Reuse Finish End Mills to Maximize Tool Life ROI
Improving tool wear and, thereby, increasing tool life is a significant factor in keeping production costs under control. One suggestion is reusing tools for lower tolerance passes as a simple method for increasing overall tool life, improving tool ROI and getting more use out a shop’s tool inventory.Sustainable manufacturing is a constant balancing act between productivity and cost. Improving tool wear and, thereby, increasing tool life is a significant factor in keeping production costs under control. Understanding how to increase tool life not only keeps tool inventories in check, but it also decreases production costs by reducing rejections and machine downtime for tool changeovers. In sum, useful tool life is the most important factor to consider in evaluating sustainable machining and production economics.
Tool life is defined in several ways: minutes of use, material removal rate and/or the number of parts it can produce. Generally, when a tool is worn to a point that it can no longer produce a part within proper specifications, it is generally time to replace it.
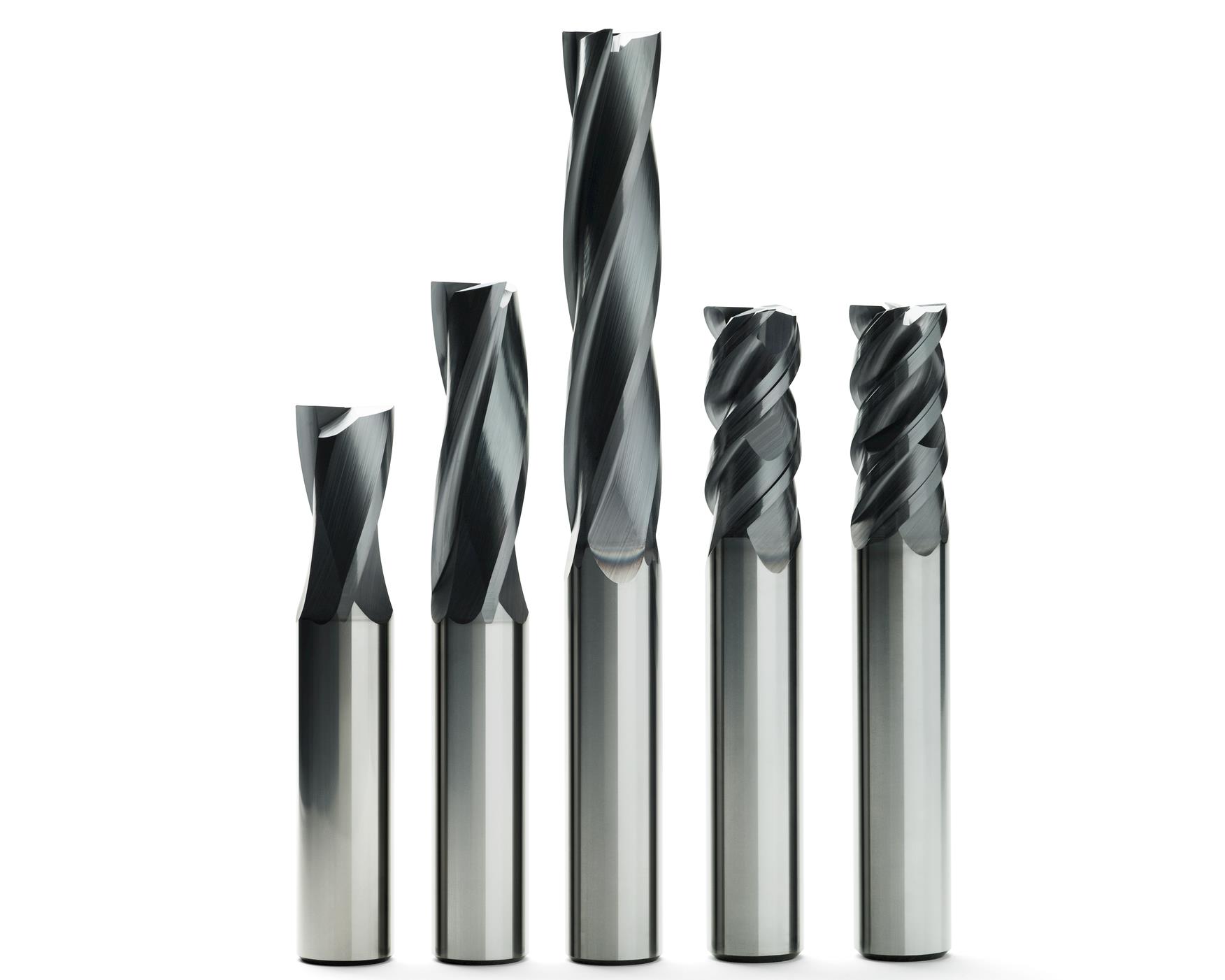
Ensuring adequate tool life starts by selecting the proper tool in terms of substrate, grade, and geometry appropriate for the material being processed. Once a tool has been selected, manipulating cutting conditions is the next path to optimizing tool life. Studies show that increased cutting conditions and increased mechanical loads speed up tool wear and shorten tool life. Cutting speeds have the most prominent effect on tool wear and life, followed by run-out, feed rates and depth of cut.
