Cylinder Head
Cylinder head designs are key to reducing fuel emissions and meeting strict government regulations. As a result, the components place high demands on processing quality. The components involve extremely complex and demanding machining operations, as well as custom tooling.
YOUR MANUFACTURING CHALLENGES
- Removing irregular stock with high productivity and reliability.
- Maintaining productivity while cutting irregular stock, cast skin and impure surfaces.
- Achieving productive and reliable roughing of valve spring seats and tappet bores.
- Finishing tappet bores with optimal quality and process security.
- Productively roughing swirl chambers and guide entrances for boring.
- Reliably performing highquality finishing of parent metal bores for valve seats and guides.
- Meeting quality and productivity requirements when finishing valve seats and guides.
- Reducing cycle times and ensuring reliability for numerous holes.
- Maintaining high productivity and reliability when finishing parts with demanding surface finish and flatness requirements.
- Drilling numerous holes with low cycle times, high quality and reliability.
- Finishing the camshaft line while maintaining quality, productivity and reliability requirements.
- Minimising cycle times when producing numerous deep, high-quality holes.
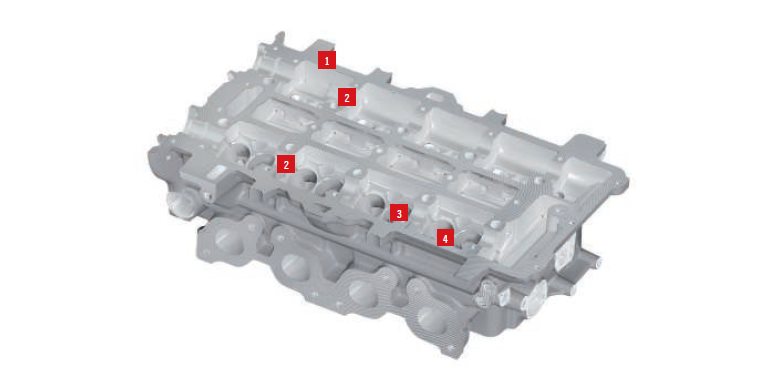
| 1 - Removing irregular stock |
Your Challenge: | | Removing irregular stock with high productivity and reliability. |
