Make better turbochargers faster with fewer tools
Find out how to cut turbocharger production costs with longer tool life, lower tool costs, fewer tools and setups, and high process reliability.Turbocharger manufacturers must speed production, lower part costs, and maintain geometry and surface finish. To succeed, they also must reduce setups and extend tool life.
Less-efficient cast iron and heat-resistant cast iron turbochargers suit older vehicles. Newer high-efficiency cars use cast stainless steel – and supercars rely on exotic alloys.
At every size, turbochargers include complex geometry. Tricky clampings affect machining strategies and production efficiency, especially with integrated manifolds. Turbochargers require large amounts of material removal, with face milling on 10%-15% of the surface.
To decrease costs and increase precision, turbocharger manufacturers strive for three setups, although some may use up to six. Versatile longer-reach tools can cut setups and larger tool magazines limit changeover times. In Turbocharger manufacturers also monitor tool life. Castings' tough skin increases tool wear, and cast iron itself is abrasive.
Seco solutions master turbocharger milling, turning and reaming. Double OctoMill™ boosts tool life and output quality. MDT addresses back-grooving, including behind flanges. Precimaster Plus offers exchangeable heads to cut costs over solid tooling. Wide-ranging options for all these tools match specific workflow needs.
With in-depth industry expertise, Seco acts as a trusted adviser to help customers find solutions and achieve success. Our high-quality tools offer proven ways to optimize processes and output.
Turbocharger manufacturers rely on expensive machine tools and custom fixturing to fulfill long contracts with automotive OEMs. These manufacturers face intense customer pressures to raise their output and lower their costs, despite the complex geometry and machining challenges of these parts. As a result, suppliers want to do more with less, from tooling to setups. The right tooling options can help overcome obstacles to yield faster, better production.
At the same time that turbocharger manufacturers cope with customer pressures on production speed and per-part costs, they also face increasing difficulties based on larger trends. Shortages of skilled workers force manufacturers to find ways to accommodate less-experienced operators while they maintain desired production efficiencies and part quality. Unattended production places increasing demands for automation-friendly workflows that can run with neither interruptions nor human supervision. Environmental considerations push toward more highly combustion-efficient designs, including twin scroll turbos, and to hybrid cars, leading to more-complex parts with greater machining challenges.
For today's internal-combustion vehicles, turbochargers fall into three categories. The least-efficient – and the largest – of these parts measure up to 50 cm, including an integrated manifold. Typically made from cast iron for older, less-powerful vehicles, these parts are exceptionally difficult to clamp because of their limited rigidity, which influences machining strategies and hinders efficient production.
The smallest turbochargers often eliminate the inlet manifold and measure only 16-18 cm, or slightly larger if they include additional features. To develop higher pressures for greater engine power and efficiency, newer vehicles use heat-resistant cast iron. Cast stainless steel offers the most heat resistance for high-efficiency vehicles, while supercars use exotic alloys that require a keenly selective approach to production.
Regional part designs vary from simple to detailed approaches to functionality. United States automakers tend to specify bigger, more-robust turbochargers with fewer part details, and still rely on heat-resistant cast iron. Outside the U.S., most automakers use cast stainless steel. European designs increase turbocharger efficiency and reduce size to achieve greater efficiency. Asian automakers create compact designs that target easier machining for lower-horsepower vehicles.
Automotive OEMs continue to develop new turbocharger materials to target lighter weight, greater strength and lower material cost. To achieve these efficiencies, OEMs must alter material cross sections. Many of these developments parallel those in the aerospace industry, and some of the metallurgy moves away from ISO materials and high nickel content. Unfortunately, although these aspects of material science can improve turbocharger performance, they also typically increase machining difficulty rather than reduce it. Regardless of part material selections, however, every turbocharger manufacturer must choose tool geometries and grades to match material needs, which can increase tooling costs by up to 40%.
Turbocharger production may strive for a single-setup approach, but that level of efficiency is all but impossible to achieve. Obviously, many suppliers try to reduce the number of setups to speed the process and reduce its cost, but this approach relies more and more on special tools. On average, efficiency measures bring the total down to three setups for a completely finalized part on a 4-axis or 5-axis machine – or up to six if the manufacturer pre-machines on multiple machine tools. All of these processes involve custom-made fixturing. Turbocharger manufacturers create some of their fixturing through their machine-tool OEMs, but they develop and produce up to 70% of it on site in extreme secrecy.
