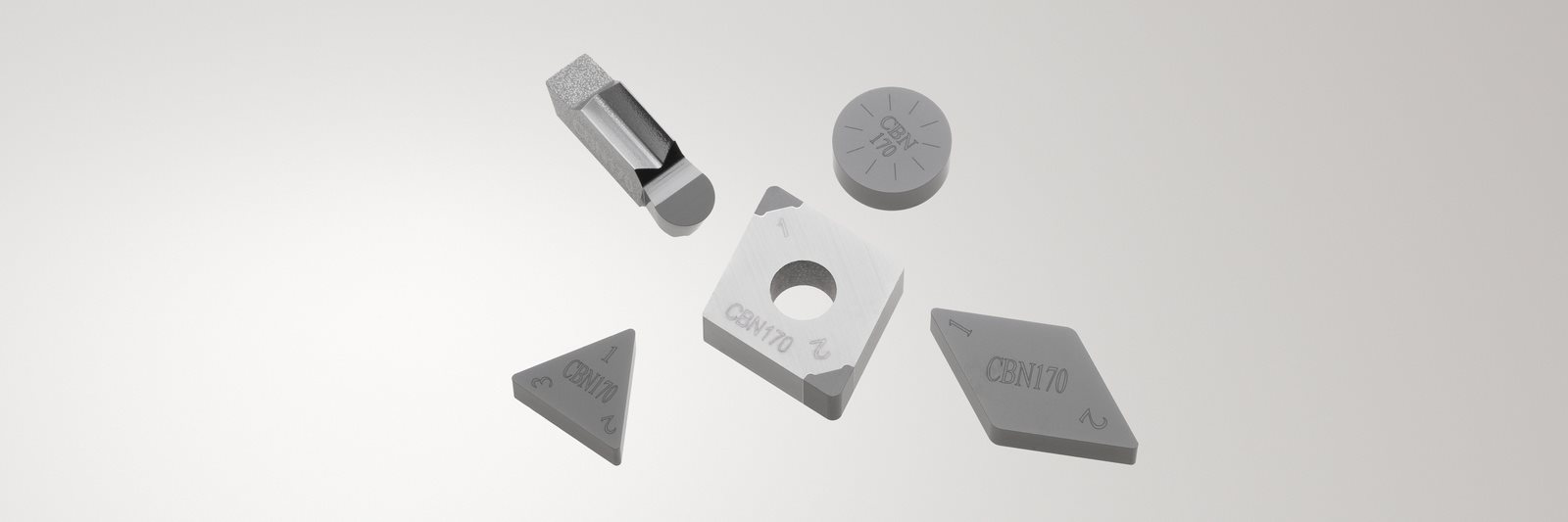
Seco Jabro Solid Carbide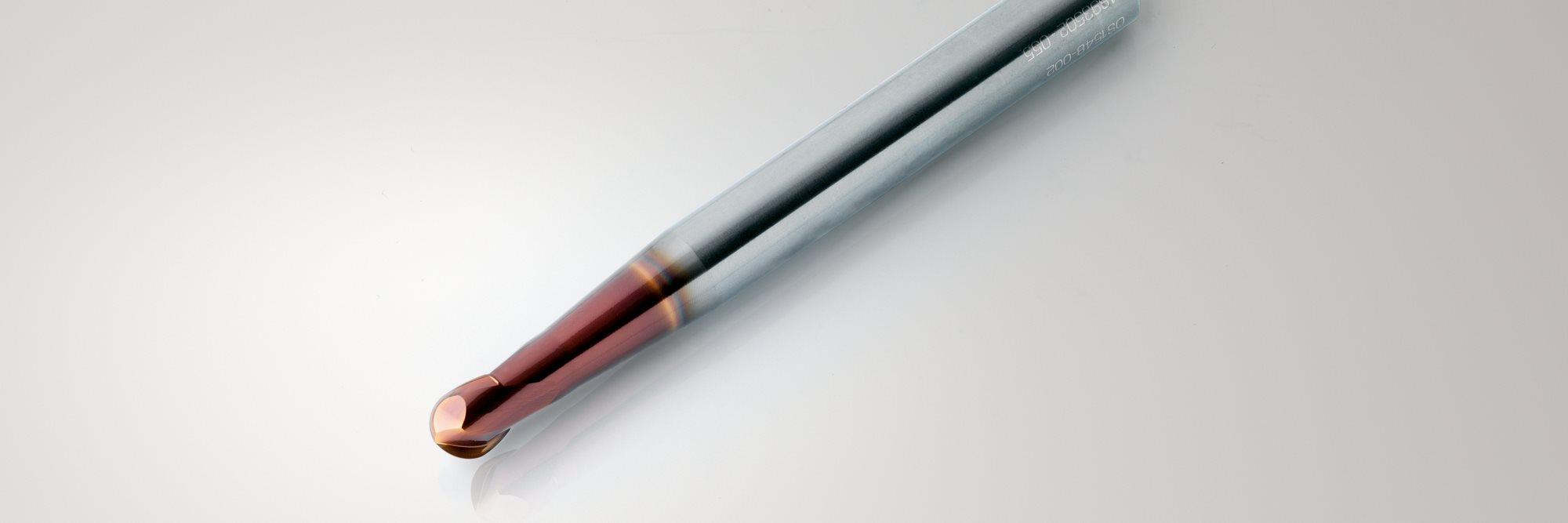