Start achieving more with less
Discover how to overcome the limitations of high-mix, low-volume production and small-batch work with Universal Drills. Start achieving more with less.If you're dealing with high-mix, low-volume production efforts or small-batch work, you know that it can be a real challenge. Every project seems to come with its own unique set of requirements and specifications, making it difficult to optimize your drilling processes efficiently. The constraints of cost limits, inventory limits, tool life limits, geometry limits, and machining limits further compound the complexity of the task at hand. But fear not, there is a solution: work with fewer drills and achieve more.
One of the key issues faced by machinists in high-mix, low-volume production scenarios is the need to constantly switch between different drills. Each drill change not only takes time but also increases the risk of errors and inconsistencies. Moreover, managing a large inventory of various drill types and sizes can be a logistical nightmare, especially when storage space is limited. It becomes evident that having to deal with numerous drills can significantly slow down the drilling process and hamper productivity.
High-mix, low-volume production efforts and small-batch work can be a real challenge for machinists. Cost limits, inventory limits, tool life limits, geometry limits, machining limits, and everything else in between.
Limits are everywhere - but what if you embraced the art of more?
It’s time to say no to machining limitations with Universal Drills.
Unleash a versatile, rock-solid range of carbide drilling and threading tools that refuse to settle for second best. Work with fewer drills and achieve more.
Discover the product range
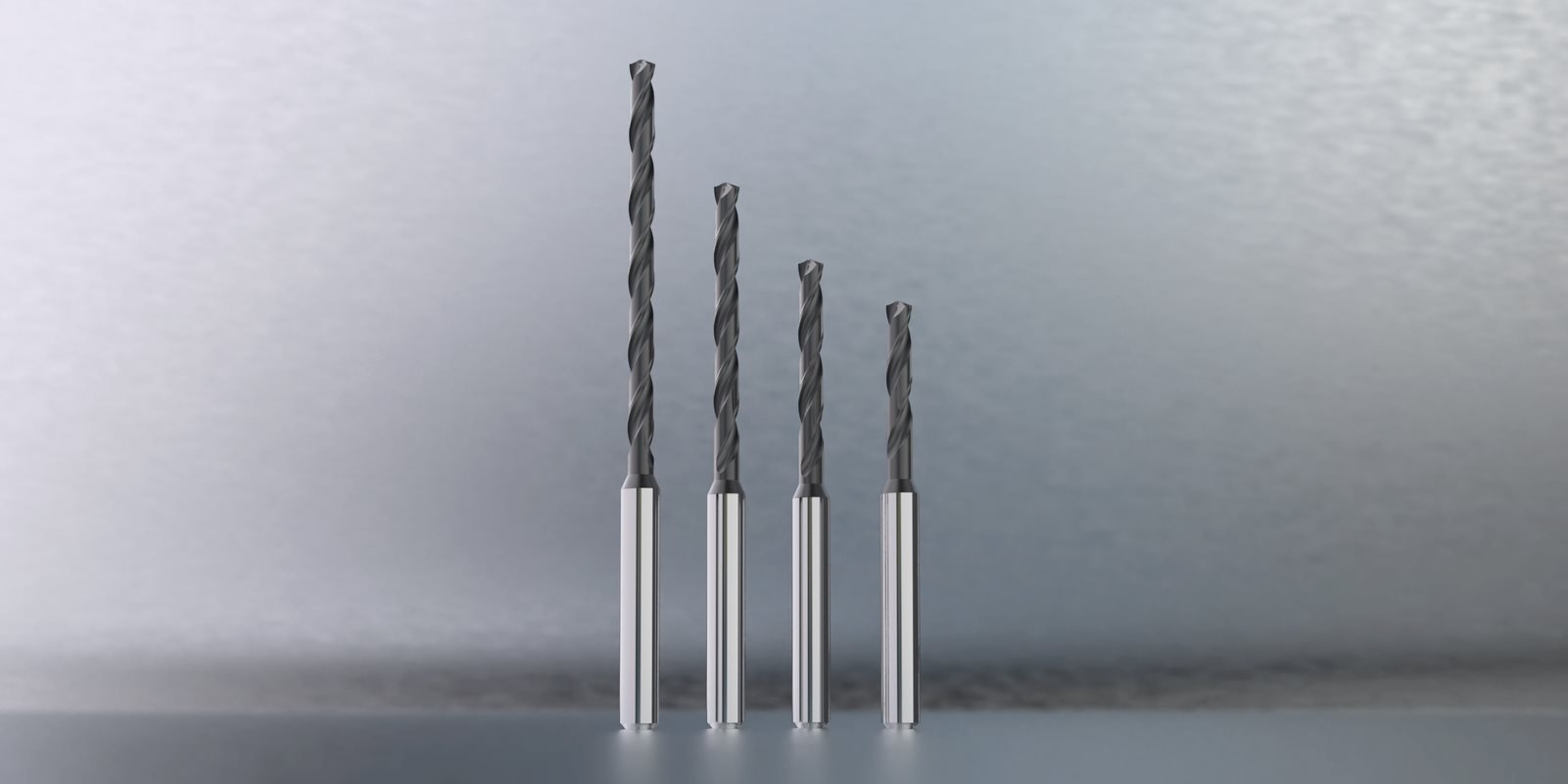
Working with small to medium-sized batches or in a high-mix, low-volume manufacturing environment can mean your tool inventory quickly gets out of hand.
Designed to work with a huge range of materials, you can trust Universal Drills to deliver unwavering performance and lean operations when working with steels, stainless steels and cast irons.
Stop spending money and start saving it. Universal Drills are made for the long haul, featuring a new TiAIN coating.
This coating helps your tools withstand the considerable temperatures produced when working with tougher steels and stainless steels.
Along with high abrasion resistance, toughness and great chip evacuation, manufacturers can expect longer tool life - even when using the same cutting parameters as before.
Nobody likes a time-waster. Universal Drills liberate your tooling inventory from deadwood by undertaking more machining applications.