Our Solution: | | Available in diameters ranging from 50 mm to 250 mm, the R220.91 provides top performance in irregular stock, with insert geometries for both roughing and finishing. The steel cutter body is balanced and features through coolant holes, while PCD-tipped inserts maximize metal removal rates and tool life. Your benefits include high accuracy, increased tool life and reduced wear on your machine’s spindle bearings. |
Product: | | R220.91 Face Milling Cutter |
| 2 - Cutting irregular stock, cast skin and impure surfaces |
Your Challenge: | | Maintaining productivity while cutting irregular stock, cast skin and impure surfaces. |
Our Solution: | | PCD-tipped to provide long, predictable tool life, the Custom PCD Ball Nose Milling Cutter incorporates through coolant holes to maximize performance. A balanced tool with an integrated HSK shank, the cutter offers retrofitting possibilities and lowers costs by reducing tool consumption and increasing part quality. Your benefits include higher process security and productivity. |
Product: | | PCD Ball Nose Milling Cutter |
3 - Achieving productive and reliable roughing
Your Challenge: | | Achieving productive and reliable roughing of valve spring seats and tappet bores. |
Our Solution: | | To maximize productivity, this custom tool performs drilling, spot facing and boring in a single operation. The highest metal removal rates are achieved with PCD 20 inserts. Your benefits include substantial productivity gains through a highly reliable process. |
