Aerospace Pintle Plate
When you balance productivity with cost per part, you save on production costs and make better parts. That's the advantage of optimized processes.Titanium pintle plates are literally pivotal components of aircraft landing gear. This part undergoes constant stress with every takeoff and landing, so its production is critical to safe, successful flight.
But from function to material (mainly titanium) and form, the pintle plate presents numerous manufacturing challenges, starting with the need for high productivity and low costs per part. With deep pockets and multiple complex design features, this part calls for a reliable process that takes advantage of new technology and techniques to optimize tool life and achieve high-quality surface finishes with shorter cycle times.
In aerospace machining, cost reduction often focuses on reduction of post-finishing operations through better production results. For example, high-feed milling increases metal removal rates on the top of the part and controls spindle load, especially when using dynamic milling. The essence of this process is the right insert, one that can withstand the stickiness and heat resistance of high tensile strength materials. With the correct tooling, shops will see excellent wear resistance and very good edge integrity.
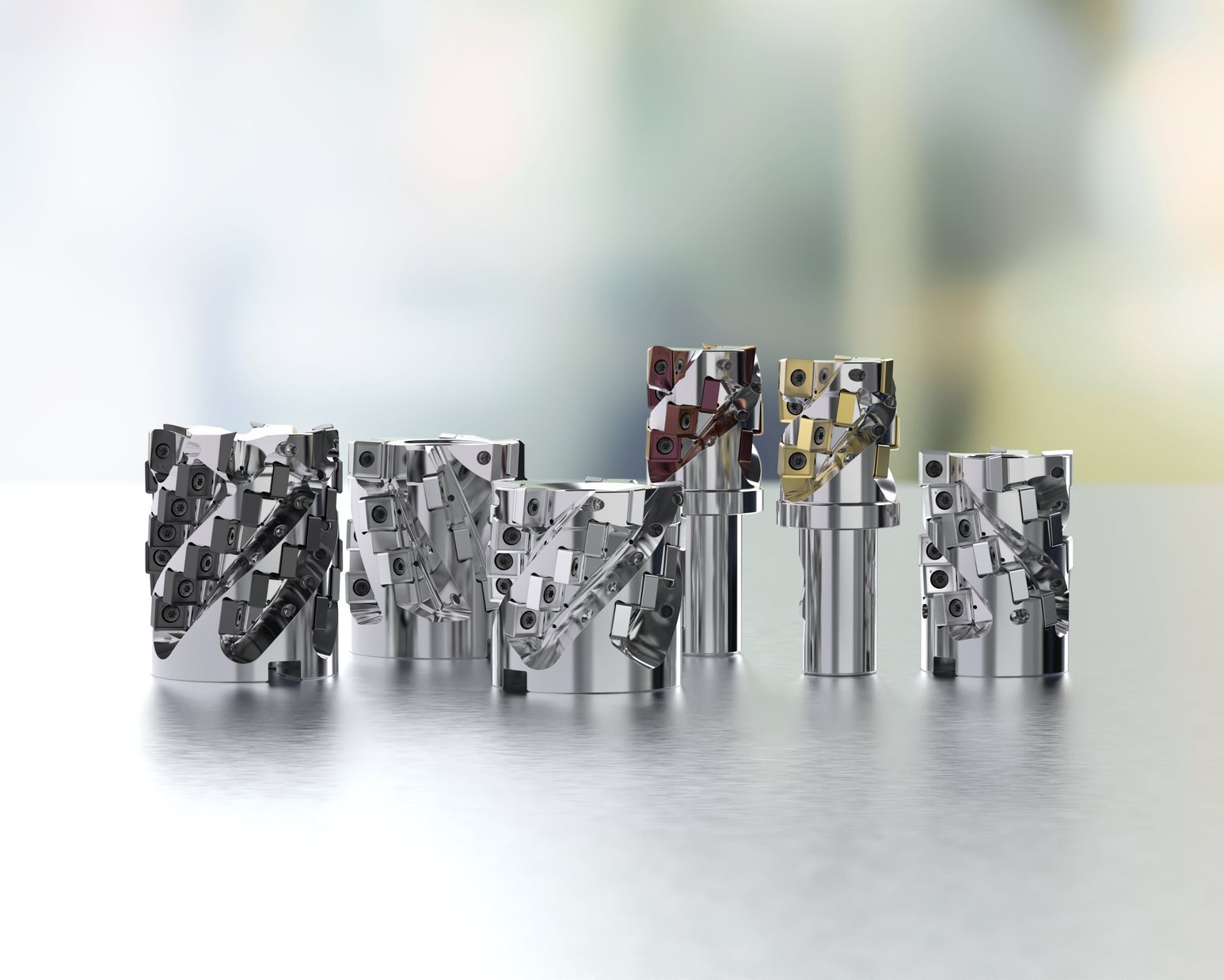
To remove large amounts of material quickly and accurately, helical milling takes care of complex part geometries. Optimized technology, dedicated grades and geometries all work together to achieve secure productivity and cost reduction.
Dynamic milling makes quick work of small-radius pocket corners and helps with chip control. Strong-cored end mills reduce tool deflection and increase dimensional stability for results that pave the way to finish machining.
Drilling typically becomes a late-stage operation, all the more critical because of the amount of value invested in the part by the time drilling occurs. To eliminate tool failure for a secure, predictable process with sharp positive geometries for good chip control, the strength of square inserts combines with strong drill bodies for optimized operations.
Finally, interpolation tackles tight-tolerance final features without heat-related workpiece distortion or unpredictable tool wear. A high-performance tooling solution quickly creates a fast, accurate bore, even on long overhangs.
The pintle plate is a complex high-value part with a critical role to play in aircraft performance and safety. As such, it's subjected to heavy stress in every takeoff and landing. Its production requires the utmost in process security and reliability – and shops can rely on Seco tooling for every demanding operation.
Many of the difficulties in pintle plate production stem from this part's material. Titanium's notoriously sticky, adhesive nature and high temperature resistance make this a difficult part to cut. Add in a high-quality surface finish, and the manufacturing process takes on far more challenges. The combination of all these requirements makes collaborative expertise even more valuable to shops that want to extract maximum value from this part.
Know more about ISO S materials and Titanium
Tooling alone cannot guarantee production success. Shops need the expertise to go beyond tooling selection to fixture management, spindle load balancing, machining strategy selection and toolpath verification. With Seco as their expert partner, shops can develop an end-to-end process that speeds production, reduces costs and increases part quality at every step in aerospace machining.
Aerospace manufacturers face enormous pressures to produce complex parts faster and at lower costs. Digital tools can offer manufacturers enormous advantages in pintle plate production. Knowledge is power, and the data derived from digitalization gives shops many powerful insights.
Measurements make the difference in every aspect and operation of aerospace machining. Digital tools help shops verify tooling, part and fixture dimensions for increased accuracy, part quality and productivity. Tool path verification relies on machining simulations to guarantee production results that match specifications and exceed expectations.
With Seco as their expert partner, aerospace manufacturers can access the latest tooling, knowledge and solutions to optimize their operations.
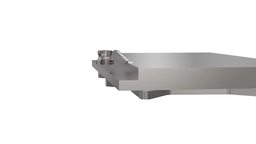
- Remove large amounts of material.
- Avoid overloading the spindle.
- Maintain good chip control.
- Optimize material removal from the top of the component.
- Avoid overloading the spindle.
- Maintain excellent chip control.
- Combine optimized cutting parameters with two high-feed solutions for maximized cutting parameters in aerospace machining.
- Use dynamic milling for high metal removal rates with a controlled spindle load and secure machining process.
- MP2050 insert combines excellent wear resistance with high edge integrity.
- New insert substrate provides increased toughness and tool life for excellent high-temperature properties with abrasive, sticky materials.
High Feed SP face mill
High Feed 2 face mill
MP2050 carbide/cermet inserts

