Connecting Rod
As the critical link between engine crankshaft and piston, connecting rods are forged and split into two parts by either a sawing or cracking process. Machining requires extremely strong and stable precision tooling and machines.
YOUR MANUFACTURING CHALLENGES
- Drilling numerous holes with low cycle times, high quality and reliability.
- Producing spot faces with maximum productivity and reliability.
- Productively and reliably producing both chamfers when roughing the crank bore.
- Establishing an efficient and secure process for finishing the crank bore.
- Productively and reliably producing both chamfers (V shape) on piston bore.
- Drilling the piston bore with minimal cost and time.
- Reliably finish cutting the piston bore brass bush with high quality and productivity.
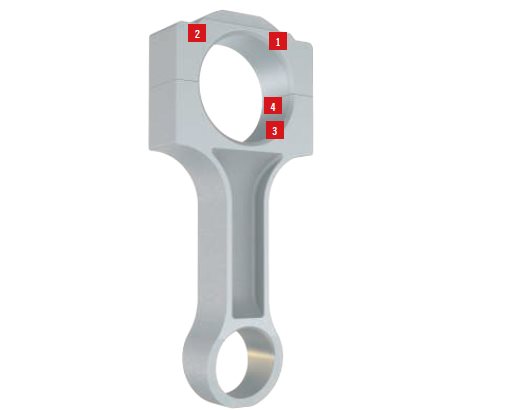
1 - Drilling numerous holes
Your Challenge: | | Drilling numerous holes with low cycle times, high quality and reliability. |