Product: | | PCD Tool |
4 - Finishing tappet bores
Your Challenge: | | Finishing tappet bores with optimal quality and process security. |
Our Solution: | | For the finishing of holes requiring close tolerances and stringent bore geometries, this custom tool achieves the needed quality with minimal cycle times. Balanced and featuring through coolant holes, the tool is PCD tipped and can be reground or reconditioned to its original condition to achieve maximum usable tool life. Your benefits include reducing the costs of achieving high-quality output. |
Product: | | PCD Reamer |
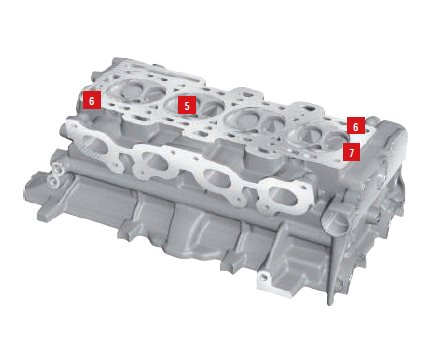
5 - Productively roughing
Your Challenge: | | Productively roughing swirl chambers and guide entrances for boring. |
Our Solution: | | To maximize productivity, this custom tool performs boring and counterboring in a single operation. The highest metal removal rates are achieved with carbide AL geometry or PCD 20 inserts. Your benefits include substantial productivity gains through a highly reliable process. |
Product: | | PCD Tool |
5 - Reliably performing high-quality finishing
Your Challenge: | | Reliably performing high-quality finishing of parent metal bores for valve seats and guides. |
Our Solution: | | For the finishing of holes requiring close tolerances and stringent bore geometries, this custom tool achieves the needed quality with minimal cycle times. Balanced and featuring through coolant holes, the tool is PCD tipped and can be reground or reconditioned to its original condition to achieve maximum usable tool life. Your benefits include reducing the costs of achieving high-quality output. |
