Crankshaft
As one of the most challenging engine components, a crankshaft involves multiple production processes using complex custom tooling. Critical to translating reciprocating linear piston motion into rotation, crankshafts demand the highest possible quality control and exacting tolerances.
YOUR MANUFACTURING CHALLENGES
- Cost effectively drilling numerous holes requiring a chamfer.
- Producing numerous holes with minimal tool cost per piece.
- Reaming precise holes with perfect surface finishes.
- Drilling numerous holes with low cycle times, high quality and reliability.
- Machining irregular stock, cast skin and impure surfaces efficiently and reliably.
- Efficiently turning and broaching irregular stock, interrupted cuts and impure surfaces.
- Productively machining the pins despite irregular stock and impure surfaces.
- Cost effectively drilling numerous holes requiring a chamfer.
- Maintaining productivity and reliability while face milling irregular stock, cast skin and impure surfaces.
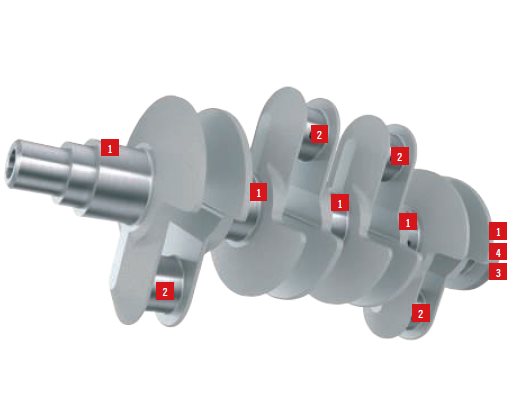
| 1 - Turning and broaching irregular stock |
Your Challenge: | | Efficiently turning and broaching irregular stock, interrupted cuts and impure surfaces. |
Our Solution: | | By incorporating various turning cartridges, the custom turn broaching disc can perform a variety of turning and grooving operations, from roughing with interruptions to finishing. Using standard, thick inserts in cartridges protected by carbide anvils, the tool offers high process stability and exceptional reliability. Your benefits include a cost-effective, flexible solution with limited machine tool investment. |
Product: | | Turn Broaching Disc |
| 2 - Machining the pins despite irregular stock |
Your Challenge: | | Productively machining the pins despite irregular stock and impure surfaces. |