This means you can stock fewer types of drills, confident in the knowledge that the ones you do have will perform. Plus, Universal Drills are simple to recondition, helping you keep profits safe by avoiding costly regrinding.
Show ‘em who’s boss. Universal Drills fulfil the unwavering performance, tolerances and repeatability your production line demands.
Because, like you, these tools can’t stand laziness. Universal Drills unleash a new level of versatility - helping to fight frustrating tool changeovers, lost time and low-quality work.
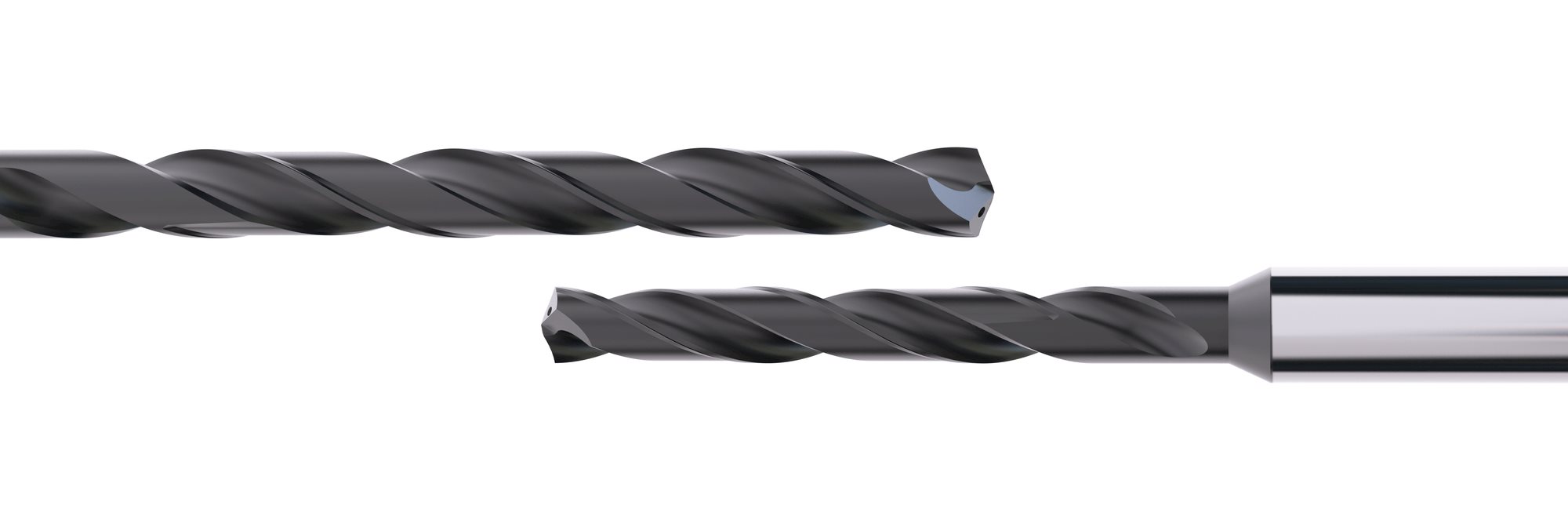
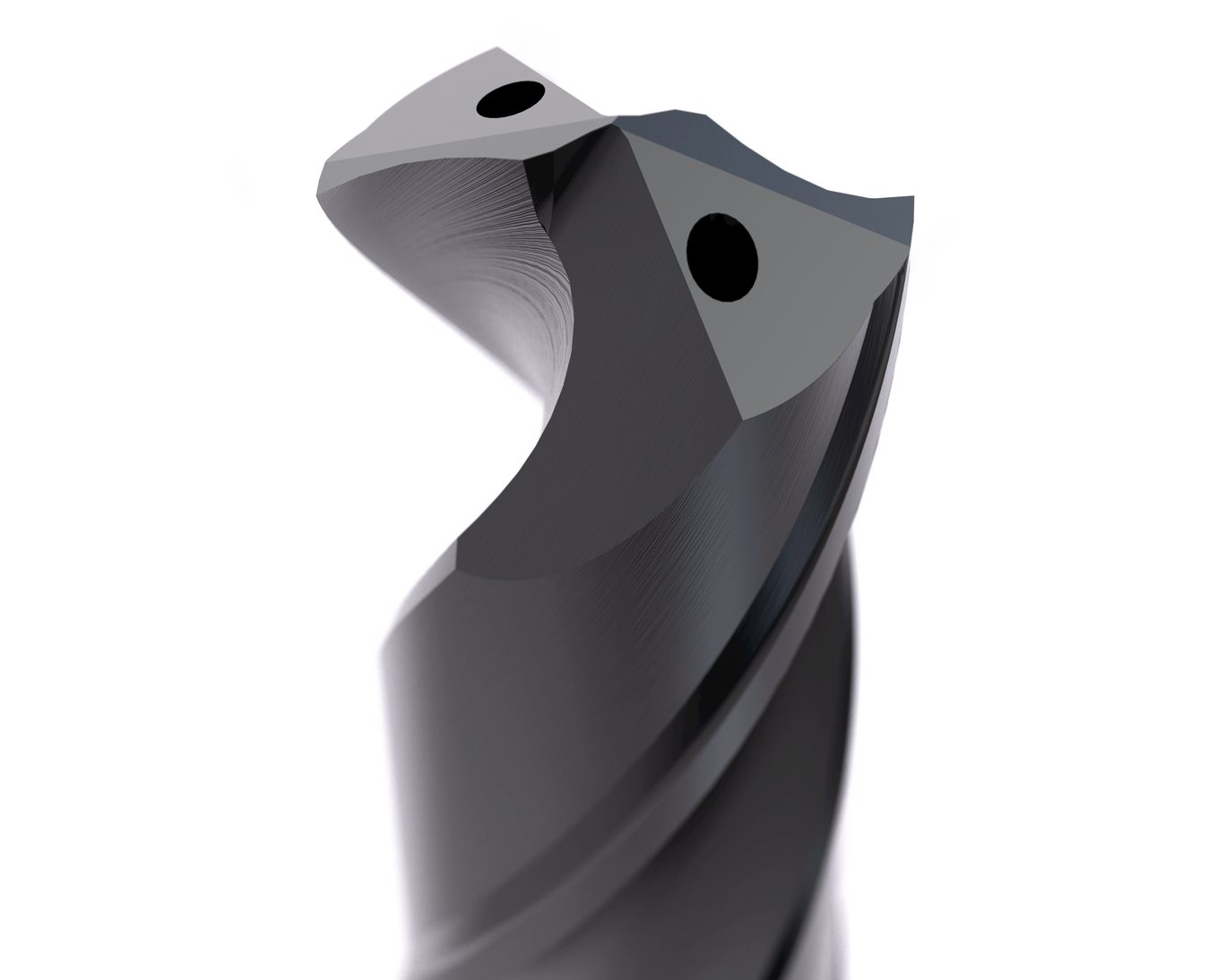
Universal Drills have been designed from the ground up to benefit the modern machinist - ensuring versatility and reduced stockholding costs when working with smaller batch sizes.
- Increased tool life
- Withstand higher temperatures
- Find versatile geometries
- Save money on small-batch work
- Work from a comprehensive range
- Swap regrinding for reconditioning
- Applicable across materials and industries
- Guarantee high-quality and repeatable work
Discover game-changing tips that will minimize drill changes, maximize productivity, and empower you to work with fewer drills while achieving great results. Below find two tips, for more download the whitepaper:
- For irregular/rough hole entrance surfaces, use pre-operations, such as milling a flat, or reduce feed by 50% until the drill has reached full cut.
- Drilling a concave part surface requires that the part radius be five times larger than the drill and a reduced feed rate at point of entrance until drill has reached full cut.
- ...
Find more useful tips in our White paper
Watch our webinar "How to unleash your drilling potential"
Discover the Frequently Asked Question with Seco's Experts
Speak to our team today, and start realising your machine’s full potential tomorrow.
Get in touch with us and ask your questions
HOMERelated content
Seco Universal - Single-Diameter Drills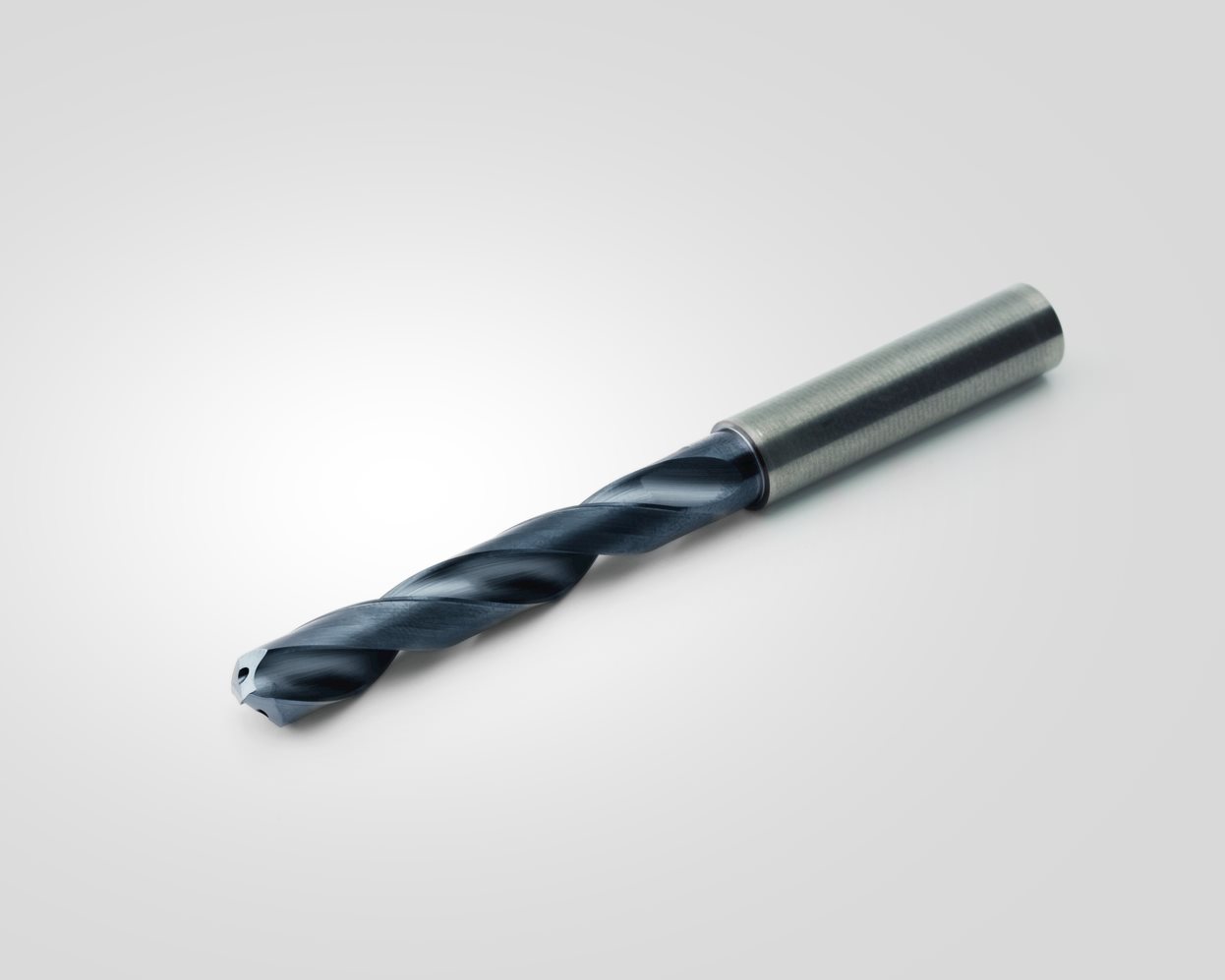
Seco X-Tra Long Solid Carbide Drills – 40xD-60xD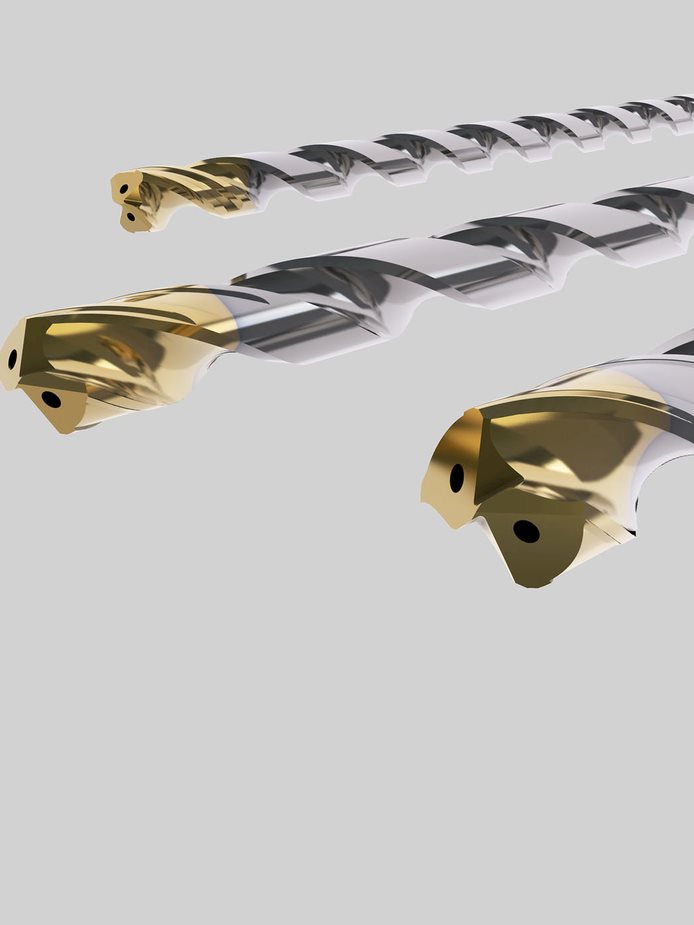
Optimize Multi-Task Machining Coolant And Results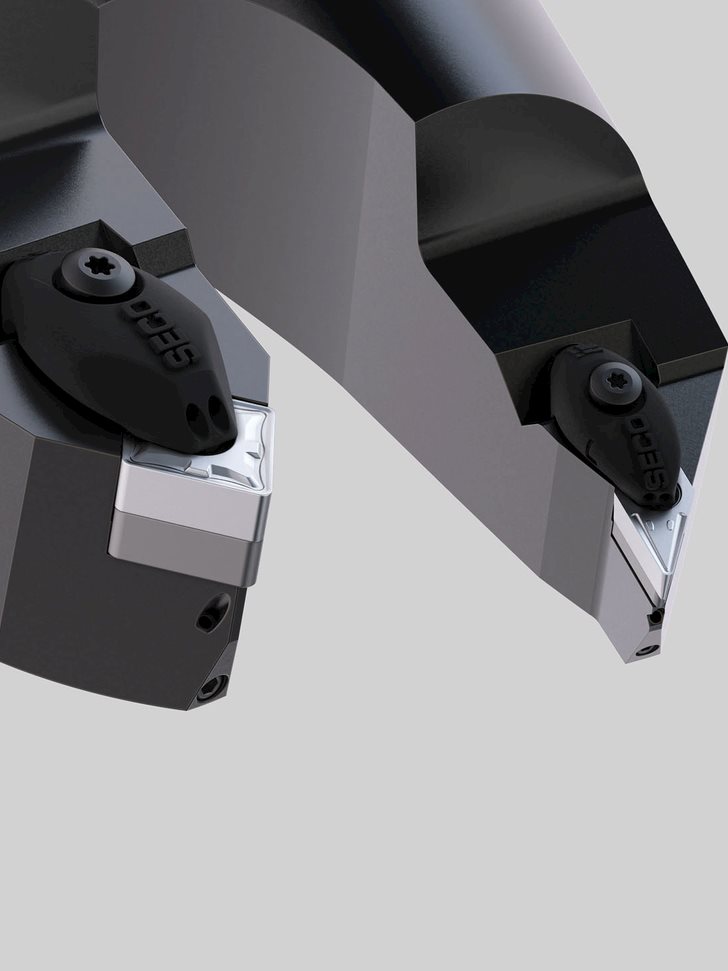
Seco CH1050/CH2581 PCBN Hard Part Turning Inserts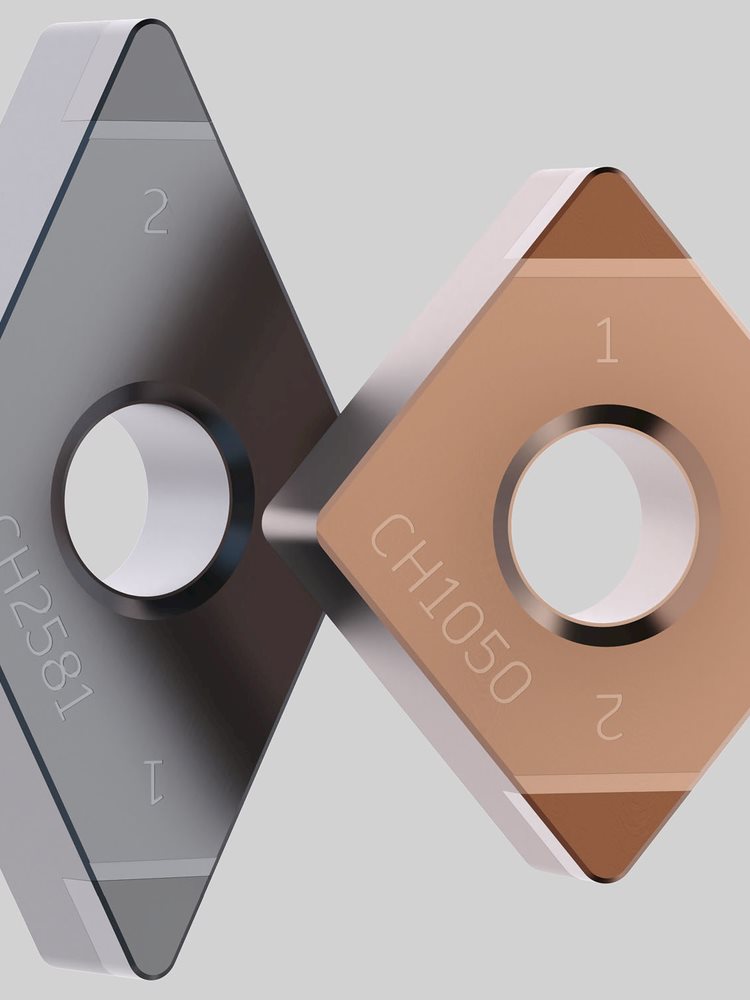
MF2 Chipbreaker on Round RCMT/RCGT Inserts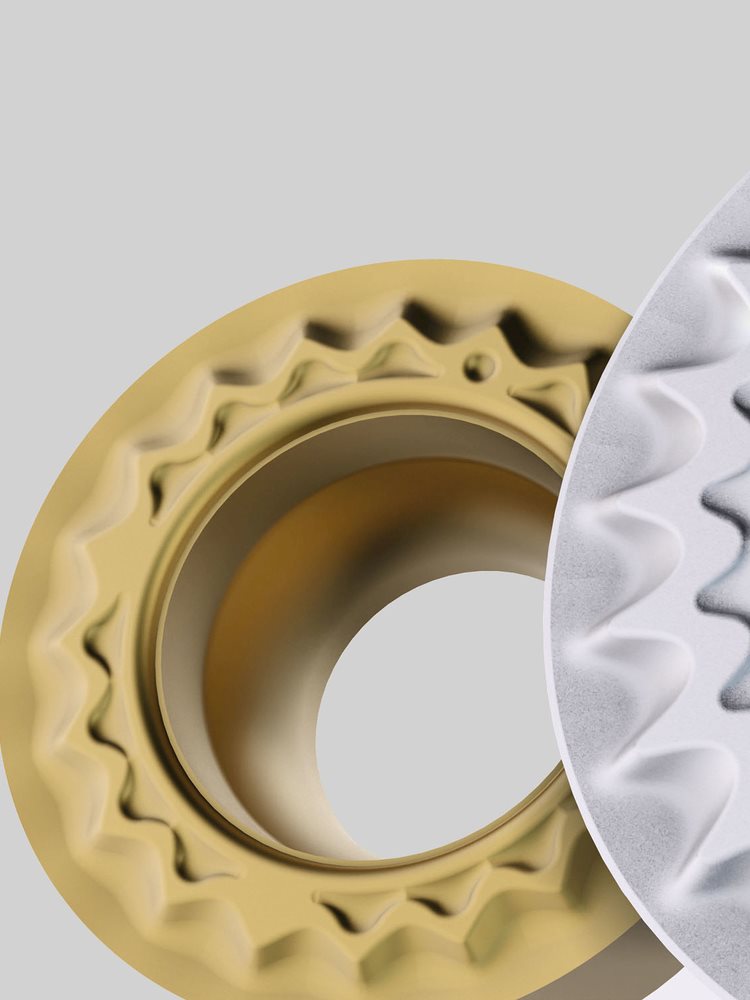
The Right Drill to Achieve Holemaking Production Goals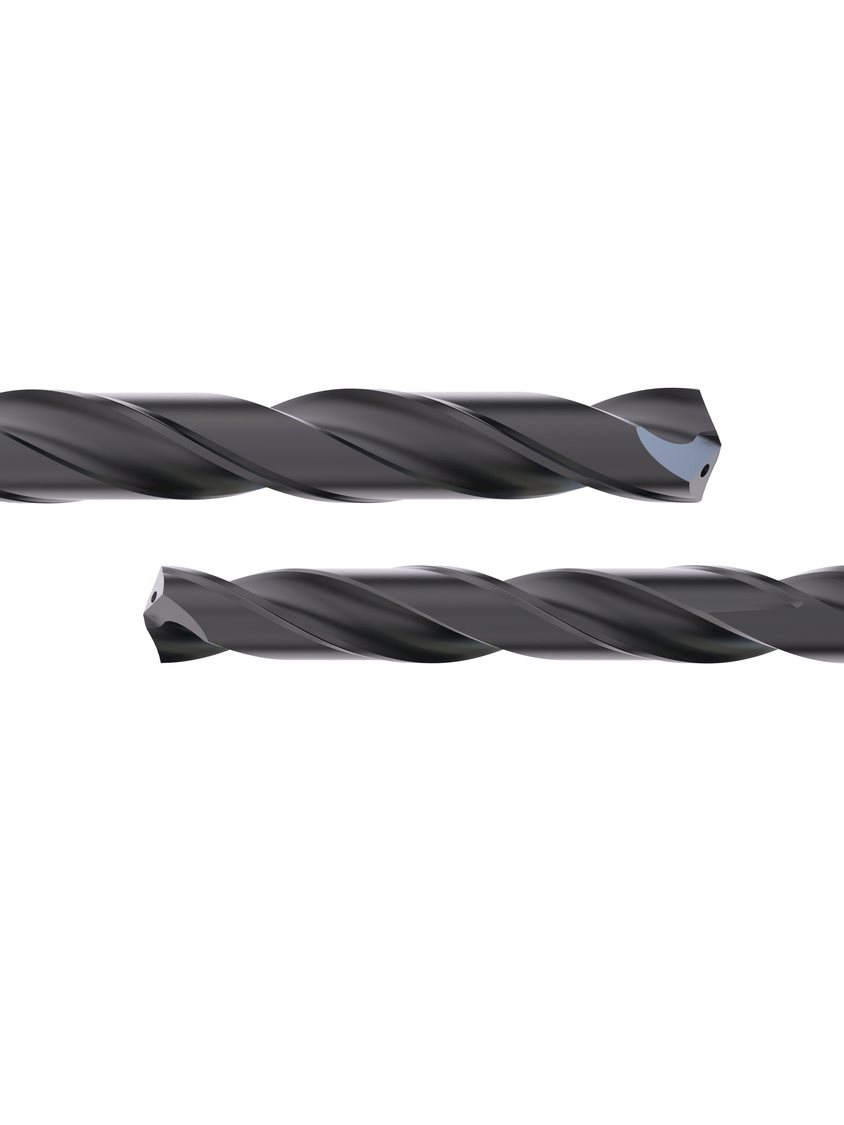
Webinar - How to unleash your drilling potential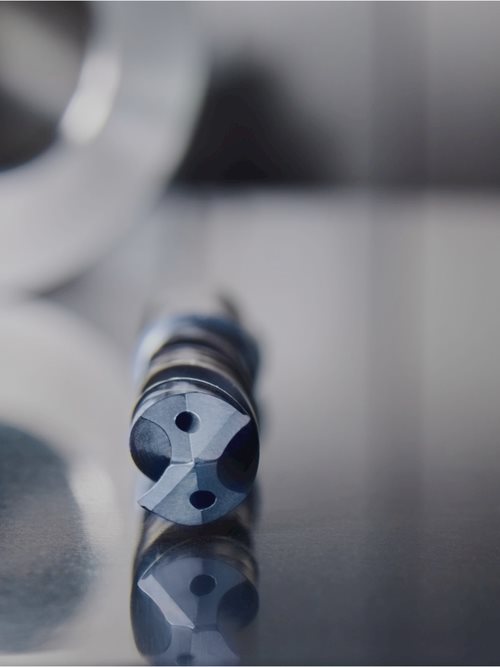
Drilling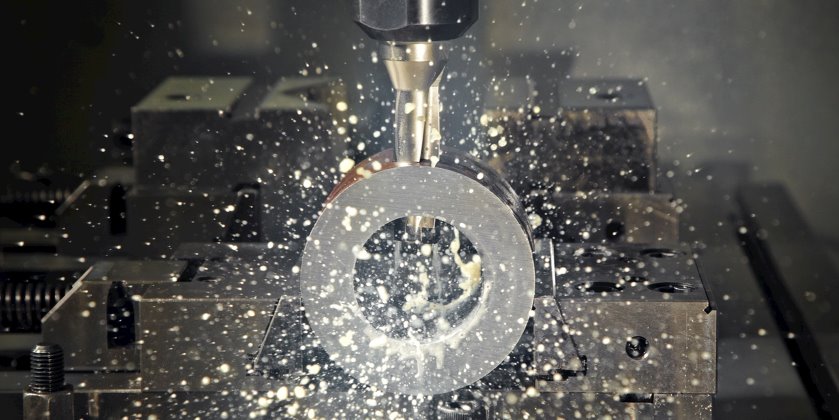