- Remove large amounts of material in a stable, secure process.
- Achieve long, consistent tool life.
- Large amounts of material removal.
- Maintain high MRR in a productive, stable, secure process for aerospace machining.
- Maximize tool life.
- Combine an 8-edge helical mill with optimized cutting parameters for secure productivity.
- Dynamic milling with dedicated grades and geometries produce successful results in aerospace machining with titanium.
SN8 helical mill
MP2050 carbide/cermet inserts
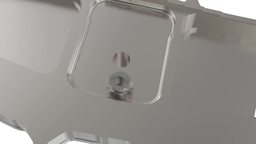
- Reach small-radius corners in deep-walled pockets.
- Maintain good chip control to avoid recutting that increases per-part costs through wasted time and material.
- Small-radius pocket corners require smaller-diameter cutters.
- Milling is difficult deep in the pocket wall.
- Good chip control is essential to avoid recutting of chips.
- Tooling provides a strong tapered core to reduce tool deflection and increase dimensional stability.
- Milling optimizes surfaces for finish machining.
- Advanced cutting parameters increase productivity in roughing and semi-finishing for aerospace machining.
Jabro JS720 solid carbide end mill

- Create a secure, predictable process that eliminates costly tool failures.
- Maintain good chip control.
- Avoid tool failures in challenging materials and high-value parts.
- Create a secure, predictable aerospace machining process with effective chip control.
- Combined strength of drill body and square inserts produce reliable, secure drilling.
- Sharp, positive MC and MP geometries provide chip control and minimize heat generation.
- NIB top layer prevents chemical reactions.
Perfomax drill
DS2050 carbide inserts

- Achieve exceptional surface finishes and dimensional tolerances.
- Avoid the use of expensive precision bearing tools that require complex adjustments.
- Eliminate heat-related distortion of workpiece dimensions.
- Maintain predictable tool wear in aerospace machining.
- Overcome programming difficulties in angularly fixtured part.
- Achieve proper surface finish and tight dimensional tolerances in aerospace machining.
- Avoid expensive precision boring tools and complex adjustments.
- Avoid heat-related distortion of the workpiece.
- Achieve predictable tool wear.
- Overcome the difficulties of programming and machining in an angular orientation.
- Create a reliable tooling solution for high-performance turning in aerospace machining.
- Achieve fast, accurate boring in a challenging material.
Seco-Capto toolholder
TS2000 carbide/cermet insert with PVD coating and MF1 geometry
Contact us here