Our Solution: | | Offering a safe and reliable process for machining the pin, this cutter provides a long cutting arc that makes contact with the workpiece materials to optimize performance. The custom tool’s profile can be suited to various bearing profiles for different crankshaft designs and maintains tight tolerances in hardened steel. Use of thick Duratomic® inserts allows high feed rates to be reliably applied. Your benefits include a stable process for a challenging application. |
Product: | | Internal Milling Cutter |
3 - Drilling numerous holes
Your Challenge: | | Cost effectively drilling numerous holes requiring a chamfer. |
Our Solution: | | By offering the ability to chamfer a hole by plunging after drilling, the custom PerfomaxTM Chamfer Drill combines operations to increase productivity. A unique flute design optimizes chip removal, and the use of Perfomax drilling inserts allows for a very cost-effective process. Your benefits include reducing costs while maintaining high process stability. |
Product: | | PerfomaxTM Chamfer Drill |
4 - Face milling irregular stock, cast skin and impure surfaces
Your Challenge: | | Maintaining productivity and reliability while face milling irregular stock, cast skin and impure surfaces. |
Our Solution: | | With sixteen cutting edges per indexable insert, Double Octomill significantly reduces the cost of obtaining high quality results. The tool provides superb surface finishes with maximum security, achieves tremendous cutter body life and can be used for both roughing and finishing. Your benefits include cost reduction while maintaining top performance. |
Product: | | Double Octomill Face Milling Cutter |
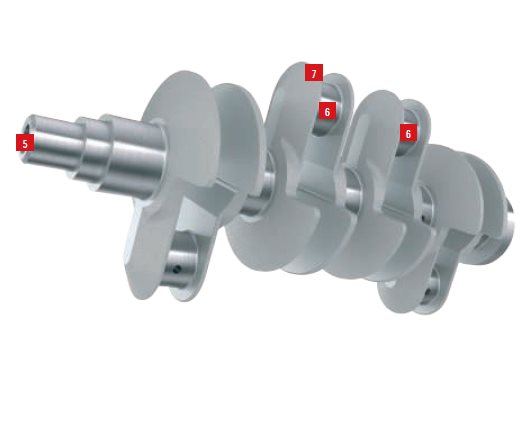
5 - Drilling numerous holes
Your Challenge: | | Cost effectively drilling numerous holes requiring a chamfer. |
