What is K material group?
Basic Cast Iron is an alloy consisting of iron and 5 main attendant elements Carbon, Silicon, Manganese, Phosphorus and Sulfur.Basic Cast Iron is an alloy consisting of iron and 5 main attendant elements Carbon, Silicon, Manganese, Phosphorus and Sulfur. The elements C, Si and Mn have got the most important influence on the Ultimate Tensile Strength (UTS or Rm) and Brinell hardness (HB). The higher the content of C and Si, the higher the values are of UTS and HB. Compared to steel, Cast Irons (CI) as a iso K material group has poorer strength and ductility. In many applications though, neither of these are the limiting factors when choosing material.
Basic advantages of Cast Iron:
- Low costs for long series
- Ability for near-net and complex shapes
- Good damping properties
- Abrasion resistance
Depending on microstructure, Cast Irons can be divided into sub-groups and this is normally done based on;
- Graphite shape:
- Flake (Lamellar)
- Vermicular (Compact)
- Malleable
- Nodular (Spheroidal)
In material standards all over the world the graphite shape is the prime dividing factor of the different Cast Iron types when considering the bulk of materials, but in some cases the matrix is being considered.
- Matrix type:
- Austenitic
- Martensitic
- Austempered
With its relatively low melting point, good fluidity, castability, excellent machinability, resistance to deformation and wear resistance, cast irons have become an engineering material with a wide range of applications and are used in
- pipes,
- machines and automotive industry parts such as,
- cylinder heads,
- cylinder blocks,
- gearbox cases,
It is resistant to damage by oxidation.
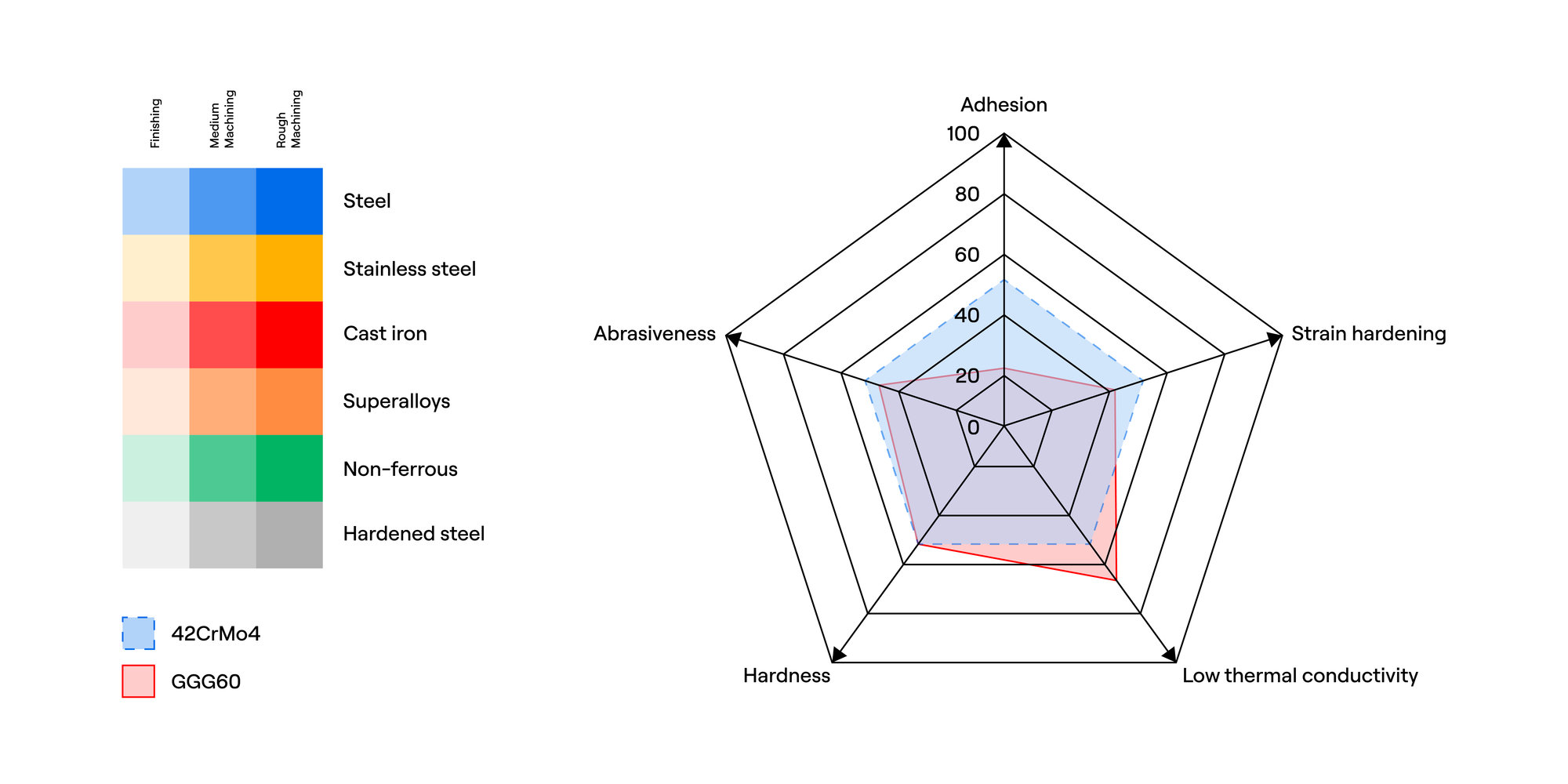
Seco classifies the machinability of materials based on 5 important properties: abrasiveness, ductility, strain hardening, thermal conductivity and hardness.