Seco Nanojet Reamers: reliable precision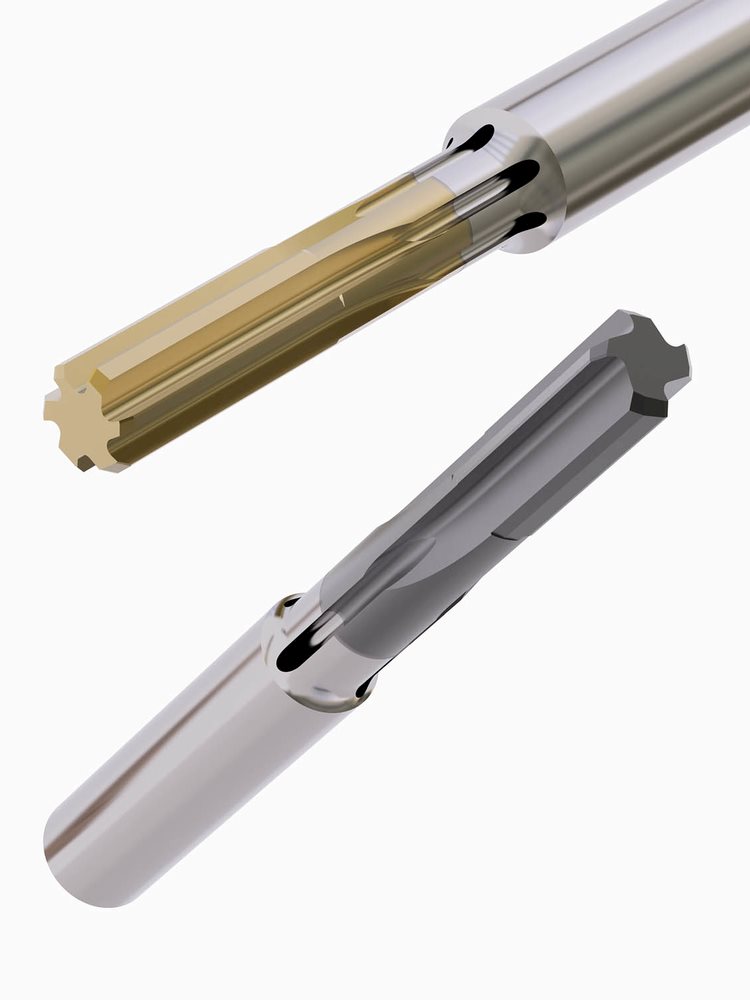
JS720 Solid End Mills addition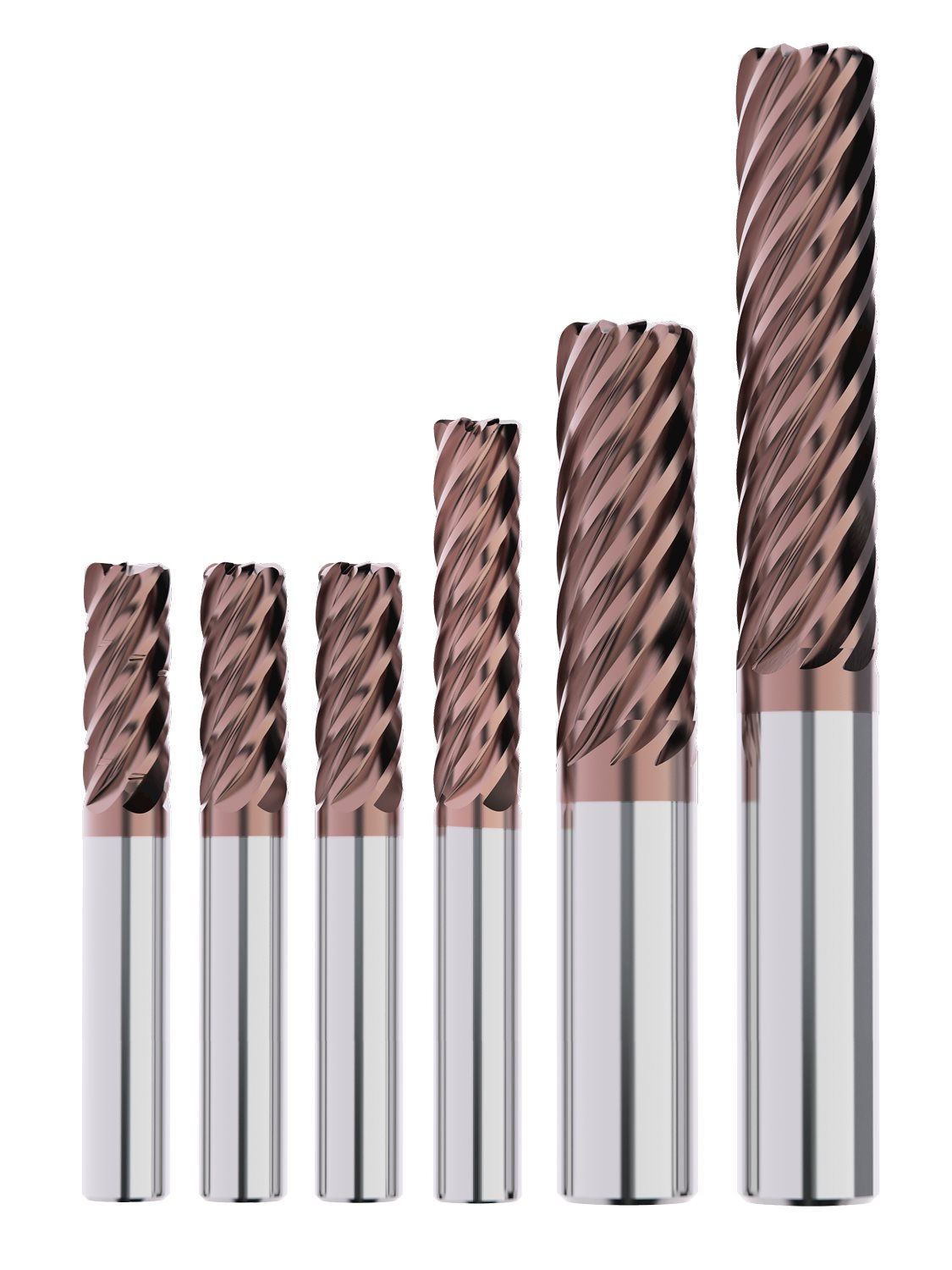
Seco Digital Tool Assembly: quick, accurate data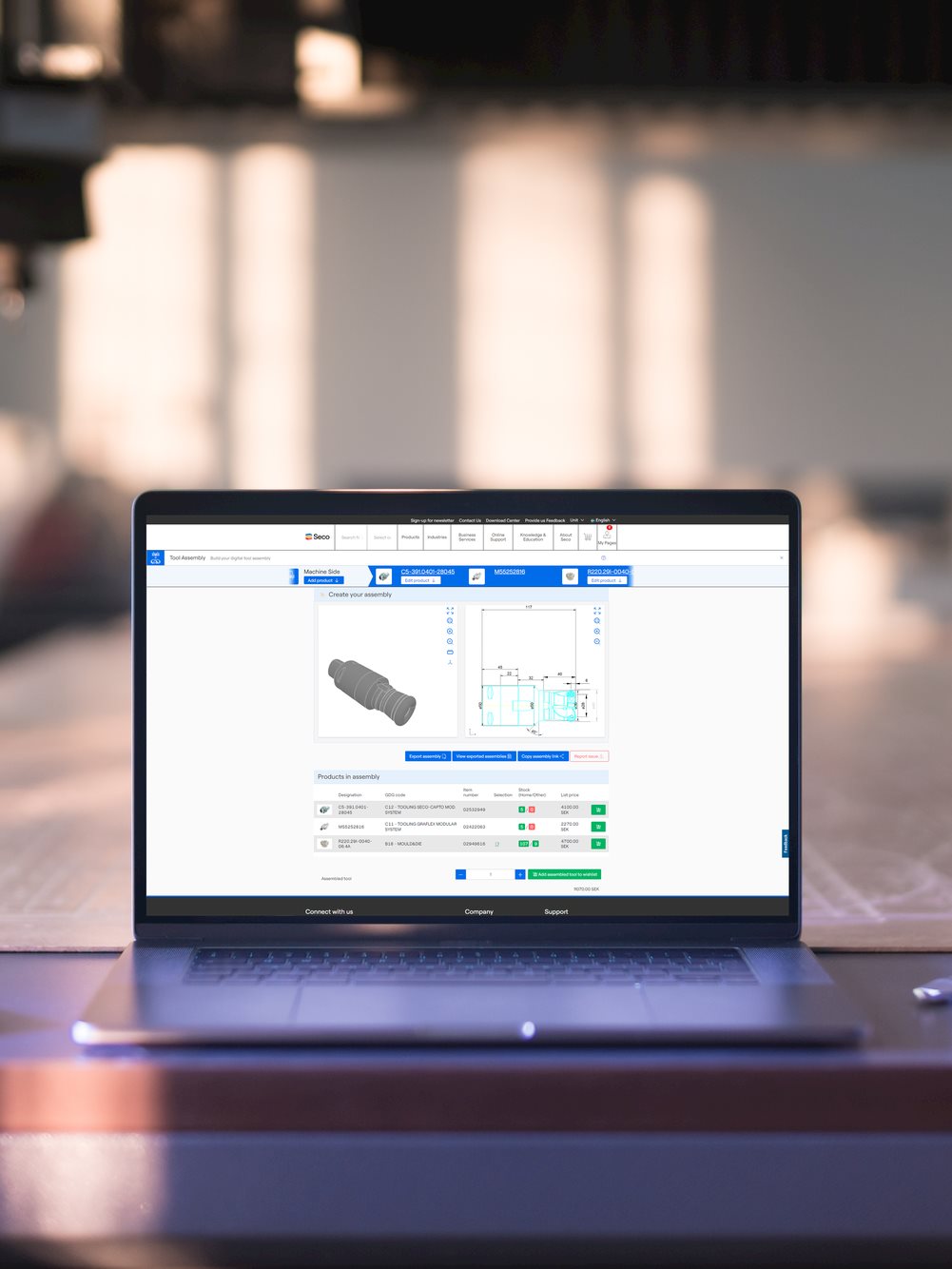
Easy setup with Seco Digital Axial Boring Heads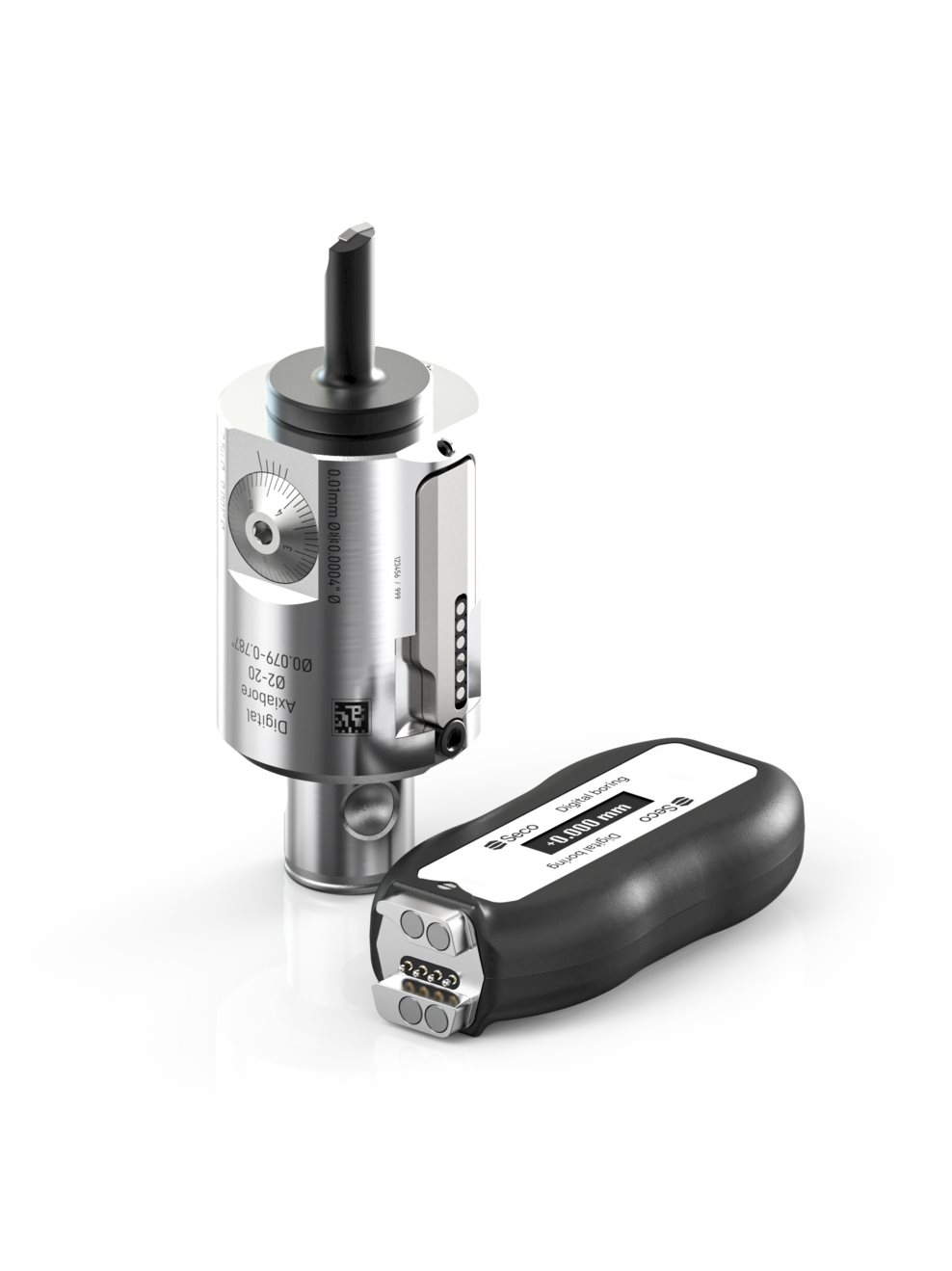
JH730 Solid End Mills addition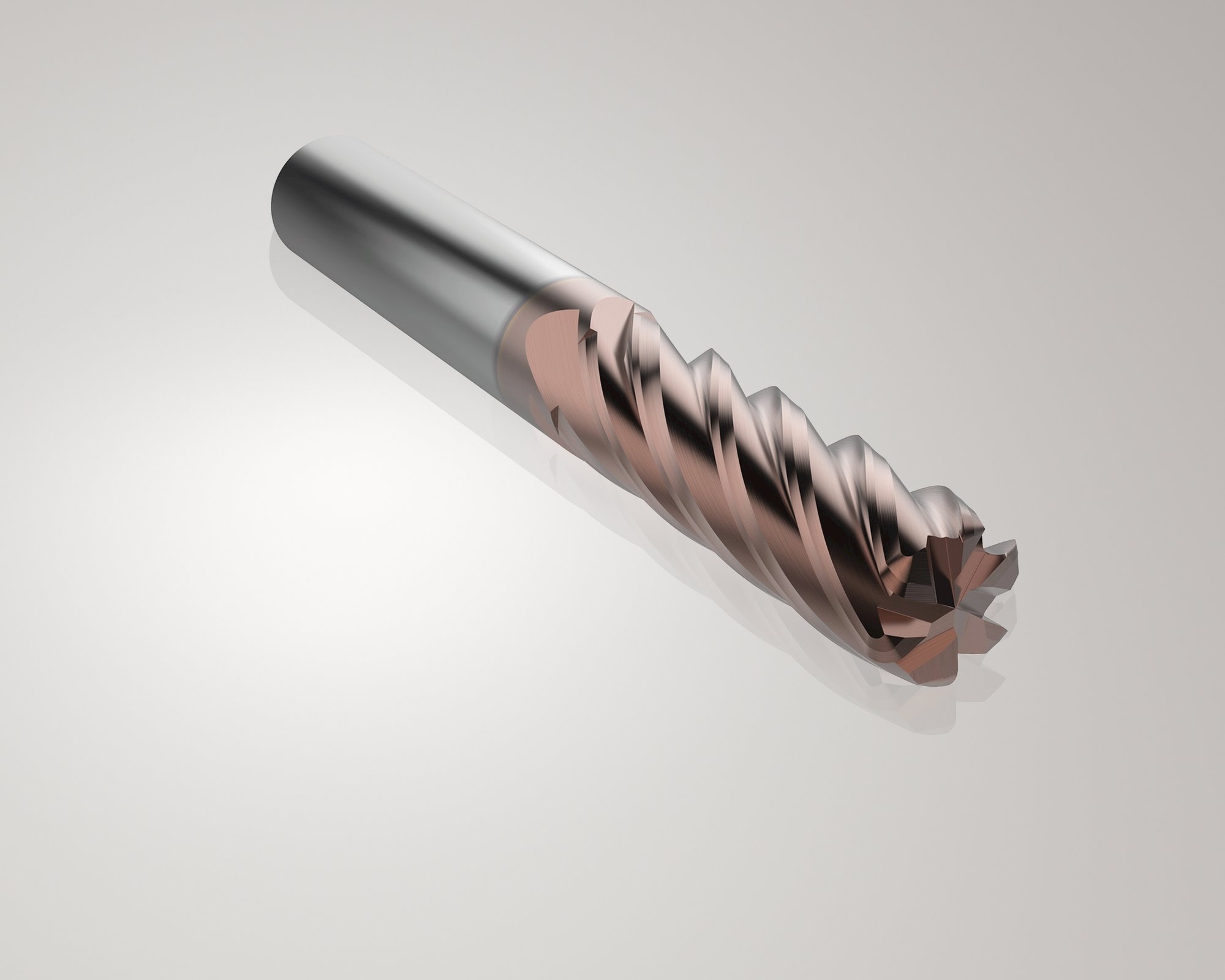
Square T4-12 Upgrades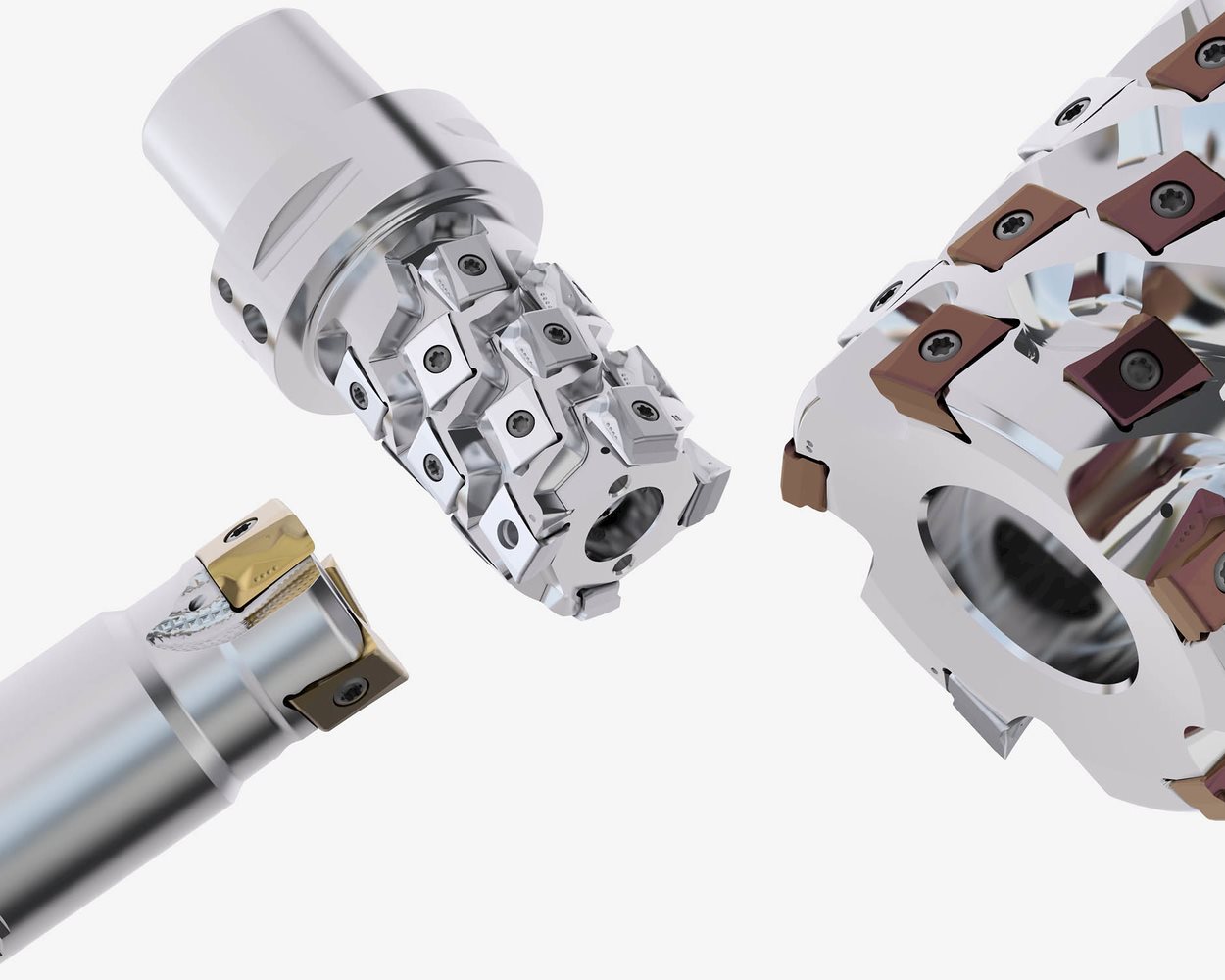
TURBO 16 SQUARE SHOULDER MILLING CUTTERS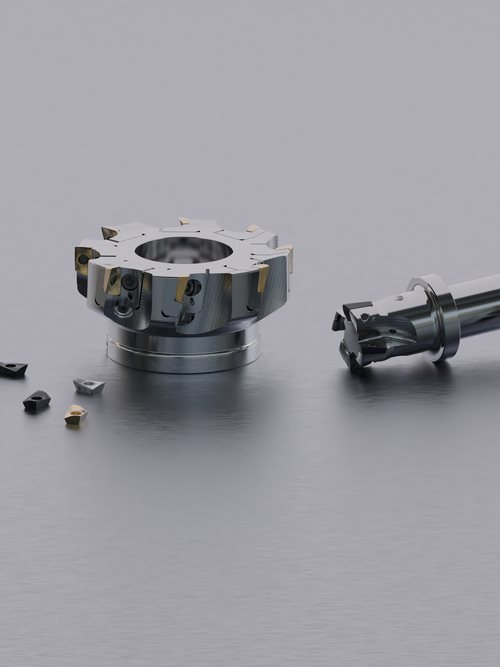
Drilling Application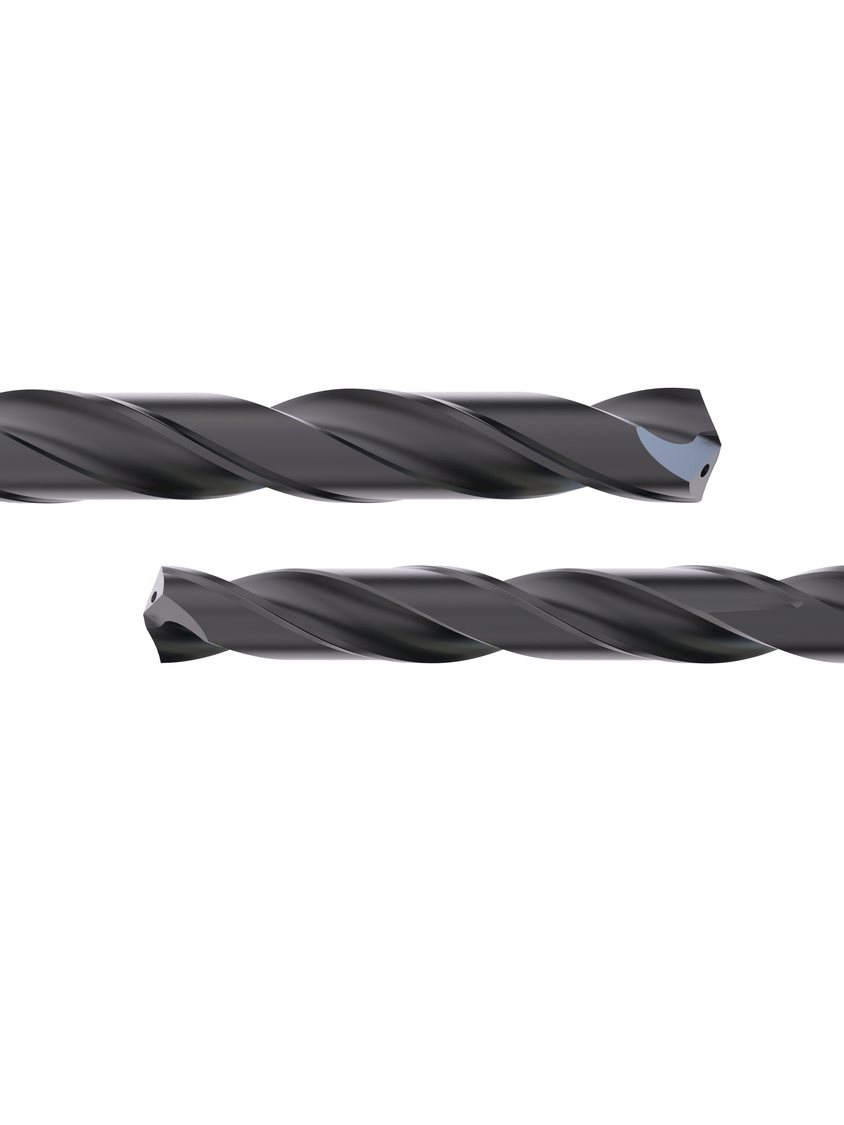
Seco launches innovative solutions for optimized part processing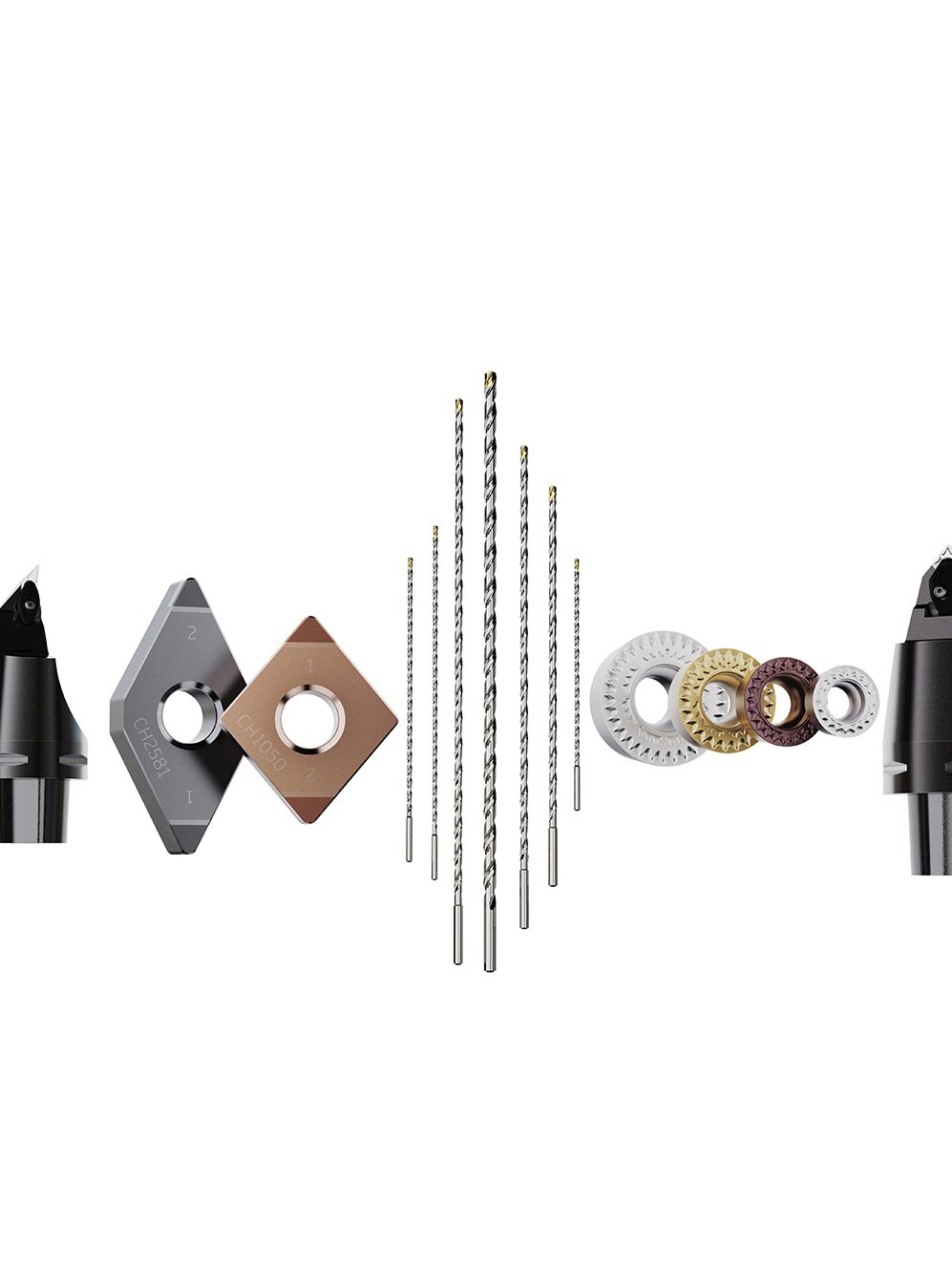
Unleash your drilling potential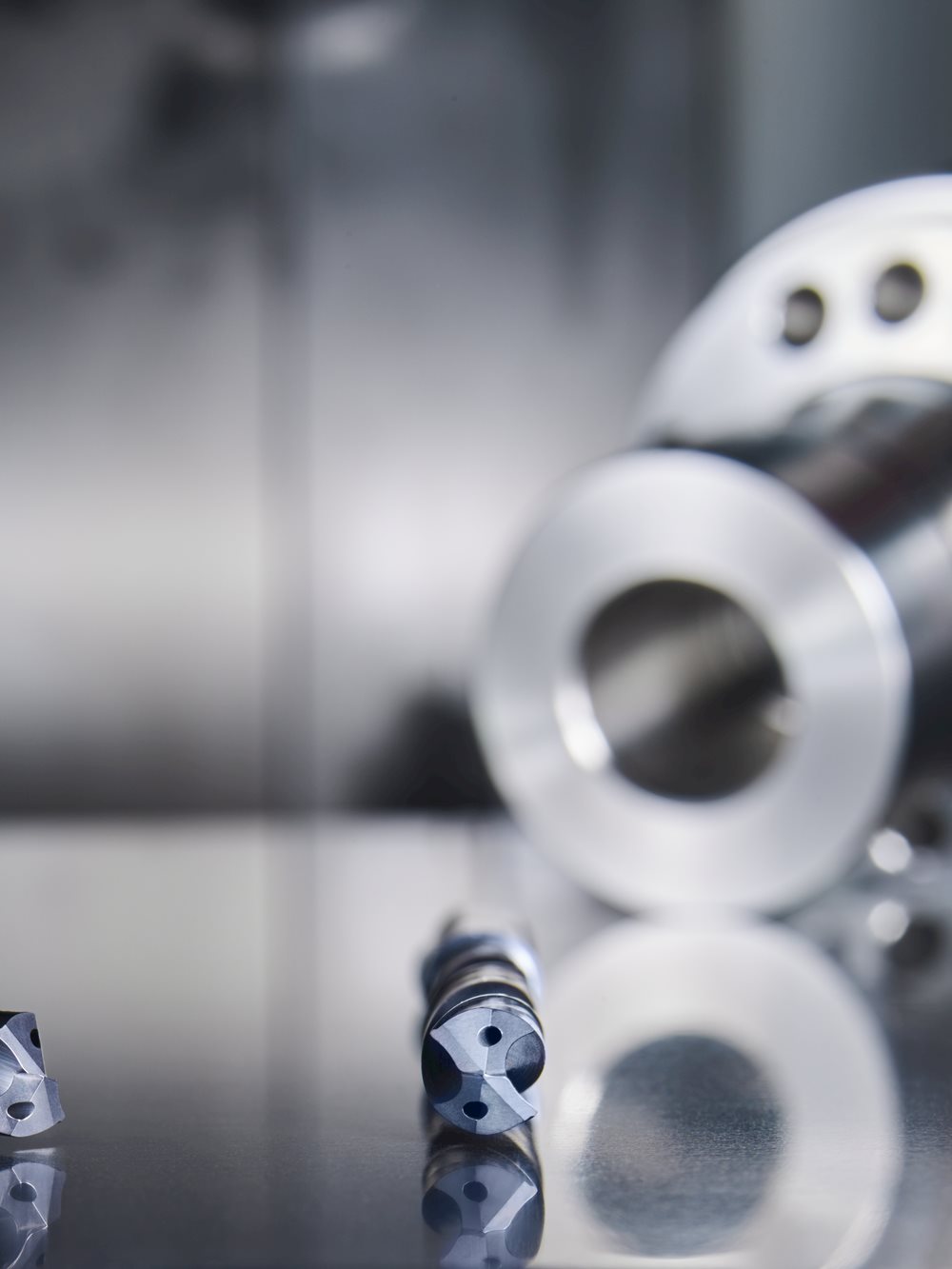
Seco Component Guidance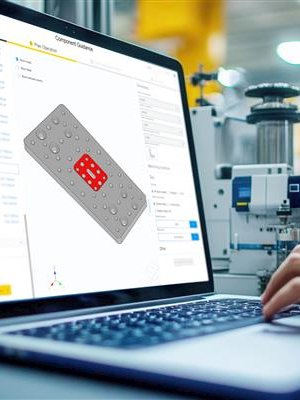
Versatile Round 20 Inserts Increase Tool Life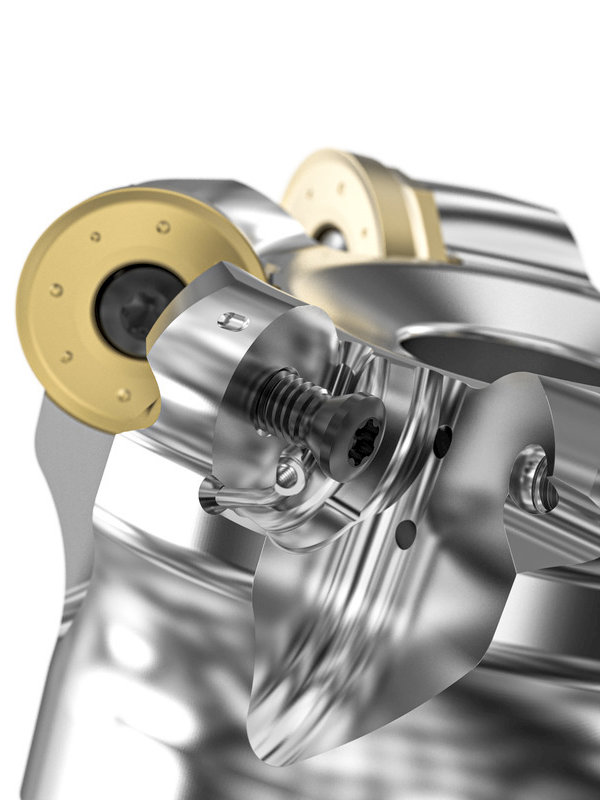
Seco Octomill™ 06: Flexible, Robust Tooling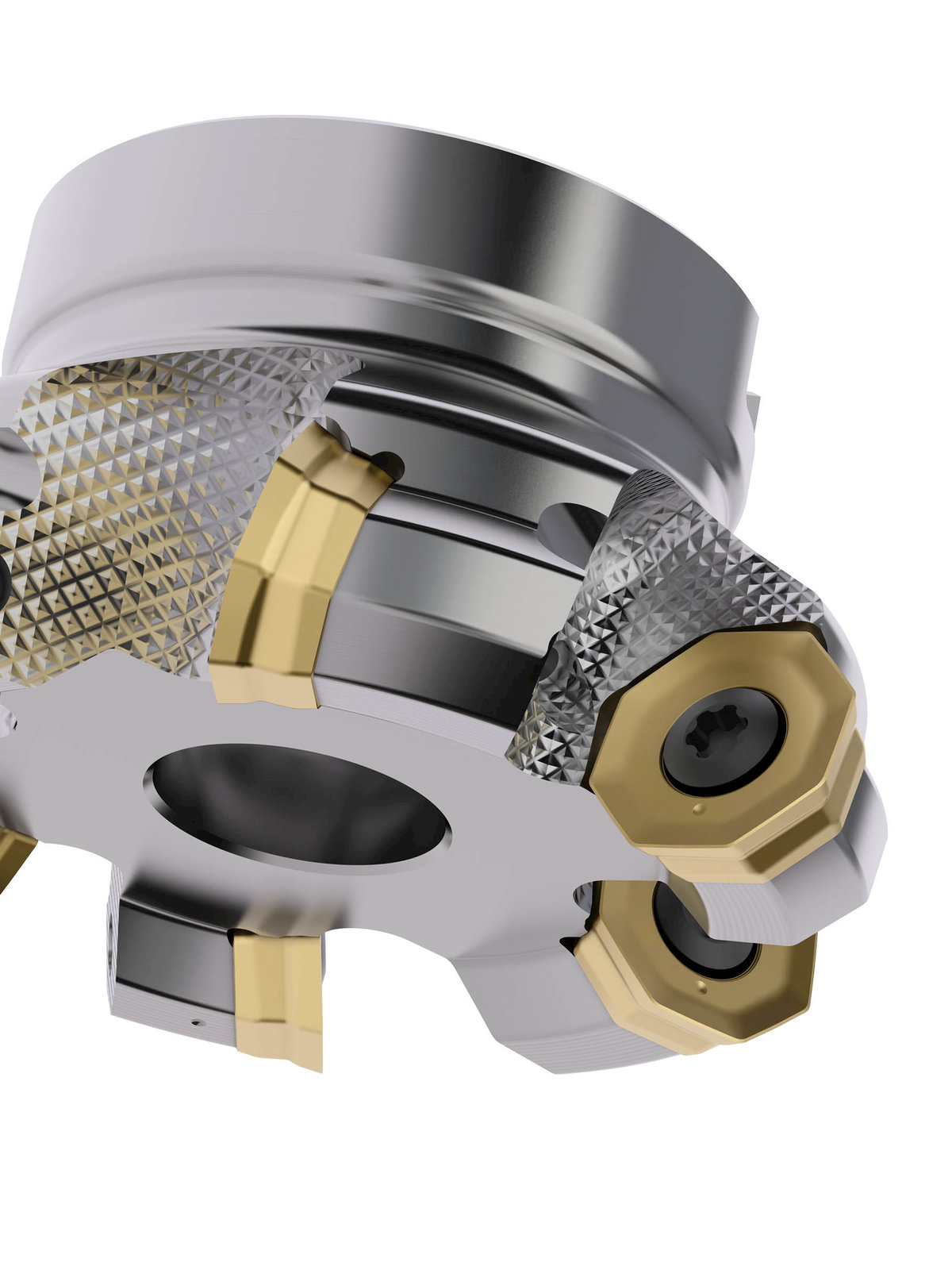
Seco Stabilizer Series: Unmatched Metal Removal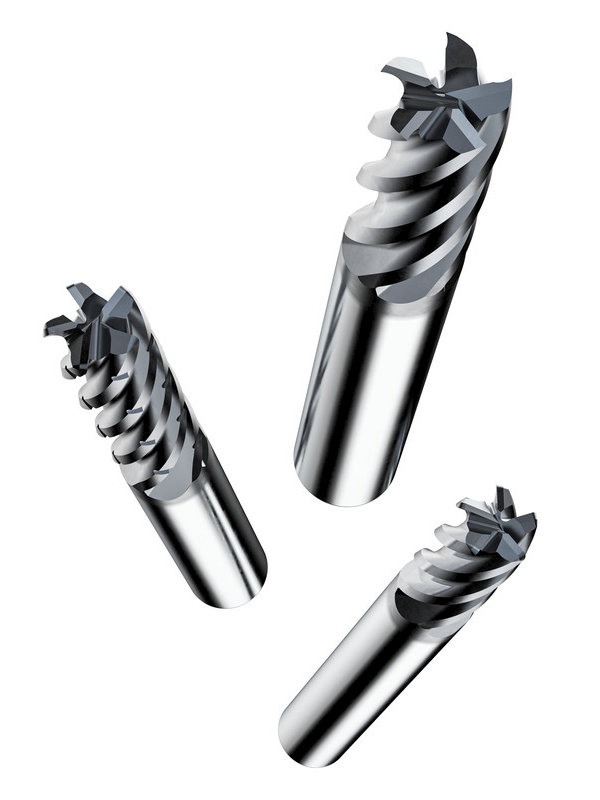
335.14 Disc Milling Cutter extension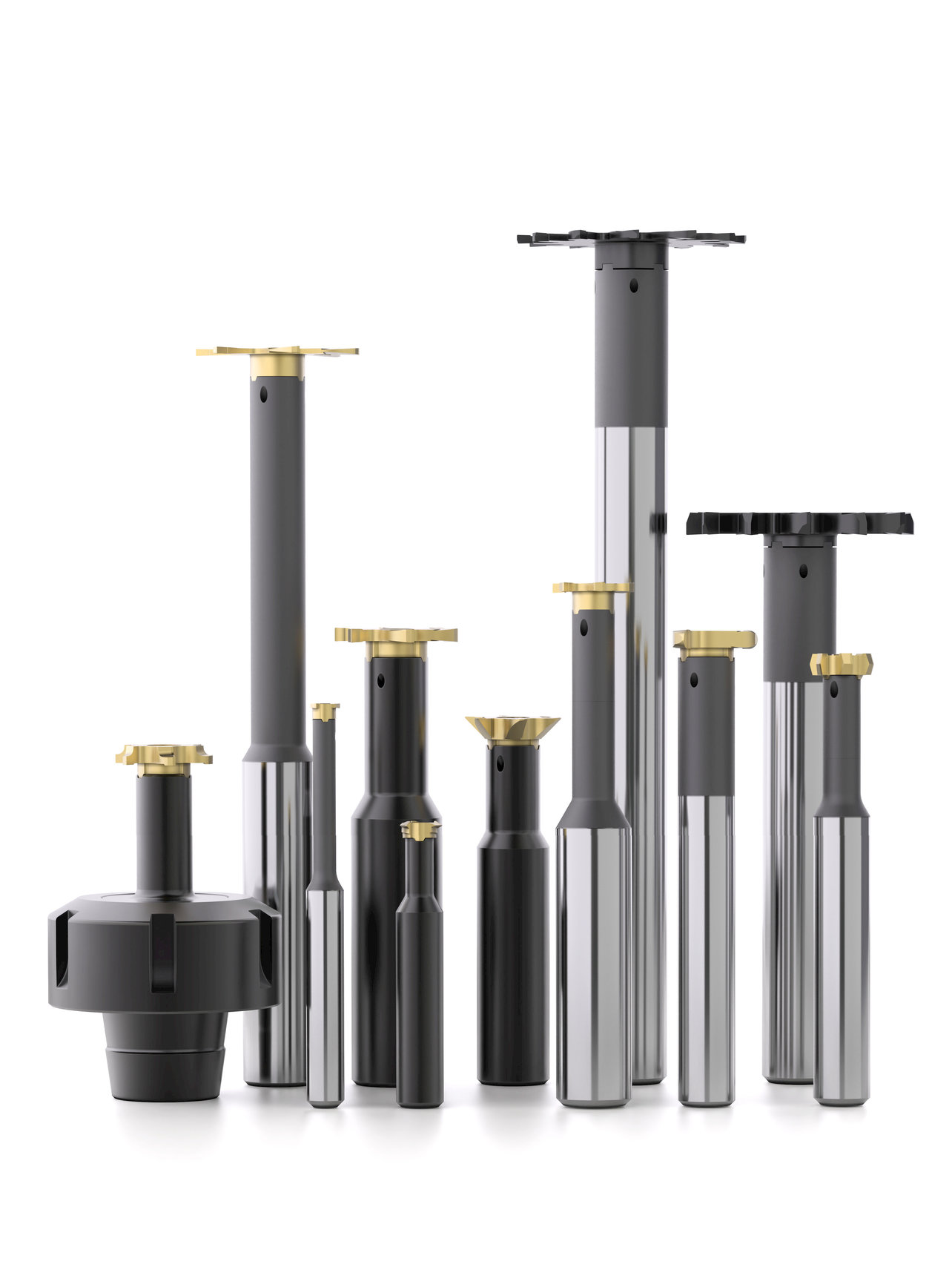
Seco T30 Taps: a versatile universal geometry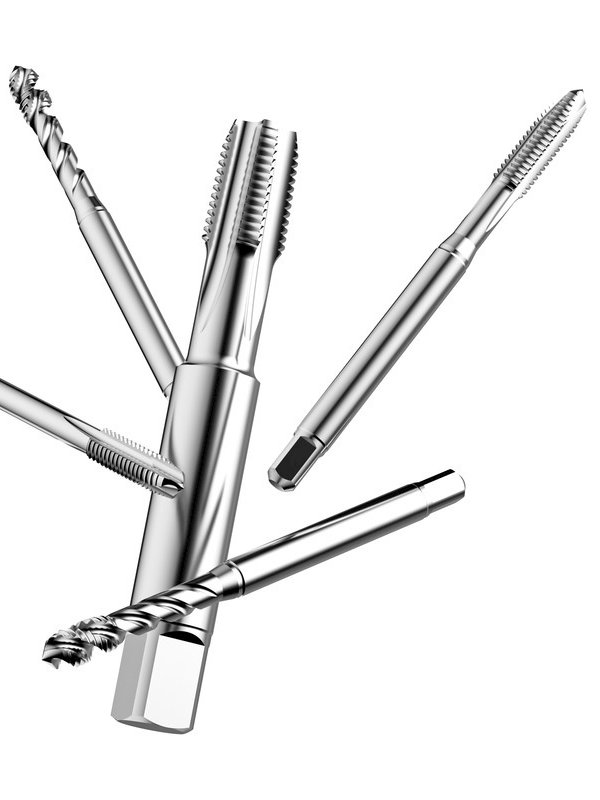
Seco 335.98 Disc Milling Cutter system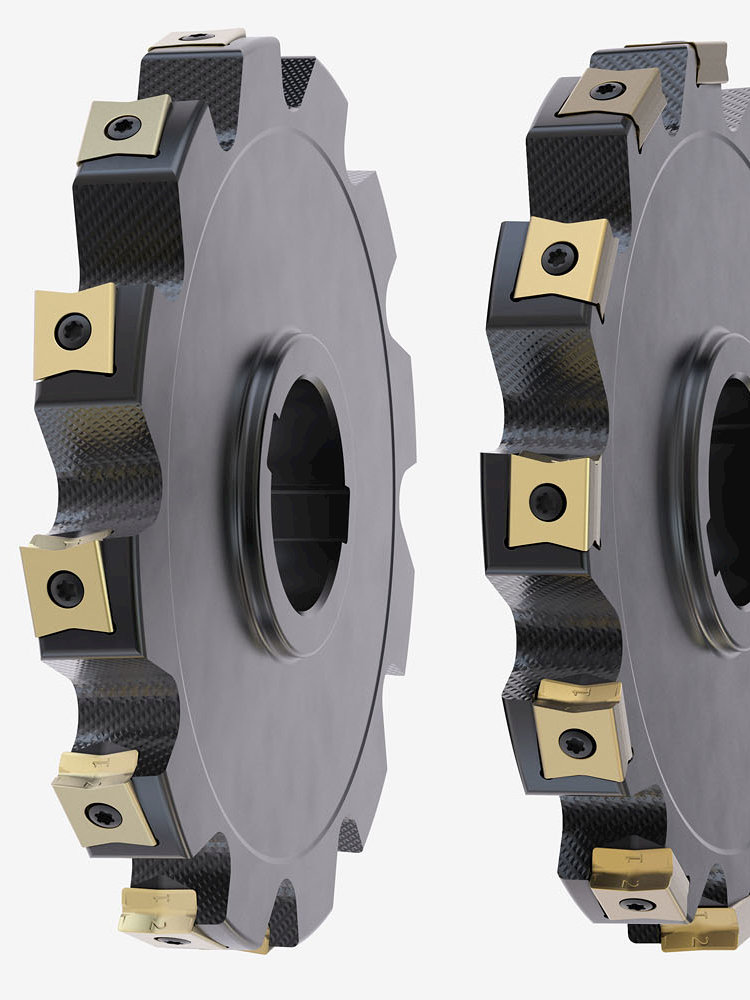