Our Solution: | | This custom tool incorporates turning inserts with a Crownloc drill to combine drilling and chamfering into a single operation. Crownloc drills use exchangeable heads with a strong locking system to avoid deflection and provide high chip removal rates. This approach eliminates regrinding costs and increases flexibility by allowing appropriate drill geometries to quickly and easily be applied to different applications. Your benefits include reducing tool inventory and increasing production efficiency. |
Product: | | Crownloc® Spot Face and Chamfer Drill |
5 - Producing numerous holes
Your Challenge: | | Producing numerous holes with minimal tool cost per piece. |
Our Solution: | | Crownloc drills use exchangeable heads with a strong locking system to avoid deflection and provide high chip removal rates. This approach eliminates regrinding costs and increases flexibility by allowing appropriate drill geometries to quickly and easily be applied to different applications. Your benefits include reducing tool inventory and increasing production efficiency. |
Product: | | Crownloc® Drill |
Your Challenge: | | Reaming precise holes with perfect surface finishes. |
Our Solution: | | An interchangeable head reamer, Precimaster™ Plus minimizes cost per hole while providing excellent results. Additionally, our Nanofix™, Precifix™ and Xfix™ lines fill out our range of reaming products, guaranteeing a productive and high quality solution for holes ranging from 2.97 mm to 155 mm in diameter. Your benefits include reducing costs while maintaining exacting tolerances and surface finish requirements. |
Product: | | Seco Reaming Solutions |
6 - Drilling numerous holes
Your Challenge: | | Drilling numerous holes with low cycle times, high quality and reliability. |
