Why the electrification of the car industry is causing a turbocharger boom
When all cars are electric they will not need turbochargers. For now, though, demand for this key component is booming, as automotive manufacturers seek to exploit one of the cheapest and most efficient ways of reducing carbon emissions.
Annual turbocharger production is currently at 47 million units and is growing by at least seven percent a year. According to Allied Research, the market will be worth as much $24bn in 2027, when production is expected to reach its peak.
"If you take the growth pattern of turbocharger manufacturing for the past two or three years, it is the only component that is seeing growth, and even double-digit growth," says Vidyadhar Kulkarni, Business Development Manager for Seco Tools' Asia-Pacific auto division.
According to Kulkarni, manufacturers are investing in adding turbochargers to ever more vehicles, as they seek to meet tightening fuel efficiency regulations.
The US Environmental Protection Agency is soon to re-introduce fuel economy standards rolled back by the Trump administration; the European Union is targeting a 15 percent reduction in fuel use between 2021 and 2025, and a 55 percent reduction by 2035; China is requiring a 6.5 percent annual improvement in fuel efficiency for new vehicles up until 2025, and thereafter 5.5 percent a year up until 2035.
"If we downsize the engine, with a turbocharger it can produce the same power as a big engine. At the same time, we are controlling CO2 emissions," Kulkarni explains.
A turbocharger can improve fuel efficiency by between 20 percent and 40 percent by using a car's exhaust gases to spin a turbine, which then pumps air into the engine's cylinders.
Turbochargers are expected to be fitted to 57 percent of new passenger cars produced worldwide in 2022.
Regions where few cars have turbochargers, such as South America and South Asia, are starting to catch up with the European Union, where they are already fitted to 74 percent of passenger vehicles.
In fact, Turbochargers are very often being fitted to hybrid vehicles, cementing the component’s place in the transition. Hybrid vehicles almost always have smaller engines than their pure petrol or diesel equivalents, with an electric motor and turbocharger together acting to compensate for the lower power.
Turbocharger technology is also developing rapidly, with increased use of integrated manifold, variable geometry, and dual volute designs, and new advanced alloys.
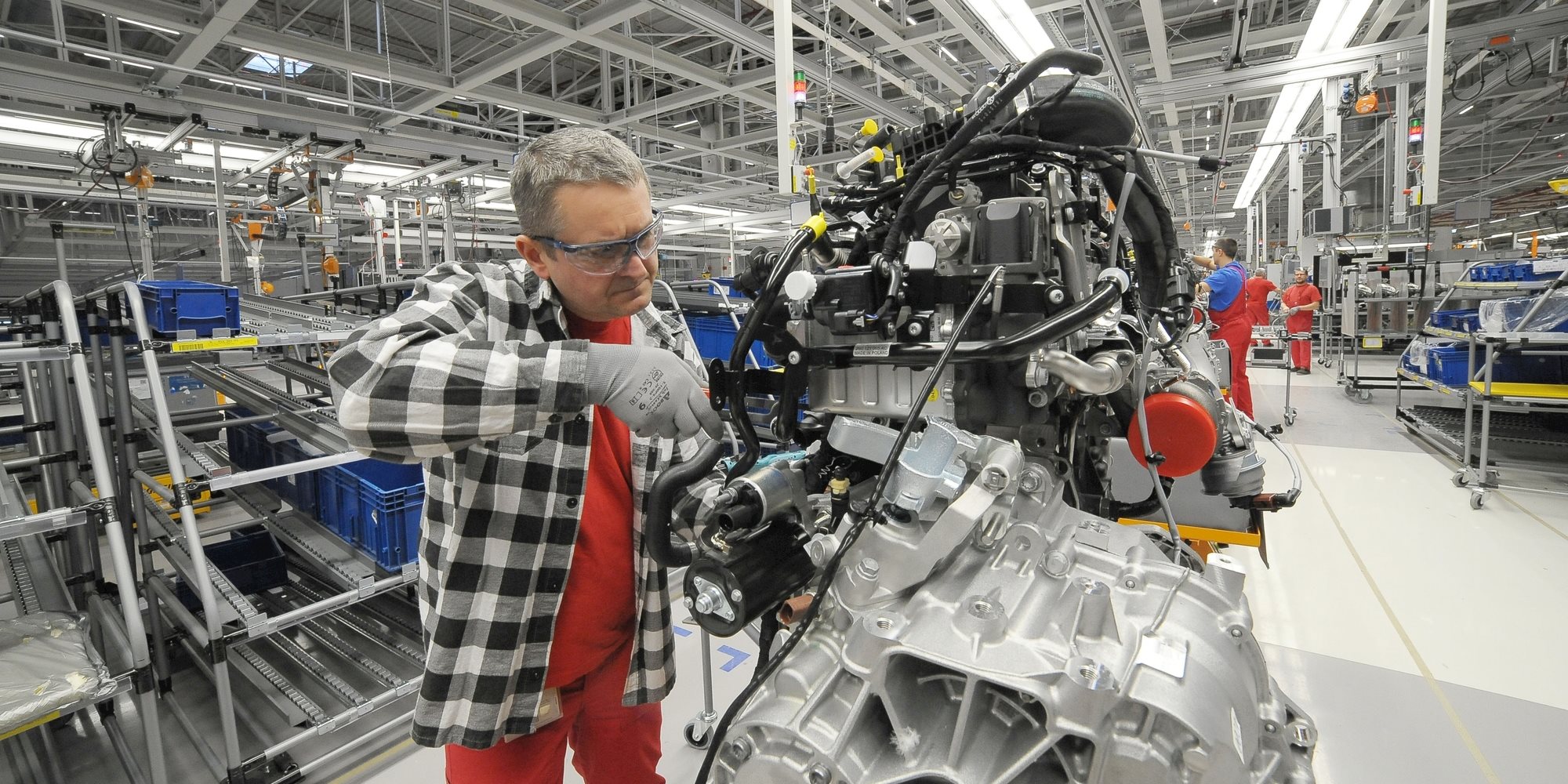
This is partly a result of the smaller size of more efficient modern engines, which produce a smaller volume of exhaust fumes to drive turbochargers, meaning the turbochargers themselves need to be more efficient. It is also partly because modern engines save fuel by shutting off some cylinders when not necessary.
Advanced alloys designed to withstand high temperatures and corrosive gases, are also often harder to tool.
Seco Tools is working at the R&D centres of some of the leading global turbocharger manufacturers, investigating the right tooling solutions for their latest designs.
Turbocharger manufacturers are expected to start to scale down research and development in the component from about 2025 in anticipation of a decline in demand. But this is by no means certain, Kulkarni a
Turbocharger componentrgues, given the slow progress in some regions towards building the necessary electrical charging infrastructure.
India, the largest manufacturer of two-wheeled vehicles in the world and the fifth largest producer of buses and trucks, is only aiming for 16 percent of two-wheelers to be electric by 2025, five percent of passenger cars, and 13 percent of buses and trucks.
"To have a full shift to battery vehicles requires tremendous infrastructure. The price of electric vehicles is a big point, and then there is the battery, which is today made from lithium, which has its own environmental challenges,” Kulkarni says of the shift. “We appreciate the move towards EV, but think it is valid to also consider the timing.”