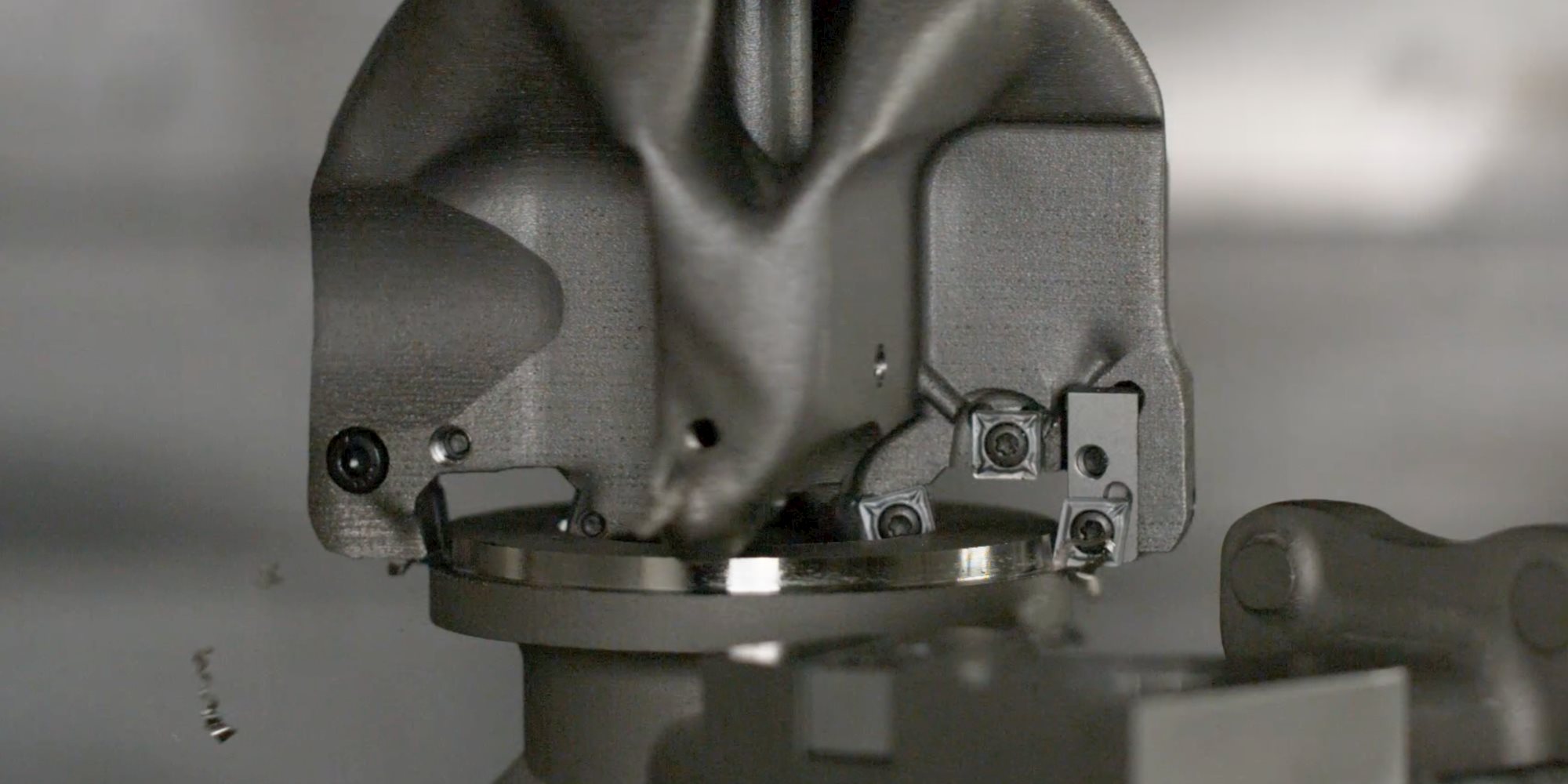
Tooling can help reduce setups with longer reaches to access internal features, and custom tools designed specifically to produce the part with fewer tools for increased productivity. Some production lines use dual-spindle machine tools that can produce two turbochargers at the same time with dynamic cutting interaction, or tombstone-mounted workpieces to build four to eight parts with one spindle. Larger tool magazines also streamline tool loading with special toolsets that use fewer roughing tools to achieve close to a net part shape. Typical cycle times range between four and 12 minutes per setup, for a total of approximately 20 minutes in a three-setup process.