Seco My Design: Design custom tools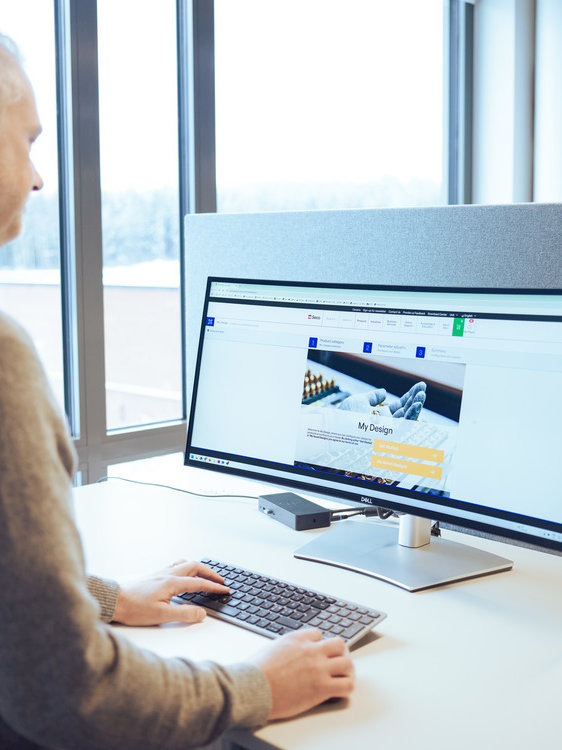
Seco Machine Library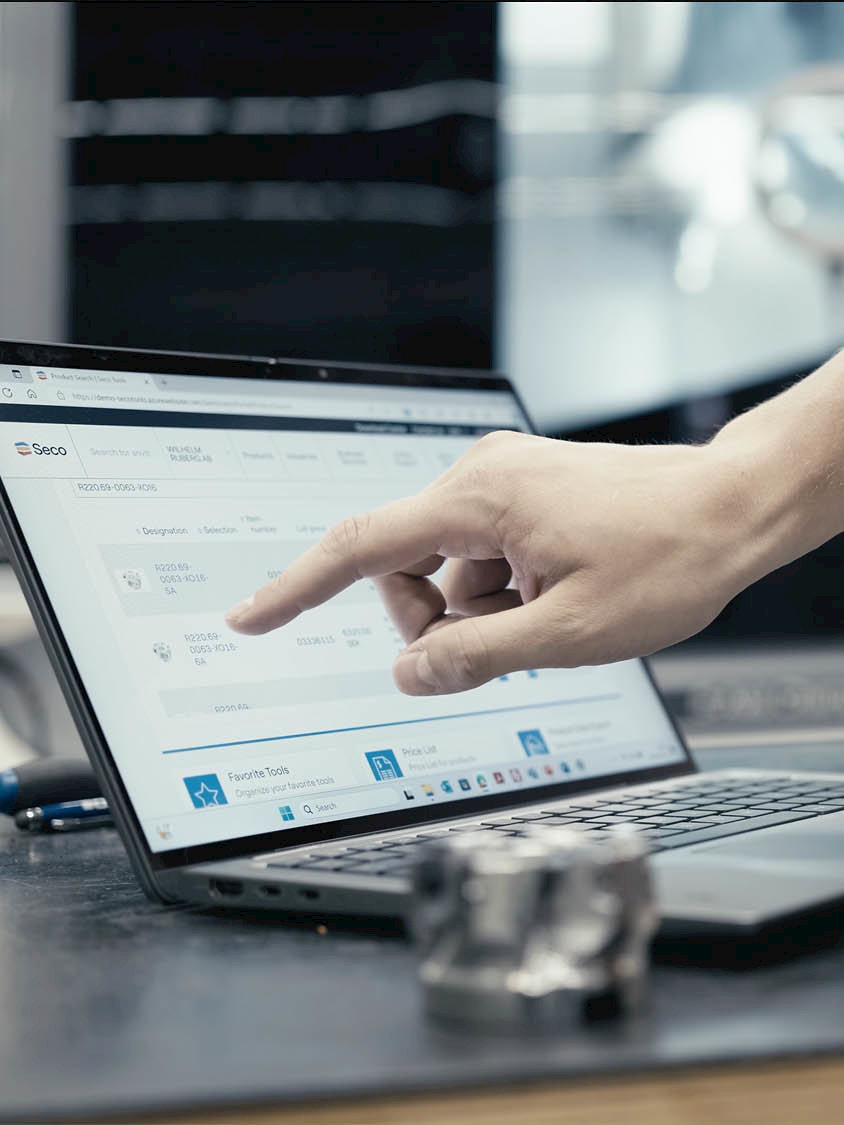
Seco T35 Taps: match Tooling to Materials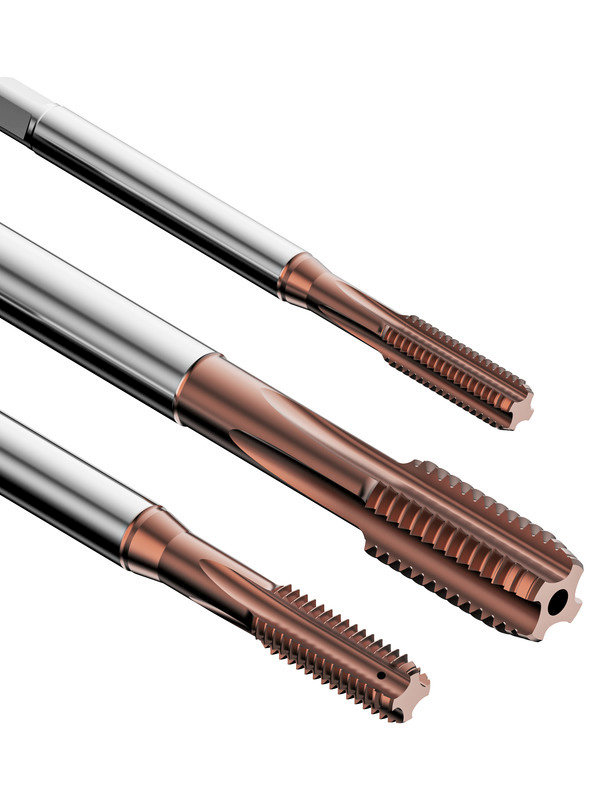
Seco X-Head Exchangeable End Mill System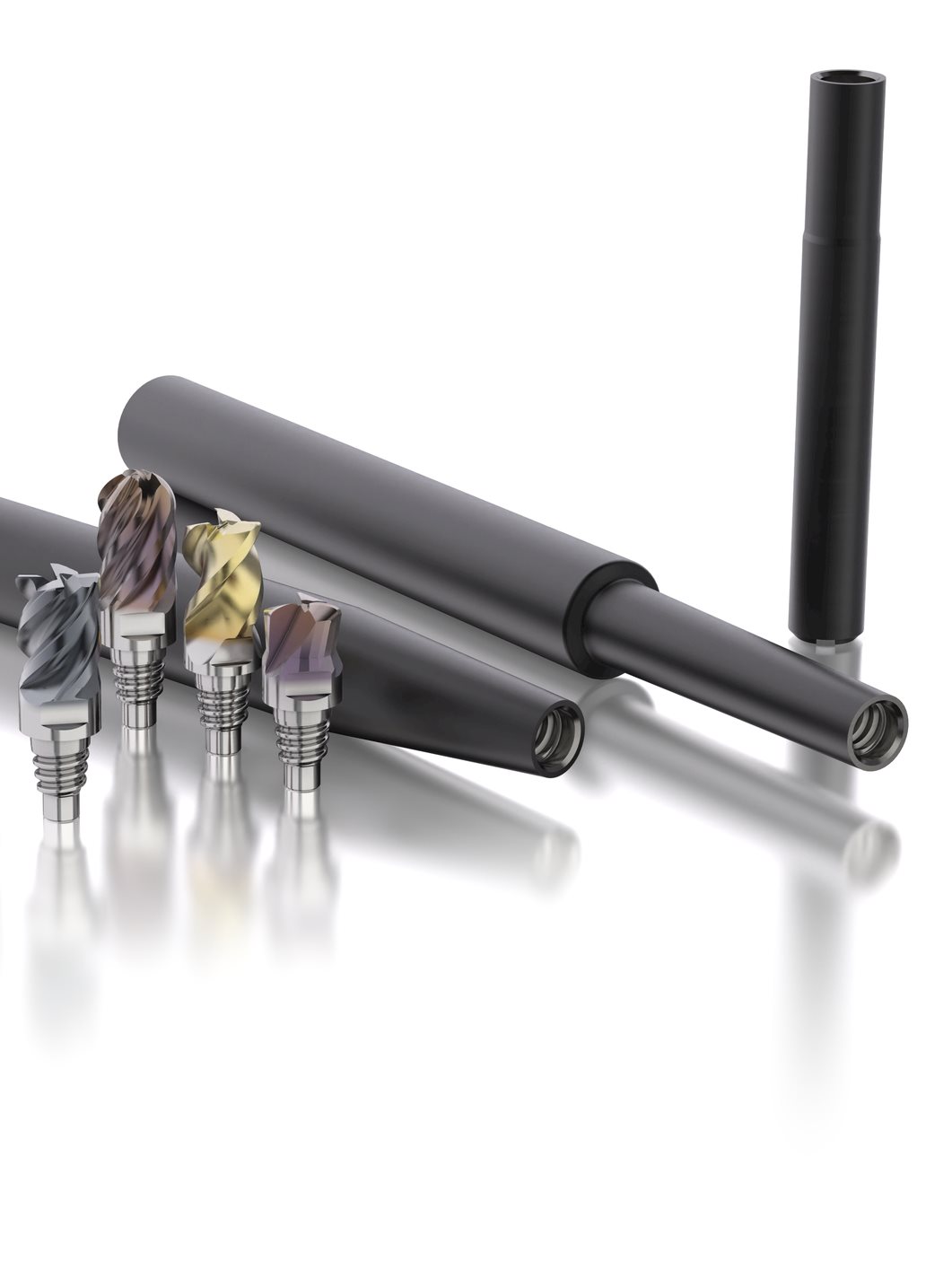
Seco Helical LN4-11 Milling Cutter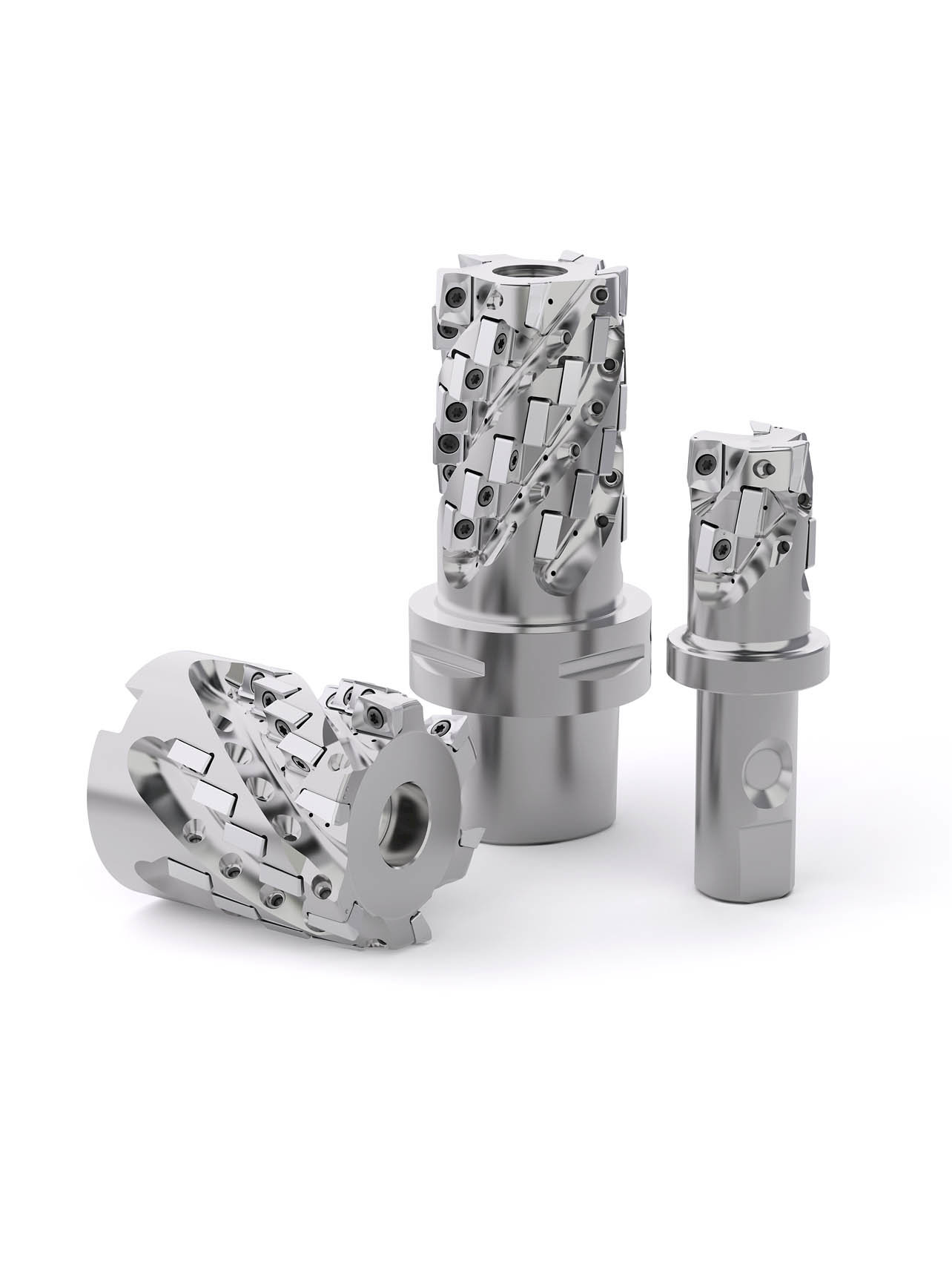
Guillaume Bourderon appointed Sales Unit Market Manager France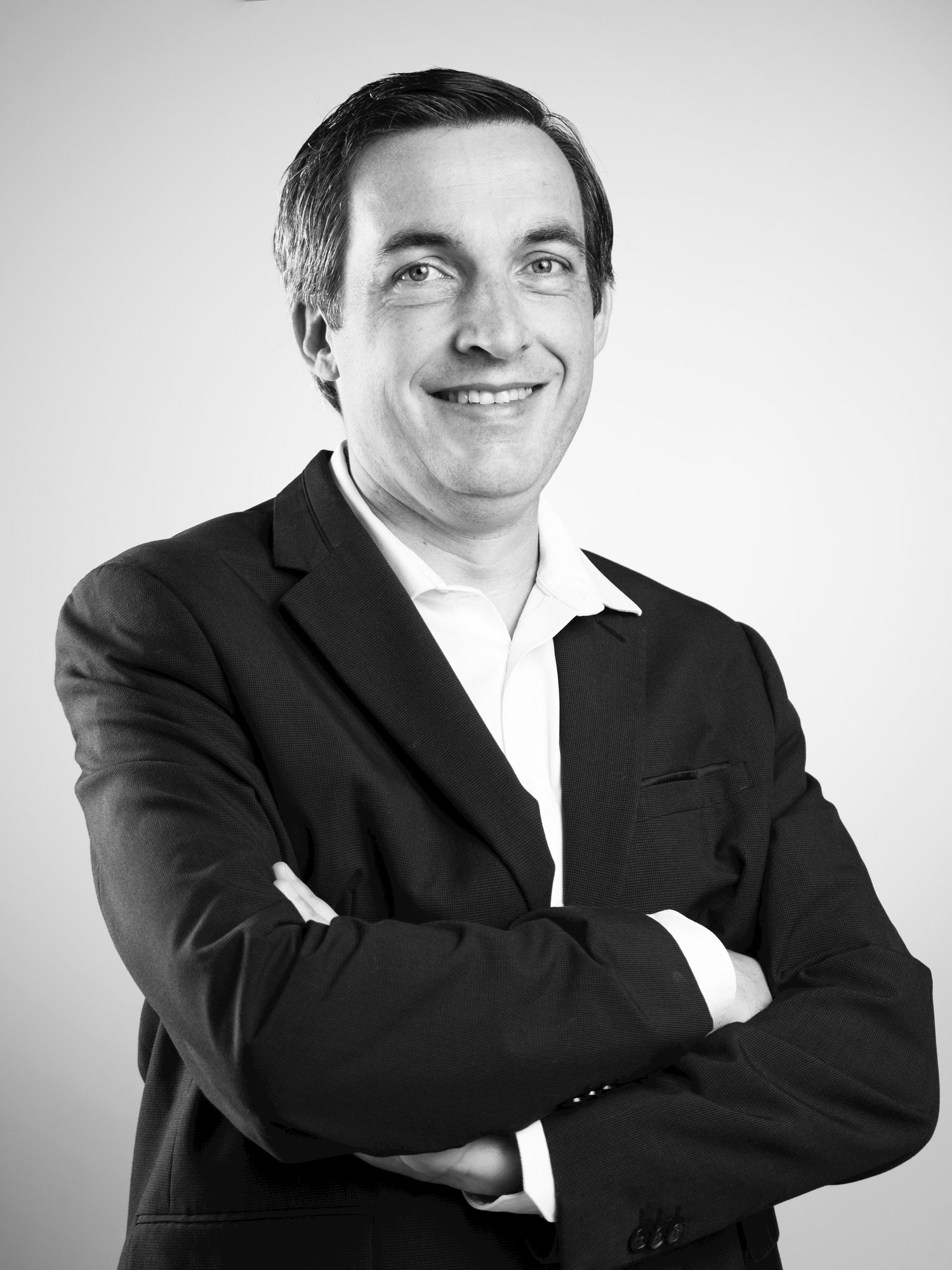
JETI CONVERSION GROOVING AND PARTING-OFF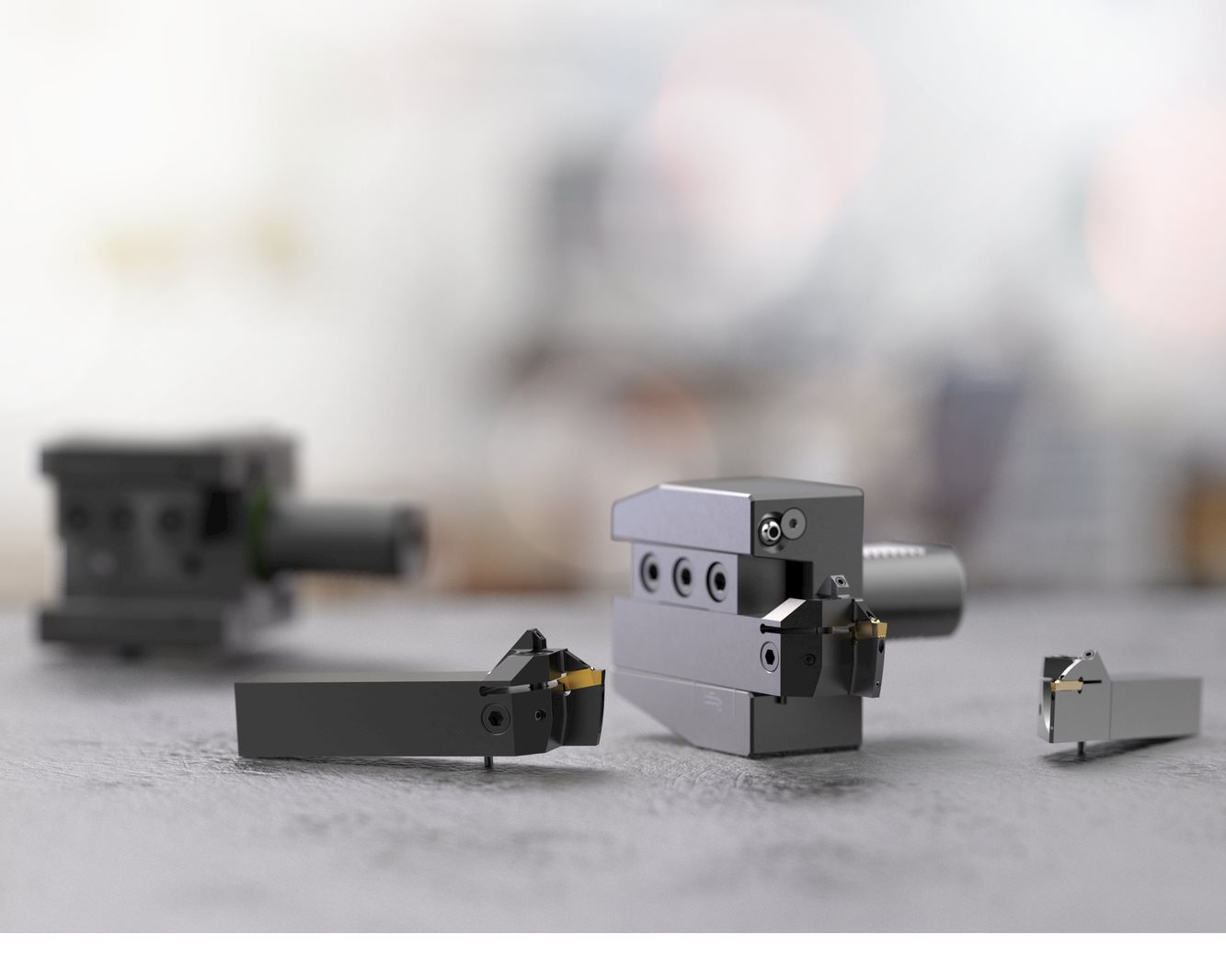
Seco X2 System for Small Part Machining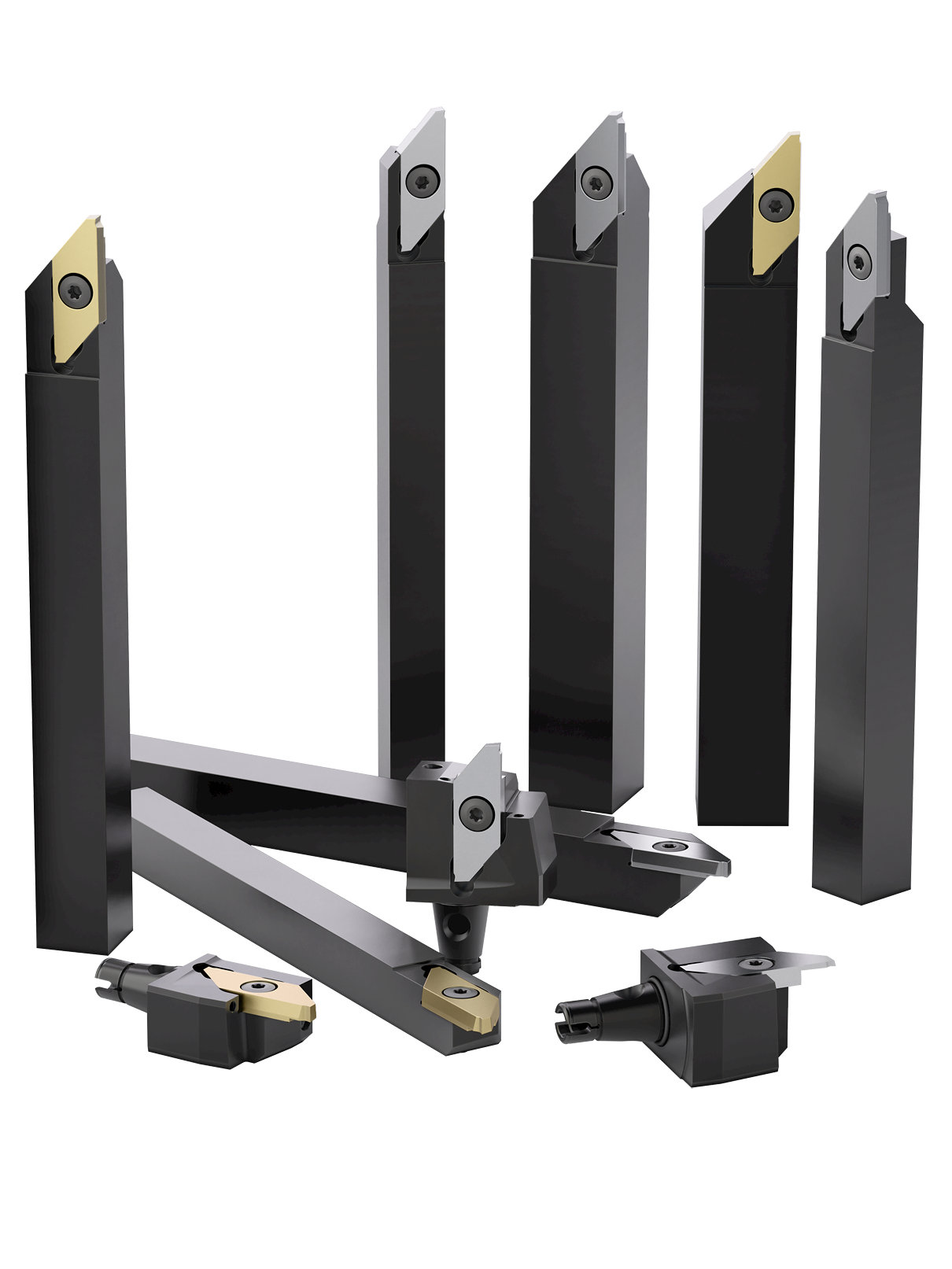
JETI Toolholder for RCMT/RCGT Turning Inserts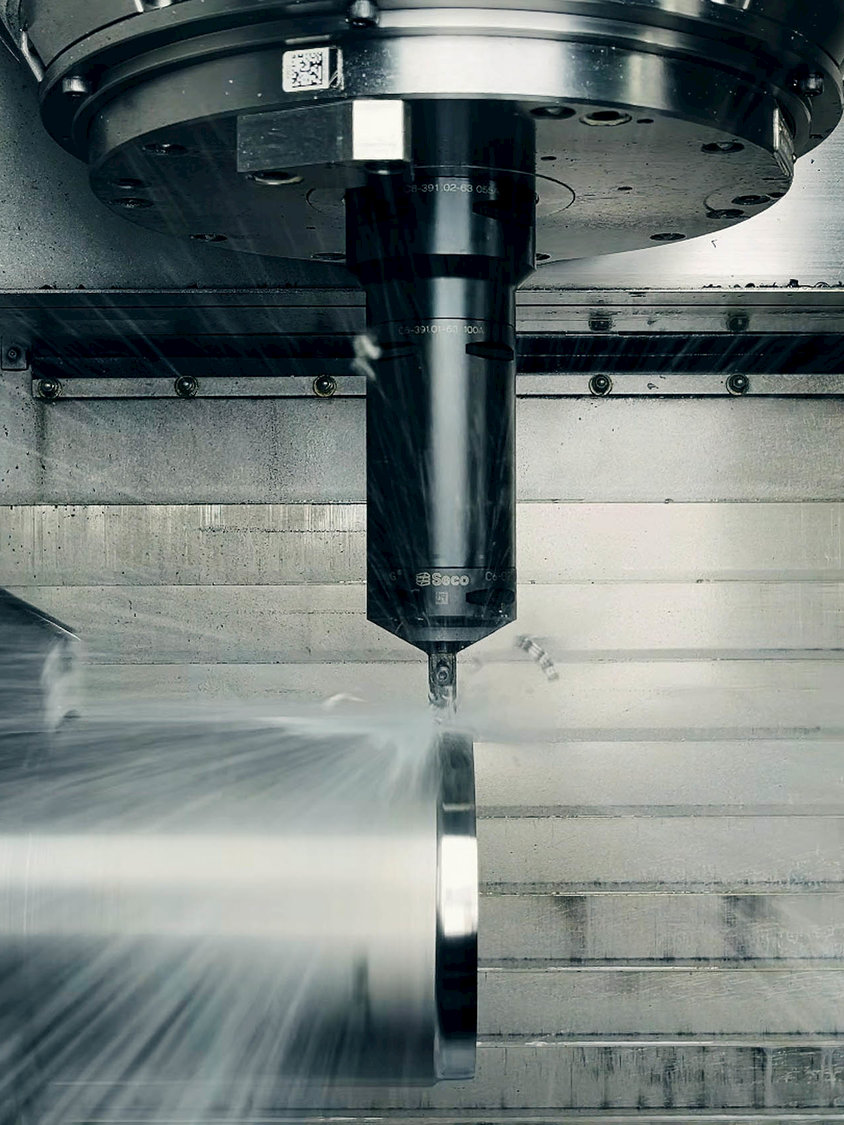
Seco S43/S45/S46 Solid End Mills for Aluminum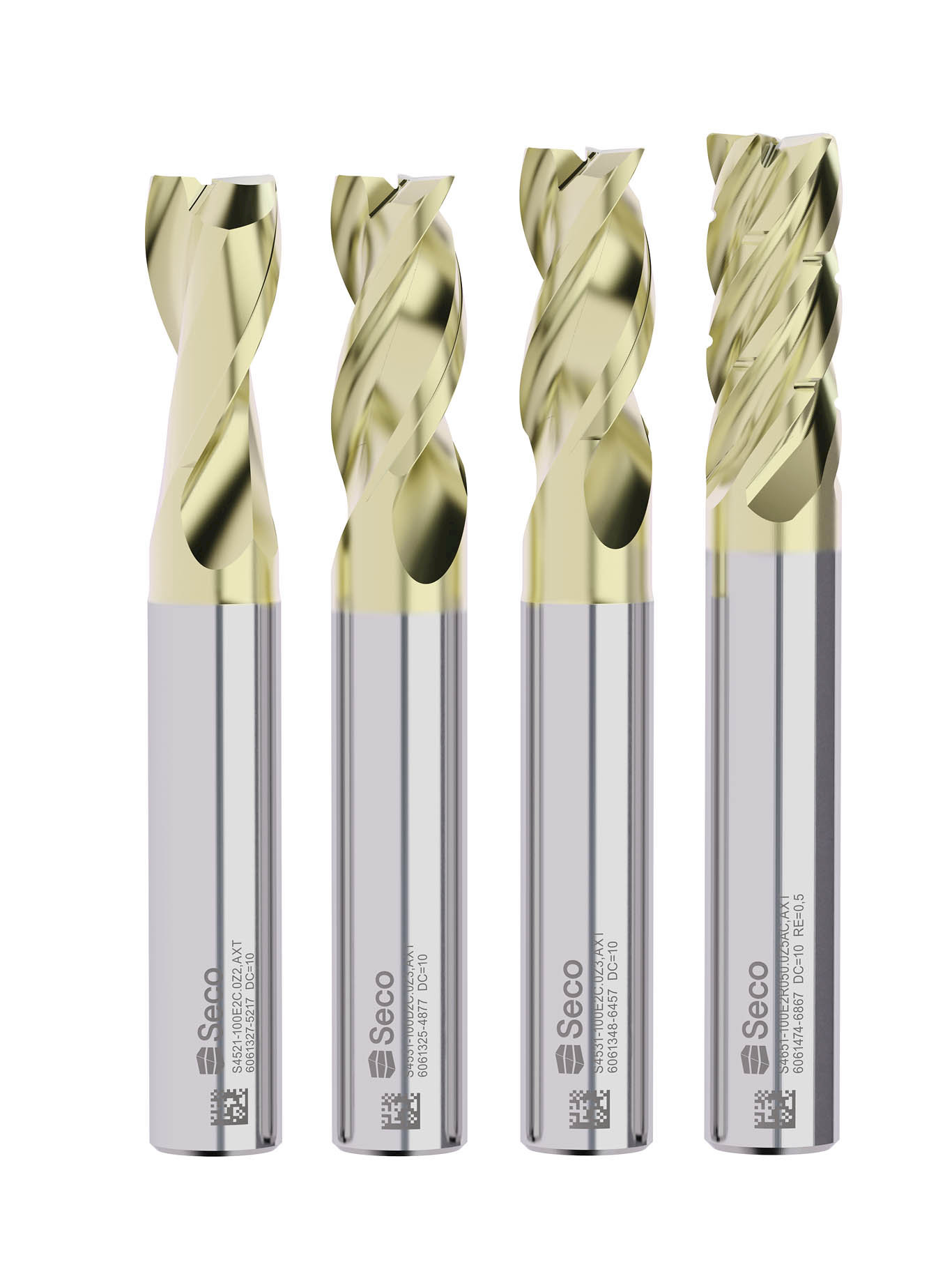
Turbo 12 & 18 Chip Splitter Inserts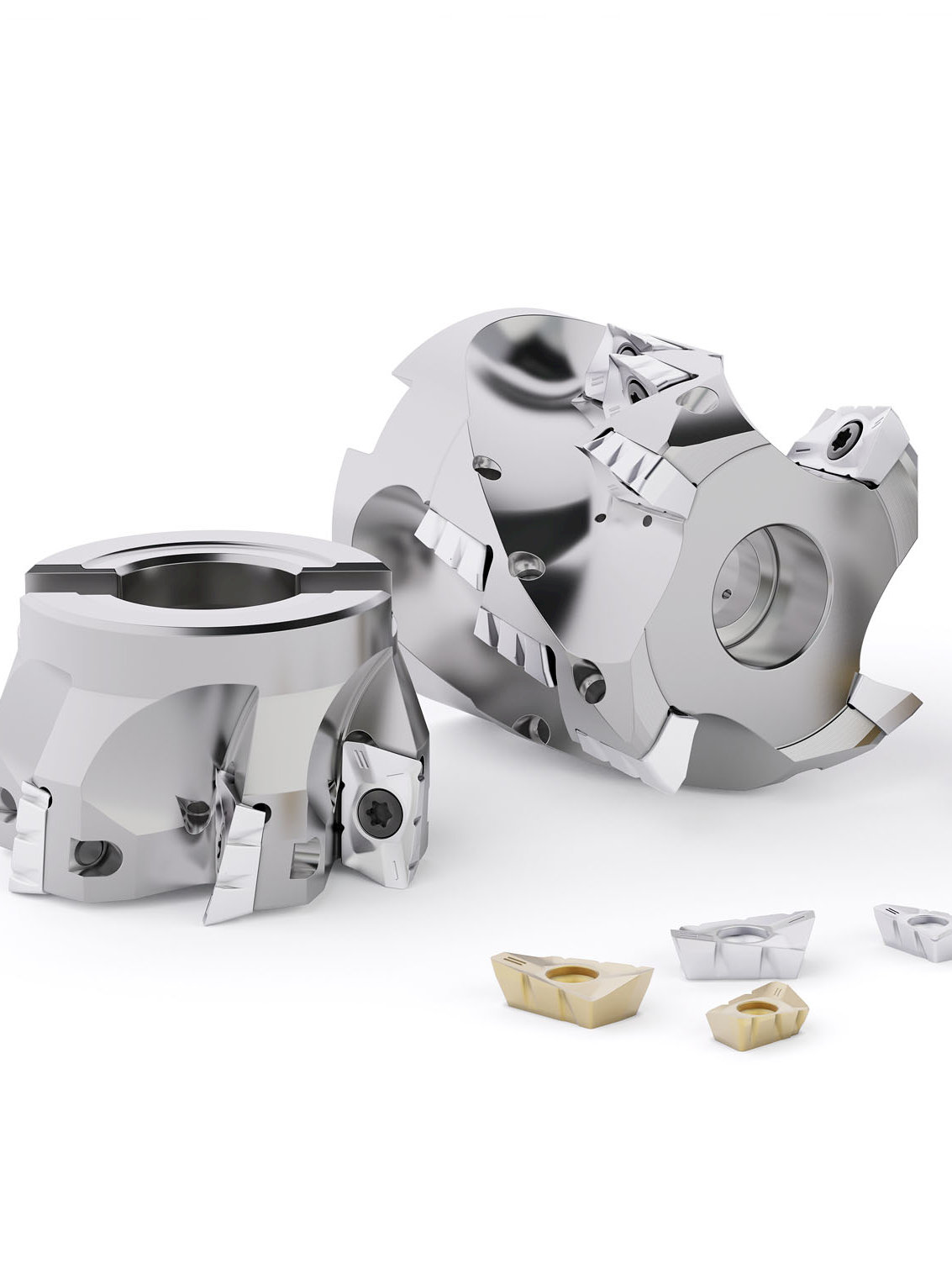
Seco C-Series General Purpose End Mills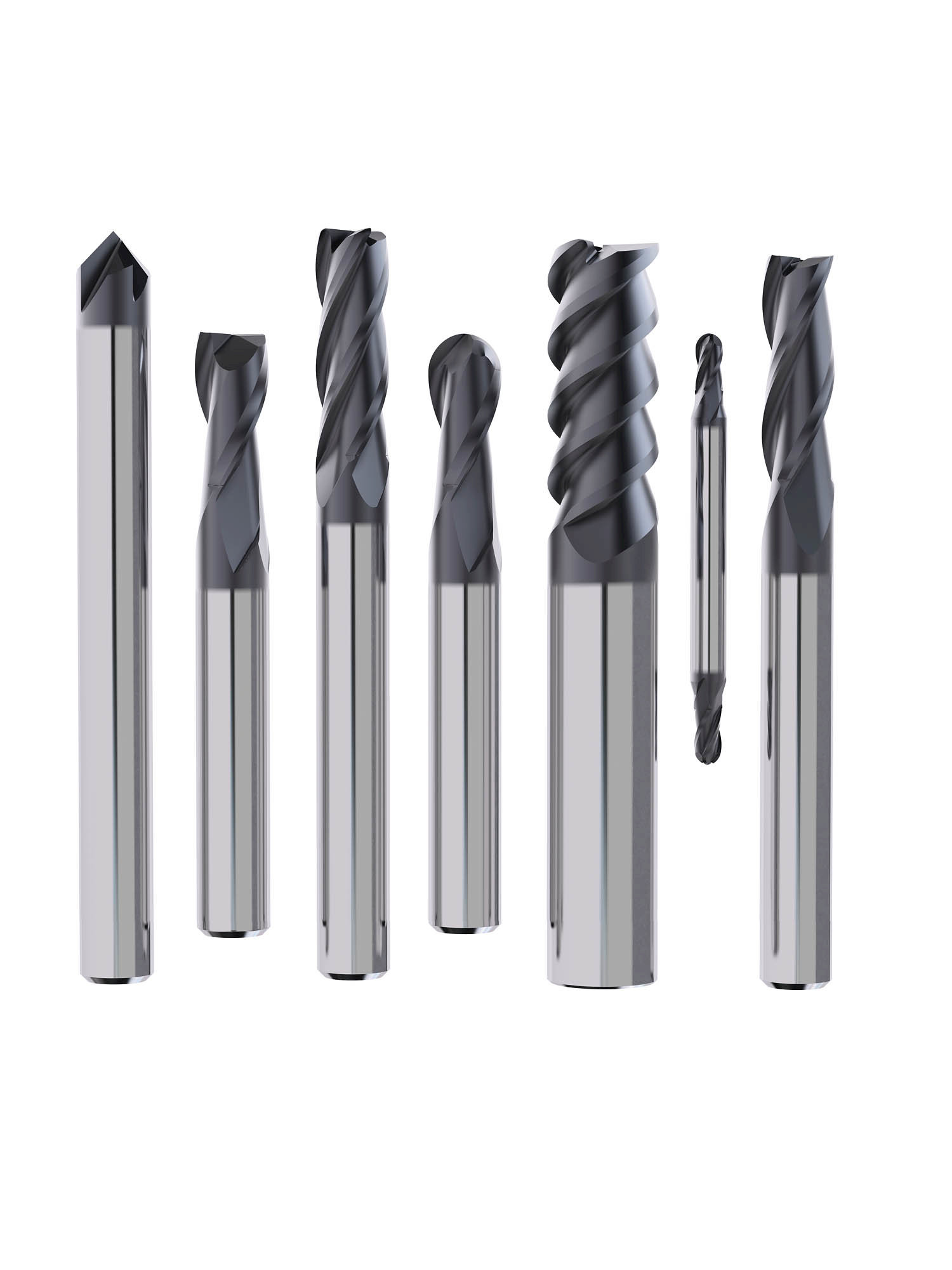
Steadyline® ø25mm (1”) series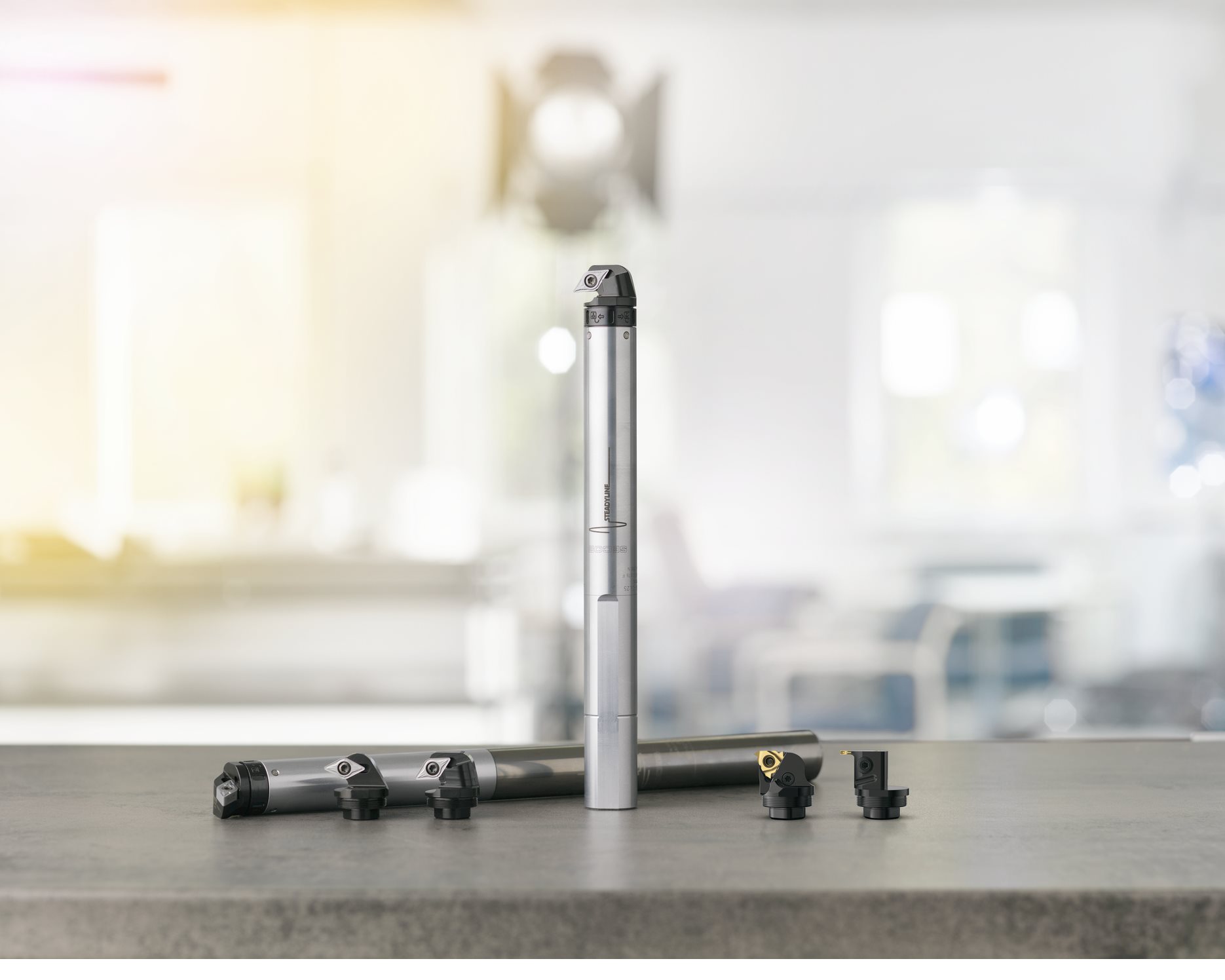
New MP Milling Grades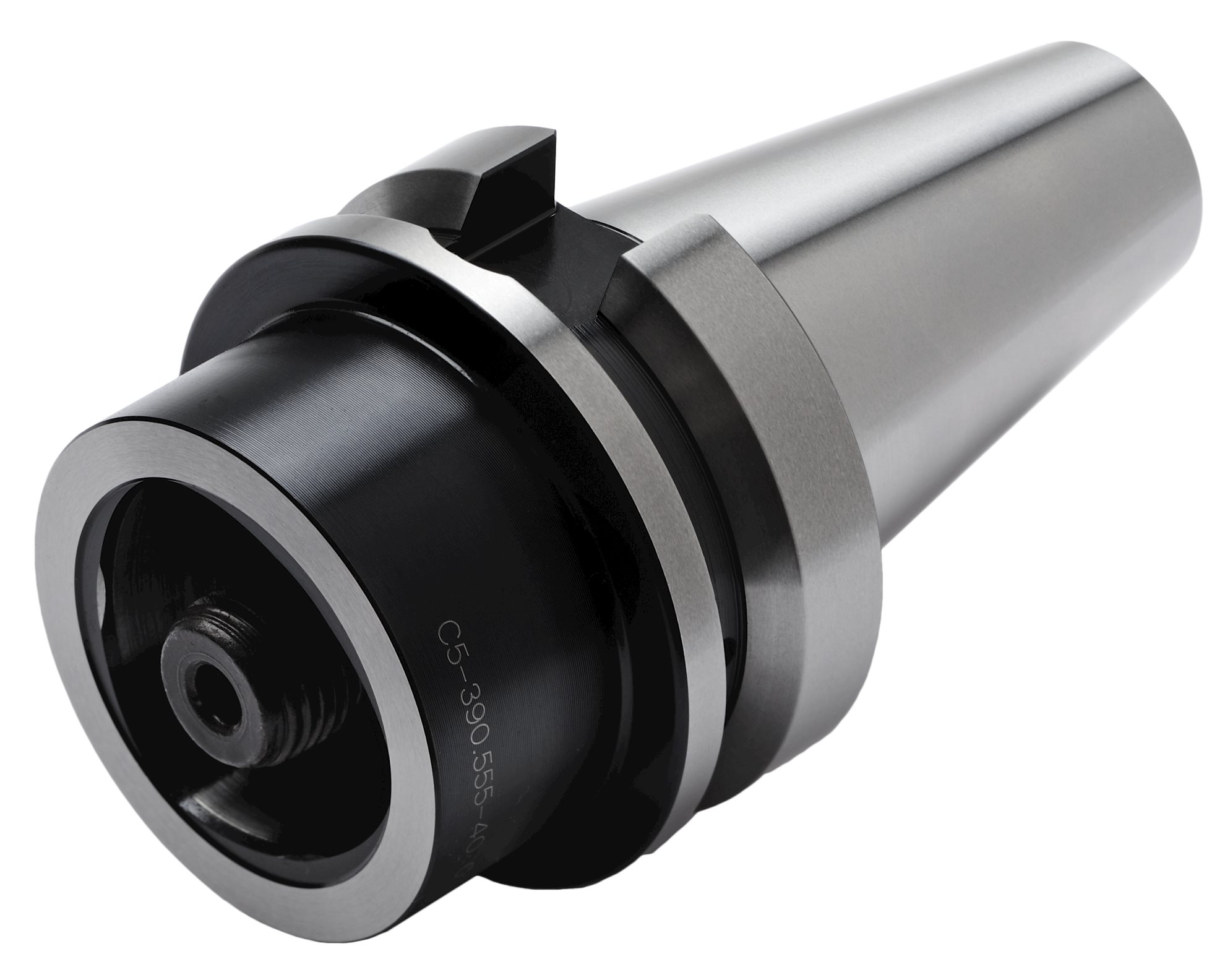
JETI ISO Toolholder range extension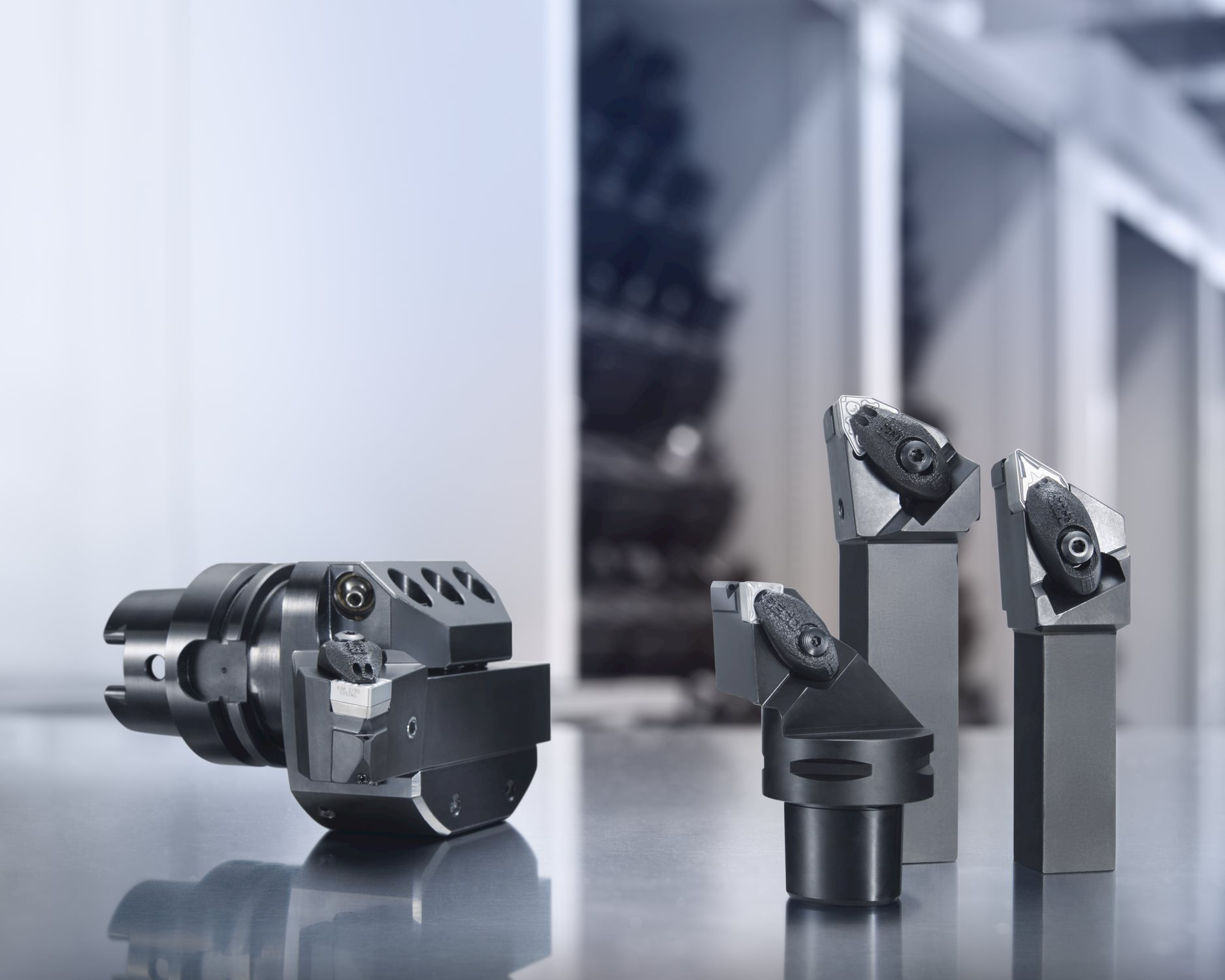
JETI conversion Grooving and Parting-off Capto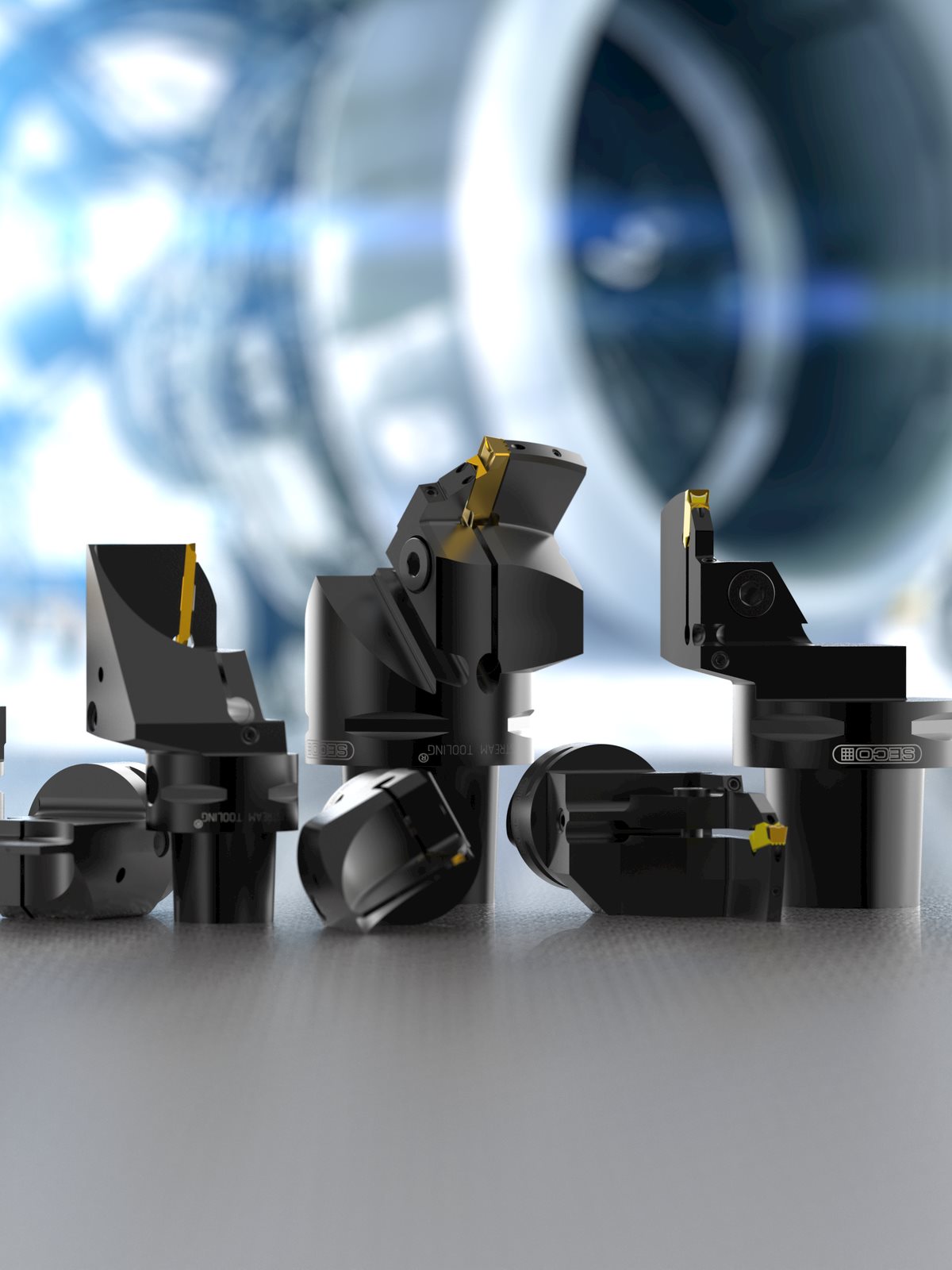