Our Solution: | | Providing high performance when dealing with angled exits or intersecting holes, the Seco Feedmax Chamfer Drill utilises the light-cutting geometry and a special edge preparation to increase process security and tool life. The tool also incorporates a low-friction coating, and uses four land margins to increase stability. Your benefits include maintaining productivity in challenging, high-tolerance holes. |
Product: | | Seco FeedmaxTM Chamfer Drill |
7 - Machining irregular stock, cast skin and impure surfaces
Your Challenge: | | Machining irregular stock, cast skin and impure surfaces efficiently and reliably. |
Our Solution: | | This unique cutter offers a profile that mills the bearing surface and two under cuts, and can be adjusted to suit various profiles for differing crankshaft designs. Thick inserts achieve reliable performance with high feed rates, and the tool provides excellent chip evacuation and material removal rates. Your benefits include dramatic reductions to cycle time with a highly secure and safe process. |
Product: | | Pin Milling Cutter |
HOMERelated content
Case Studies: Crankshaft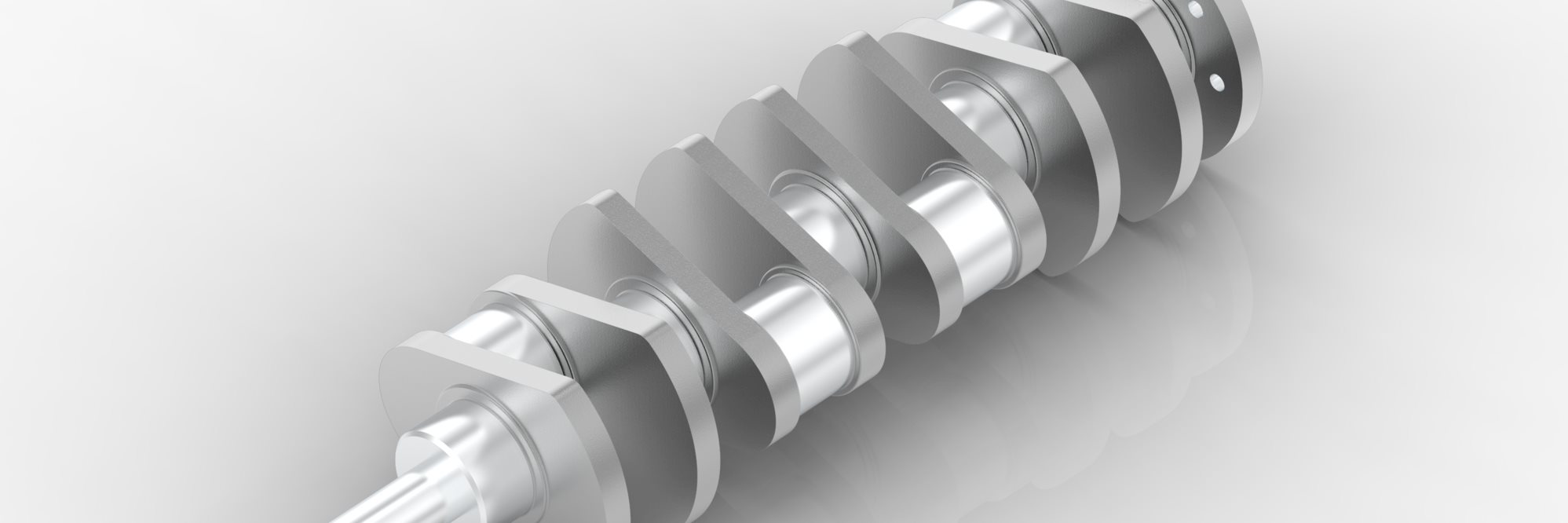
Video: Crankshaft machining with long drills | Seco Tools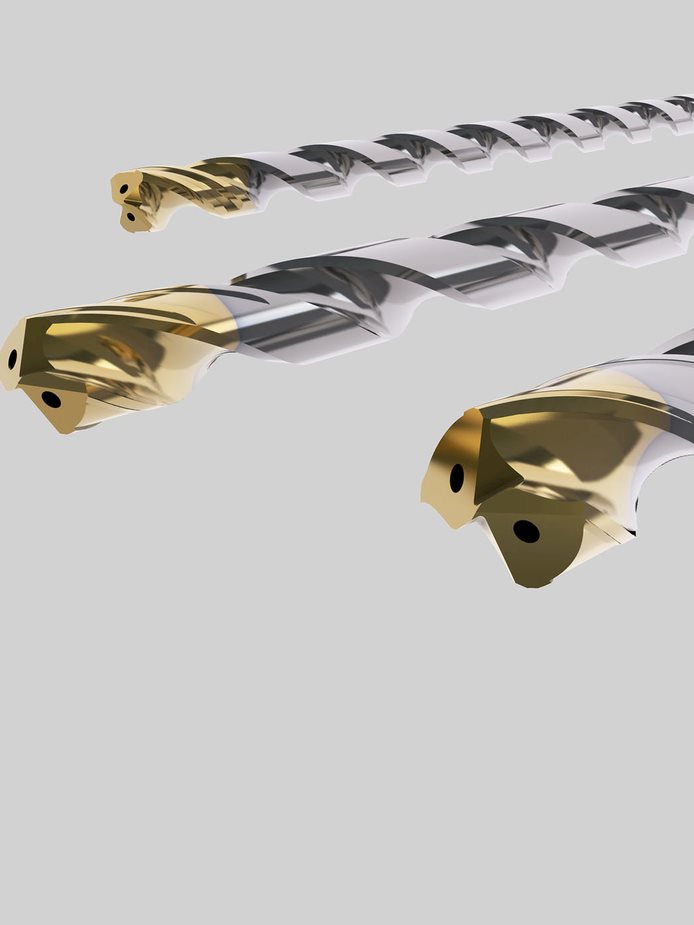
Gearing up for the win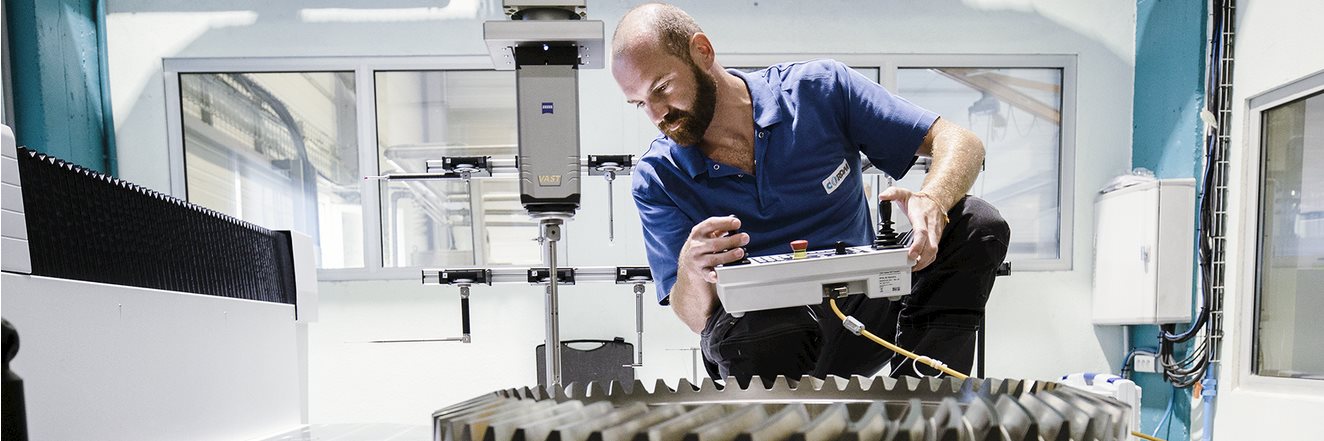
Component Engineered Tooling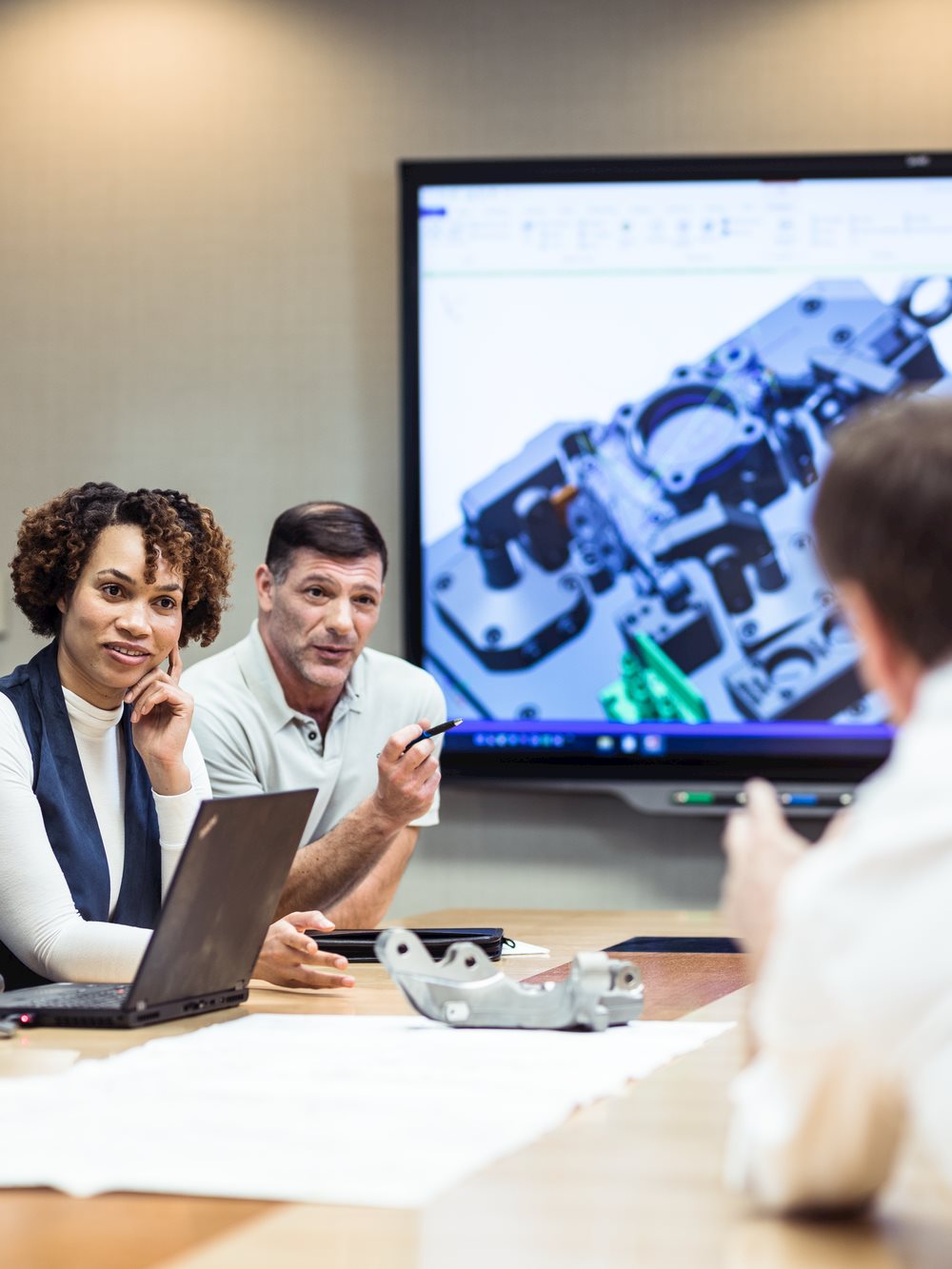
Video: Boosting Gear Production: Custom Hob Cuts Time & Increases Efficiency | Seco tools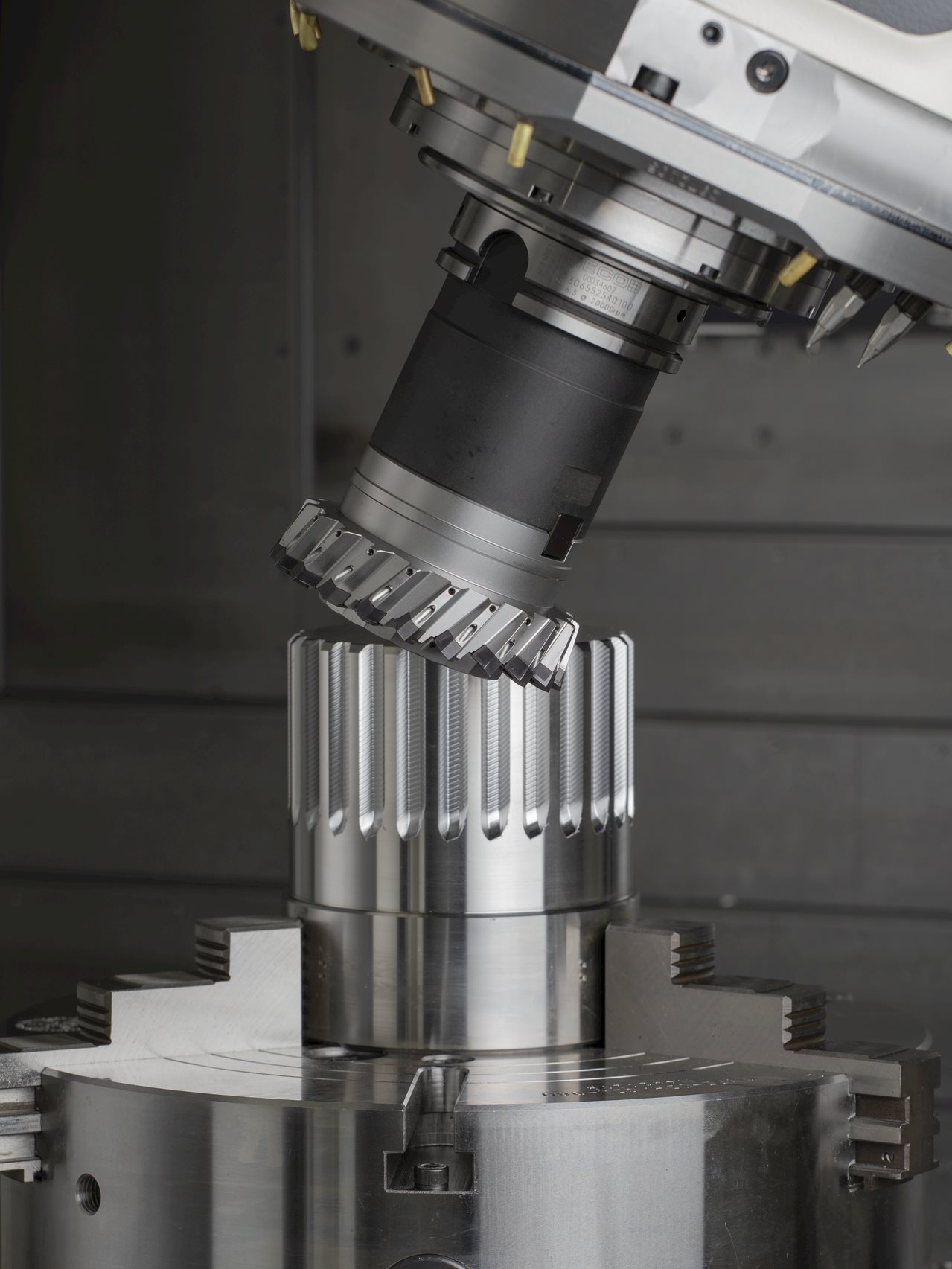
Turbocharger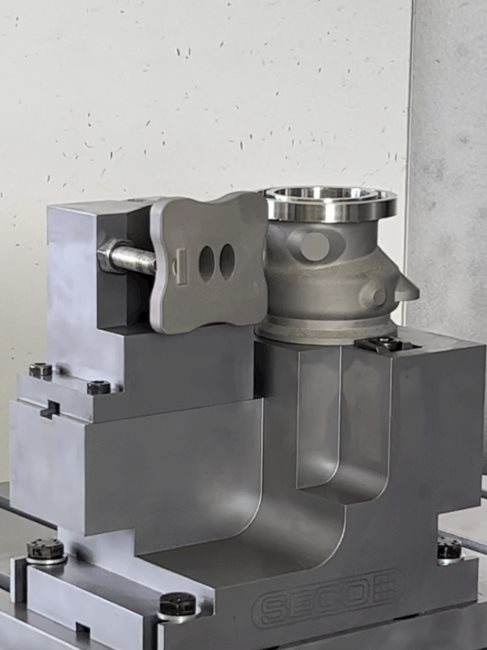
Truck Engine Block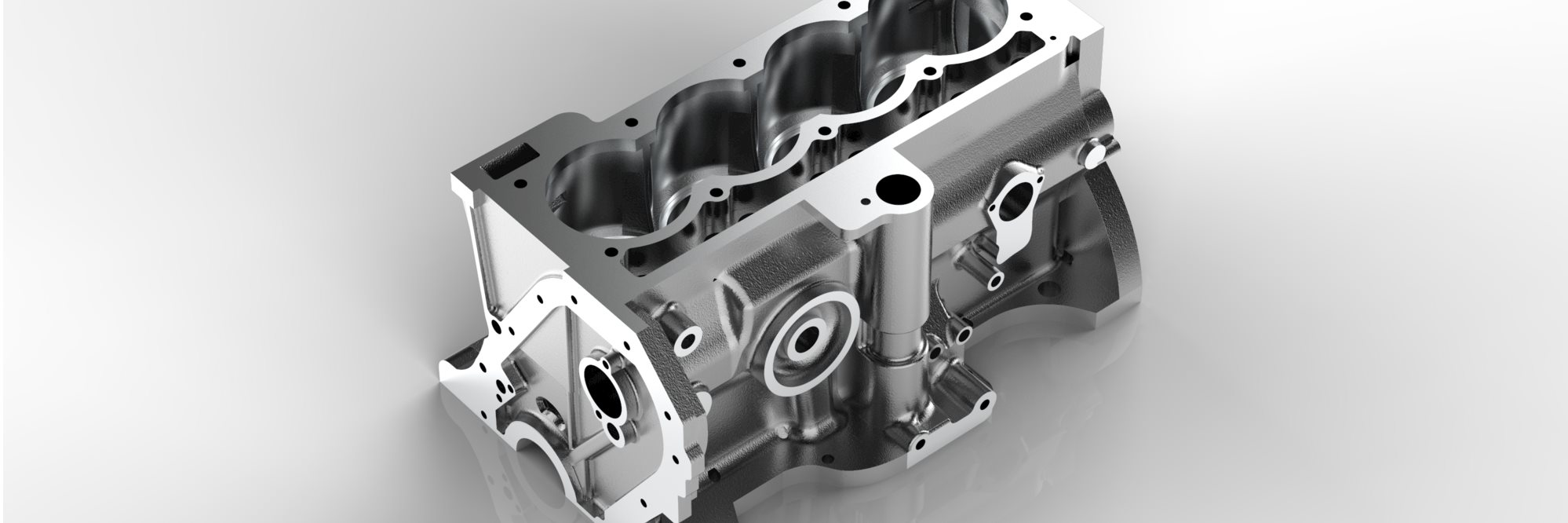
Video: 5 solutions to the main engine block challenges | Seco Tools
Custom Products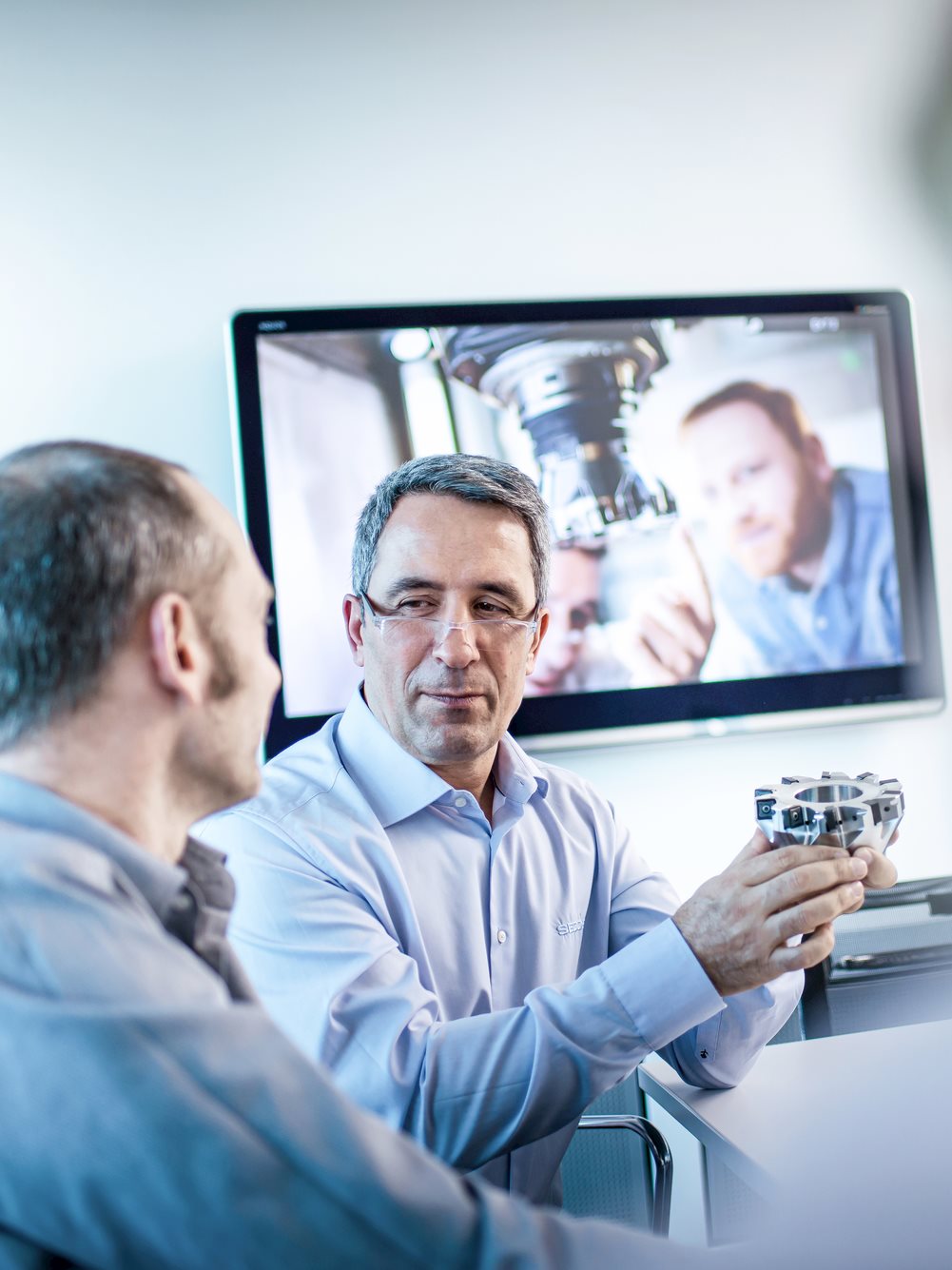
Piston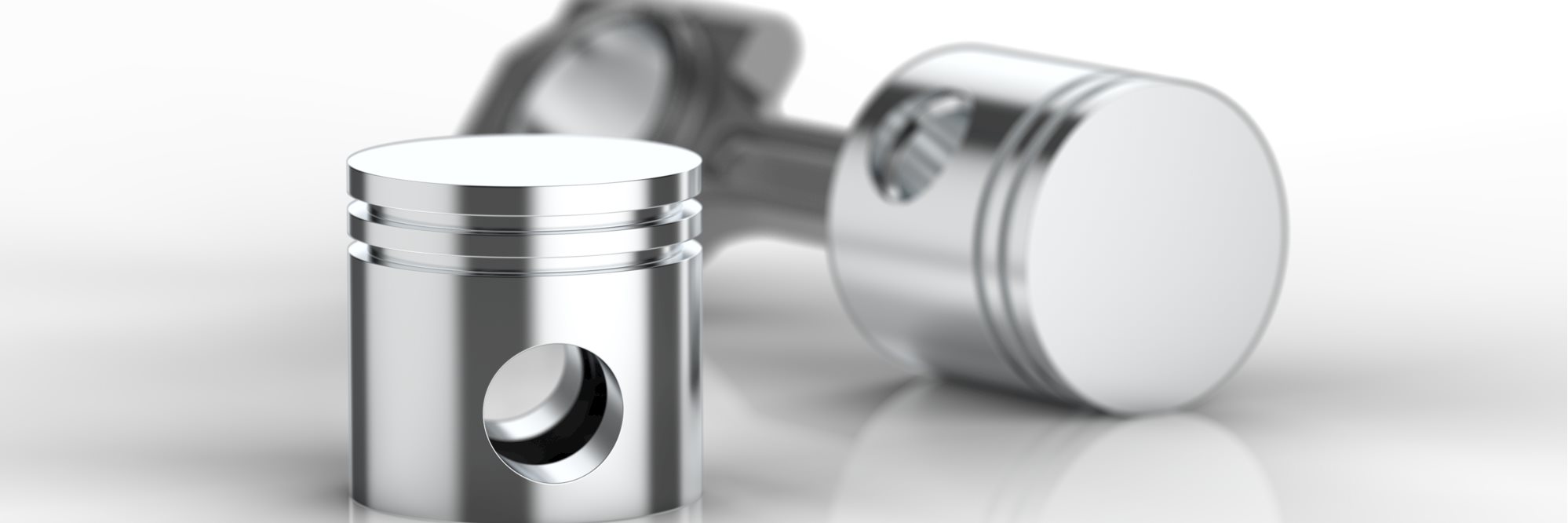
Cylinder Head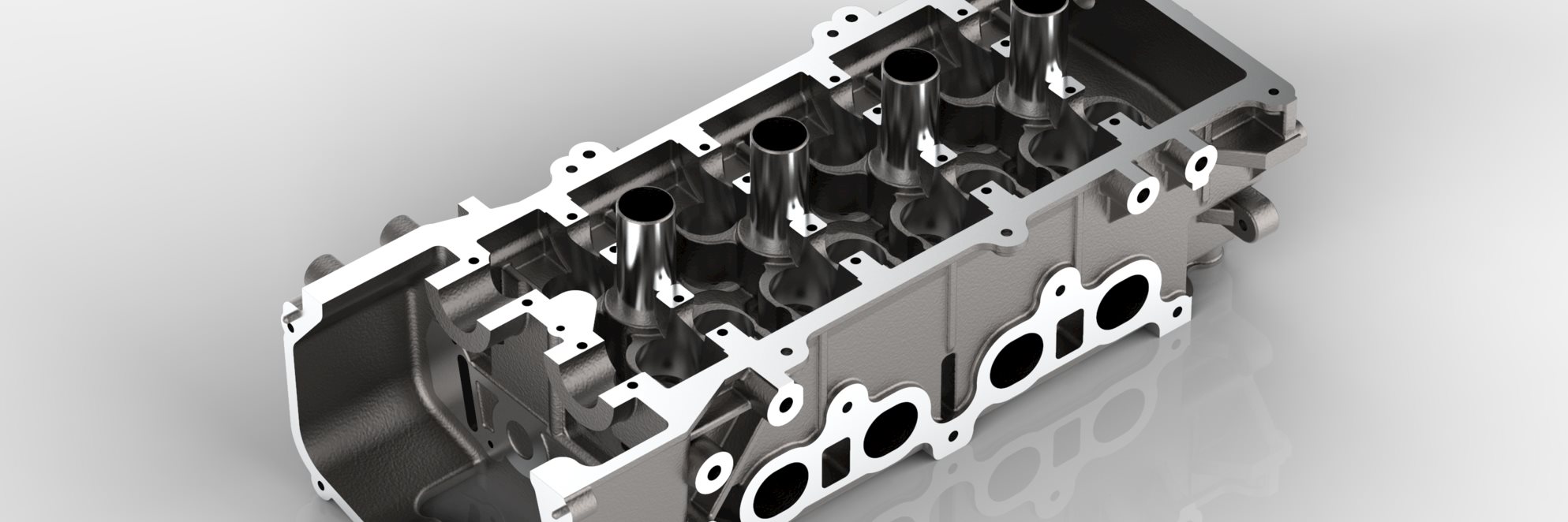
Connecting Rod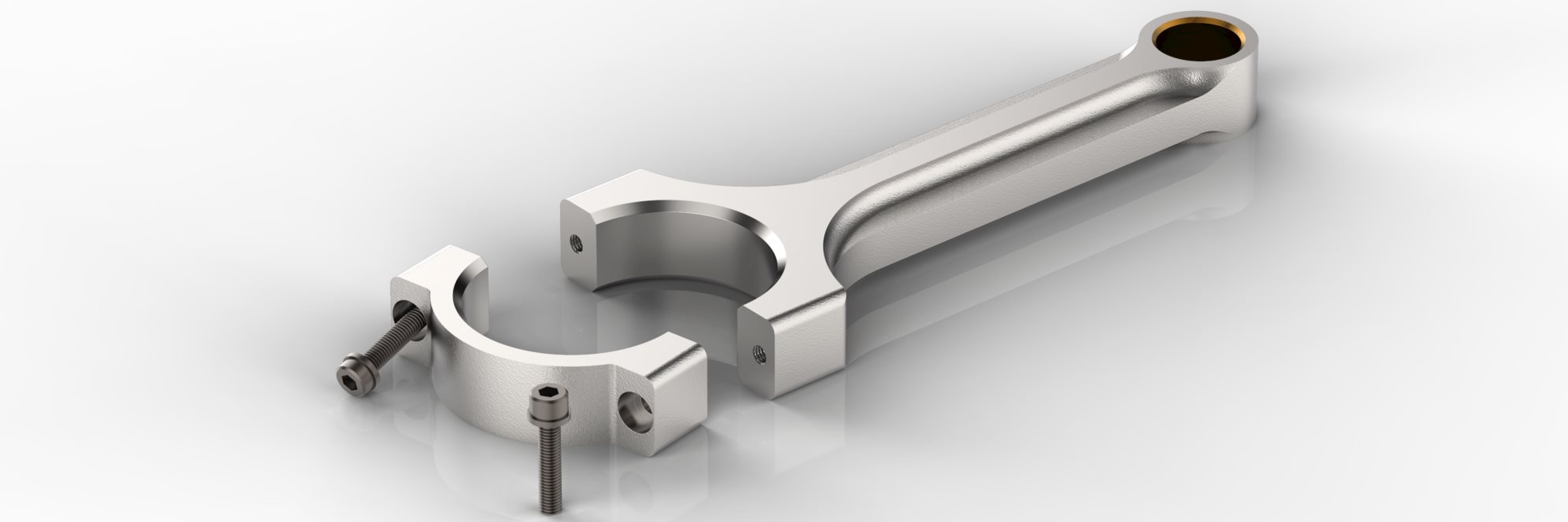
Bearing Cap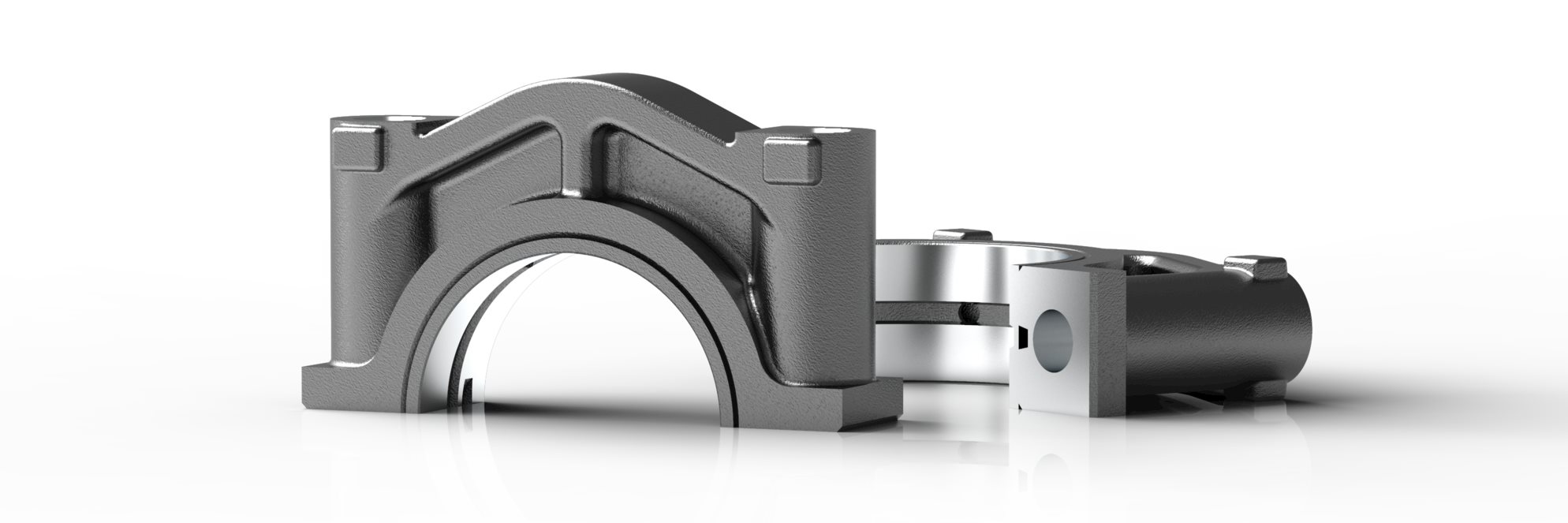