Product: | | PCD Reamer |
5 - Finishing valve seats and guides
Your Challenge: | | Meeting quality and productivity requirements when finishing valve seats and guides. |
Our Solution: | | Fully integrated with an HSK attachment, custom Bifix reamers combine multiple operations. Available as single or multi tooth guide reamers made from carbide or PCD, the cutters incorporate patented adjustable cartridges to provide maximum security. Fullface, 4-edge CBN inserts finish the different chamfers on the sintered steel ring seat, and the tool is balanced to minimize wear on spindle bearings. Your benefits include reducing cost per part while increasing the stability of your operations. |
Product: | | BifixTM Reamer |
Your Challenge: | | Reducing cycle times and ensuring reliability for numerous holes. |
Our Solution: | | Featuring a low friction PCD tip and high strength geometry, this tool provides high process security and offers long, predictable tool life. Sharp cutting edges increase hole quality and reduce exit burrs, and the tool allows the use of aggressive cutting data, making it an ideal method for increasing productivity on high speed machining centers. Your benefits include superb quality and reduced costs from higher throughput. |
Product: | | PCD Step Drill |
7 - Maintaining high productivity and reliability
Your Challenge: | | Maintaining high productivity and reliability when finishing parts with demanding surface finish and flatness requirements. |
Our Solution: | | Available in diameters ranging from 50 mm to 250 mm, the R220.91 provides top performance with insert geometries for finishing. The cutter body is balanced and features through coolant holes, while PCD-tipped inserts maximize metal removal rates and tool life. Your benefits include high accuracy, increased tool life and reduced wear on your machine’s spindle bearings. |
Product: | | R220.91 Face Milling Cutter |
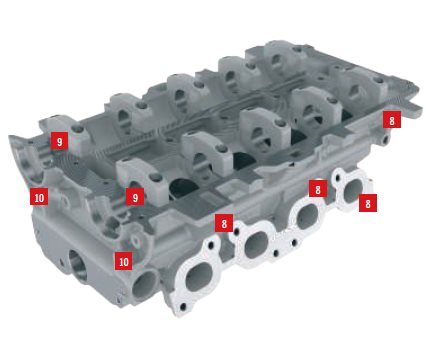
8 - Drilling numerous holes
Your Challenge: | | Drilling numerous holes with low cycle times, high quality and reliability. |
Our Solution: | | Providing high performance when dealing with angled exits or intersecting holes, the Seco Feedmax Chamfer Drill utilises the light-cutting N geometry and a special edge preparation to increase process security and tool life. The tool also incorporates a low-friction coating, and uses four land margins to increase stability. Your benefits include maintaining productivity in challenging, high-tolerance holes. |
Product: | | Seco FeedmaxTM Chamfer Drill |
9 - Finishing the camshaft line
Your Challenge: | | Finishing the camshaft line while maintaining quality, productivity and reliability requirements. |