Tool selection, however, should not be completely application driven. In addition to considering unique application requirements and cutting conditions, shops should also consider their overall production targets and economic goals. While the cost of designing and using special tools for a specific high-volume/low-mix process might make sense for long production runs, that method would prove cumbersome and costly in high-mix production.
Additionally, just-in-time production is moving manufacturing away from high-volume/low-mix mass production to a more high-mix/low-volume model. For shops running a variety of small-batch parts, cost-effective, sustainable machining requires more universal tooling for a broader application window.
Seco Product Manager Jay Ball suggests reusing tools for lower tolerance passes as a simple method for increasing overall tool life, improving tool ROI and getting more use out a shop’s tool inventory.
A Seco solid carbide end mill used for finishing passes on non-ferrous metals, for example, may begin to lose its ability to provide high surface quality with the desired RA values after some two + hours of machining. Performance will also depend upon how much stock is left for the finishing pass. Good practice recommends a finish stock allowance of 1% - 2% of the finish cutter diameter to avoid premature tool wear and poor surface finish.
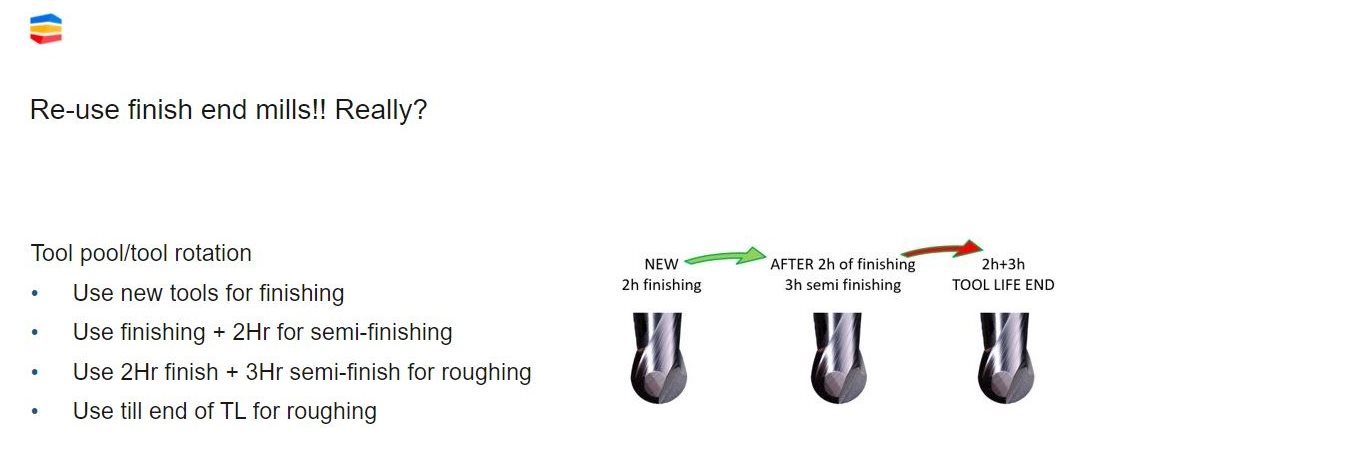
However, just because an end mill cannot finish to the required specifications does not mean its productive life is over.
By using it for increasingly less refined passes such as semi-finishing and rest-roughing, shops can potentially extend the end mill’s productive life by five hours or more.
In addition to adding tool life, rest-rough and semi-finish tool paths are excellent measures to remove material left by a larger roughing tool that could not reach into tight corners and ensure a consistent finish stock on all surfaces of the workpiece. Though tool performance would need to be sufficient for a roughing pass, it would not need to approach that required for a finishing pass.
For tips on getting the most from your machining operations, catch more episodes of Jay’s #SecoTechTalk on Seco’s Instagram
You’ll find practical advice that makes your machining more efficient and sustainable. Leave a comment to let him know what you want to hear about next.
Inline Content - Survey
Current code - 5fce8e61489f3034e74adc64