Our Solution: | | Providing high performance when dealing with angled exits or intersecting holes, the Seco Feedmax SD245 Chamfer Drill utilises the lightcutting geometry and a special edge preparation to increase process security and tool life. The tool also incorporates a low-friction coating, and uses four land margins to increase stability. Your benefits include maintaining productivity in challenging, high-tolerance holes. |
Product: | | Seco FeedmaxTM SD245 Chamfer Drill |
2 - Producing spot faces
Your Challenge: | | Producing spot faces with maximum productivity and reliability. |
Our Solution: | | The R417.19 custom tool uses a square positive insert and adjustable cartridge with a chamfering insert to combine spot facing and chamfering operations. The balanced cutter offers smooth cutting action and produces a constant chamfer value on a multi-spindle machine. Your benefits include cost reduction through process optimisation. |
Product: | | R417.19 Spot Face and Chamfering Cutter |
| 3 - Roughing the crank bore |
Your Challenge: | | Productively and reliably producing both chamfers when roughing the crank bore. |
Our Solution: | | This custom tool provides both crank bore roughing and chamfering by circular interpolation, with the ability to adjust the chamfer dimension by setting the insert with a fine adjustment screw. Through coolant holes increase tool life and chip evacuation, and the use of ISO/ANSI Duratomic® inserts maximize metal removal rates. Your benefits include greater process efficiency and reduced costs. |
Product: | | Chamfering and Boring Bar |
4 - Finishing the crank bore
Your Challenge: | | Establishing an efficient and secure process for finishing the crank bore. |
Our Solution: | | Maintaining high precision output while minimising cycle times, Xfix uses up to nine teeth to provide high feed rates, while holding tolerances as tight as IT6. Strong and stable insert cartridges ensure process security, while preloaded guide pads prevent vibration and increase stability. Your benefits include achieving needed tolerances without sacrificing the productivity of your production line. |
Product: | | XfixTM Multi-Tooth Reamer |
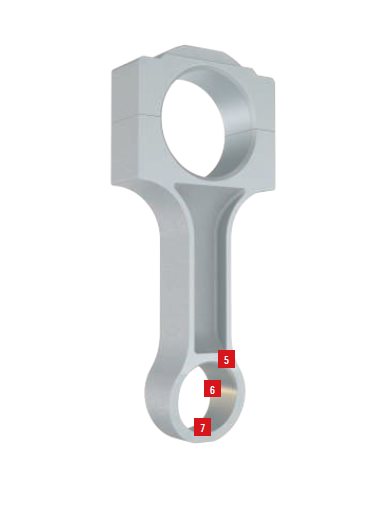
5 - Producing both chamfers on piston bore