Our Solution: | | Each of this pair of custom tools uses a single PCD indexable blade and guide pads to maintain impeccable tolerances, roundness, concentricity and surface finish. The shorter tool machines the first bearing on both camshaft lines, with the longer tool then machining all of the bearings on both lines. Through coolant holes maximize chip evacuation. Your benefits include absolute precision in a proven process for this specific application. |
Product: | | Bifix® Reamer |
10 - Minimising cycle times
Your Challenge: | | Minimising cycle times when producing numerous deep, high-quality holes. |
Our Solution: | | Featuring sharp, positive and strong cutting edges that provide excellent hole quality, Seco Feedmax SD230A provides high performance in drilling holes of up to 30x tool diameter. Optimised geometries ensure process security, long tool life and exceptional performance in aluminium, reducing exit burrs and minimising workpiece deformation. Your benefits include reliable, productive and cost-efficient holemaking. |
Product: | | Seco FeedmaxTM SD230A |
HOMERelated content
Case Studies: Cylinder Head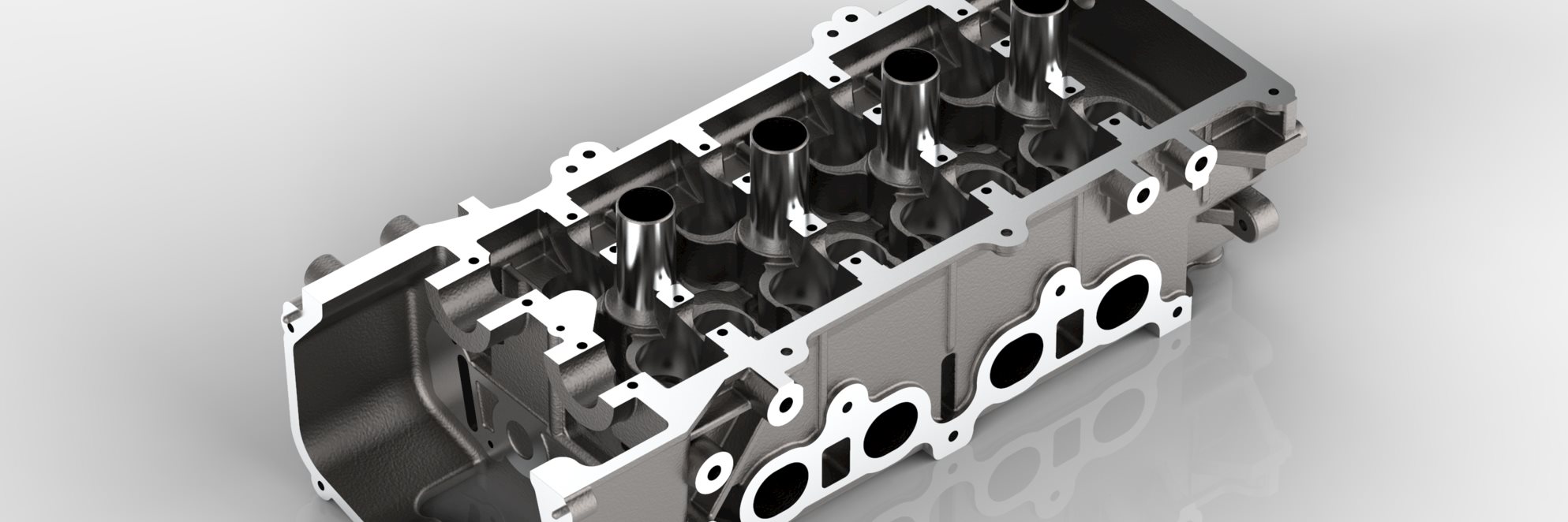
Turbocharger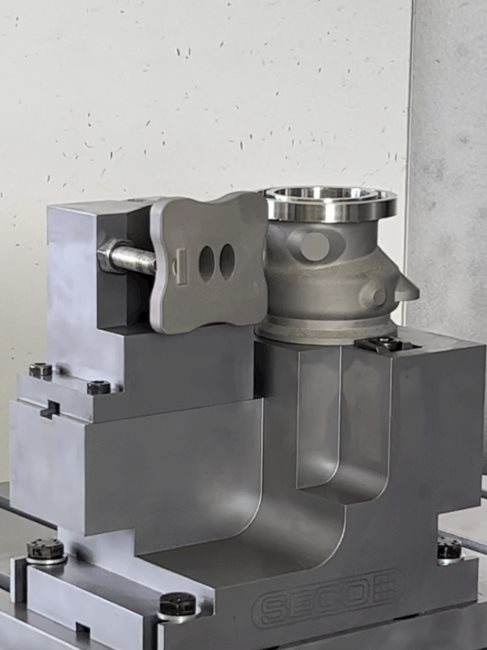
Truck Engine Block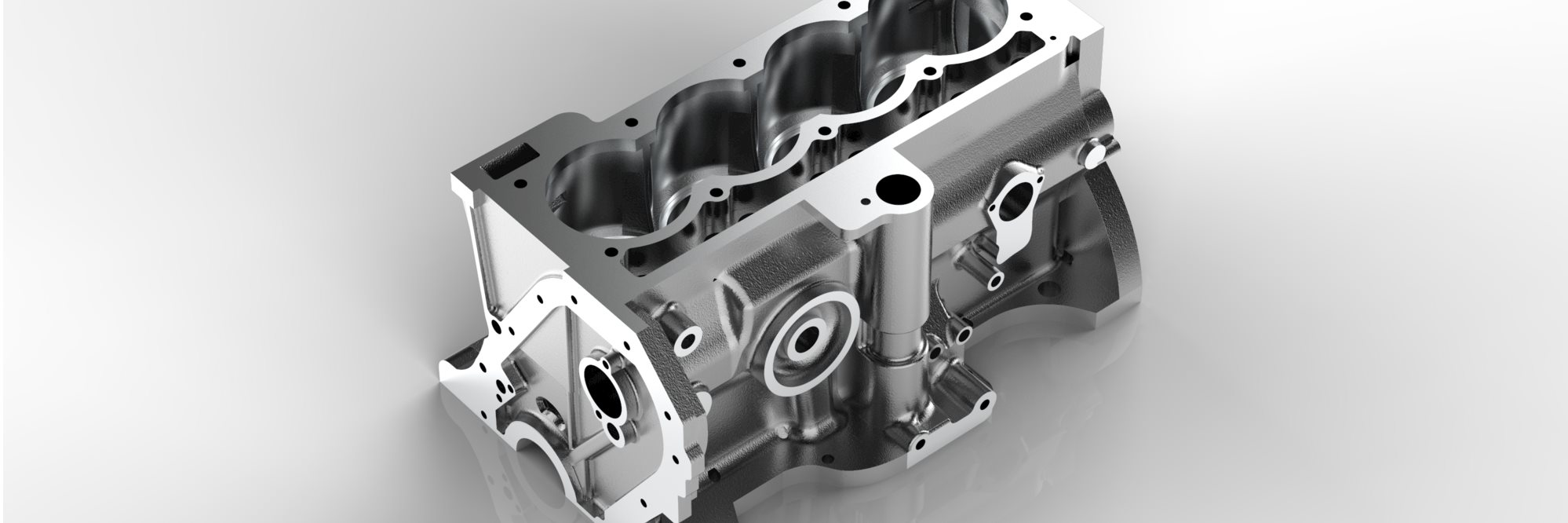
Video: 5 solutions to the main engine block challenges | Seco Tools
Crankshaft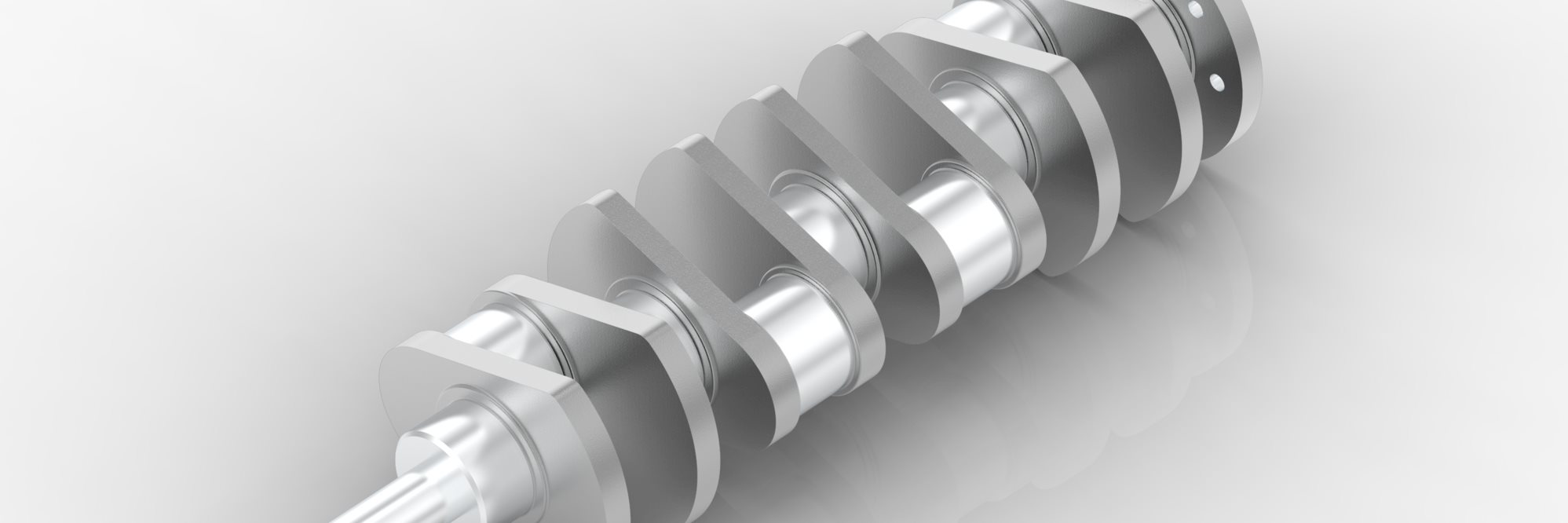
Piston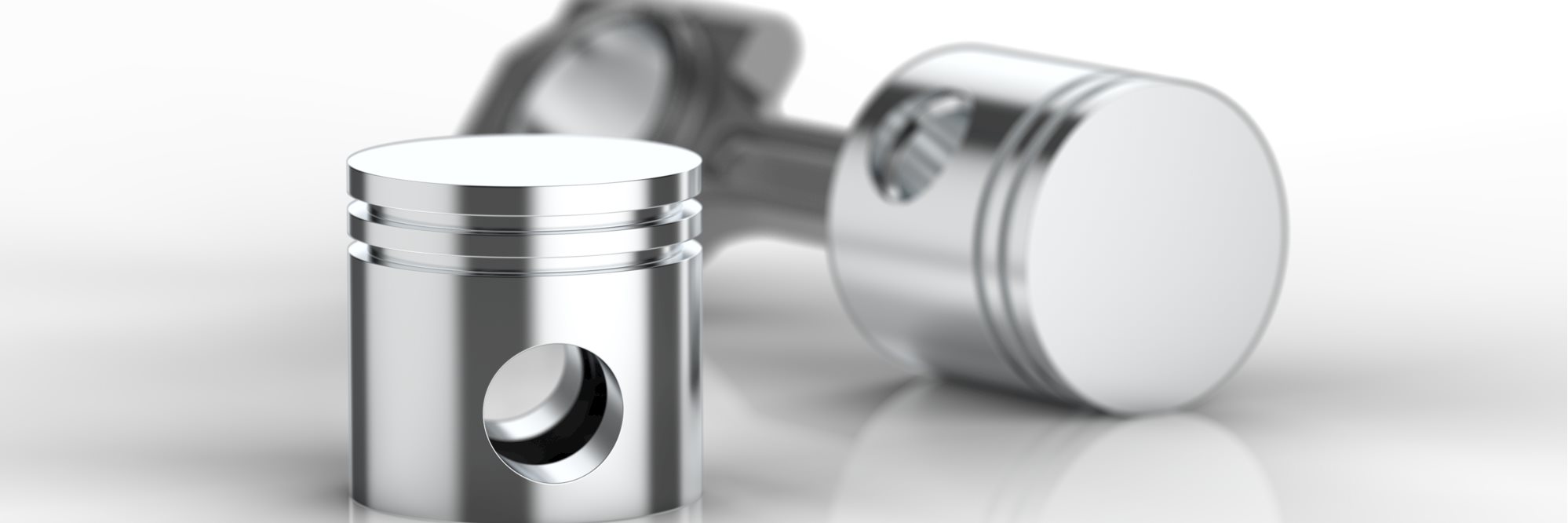
Connecting Rod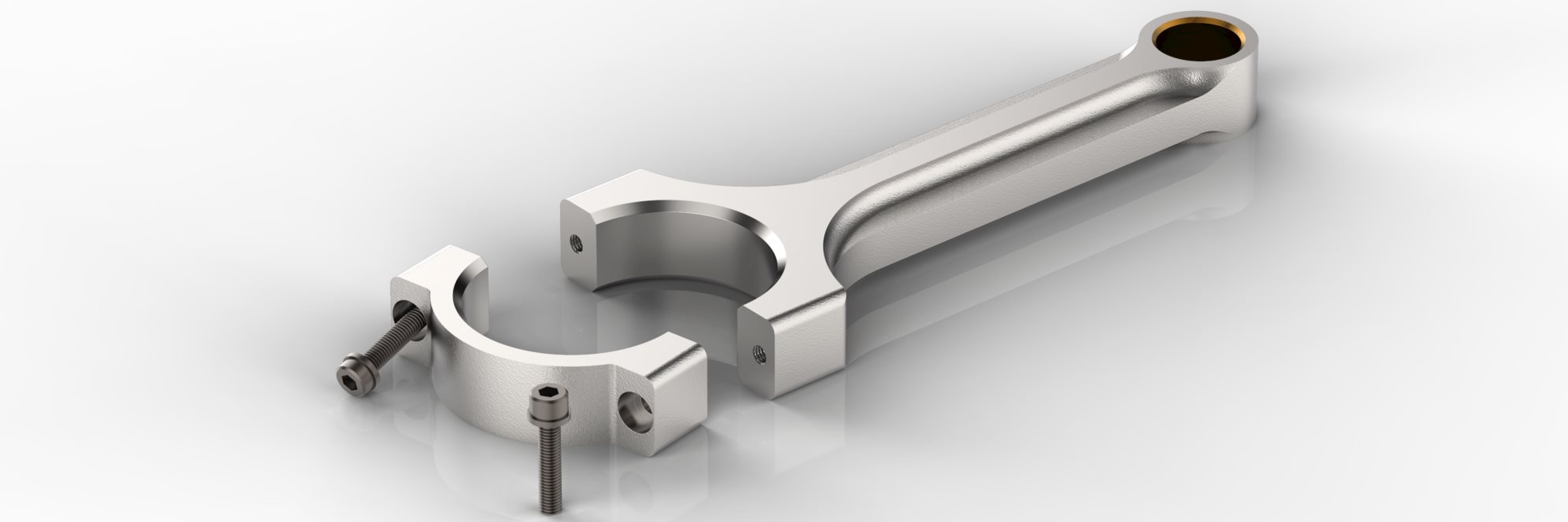
Bearing Cap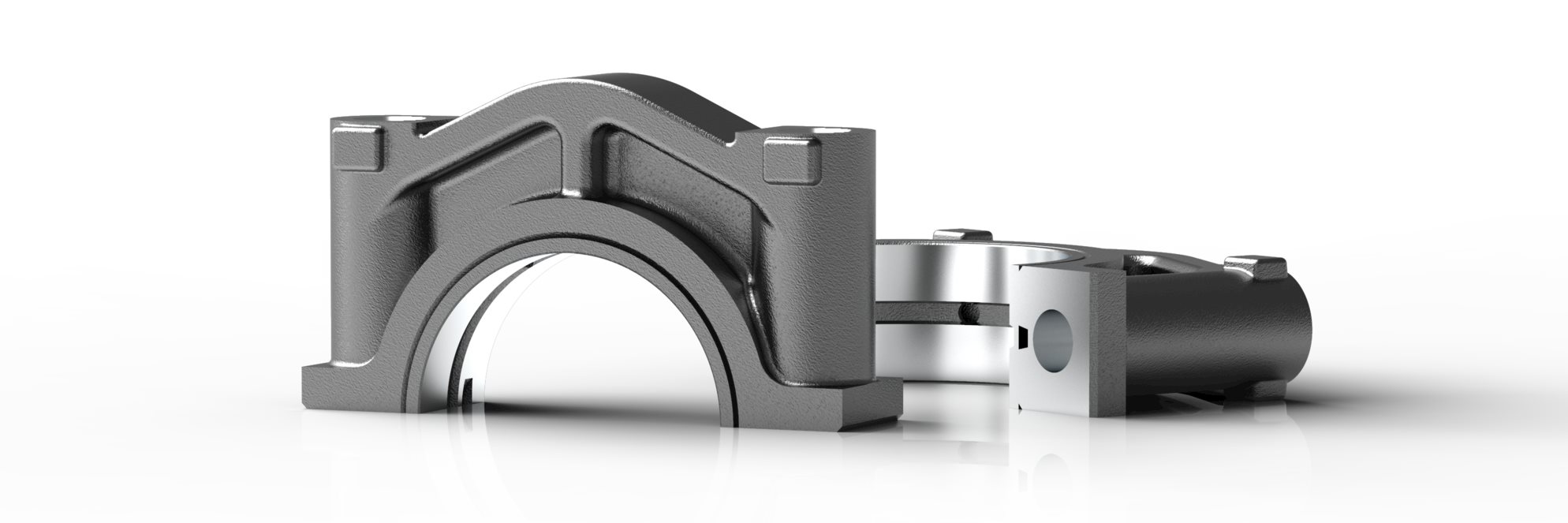