Of course, speed means nothing if it comes at the expense of precision. Some portions of turbocharger exteriors require only sandblasting to remove the outer skin that results from casting. Nonetheless, many areas of the part – especially seating and flanges – demand close adherence to tight tolerances.
To build these complex parts, manufacturers use a combination of stock and custom tools, the latter built to match exceedingly specific feature requirements. Some manufacturers rely on solid grooving tools or profiling options to achieve tolerances on flanges – all of which must be machined – and seating. Some use U-axis dynamic interpolation turning to create flange details, with tool edges continuously in the cut to apply a turning process on a milling machine. In turn, this reduces cutting speeds because of the complex freeform shapes of the part. Dynamic interpolation also heightens the pressure to choose tool grades and geometry for process security.
Flanges pose some of the greatest challenges of this application because of variances in cast workpieces and cutting conditions, long intervals in the cut, and adverse entry and exit points. Grooving operations, including back-facing grooves behind flanges, also demand extreme precision in areas surrounded with other part features. The v-band profile demands the highest tolerances of all, which many manufacturers approach with form tools because of the limits of copy turning.
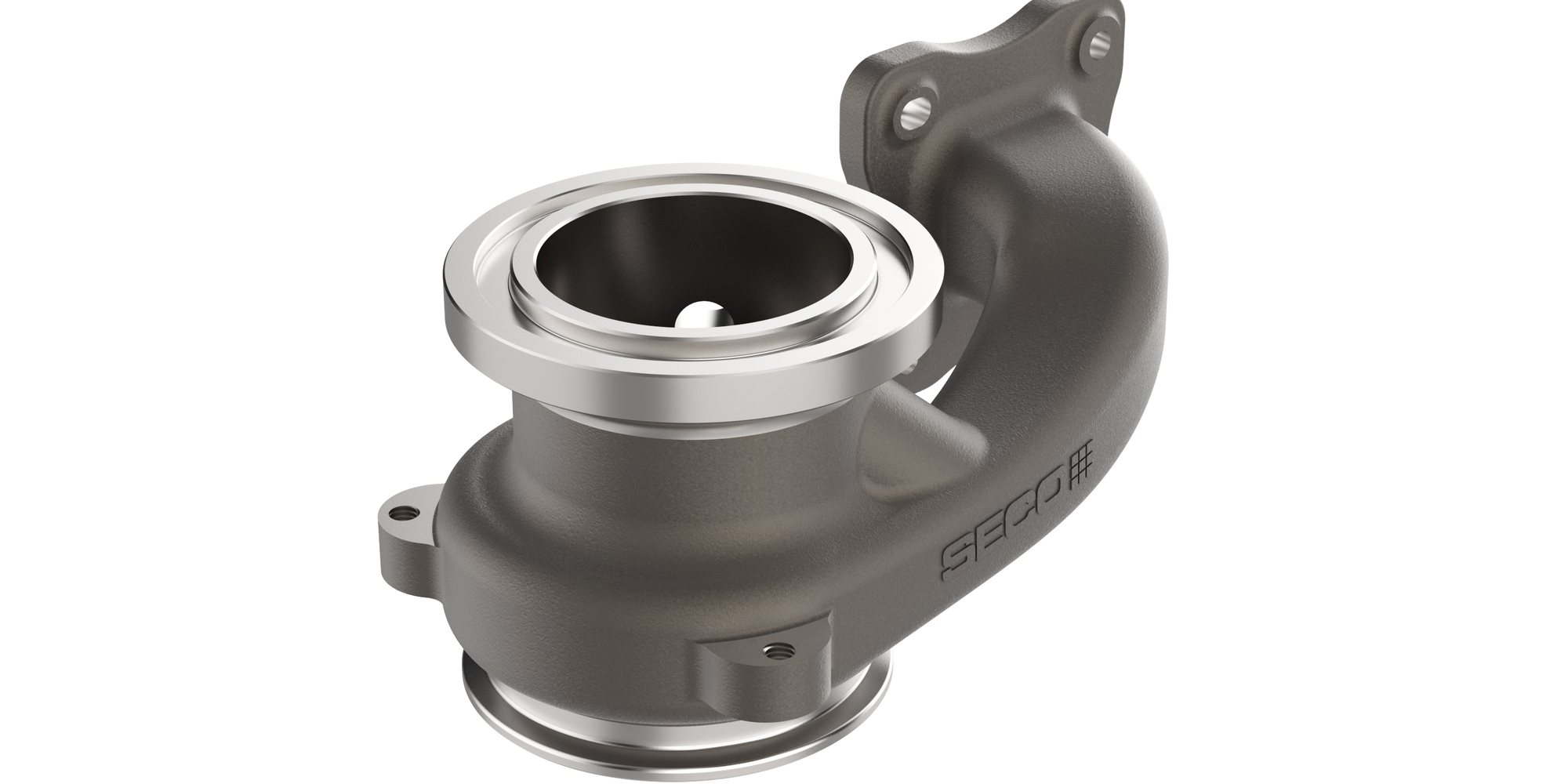
For many reasons, tool wear quickly becomes problematic in turbocharger production. Workpieces originate as castings, which develop a tough outer skin as a byproduct of the process. All heat-resistant materials become difficult to machine, including cast iron because of its abrasive nature. With 40%-50% of part surface area to machine, turbochargers require high material removal rates. As materials become harder and tougher, tool life drops and tool costs rise, especially on cast stainless steel.