Your Challenge: | | Productively and reliably producing both chamfers (V shape) on piston bore. |
Our Solution: | | Specially designed for machining the V shape on the piston side of the connecting rod, this cutter combines spot facing and chamfering to increase productivity. The use of insert cartridges protects the cutter body and allows the chamfer value to be easily adjusted by setting the chamfering insert. Your benefits include an economical solution that streamlines your production process. |
Product: | | Plunging and Chamfering Cutter |
| 6 - Drilling the piston bore |
Your Challenge: | | Drilling the piston bore with minimal cost and time. |
Our Solution: | | Developed specifically to avoid deflection when starting to drill the large stamping dimple, this custom Perfomax drill features two inserts on the outer diameter to stabilise the tool until the center insert engages the material. A unique flute design optimises chip removal, and the use of Perfomax drilling inserts allows for a very cost-effective process. Your benefits include reducing costs while maintaining high process stability. |
Product: | | PerfomaxTM Chamfer Drill |
7 - Reliably finish cutting the piston bore brass bush
Your Challenge: | | Reliably finish cutting the piston bore brass bush with high quality and productivity. |
Our Solution: | | To allow for high cutting speeds while maintaining accuracy, the Bifix PCD reamer uses a PCD reaming blade and multiple guide pads to maintain stability. The PCD-tipped blade provides long tool life and excellent surface finishes. Your benefits include highly productive precision machining with lower production costs. |
Product: | | BifixTM PCD Reamer |
HOMERelated content
Case Studies: Connecting Rod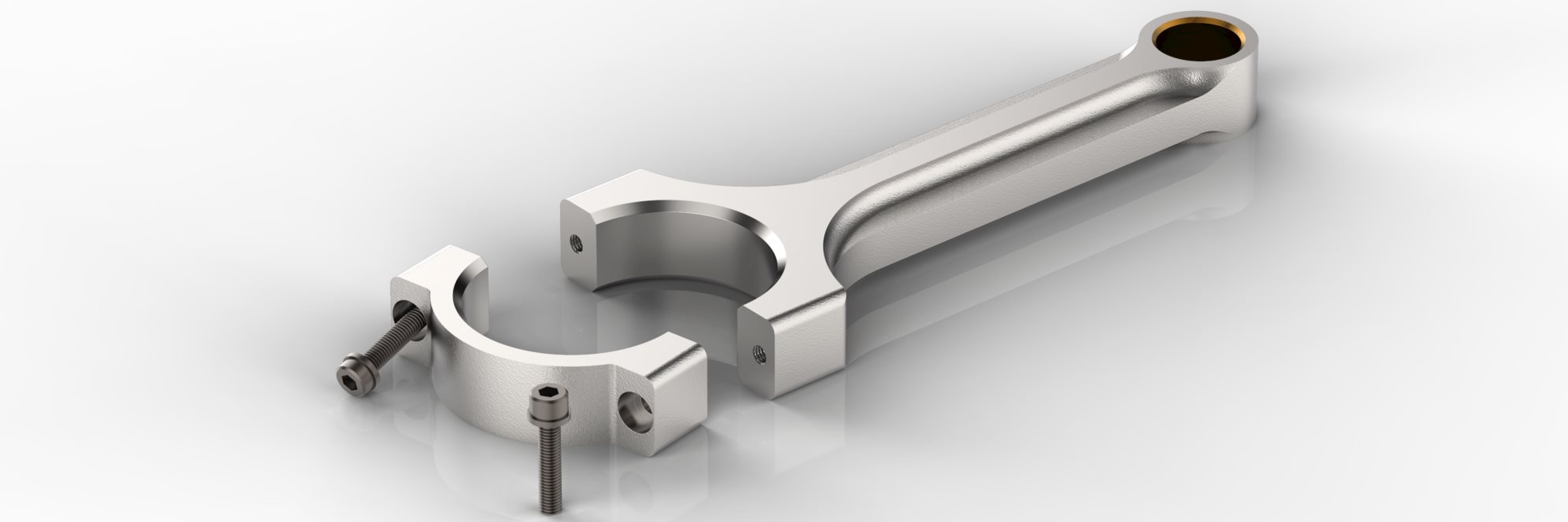
Turbocharger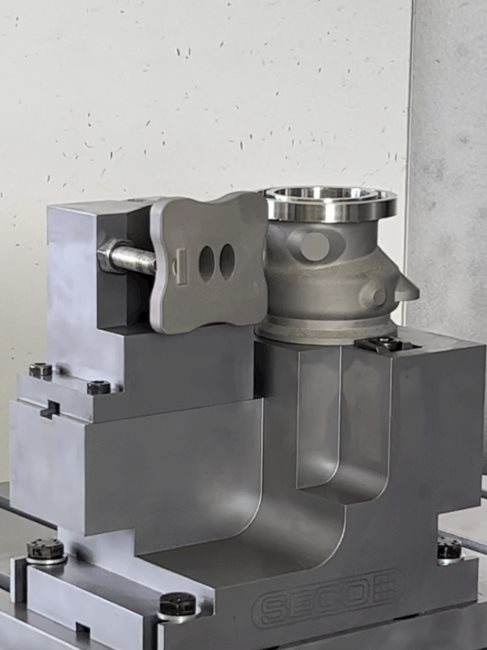
Truck Engine Block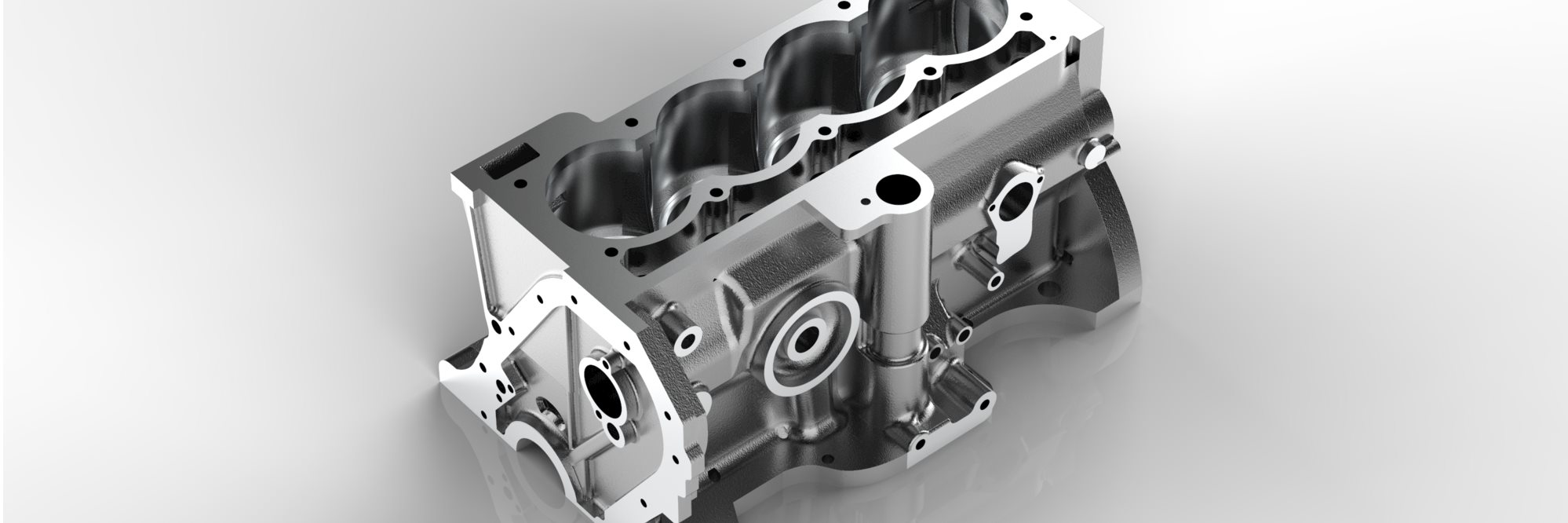
Video: 5 solutions to the main engine block challenges | Seco Tools
Crankshaft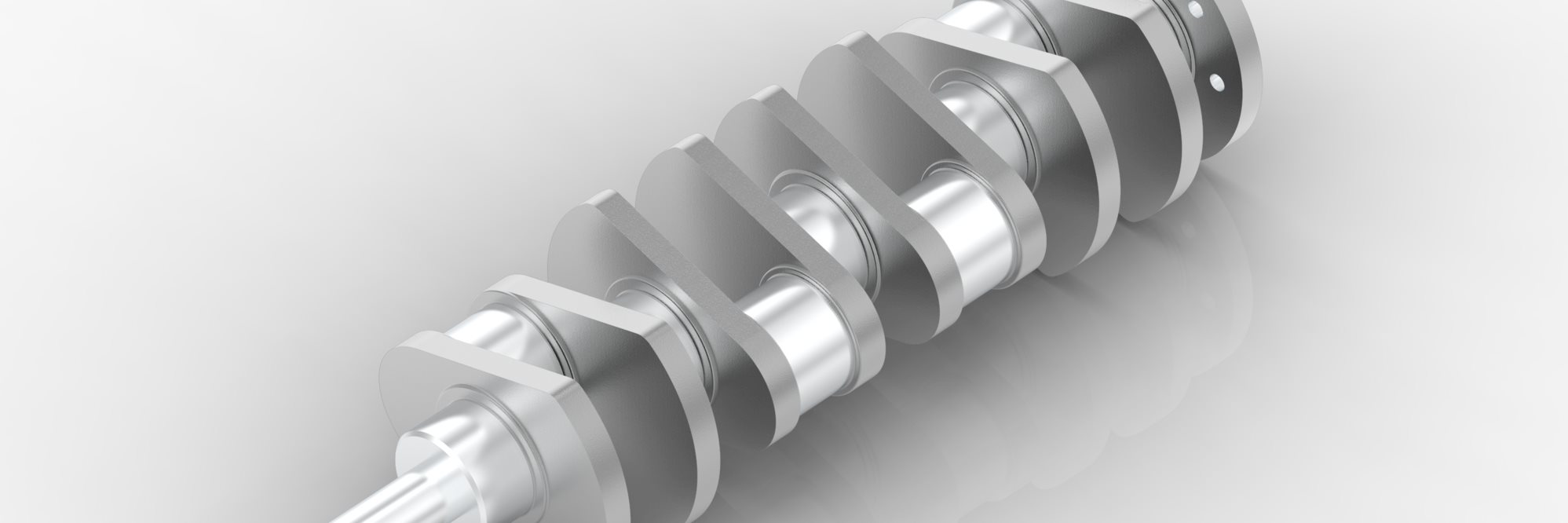
Piston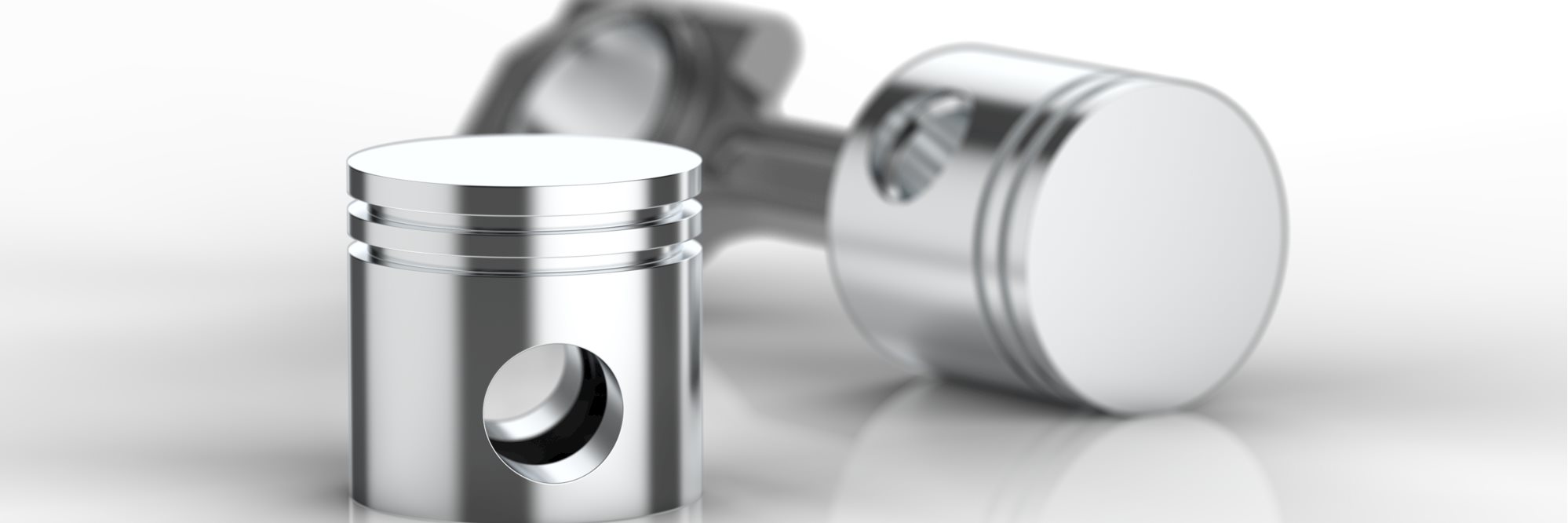
Cylinder Head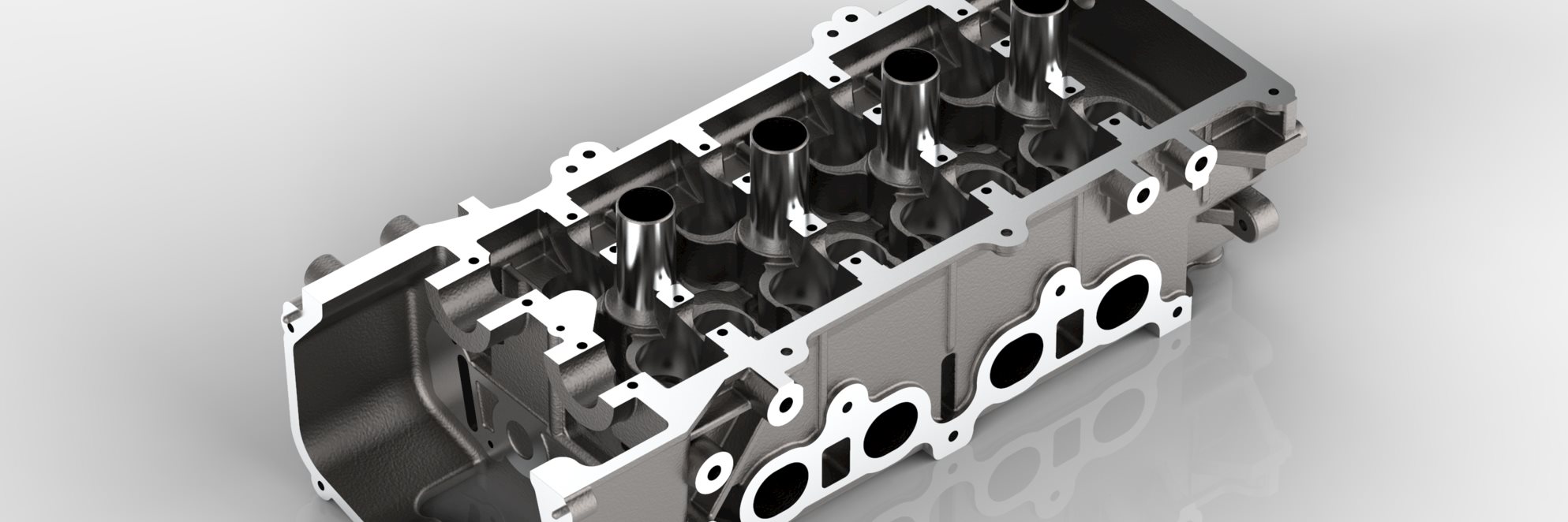
Bearing Cap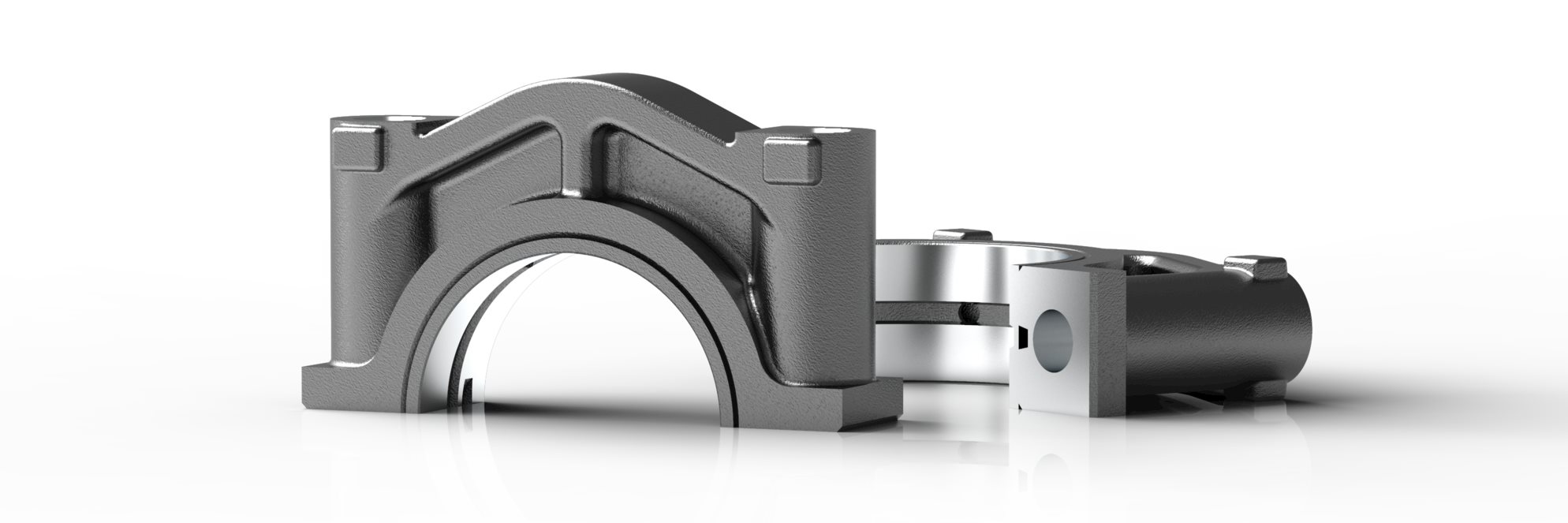