JM100 MINI END MILLS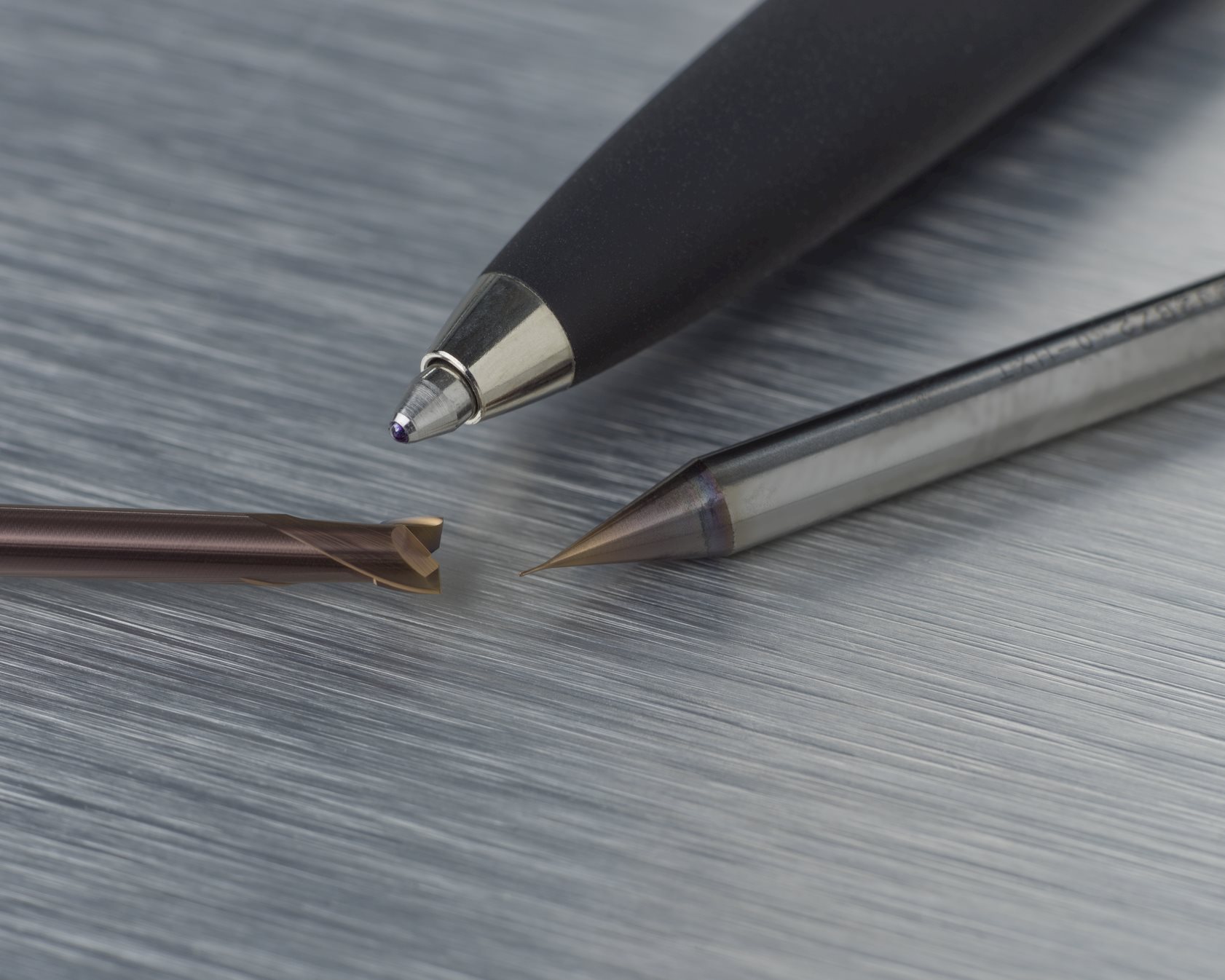
Modular QC (quick-change) toolholder for small part machining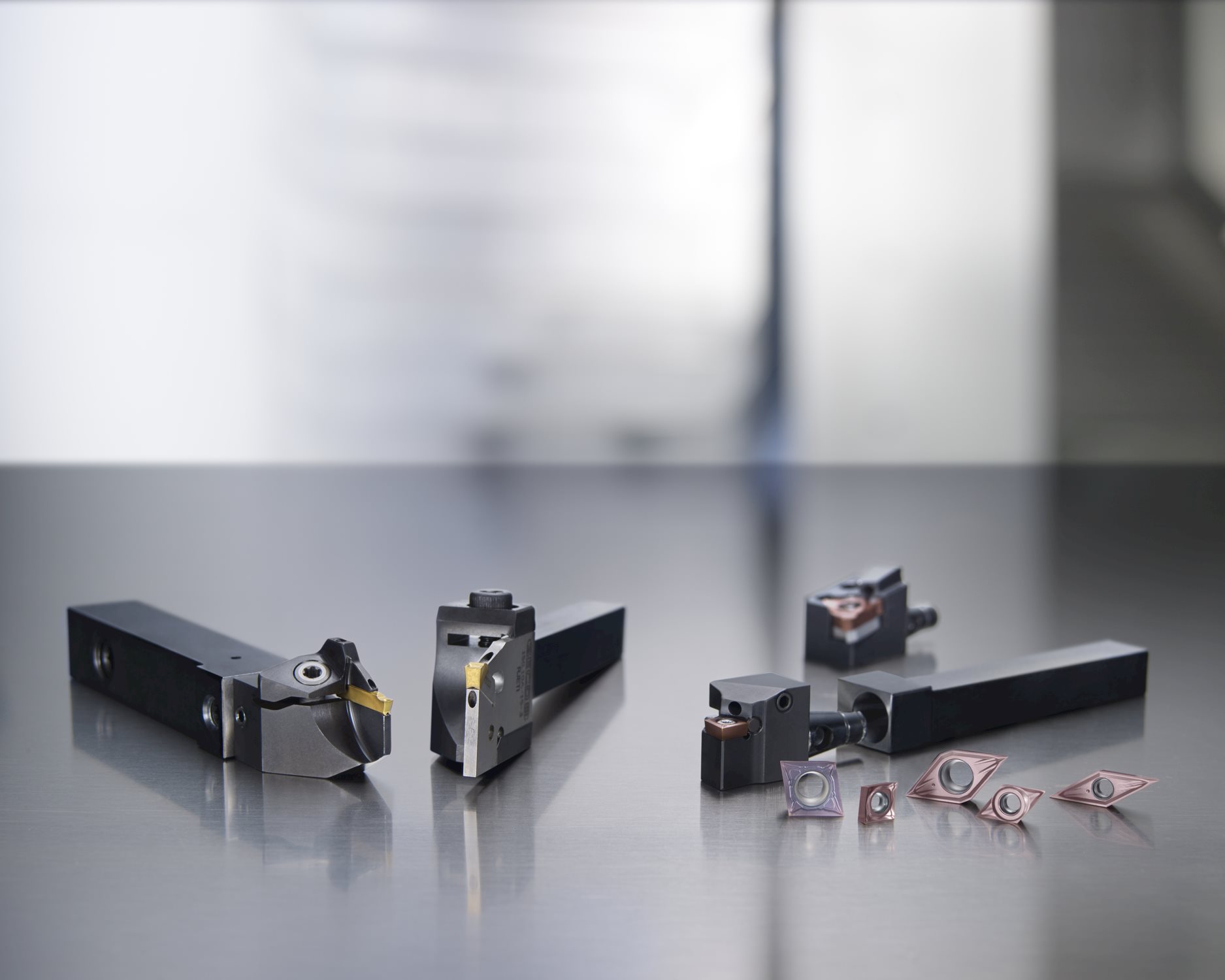
SECO-CAPTO TOOLHOLDERS & CASSETTES FOR ADVANCED MATERIAL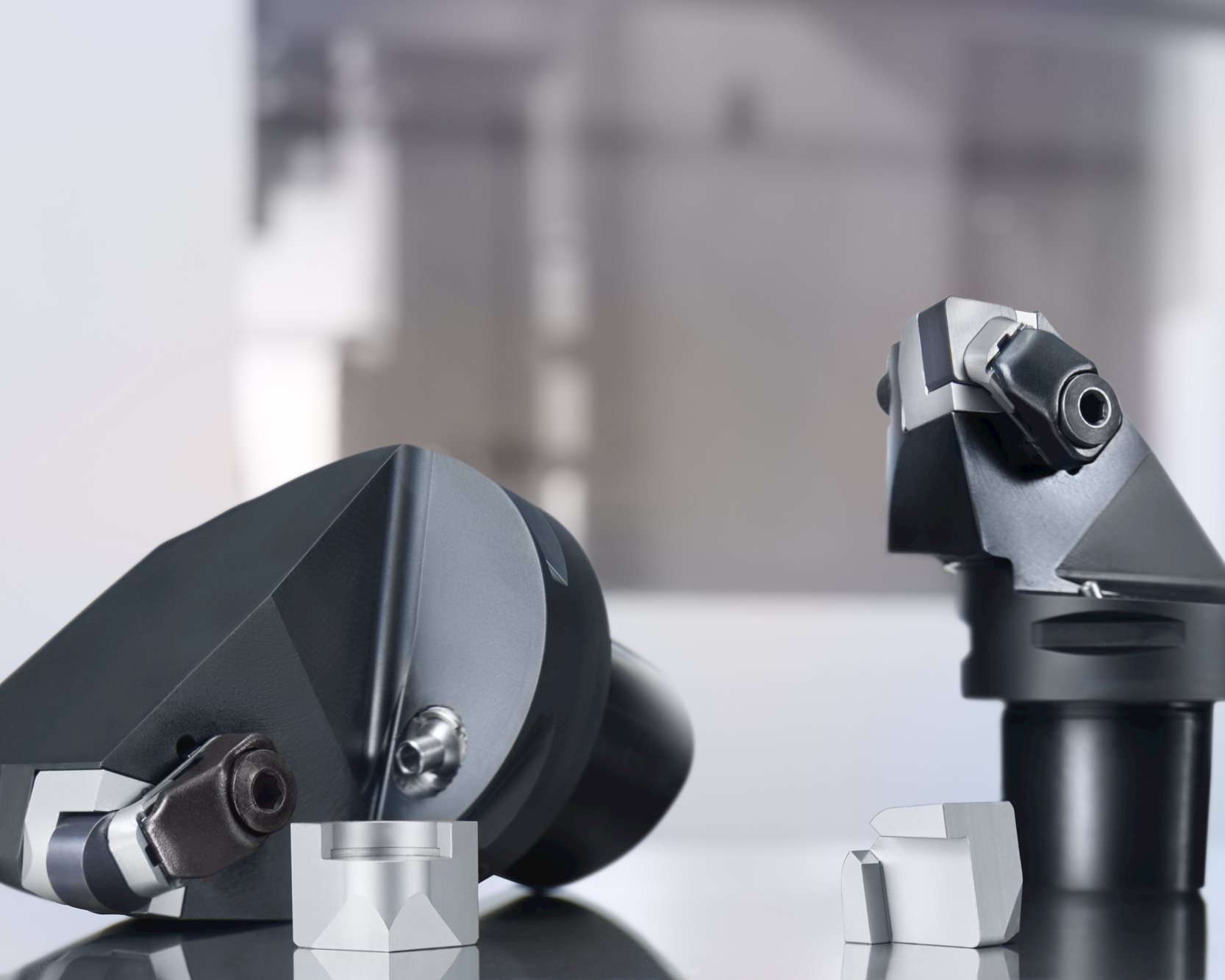
XP08 ALUMINIUM ROUTER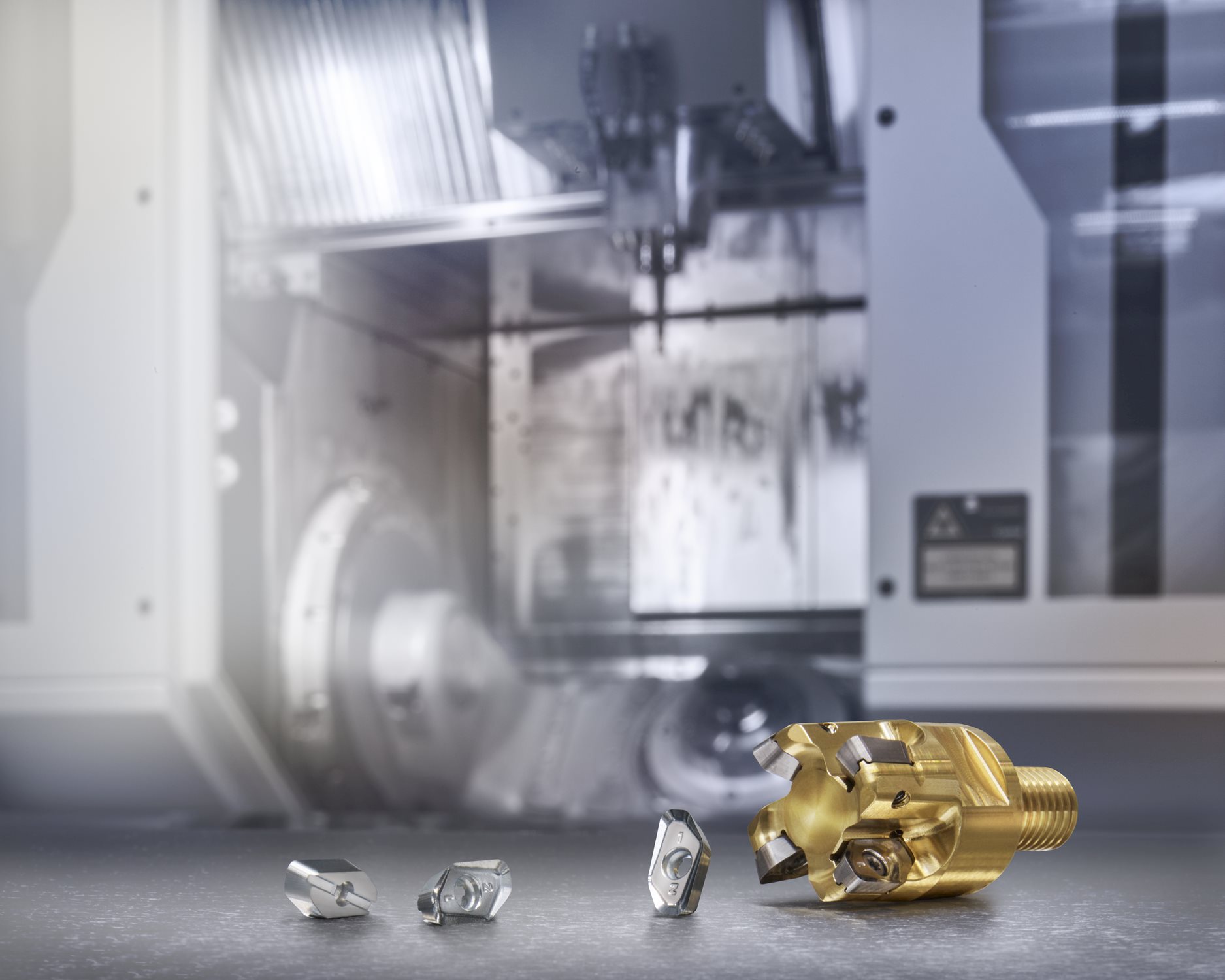
RANGE EXTENSION OF SHELL MILL HOLDERS, SMALL FACE & SIDE LOCK HOLDERS IMPROVEMENTS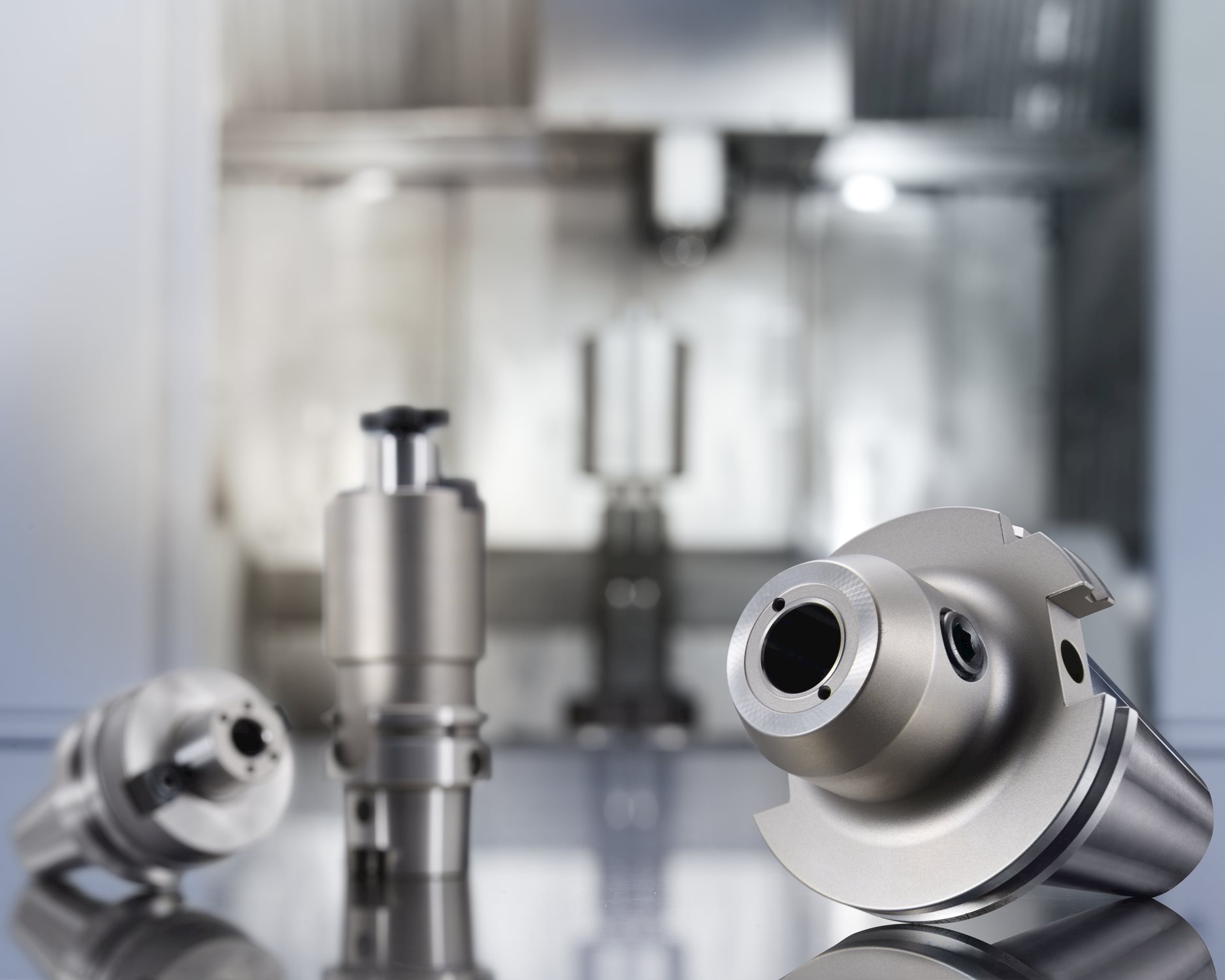
COMBIMASTER™ M20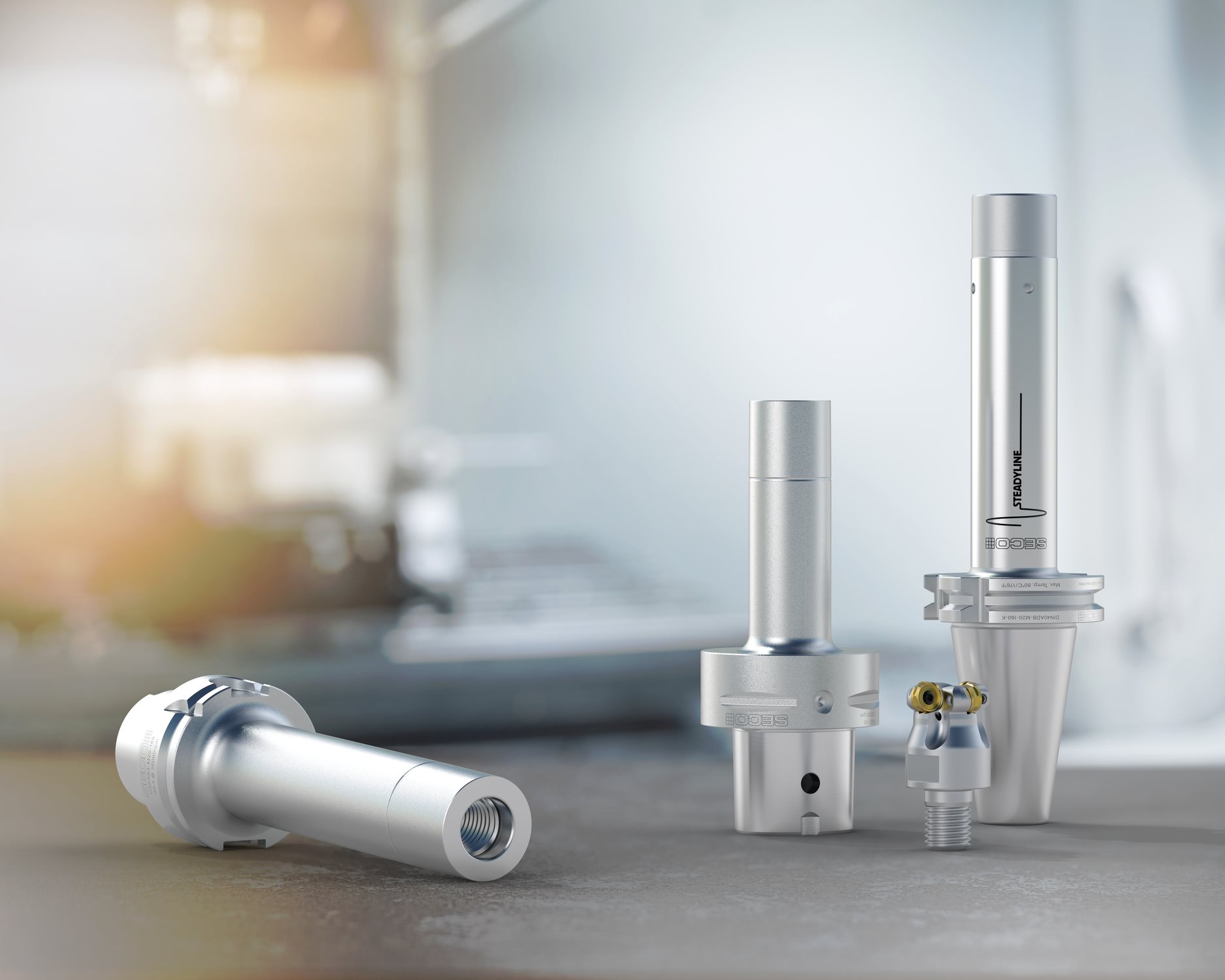
EASYSHRINK EVO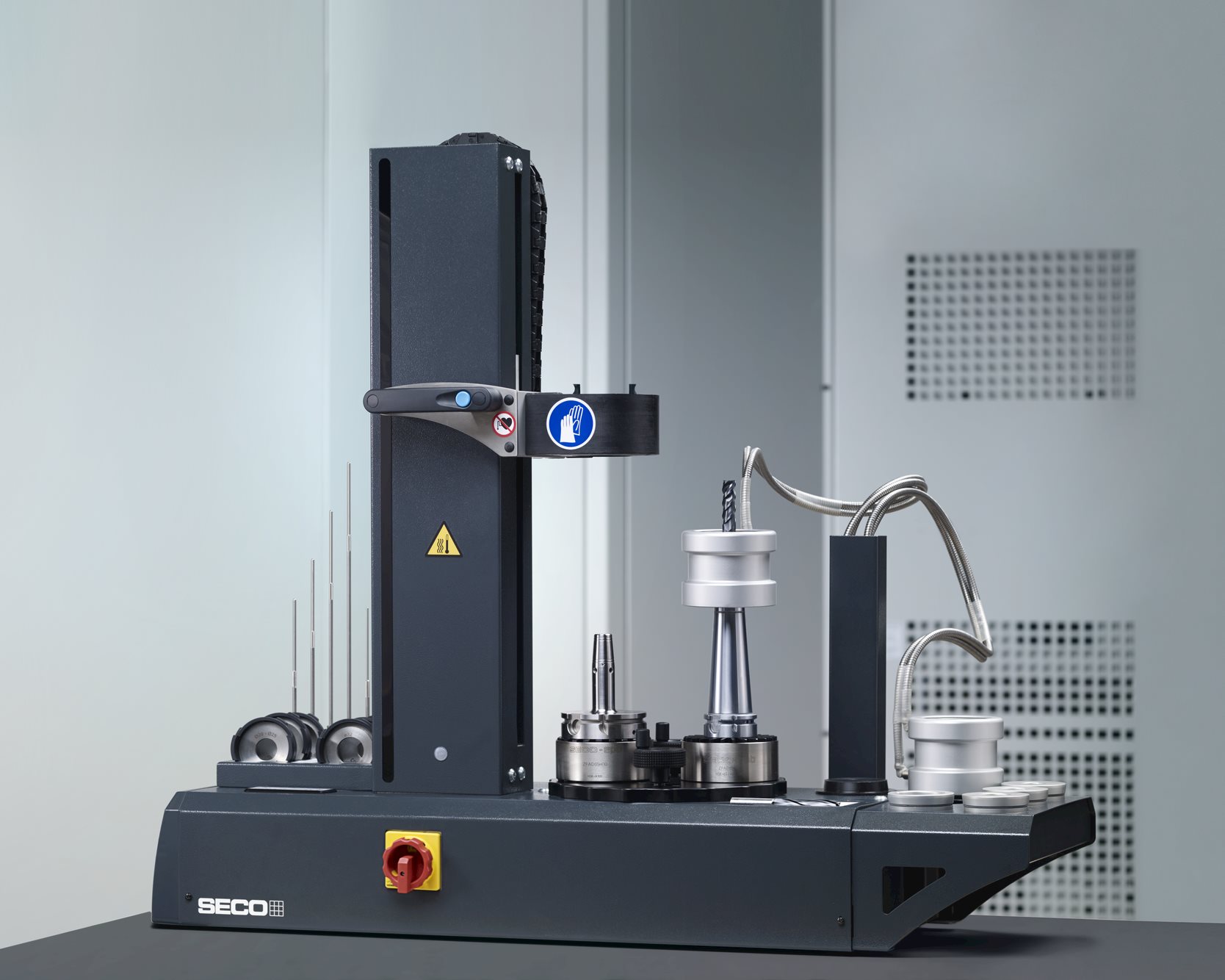
UNIVERSAL DRILLS 8XD AND 12XD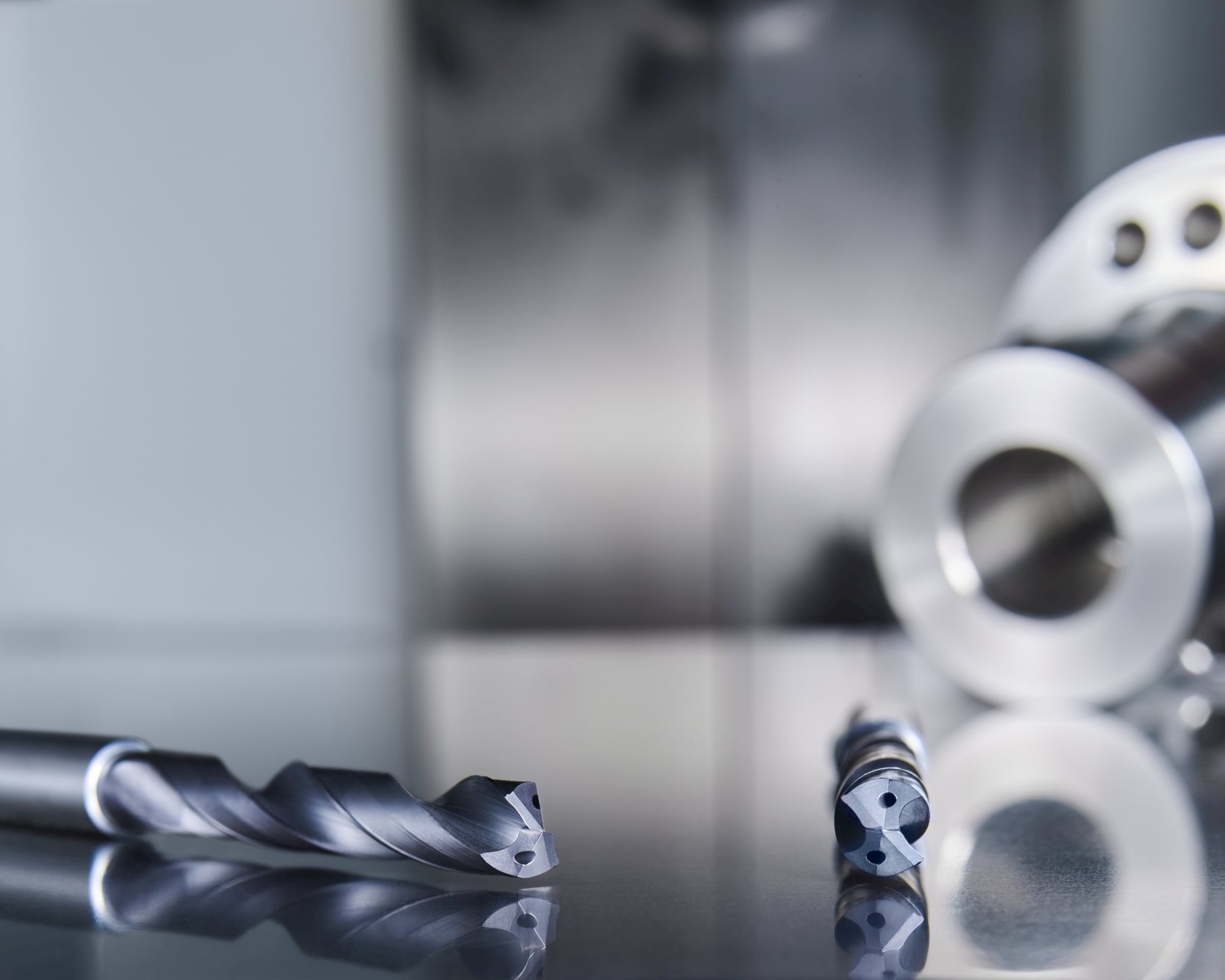
SECO ROUND 10 AND 16 COPY MILLING INSERTS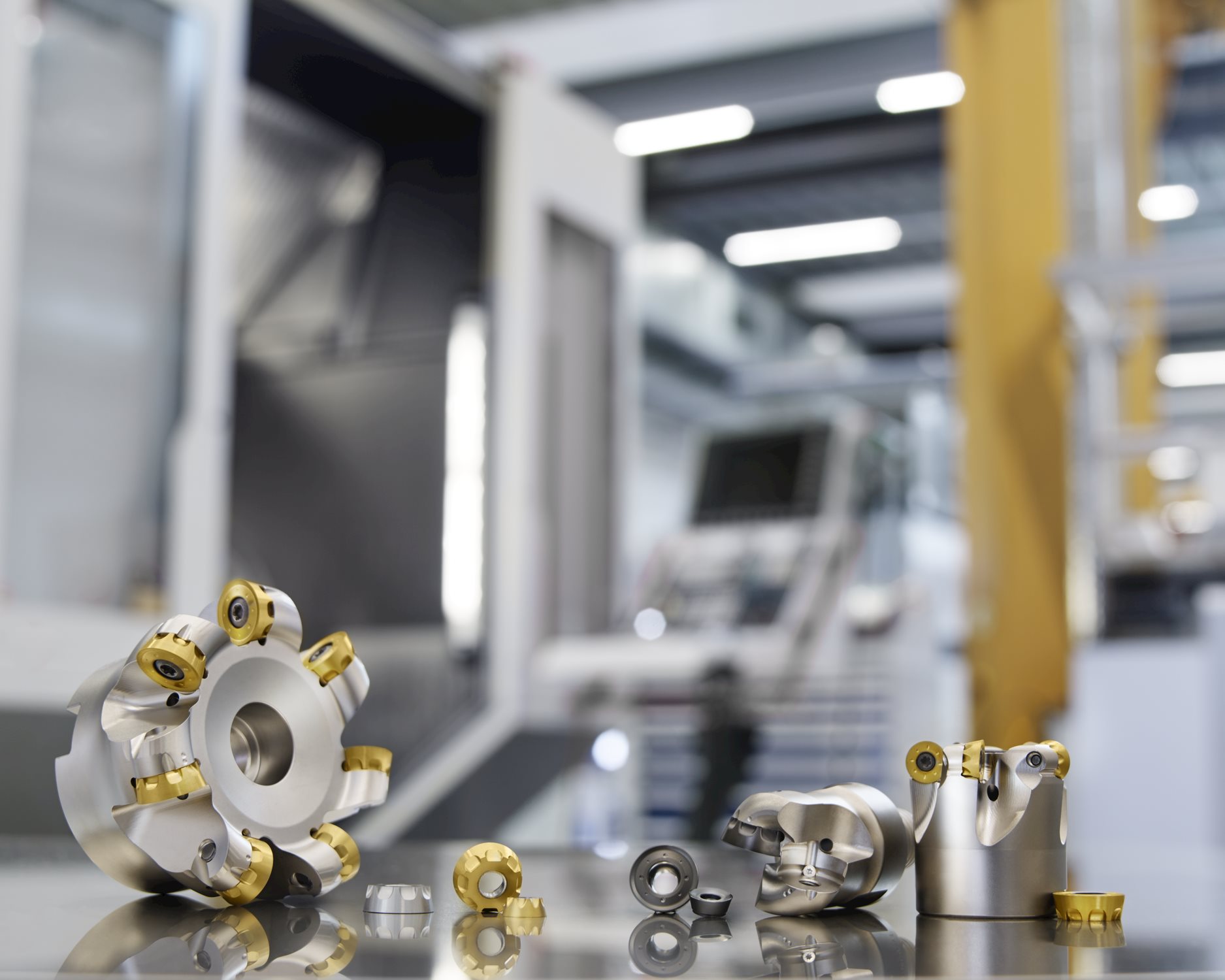
DOUBLE TURBO 16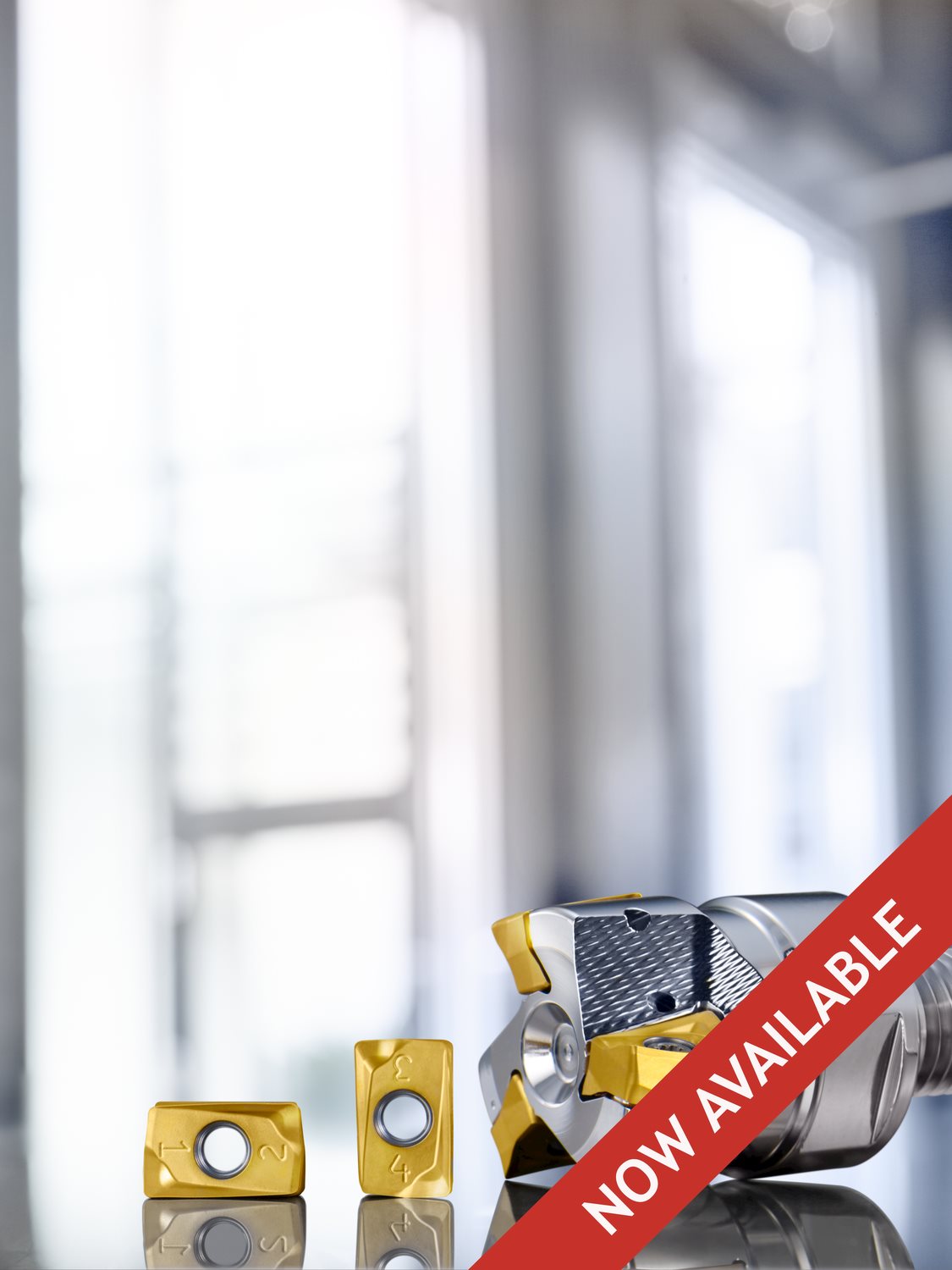
High Feed square cut size 14 insert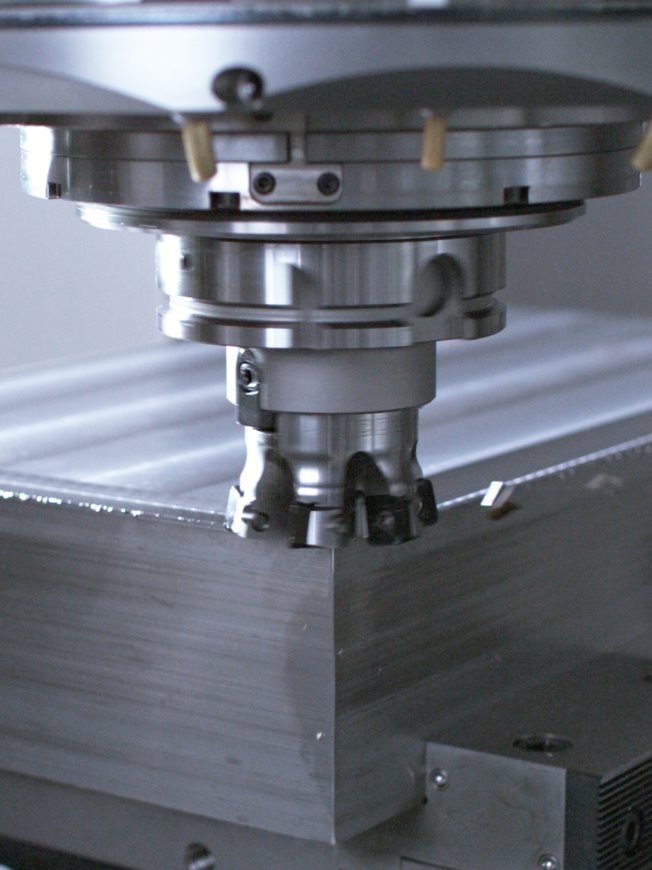
ISO K THREADING TAPS
R220.88 WITH SNMU INSERTS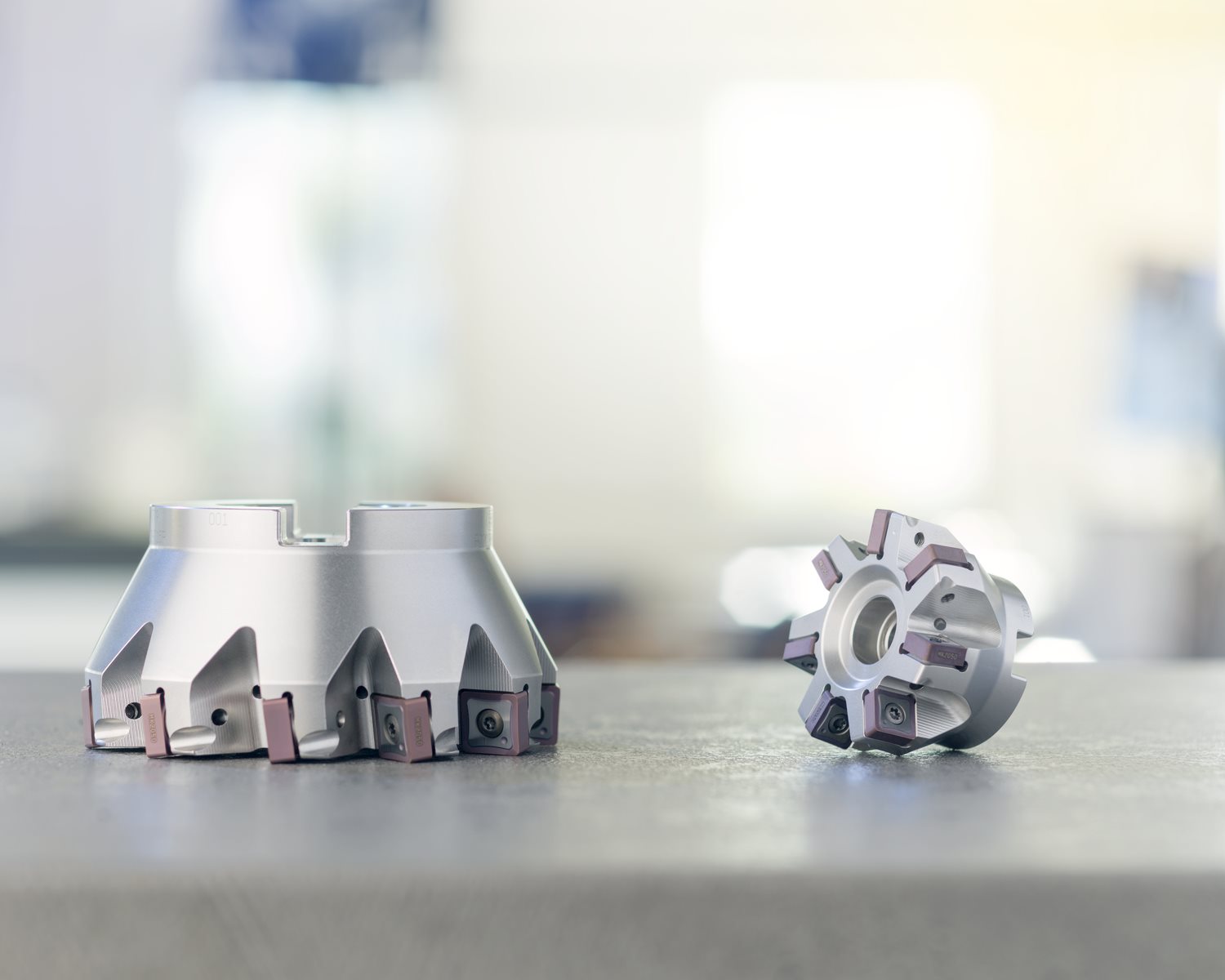
TTP2050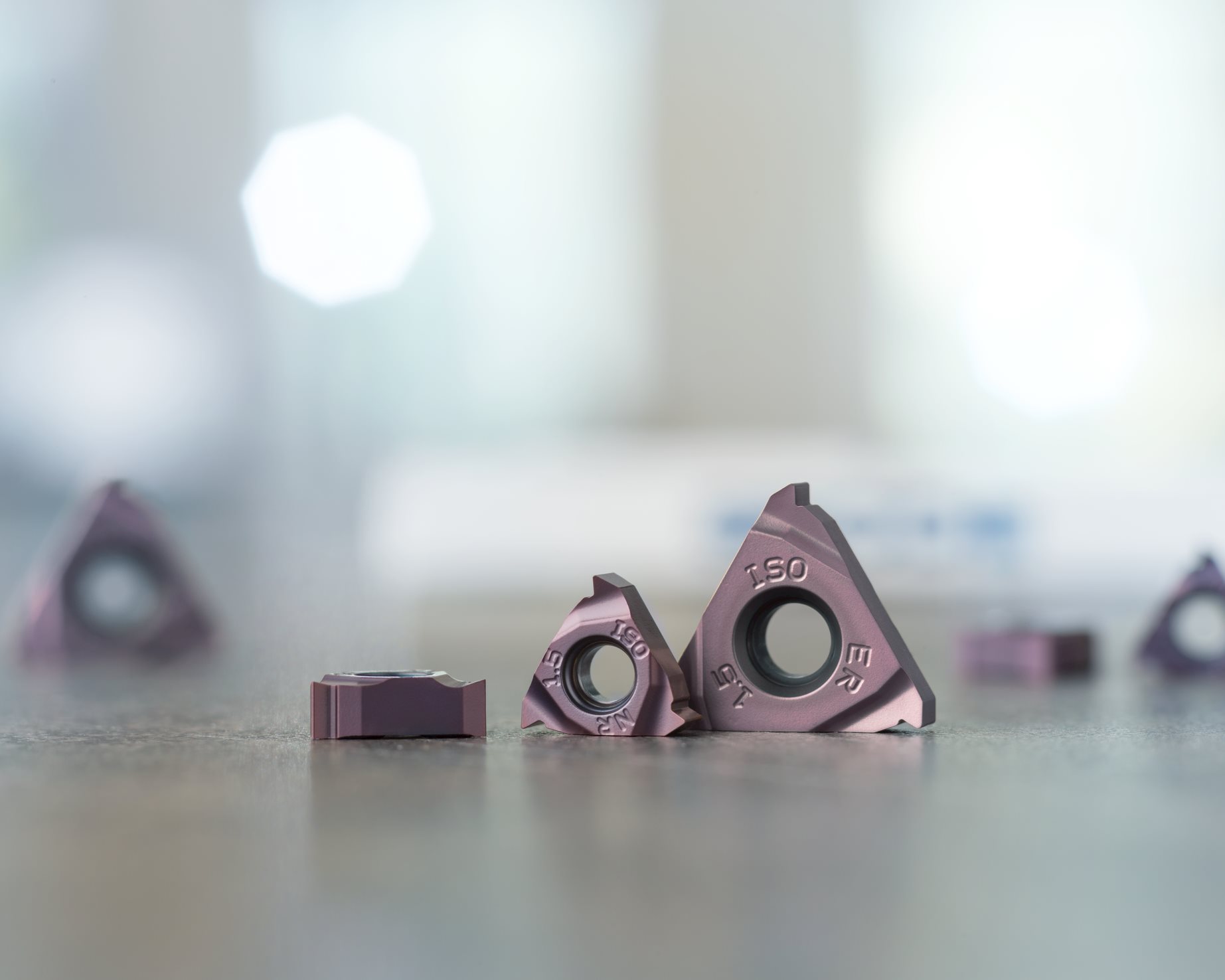
DOUBLE QUATTROMILL™ 14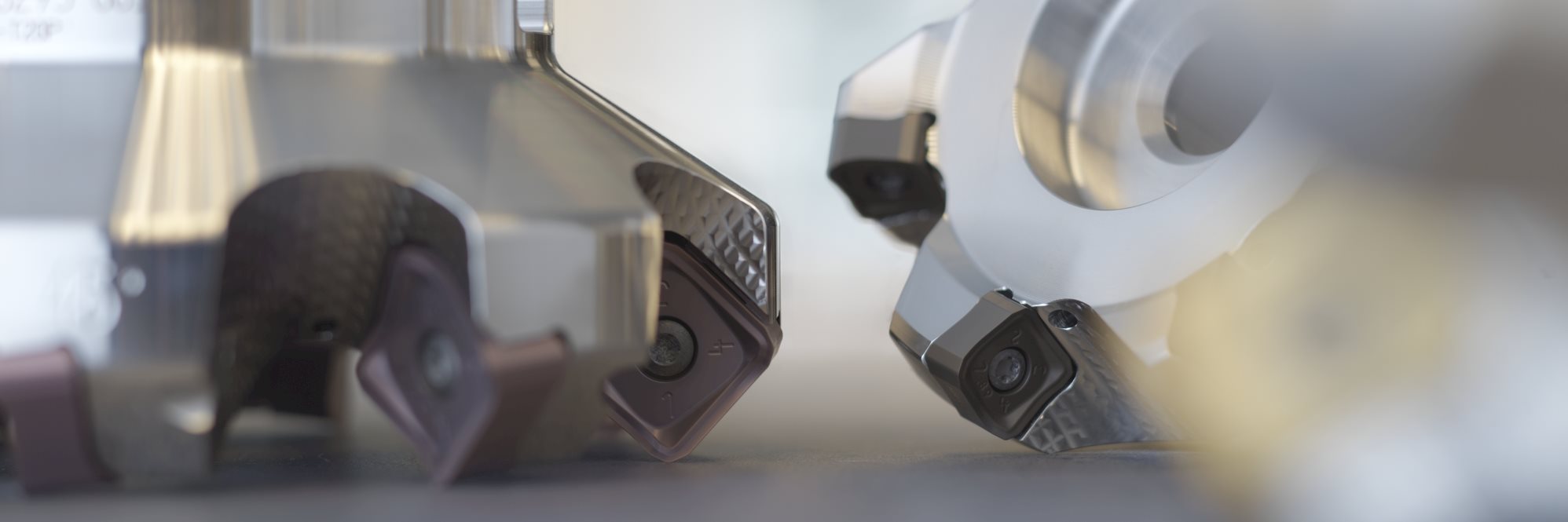
DOUBLE OCTOMILL™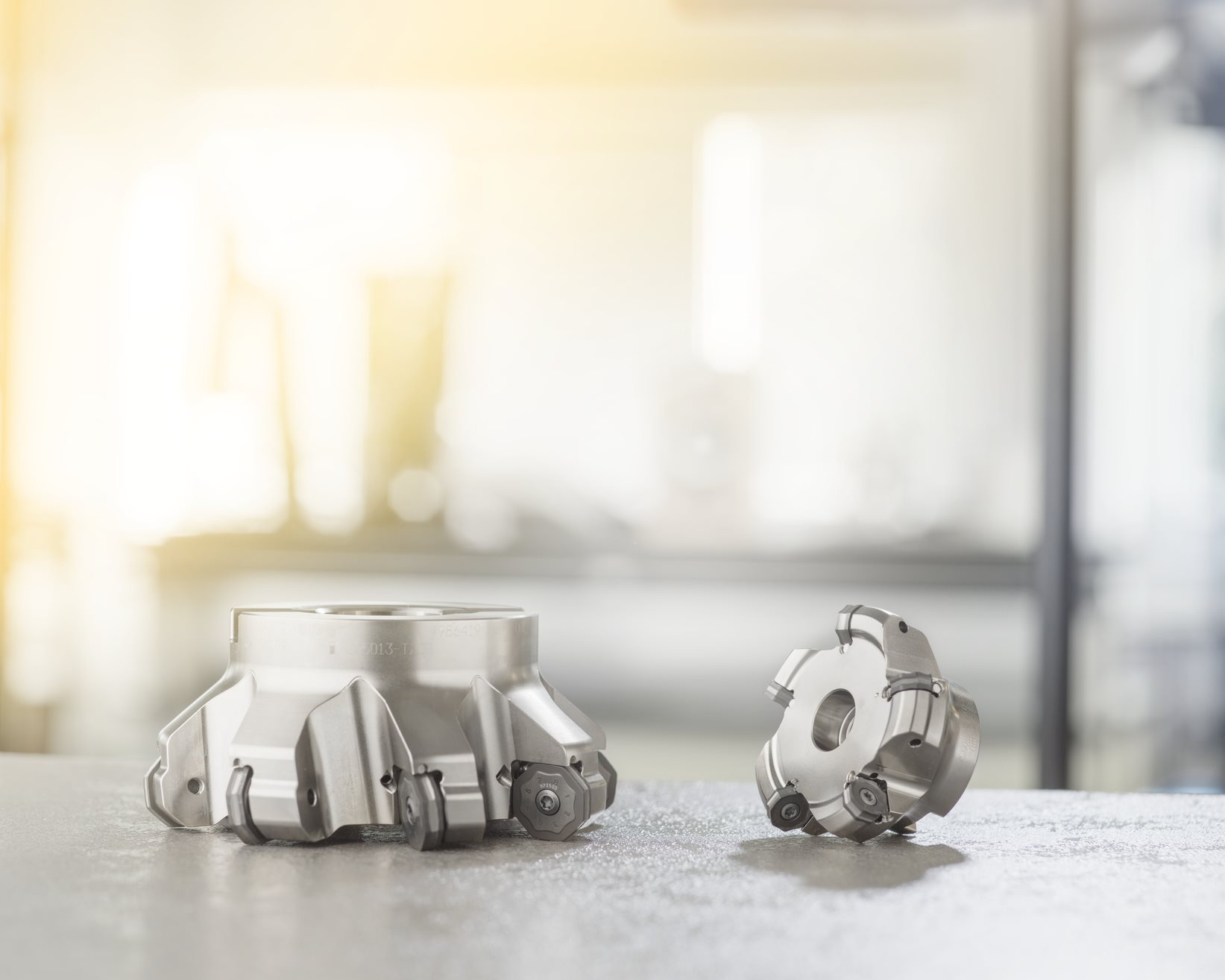
DOUBLE QUATTROMILL™ 22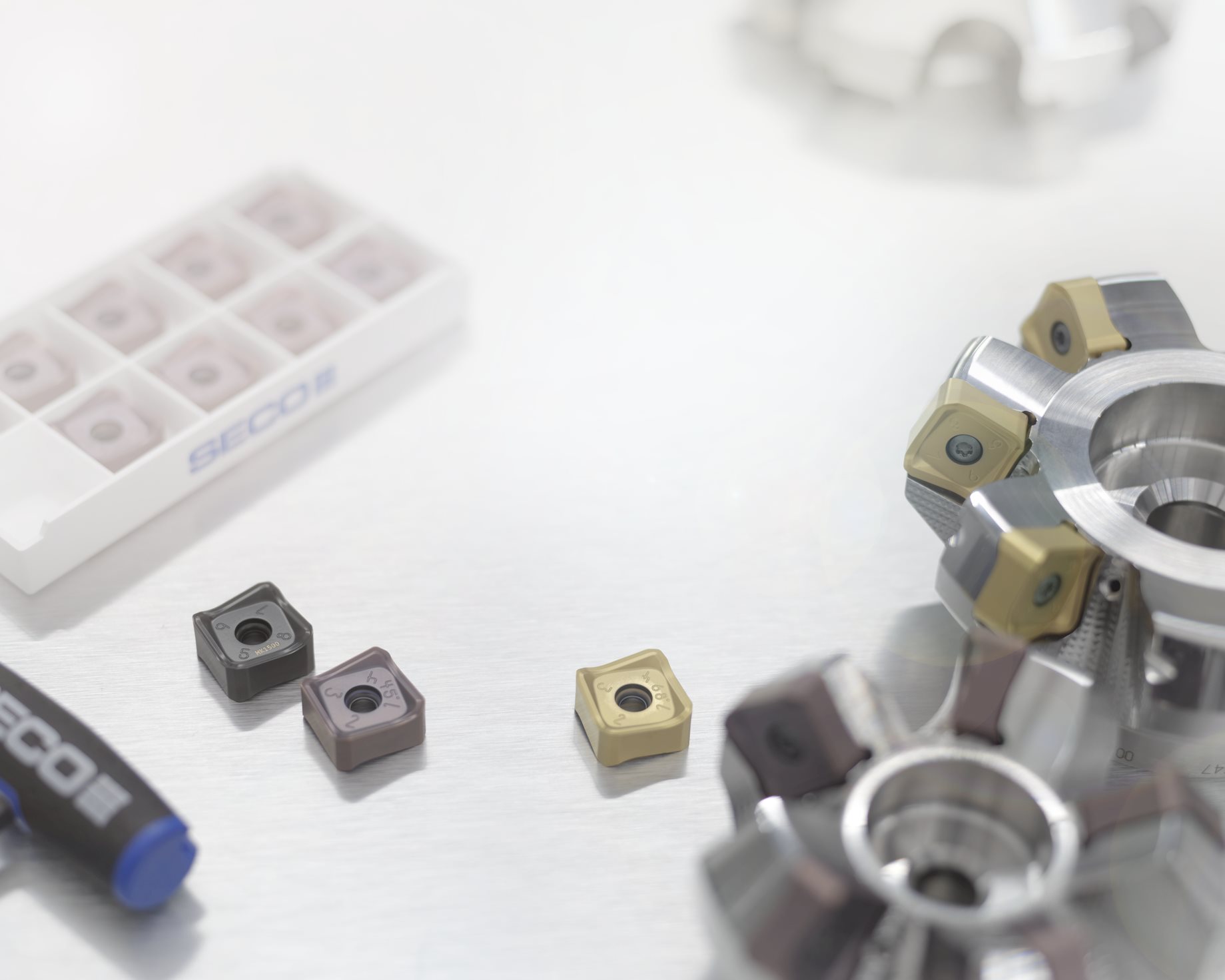
Webinar: How to Achieve High-Quality Threads in Machining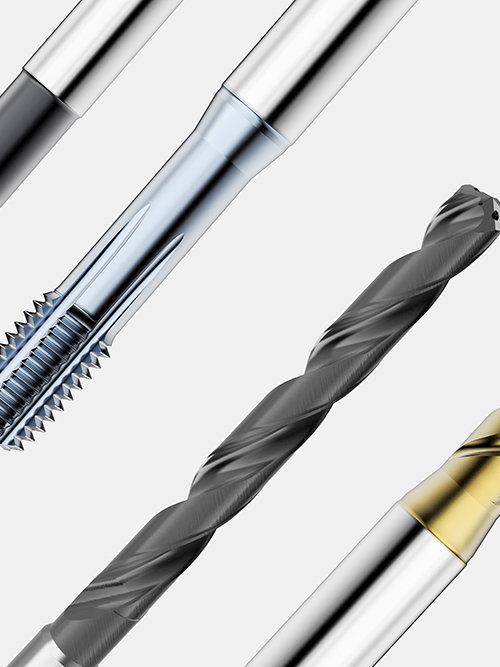
Machining Navigator / Catalog Holemaking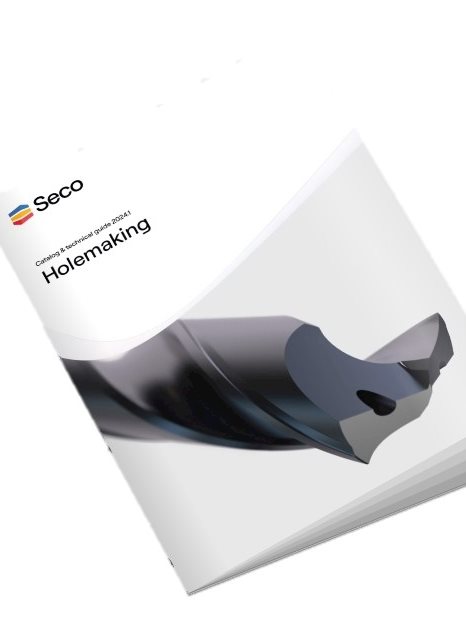