In fact, tool costs lead turbocharger manufacturers' concerns in seeking greater application efficiency, even more so than tolerances and surface requirements. Setup reduction also dominates the list, as manufacturers search for versatile tools that can perform more than one operation. Surface finishes can prove difficult to achieve because of demanding specifications and the need to minimize burrs. Chip control also becomes essential, with short chips in cast iron and long ones in cast stainless steel.
As much as 10%-15% of the turbocharger surface requires face milling cutters to meet part specifications. Features such as the wastegate and wastegate flap also require spot facing. Chip control can be critical to avoiding adhesion marks on the top surface of the part. To maximize process reliability and uninterrupted machining, increase tool life and output quality, manufacturers need a tool family with a wide range of insert geometries and grades. The Seco Double OctoMill™ series meets these criteria for optimal performance. With 16 edges, these tools reduce cost per edge.
Double OctoMill™ maximizes process reliability for uninterrupted face milling operations. With 10%-15% of the surface to mill, this family's wide range of insert geometries and grades increases tool life and output quality.
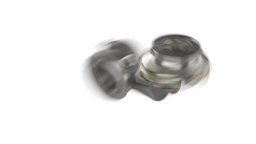
Many surfaces that require turning lie in the center of the housing, which demands tight control of chip size to avoid small chips that can get stuck in part channels or larger ones that can clog the part. Groove machining and small grooving on the v band turbine housing also add complexity, with back-facing grooves behind the flange that must be machined in the opposite direction. These operations require grooving inserts with stability, performance safety and secure clamping. The Seco MDT (Multi-Directional Turning and Grooving) series incorporates Secoloc™ clamping to stabilize performance and safety. Longer tool reaches assist in reducing setups and tool-stock requirements.
MDT (Multi-Directional Turning and Grooving) tackles back-grooving the complex v-shape, including behind flanges. Unique Secoloc™ clamping stabilizes performance and safety while longer reaches reduce setups and tool stock.
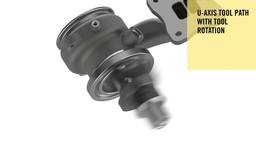
After square-shoulder milling, facing and drilling, the steering flaps and control bolt require reaming to complete these features. Reamers with exchangeable heads in multiple lead, geometry and grade options offer cost-saving advantages over solid reamers in these instances.
The Seco Precimaster Plus series provides the versatility and flexibility to accomplish these tasks efficiently and cost effectively. Precimaster Plus handles reaming duties with exchangeable heads that lower tooling costs over solid reamers. Multiple lead, geometry and head-grade options optimize performance.
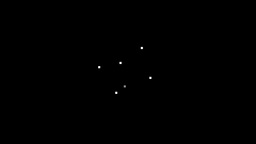
Although most turbocharger manufacturers use similar setups and machines, their approaches to strategy, fixturing, operation sequencing and tooling can vary. In these areas of the production process, a tooling manufacturer can serve as a trusted partner, offering strategic advice based on long experience of the part, material and industry challenges involved.
Grooving, valve seat turning, bearing seats, recessed housings on differentials, undercut coolant channels, track rods, external/internal contour turning: The production process spans numerous complex operations, all further complicated through the clamping difficulties inherent in complex part geometry. With dedicated insert geometries and grades, expertly developed custom tooling and decades of expertise to back up strategic recommendations, Seco Tools offers turbocharger manufacturers the options they need for efficiency and success.
If you would like to reach out to one of our automotive experts please contact us here
GET ALL NEWS, TRENDS AND STORIES AROUND THE AUTOMOTIVE INDUSTRY
SUBSCRIBE TO THE LATEST NEWS