Do you want to know more about this material?
Discover our STEP program
You already have an application in mind for this material?
Find the right tool within a minute with Suggest!
Basic guidelines for machining ISO K materials, e.g. basic cast iron machining:
- High tribological loads are your main concern (leading to flank and crater wear)
- Use big depth of cut and high feed
- Use cutting speed to balance tool life with economic considerations on the process
- Use dedicated carbide grades (thick and wear resistant coatings) (for mass production PCBN cutting materials could be your best choice) and cutting edges with no chip breaking geometries are basic choice
- Dry cutting is possible but emulsion cooling should be used for health reasons (graphite dust)
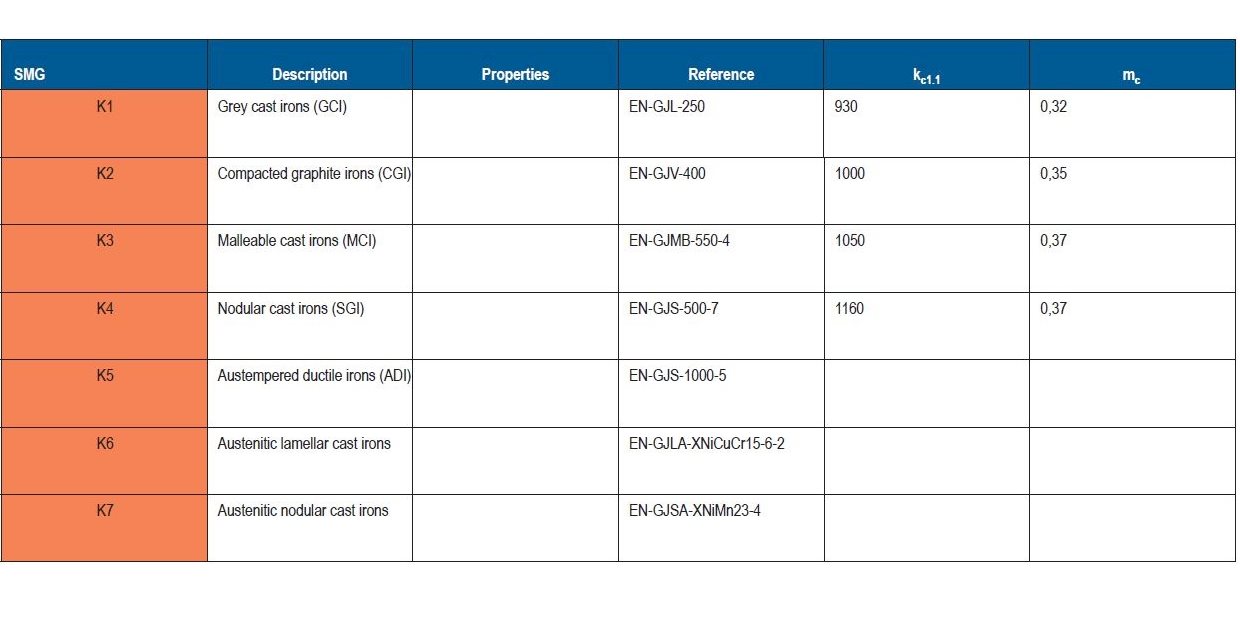
Inline Content - Survey
Current code - 5fce8e61489f3034e74adc64