Seco News - Product launch 2023.2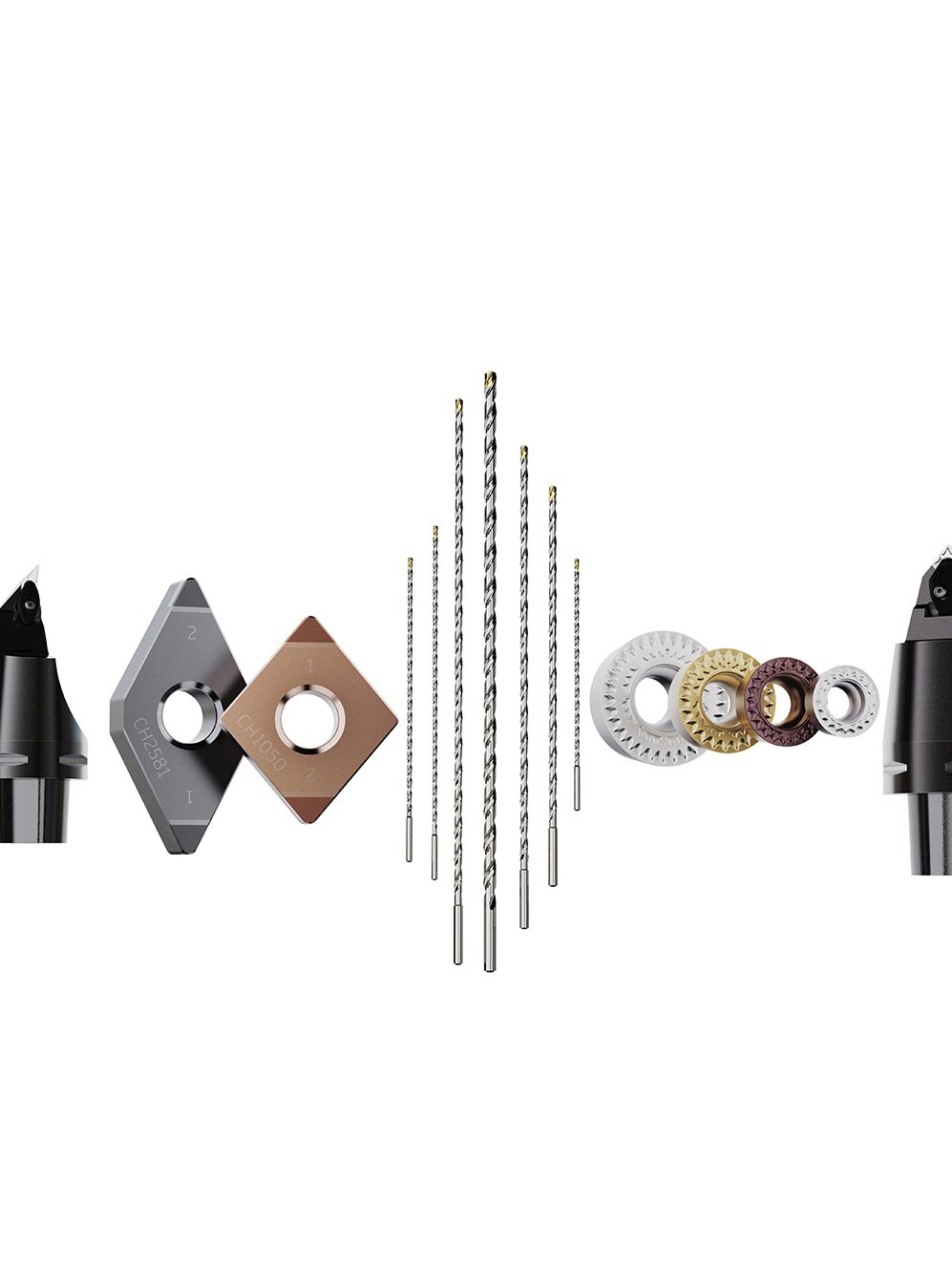
Perfomax ®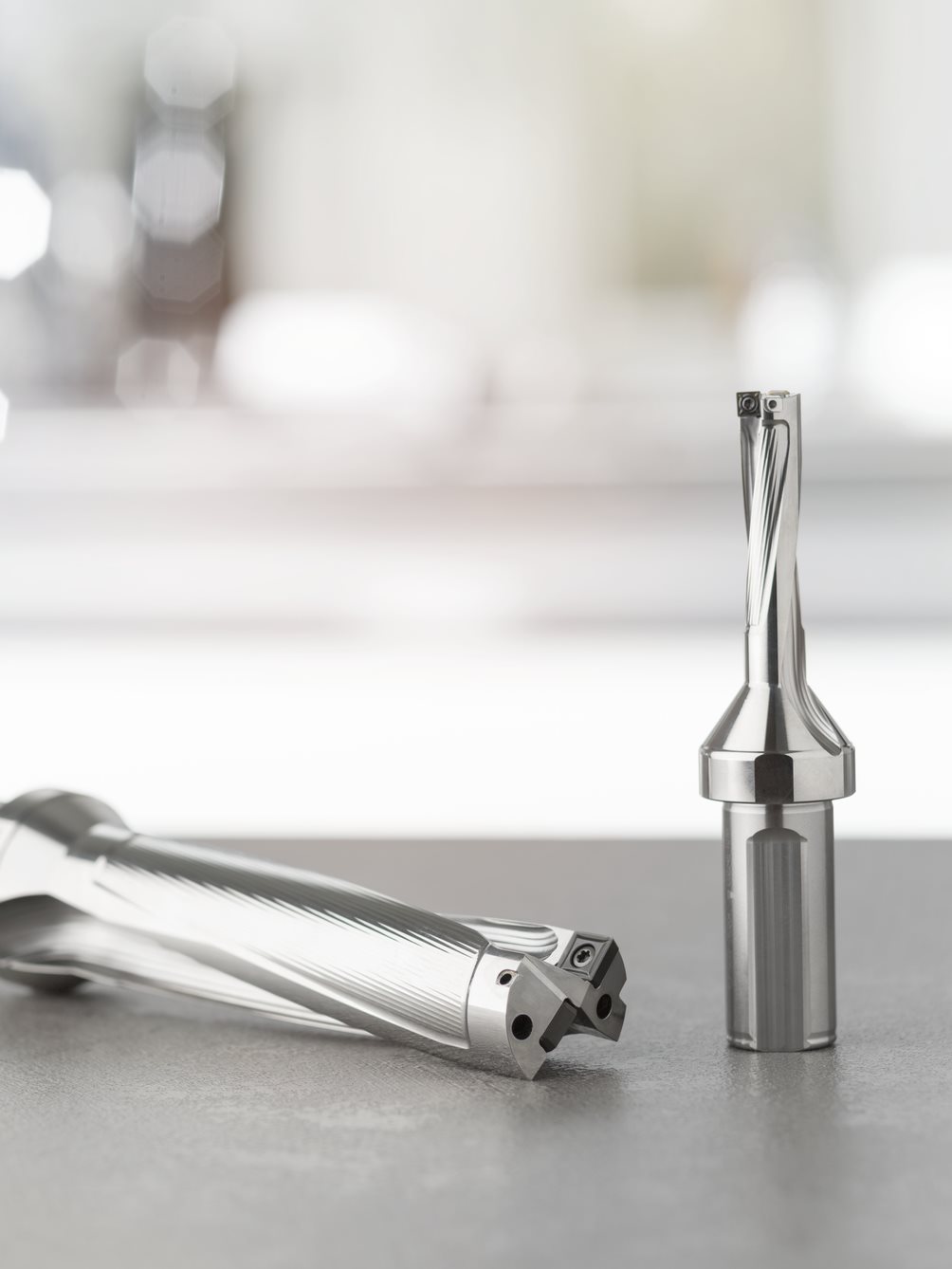
Indexable Insert Drills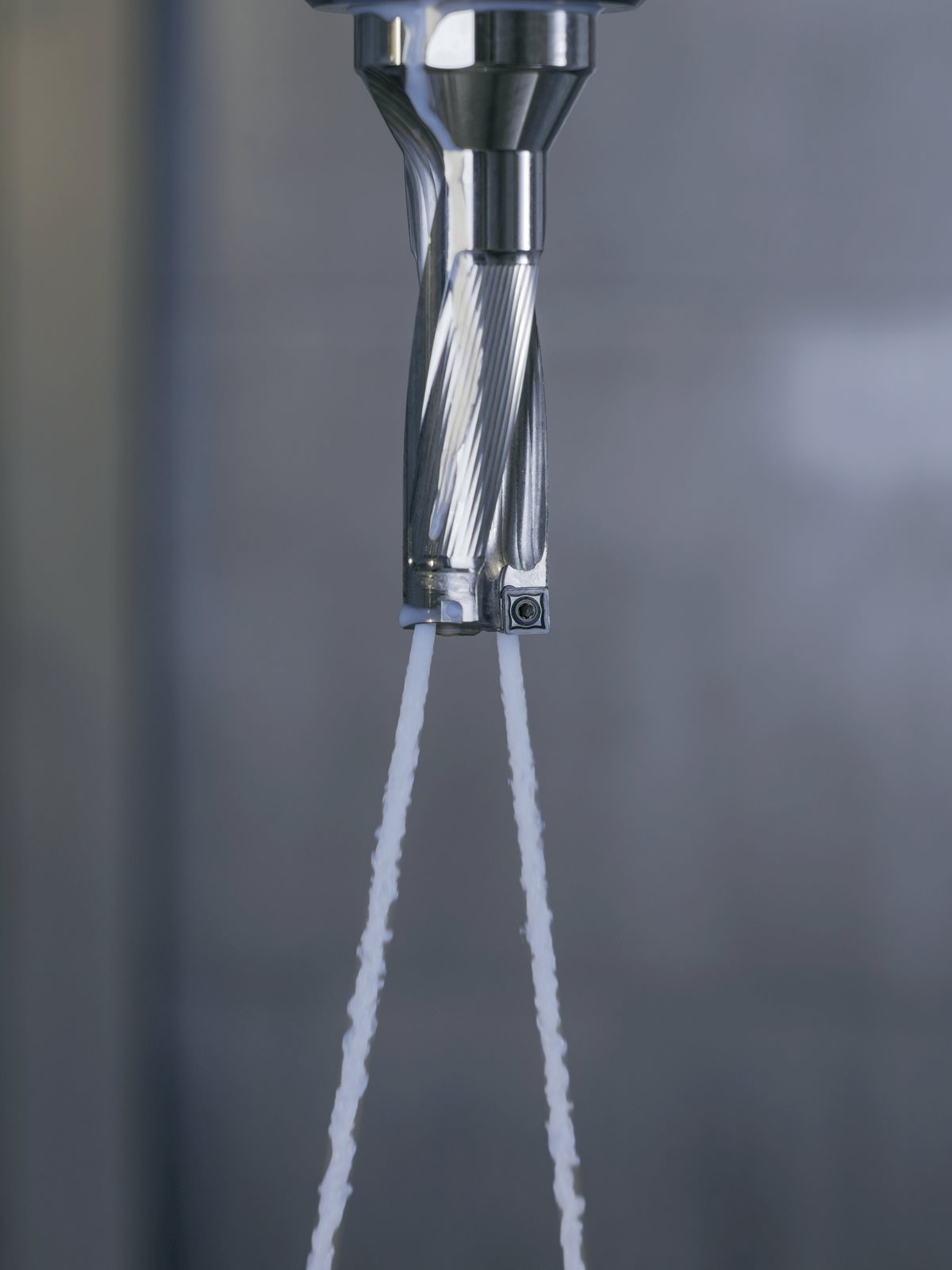
Solid Carbide Drills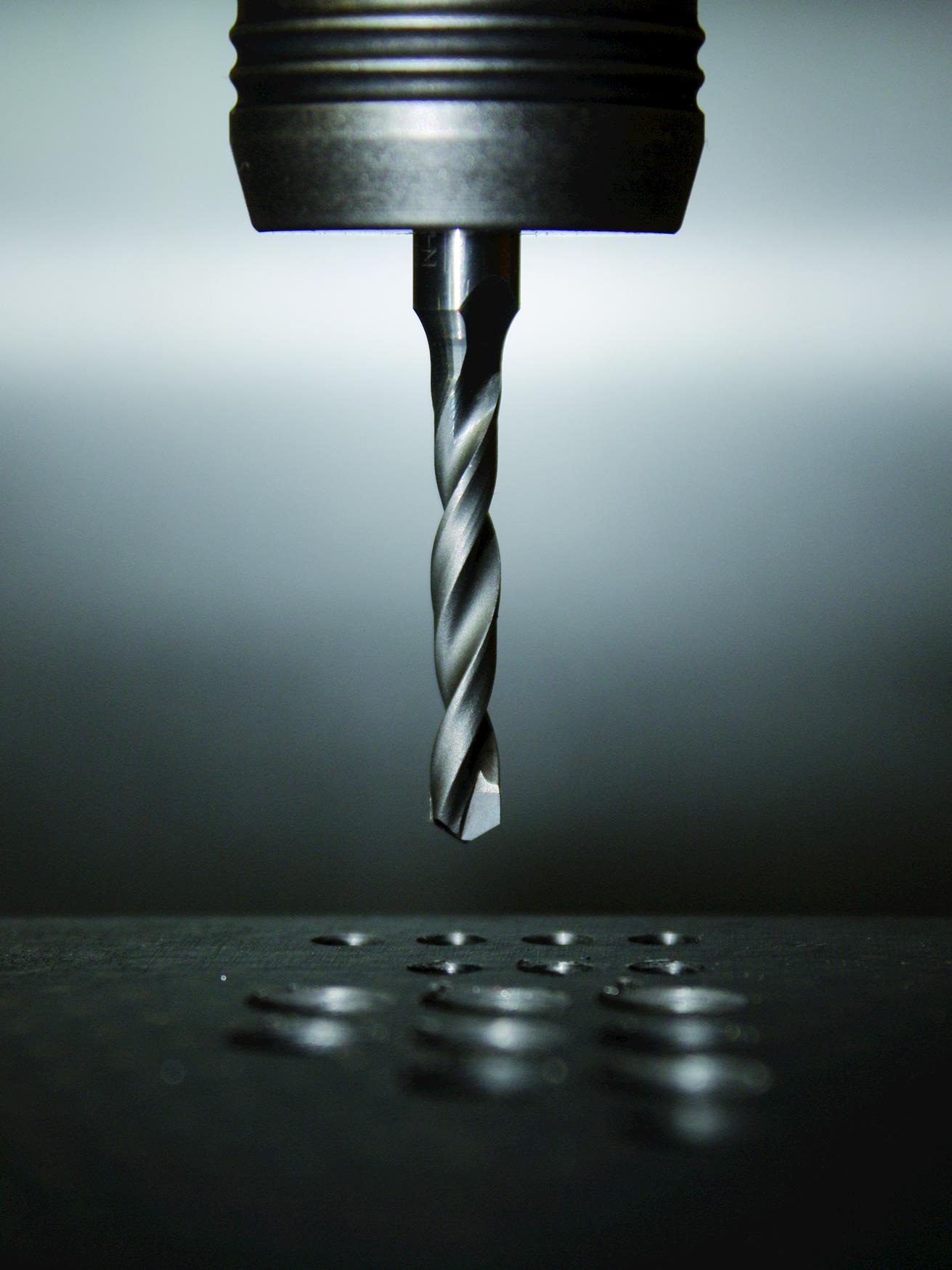
Drilling titanium with a vibration assisted technology | Seco Tools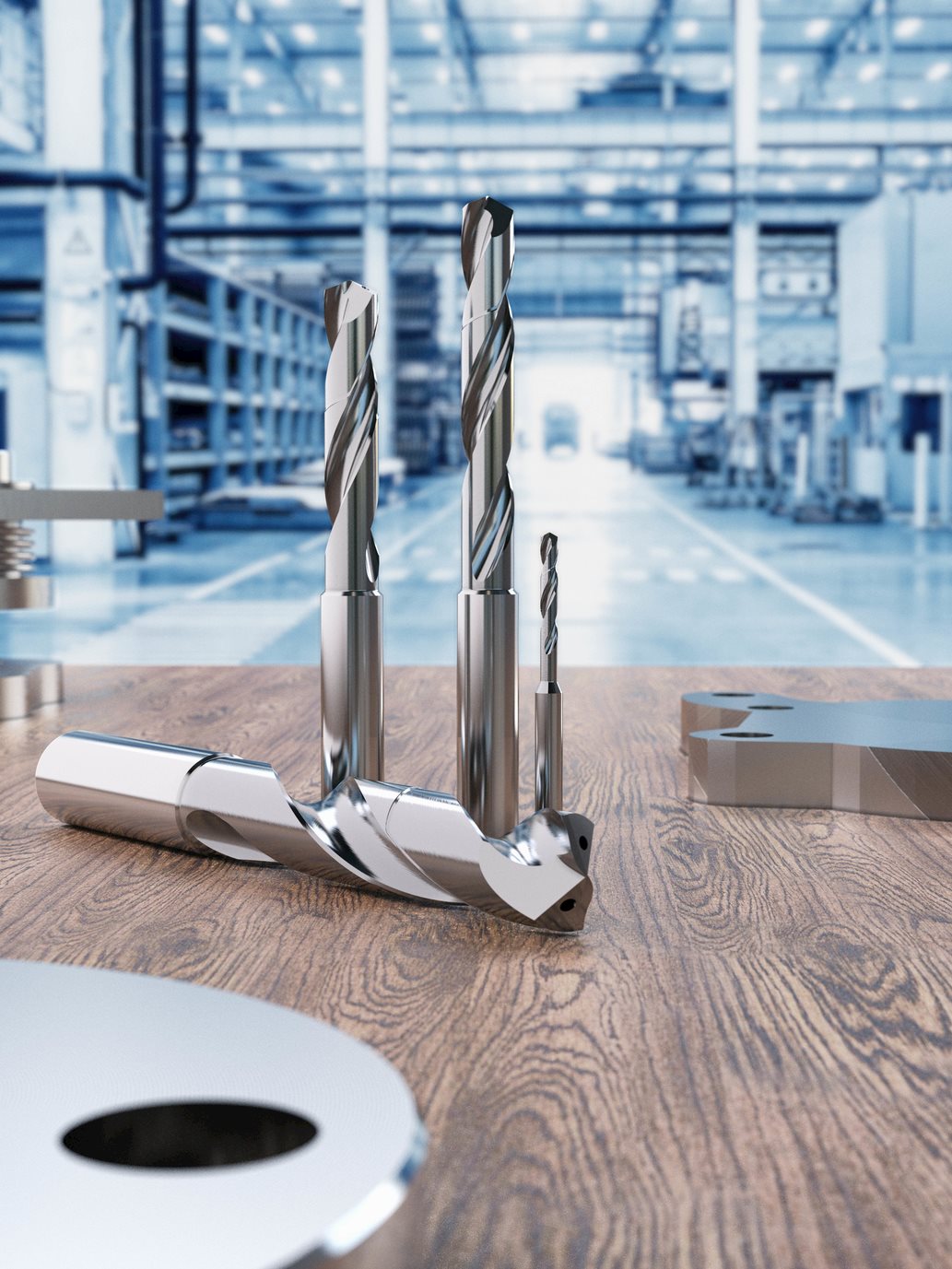
INDEXABLE SHAPER FOR GEAR MANUFACTURING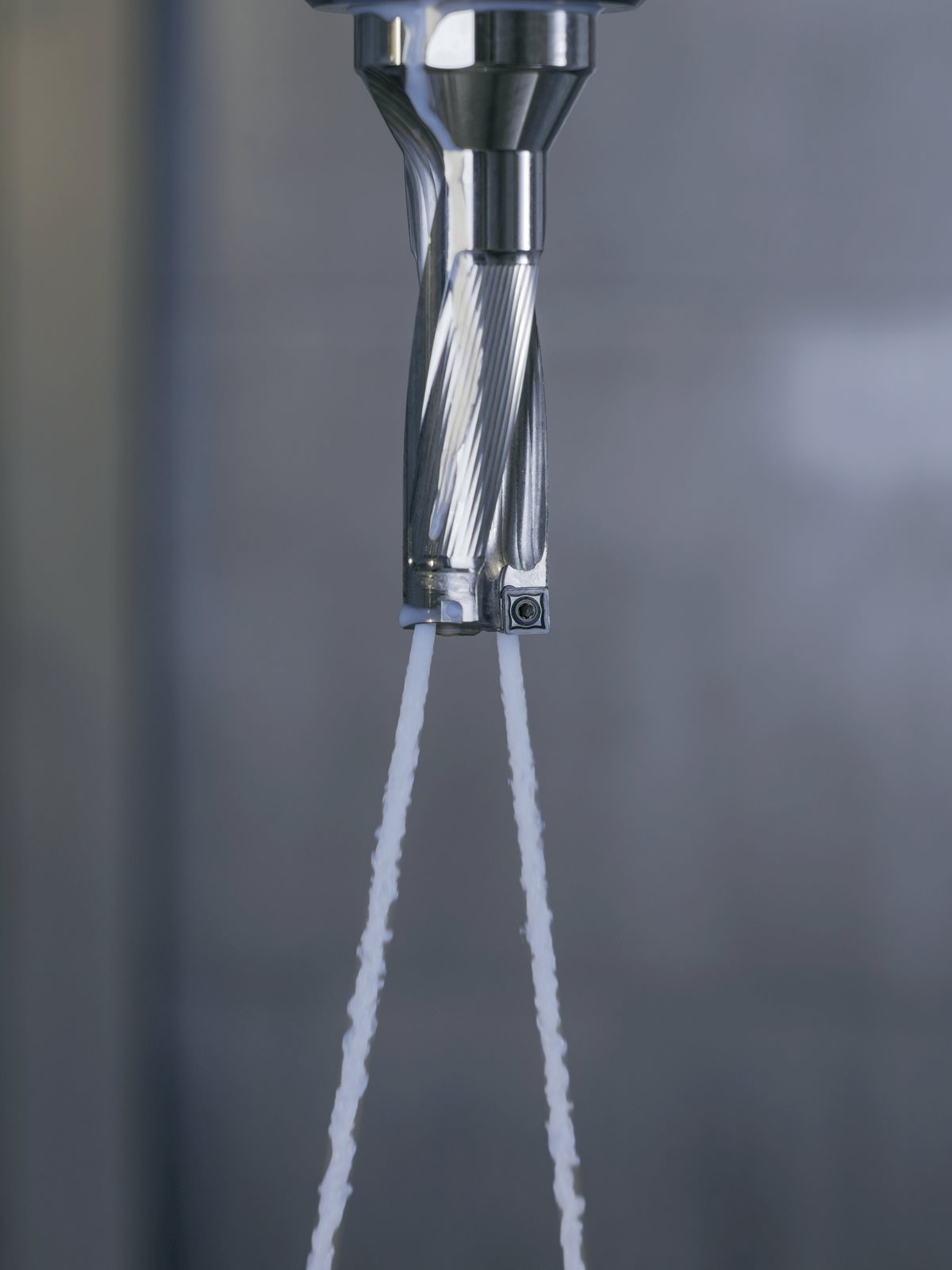
Crownloc Plus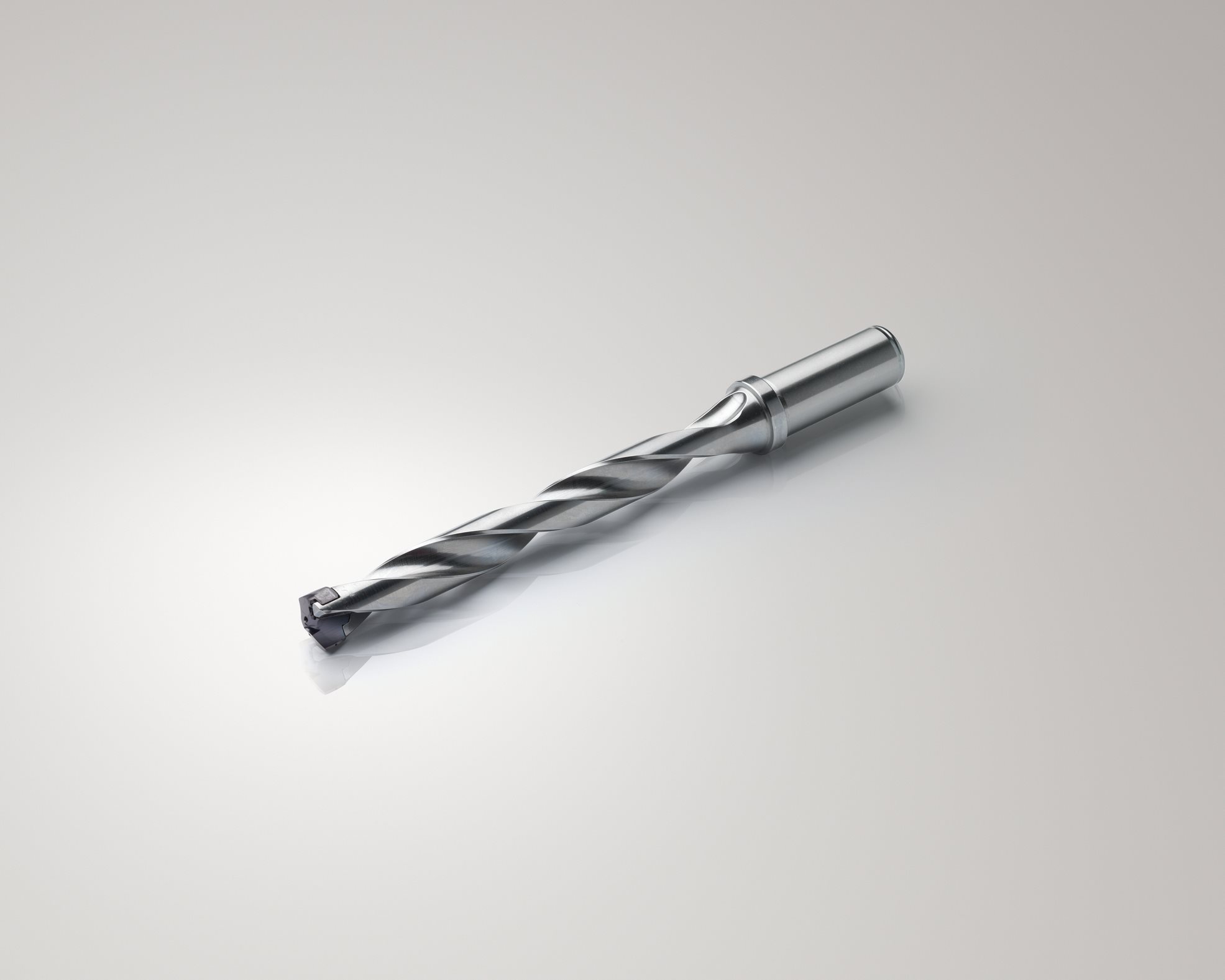
Crownloc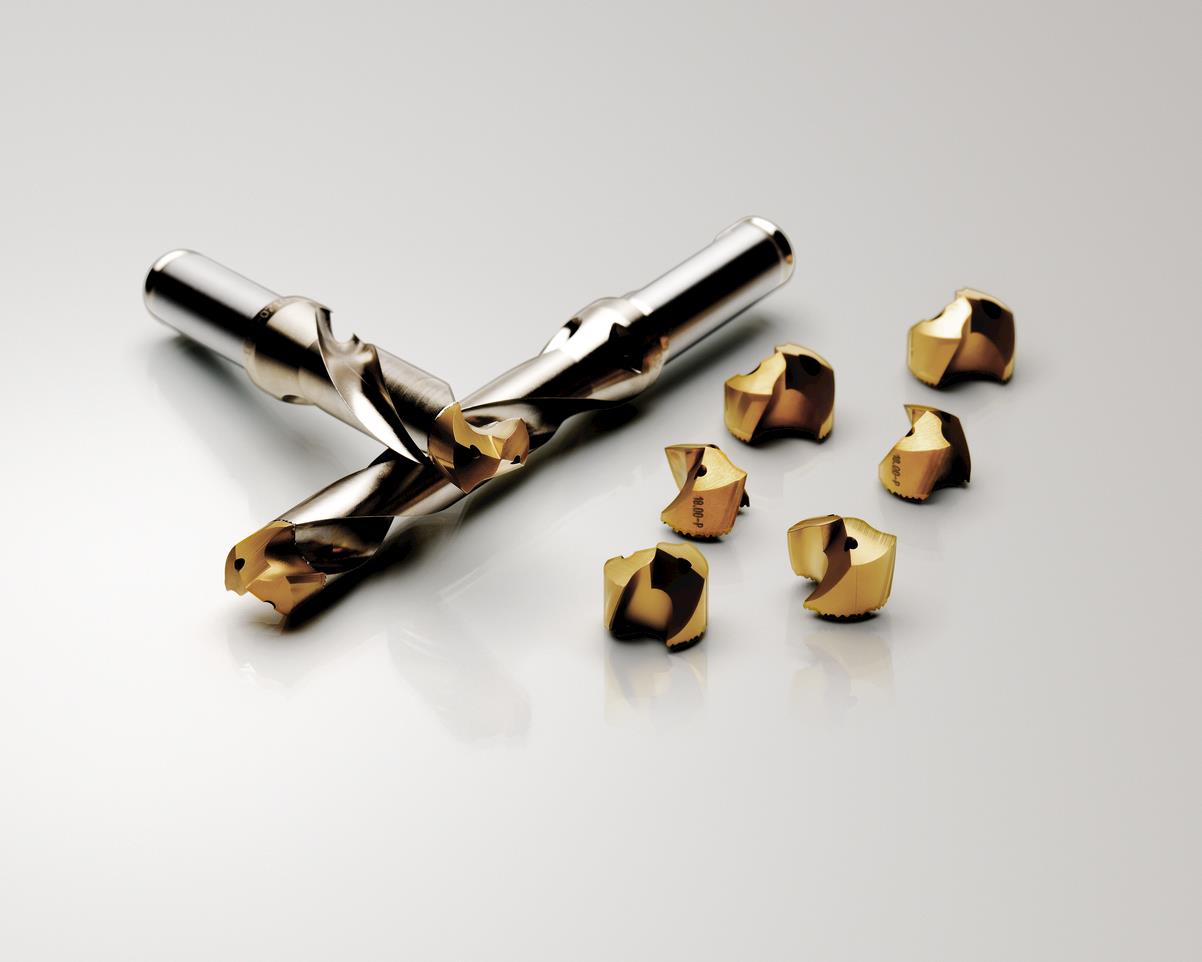
Exchangeable Tip Drills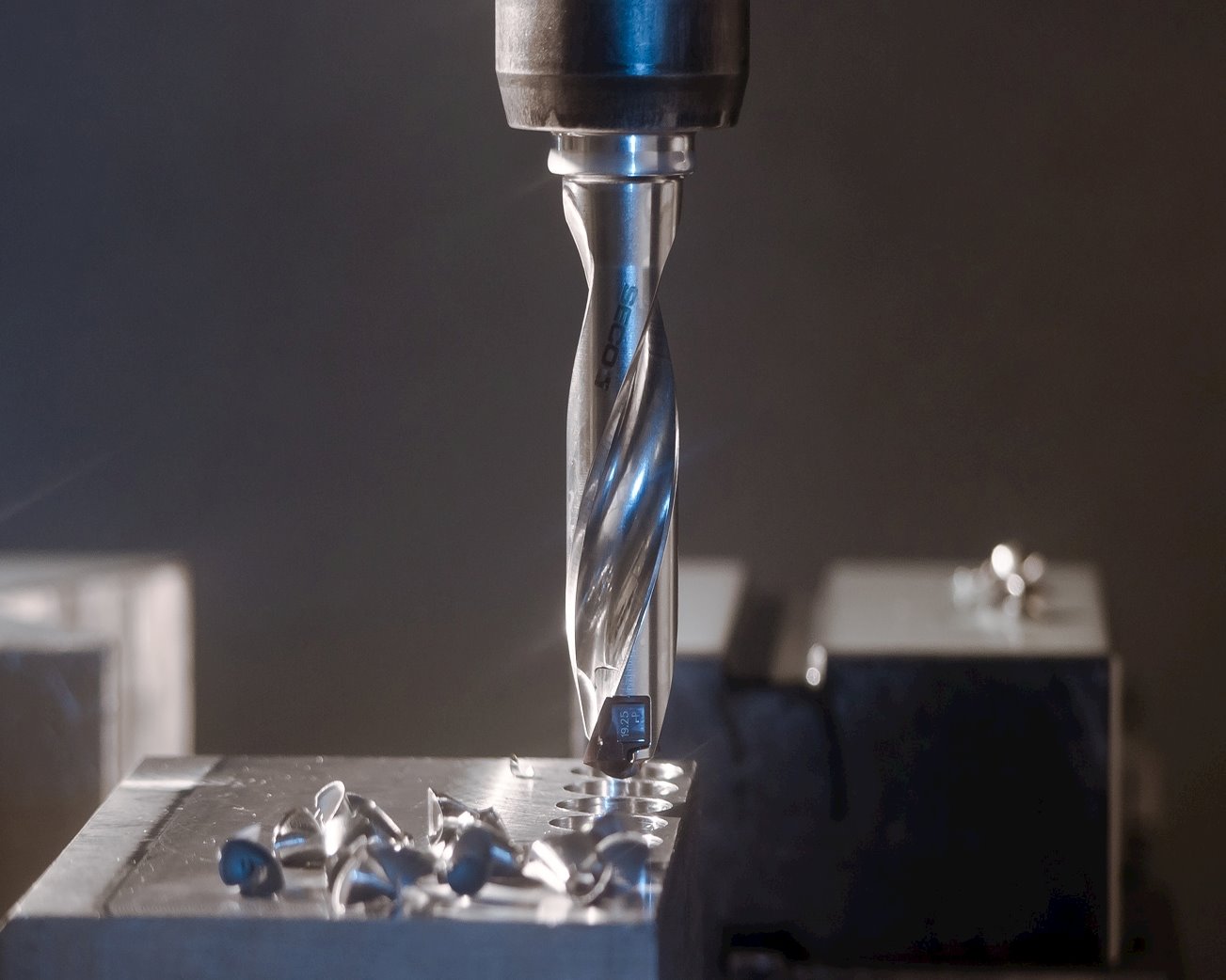
Micro Drills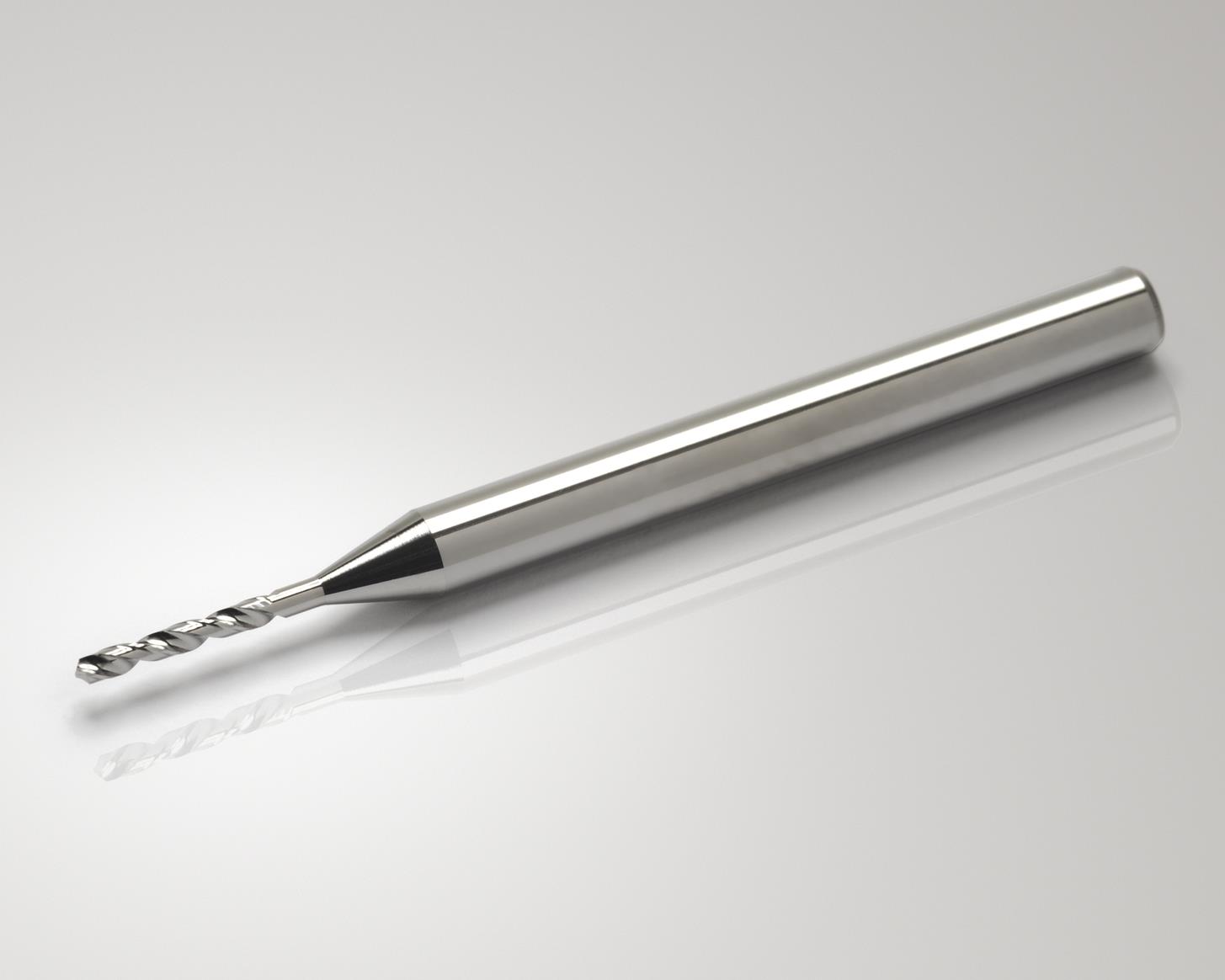
Seco Feedmax - Composite Drills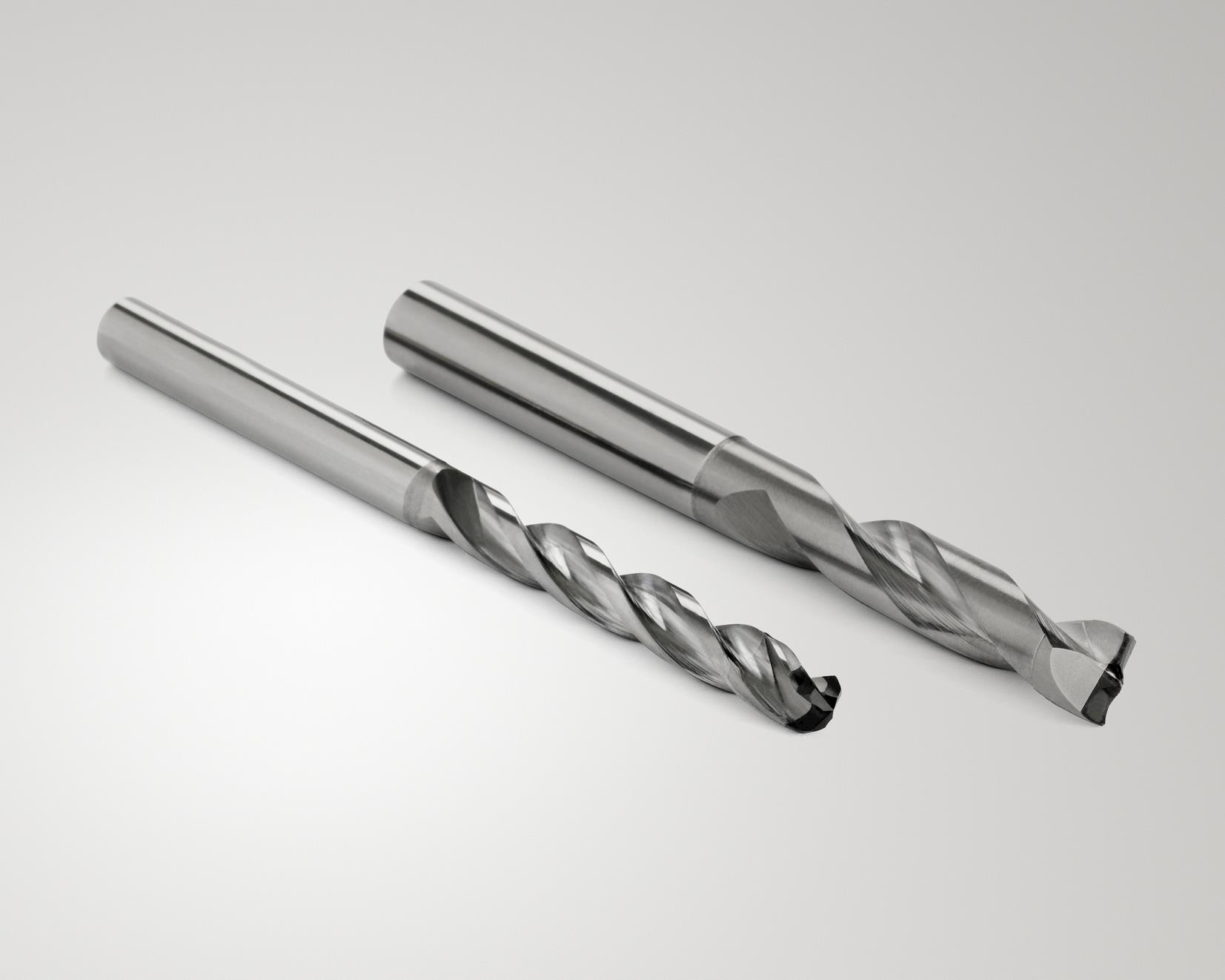
Seco Feedmax - IT 7 High-Precision Drills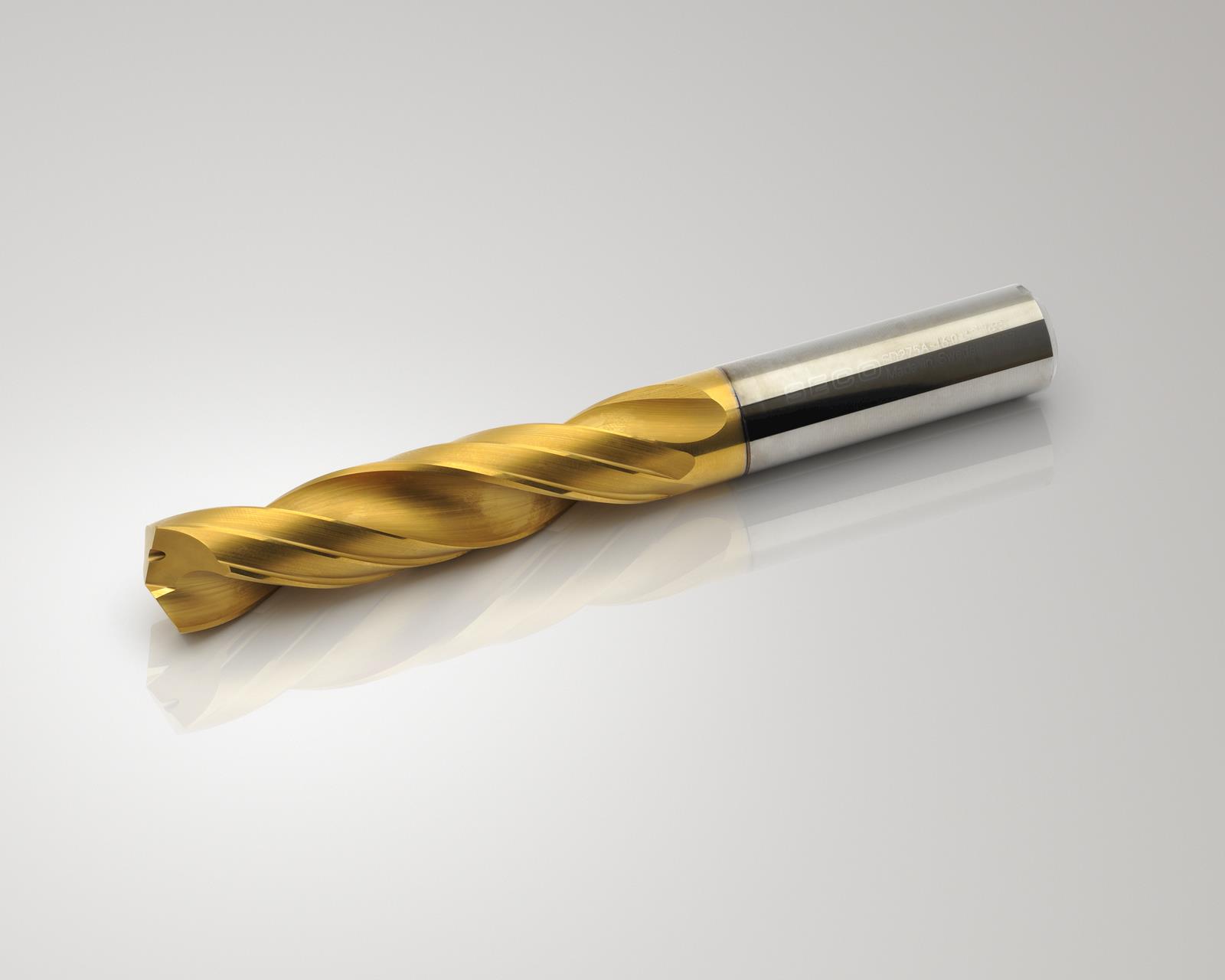
Seco Feedmax - Drills for Interrupted Cuts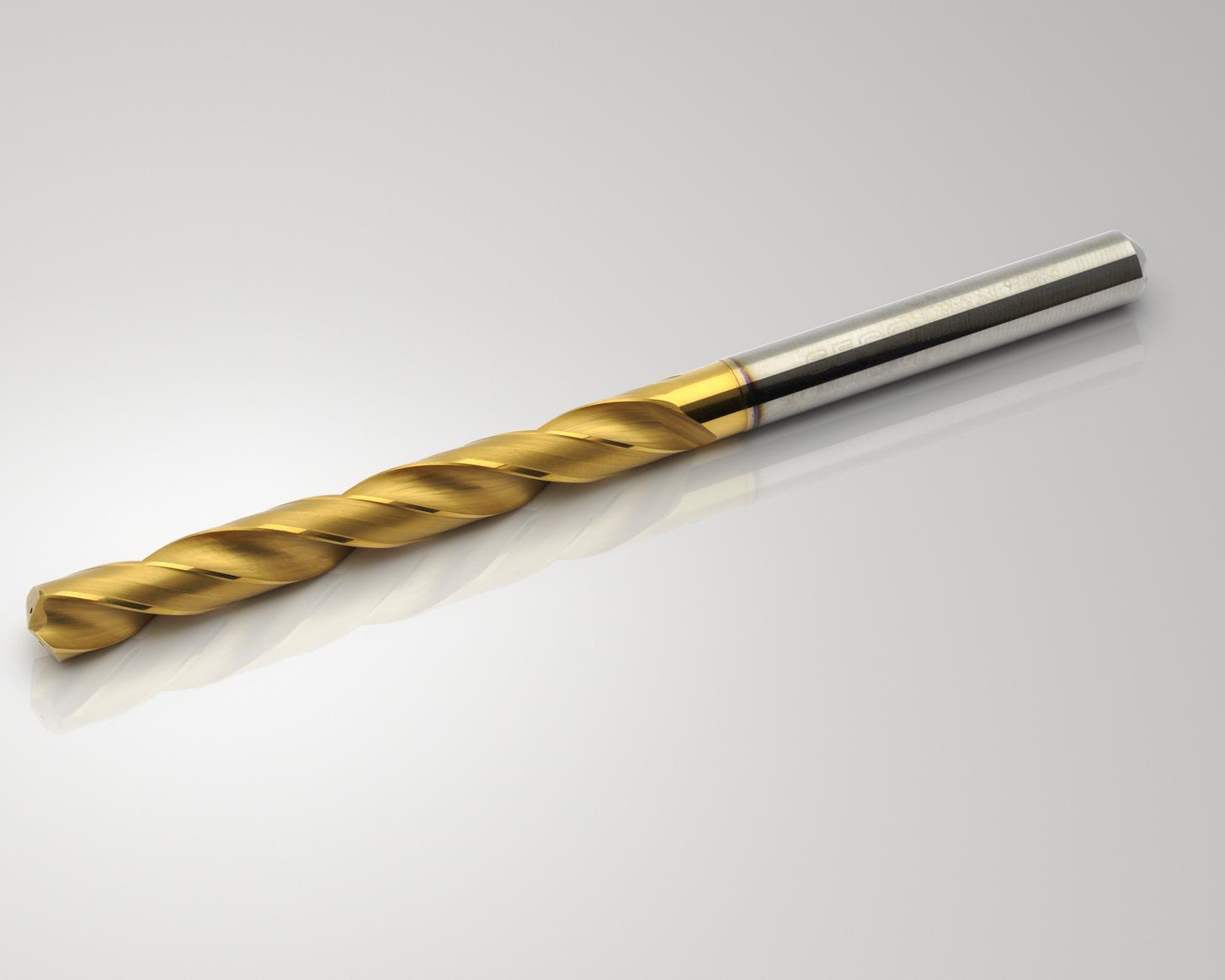
Seco Feedmax – Chamfer Drills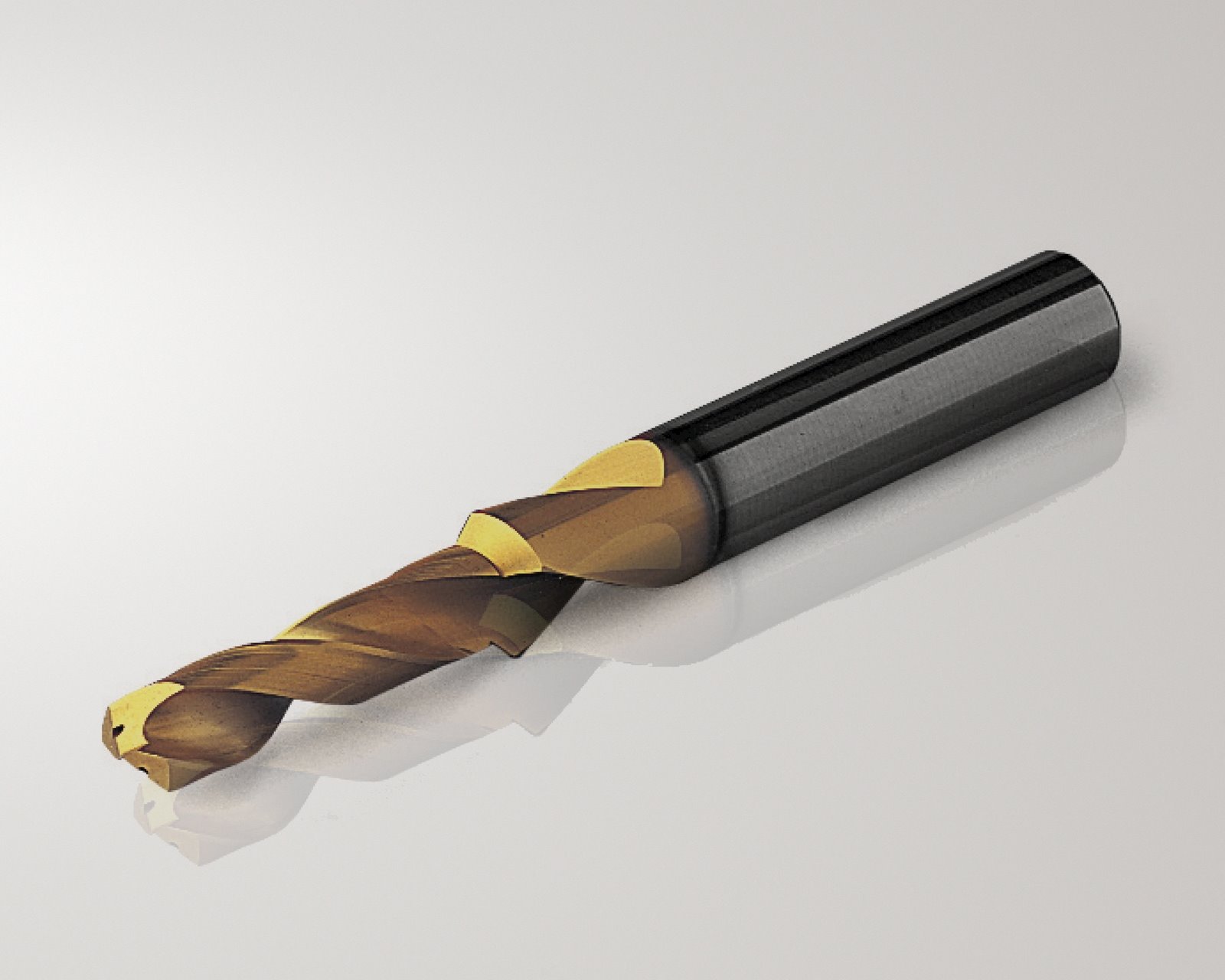
Seco Feedmax - Single-Diameter Drills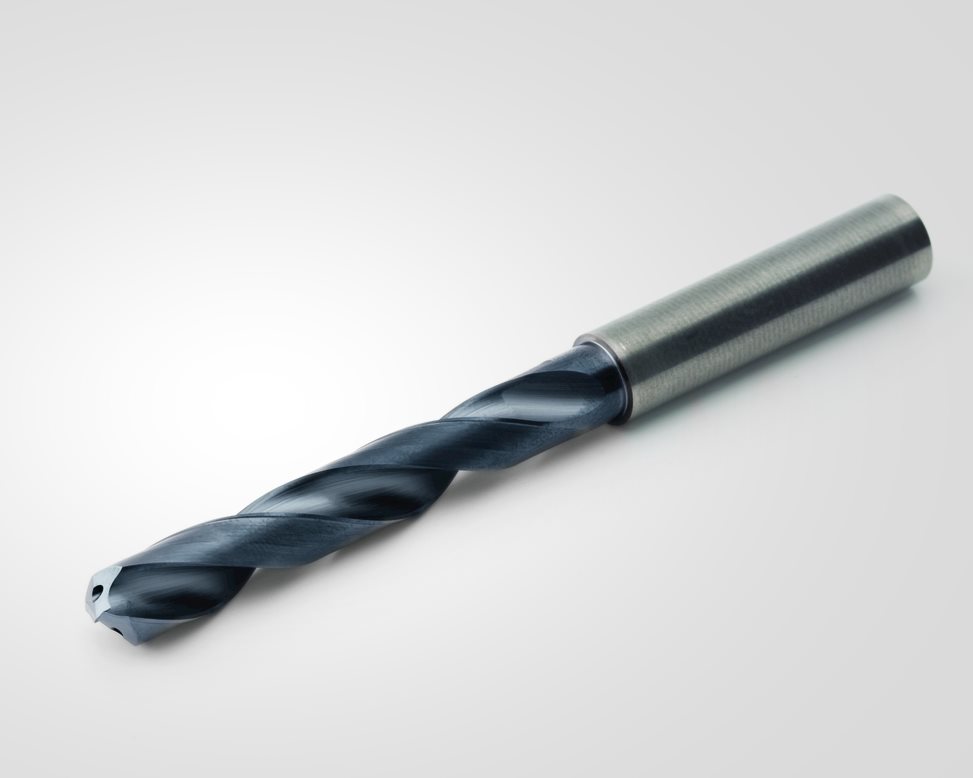
Modular Drill Heads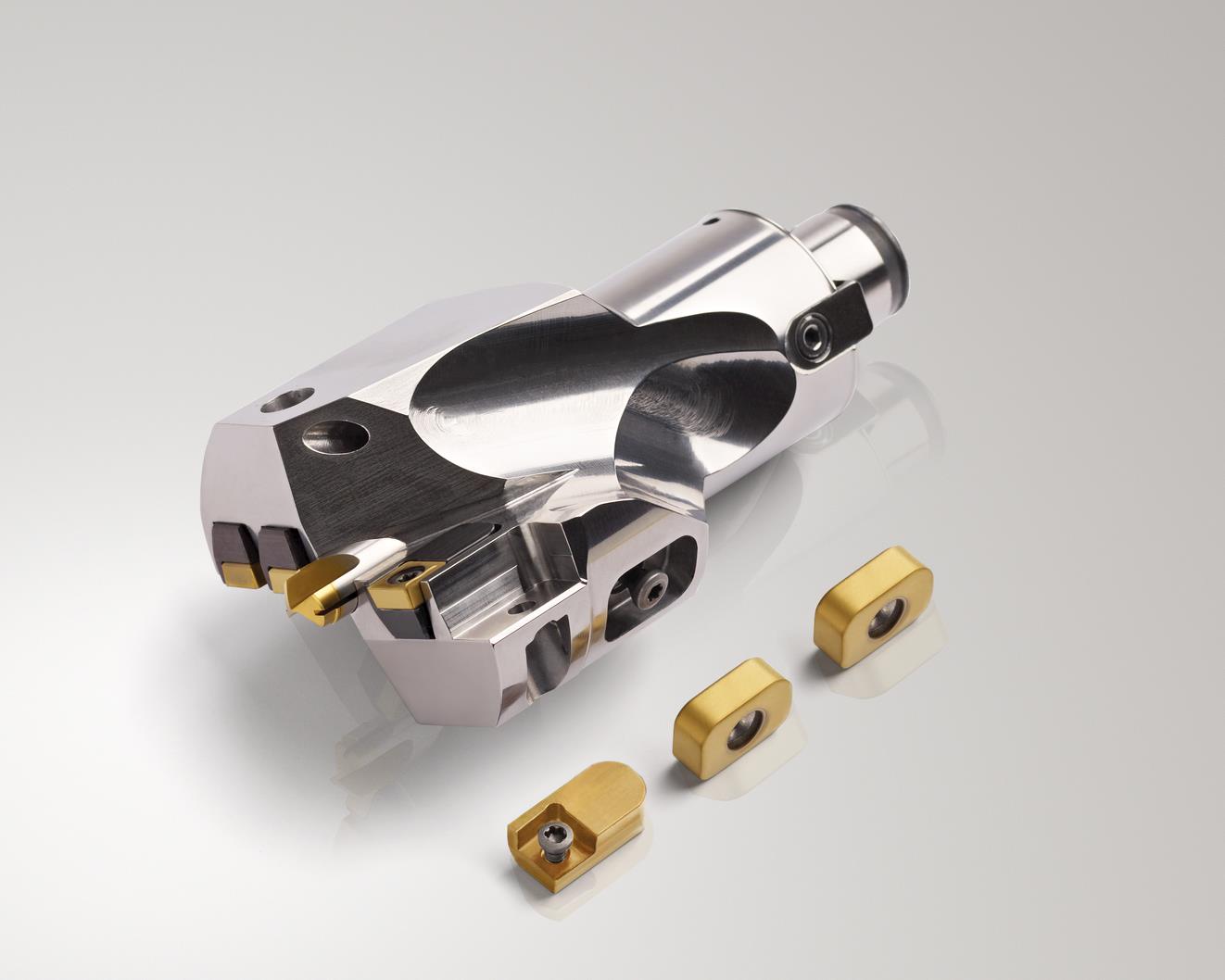
Video: Seco Feedmax SD230A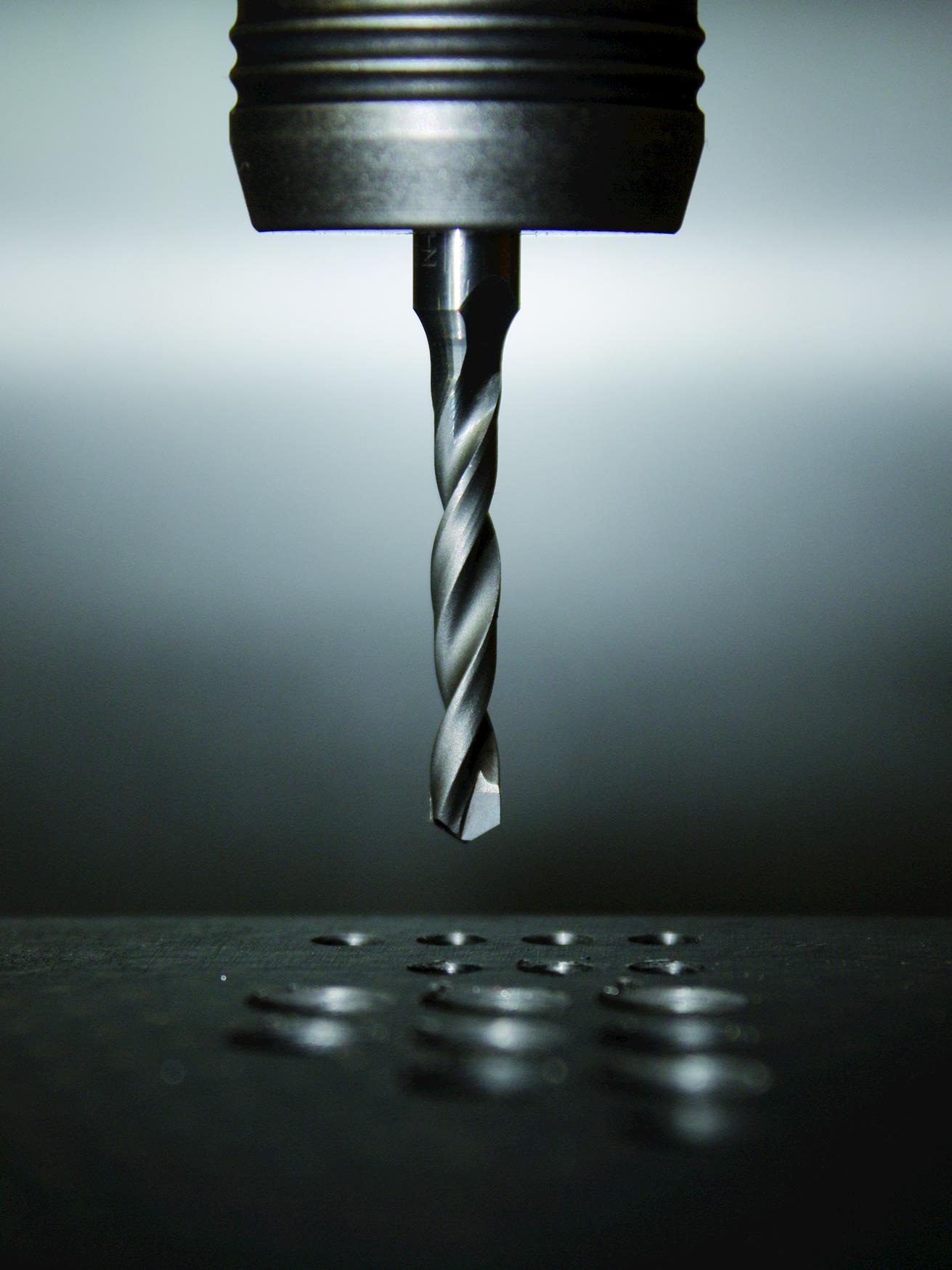
Video: Perfomax® drill by Seco Tools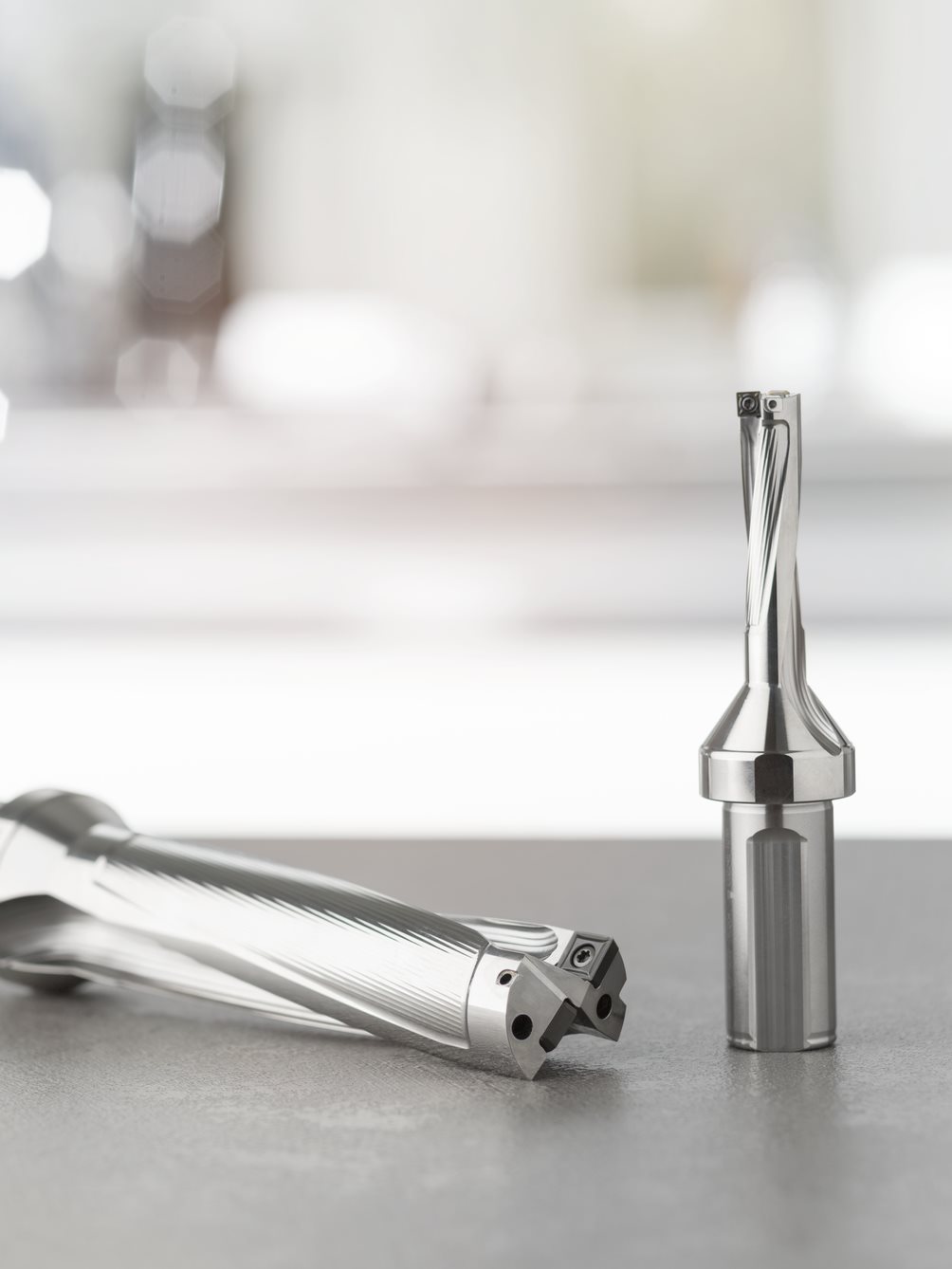
Niagara Universal - Single-Diameter Drills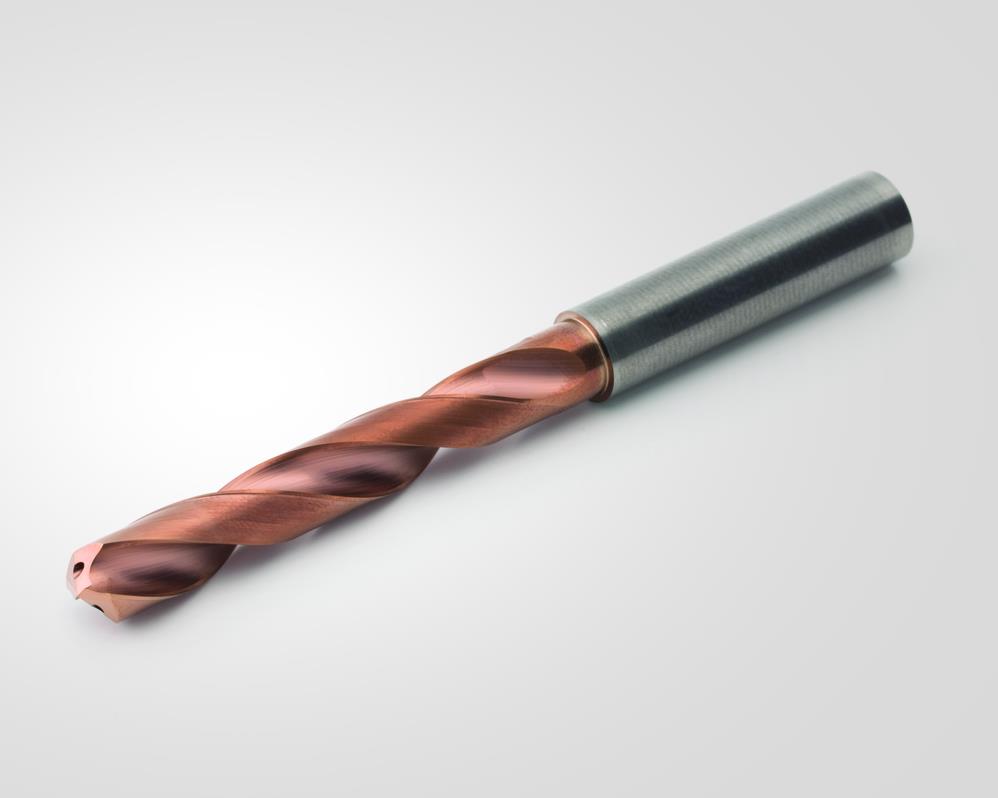